Ductile iron pipes (DIP) are a cornerstone of modern infrastructure, widely used in water distribution systems, wastewater treatment, fire protection systems, and many industrial applications. Their popularity stems from the significant advantages they offer in terms of strength, durability, and resistance to corrosion.
