The price of a Class K9 DN400 mm ductile iron (DI) pipe depends on region, lining/coating, and supplier volumes. In India, prices hover around ₹3,647 (≈ US $45) per meter for cement-lined products. In China, typical free-on-board (FOB) pricing ranges US $460–780 per ton (≈ US $90–150 per metre). European suppliers list 400 mm K9 pipes at €400–550/ton (€80–110 /m) subjected to EN 545/ISO 2531 standards. Market trends show modest price rises (3–5 % annually) driven by raw-material costs. Buyers should compare international quotations, check lining requirements (cement mortar, bitumen, epoxy) and plan for installation, transport, and storage charges that can add 10–20 % to base pipe cost.
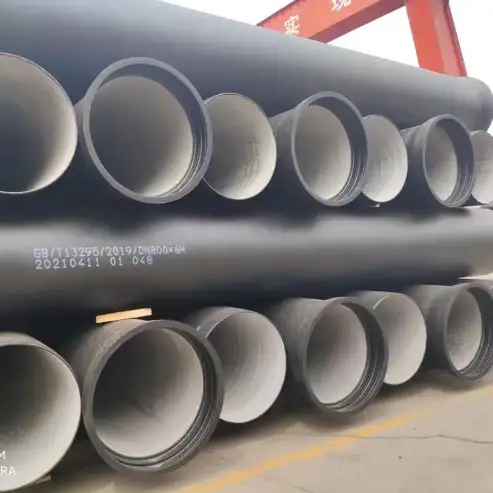
1. What Is Class K9 Ductile Iron Pipe?
Ductile iron pipe is made from spheroidal graphite cast iron, offering superior strength and flexibility over grey cast iron.
Class K9 specifies wall thickness under ISO 2531/EN 545 standards, giving a nominal outside diameter of 429 mm and minimum wall of 8.1 mm. It’s rated for 25 bar internal pressure, ideal for high-pressure water mains.
2. Key Specifications of 400 mm K9 DI Pipe
Parameter | Value |
---|---|
Nominal Diameter (DN) | 400 mm |
Outside Diameter | 429 mm |
Wall Thickness (min) | 8.1 mm |
Pressure Rating | 25 bar |
Standard Internal Lining | Cement mortar |
Common External Coatings | Bitumen, zinc, epoxy |
Length per Piece | 6 m |
3. Factors Influencing K9 400 mm DI Pipe Price
-
Material Costs: Iron ore and scrap-metal indexes strongly impact unit cost.
-
Lining & Coating: Cement-mortar lining adds ~5 % cost; bitumen/epoxy ~8–12 %.
-
Volume Discounts: Bulk orders (≥ 50 t) often get 10–15 % off list price.
-
Transport & Handling: Long-distance/shipping raises cost by 10–20 % of FOB pipe price.
-
Currency Fluctuations: USD/CNY and INR/USD rates directly influence export quotes.
4. Regional Price Comparison
Region | Price (per m) | Currency | Conditions |
---|---|---|---|
India | ₹3,647 | INR | Cement-lined, bulk (≥ 5 t) |
China | US $77–130 | USD | FOB, bitumen-coated, 6 m lengths |
Europe | €80–110 | EUR | EN 545 standard, epoxy-coated |
USA | US $90–150 | USD | AWWA C151, cement-lined |
5. Market Trends & Forecast
Global K9 DI pipe prices rose 4 % in 2024 due to higher steel scrap rates and logistics constraints. Analysts forecast a 3 % CAGR through 2028, driven by urban water infrastructure upgrades in Asia and Europe.
6. How to Source & Purchase
-
Identify Standards: ISO 2531/EN 545 in Europe; AWWA C151 in North America; IS 8329 in India.
-
Request Quotations: From at least three approved vendors, specifying DN, class, lining, quantity.
-
Assess Total Landed Cost: Include transport, customs, taxes, storage, and handling.
-
Inspect Sample Pipes: Verify dimensions, lining adhesion, coating quality before bulk order.
7. Installation & Lifecycle Costs
While the unit price is 10–15 % of total project cost, installation adds:
-
Jointing materials & labor (¥ 100–150 /m in China; US $20–30/m in the US).
-
Trench excavation/backfill (~ US $50–70 /m)
-
Maintenance (expected service life 100+ years with proper lining).
8. Quality Standards & Certifications
-
ISO 2531 / EN 545 / EN 598 (Europe)
-
AWWA C151/C110 (US)
-
IS 8329:2000 (India)
-
WRAS / NSF-61 approvals for potable water.
9. Environmental & Sustainability Considerations
Ductile iron pipes are > 90 % recycled content; fully recyclable after use. Life-cycle analyses show lower carbon footprint vs. PVC and HDPE for diameters ≥ 300 mm.
Frequently Asked Questions
1. Why choose Class K9 over other classes for 400 mm DI pipe?
Class K9 offers a balanced wall thickness of 8.1 mm, rated for 25 bar pressure—ideal for municipal water mains that require durability without excessive material cost. Higher classes (K10, K12) add > 10 % material but are only needed for extreme pressures (> 30 bar). Lower classes (K7, C40) have thinner walls, risking deformation and shorter service life in aggressive soils.
2. Why Do Prices of K9 400 mm DI Pipes Vary So Much Across Regions?
Prices for Class K9, 400 mm ductile iron pipes differ significantly due to local production costs, raw‐material availability, and standards compliance. In India, for example, domestic manufacturers benefit from lower labor costs and abundant scrap‐iron supply, resulting in pipe prices ranging between US $450 and US $650 per meter for cement‐mortar‐lined K9 pipes. Conversely, Chinese suppliers often quote FOB prices of US $460–520 per ton (≈US $77–87 per meter) for bitumen‐coated, ISO 2531 Class K9 pipes in 6 m lengths. European producers incur higher energy and labor costs, and must comply with EN 545/ISO 2531 certifications, driving prices to approximately €80–110 per meter (≈US $85–118). In the United States, adherence to AWWA C151 standards, NSF‐61 approval, and more stringent quality control can push costs to US $90–150 per meter for cement‐lined, flange‐ready pipes. Import duties, transport distance, and currency exchange fluctuations further contribute: a weakening local currency against USD can increase import‐quoted prices by 5–10 % within weeks. Ultimately, regional differences in production scale, standard requirements, and logistics explain why the same nominal DN400 K9 pipe can cost almost twice as much in one market versus another.
3. How Can Buyers Negotiate Bulk Discounts on 400 mm Class K9 Pipes?
Bulk purchasing is the most effective way to secure significant price reductions on 400 mm K9 ductile iron pipes. Suppliers commonly offer tiered pricing: orders of 1–10 tons may receive standard list prices (e.g., US $550–630 per ton), while orders exceeding 25 tons often attract 10–15 % off the base FOB rate. On Alibaba‐listed offerings, minimum order quantities (MOQs) of 10 tons typically unlock the lower end of quoted ranges—for instance, US $460–520 per ton for EN 545 Class K9 pipes —but negotiating a higher MOQ (e.g., 50 tons) can reduce unit costs further to US $400–600 per ton. Additionally, specifying standardized lengths (e.g., 6 m or 12 m) and consistent lining/coating preferences simplifies production runs and minimizes changeover costs, which suppliers can pass on as discounts. To negotiate effectively, buyers should:
-
Compare multiple quotations—request detailed cost breakdowns (material, lining, coating, handling) from at least three vendors.
-
Commit to repeat business—outline a multi‐shipment schedule over 6–12 months to leverage ongoing volume discounts.
-
Offer upfront payment—cash‐in‐advance or letter of credit payments can lower supplier financing costs by 2–3 %.
-
Collaborate on logistics—coordinating consolidated shipping containers or shared transport with other buyers reduces per‐meter freight costs.
By combining these tactics—volume commitment, standardized specifications, and strategic payment and logistics planning—buyers can often negotiate 12–20 % off initial list prices for large K9 pipe orders.
4. What Components Beyond Pipe Cost Should Be Included in Total Project Budget?
The nominal purchase price of a K9 400 mm ductile iron pipe is only one component of the overall infrastructure budget. Buyers must account for:
-
Transportation & Handling: Inland trucking, port handling, and final‐mile delivery can add 10–20 % to FOB pipe cost, particularly for heavy 6 m lengths that require special flatbed trailers or escorted moves.
-
Customs & Duties: Import tariffs vary by country (e.g., 5 % in the EU, 7 % in India, 2 % in some African markets) and are calculated on CIF (Cost, Insurance, Freight) value.
-
Storage & Insurance: On‐site storage facilities to prevent corrosion and damage, plus marine/shipping insurance—typically 0.5–1.0 % of cargo value.
-
Jointing Materials & Labor: Mechanical or push‐on joints, gaskets, and labor typically cost US $20–30 per meter in the US, ¥100–150 (≈US $14–21) per meter in China, and ₹1,000–1,500 (≈US $12–18) in India.
-
Trench Excavation & Backfill: Depending on soil conditions and local wages, excavation and reinstatement range from US $50 to US $70 per meter.
-
Quality Testing & Certification: Hydrostatic pressure tests, lining adhesion tests, and third‐party inspection can add US $5–10 per meter.
-
Contingency: A standard 5–10 % project buffer to cover unforeseen delays or material price escalations.
Factoring all these elements, the installed cost of a 400 mm K9 ductile iron water main can be 3–4 times the raw pipe purchase price, underscoring the importance of comprehensive budgeting early in project planning.
5. How Does Internal Lining and External Coating Choice Affect the Unit Price?
The type of internal lining and external coating selected for K9 pipes materially influences manufacturing complexity and thus unit cost. Cement‐mortar lining—the most common in potable‐water applications—provides corrosion resistance and a smooth hydraulic surface, but requires additional kiln‐drying steps and quality‐control testing, adding approximately 5 % to base pipe cost. Bitumen coating on the exterior is labor‐intensive and poses environmental/worker‐safety concerns, increasing cost by around 8–10 % compared to standard zinc/bitumen paint systems. Epoxy powder coating delivers superior corrosion protection and longer service life, but entails electrostatic application booths and curing ovens, resulting in a 12–15 % price premium over cement‐mortar lining alone. Specialty linings—such as polyurethane or polyethylene—are available for aggressive‐water environments, often elevating cost by 20–25 %. Buyers must balance upfront lining/coating premiums against lifecycle savings: a higher‐grade external epoxy, for instance, can reduce maintenance shutdowns and relining costs, yielding net savings over a 100-year design life.
6. What Are the Future Price Trends for DI Pipes and K9 Grades?
Global ductile iron pipe pricing has demonstrated a steady upward trajectory, with an average annual increase of 3–5 % over the past five years, driven primarily by rising scrap‐iron and energy costs. In 2025, industry analysts predict further pressure on margins as Chinese producers face stricter environmental regulations, increasing furnace operating costs by an estimated 4 % year‐over‐year. Simultaneously, infrastructure stimulus programs in Europe and North America—totaling over US $200 billion in planned water‐utility investments—are expected to boost demand for large‐diameter pipes, potentially raising lead times and supplier premiums by late 2025. Technological advances in electric‐furnace melting and automated lining processes may moderate cost growth beyond 2026, but the ongoing volatility of global steel scrap markets (currently at US $400–450 per ton) suggests price fluctuations of ±3 % per quarter remain likely. Buyers are advised to secure multi‐year supply agreements with fixed escalation clauses tied to published scrap indexes to hedge against future uncertainty.
7. How Can I Ensure Quality While Still Obtaining the Best Price?
Balancing cost and quality requires rigorous vendor evaluation and contract terms. First, verify supplier certification to applicable standards—ISO 2531/EN 545 in Europe, AWWA C151 in North America, and IS 8329:2000 in India. Request third‐party test reports for mechanical properties (tensile ≥ 420 MPa, yield ≥ 300 MPa) and lining adhesion, and insist on witness testing during production runs. Incorporate clear acceptance criteria in purchase orders: dimensional tolerances (± 2 mm), lining thickness (min. 2 mm cement), and coating holiday detection (< 10 % allowable failures per 100 m²). Bundling multiple standards (e.g., NSF‐61 for drinking water, WRAS for UK projects) can raise unit costs by 3–5 %, but avoids rework and shutdown costs. Leverage quality‐cost trade‐off by specifying higher inspection sampling rates—reducing the likelihood of batch rejections at the expense of a modest 1 % fee increase. Finally, include penalty clauses for late delivery or non‐conformance (e.g., 0.5 % contract value per week), which incentivizes supplier performance without inflating base prices.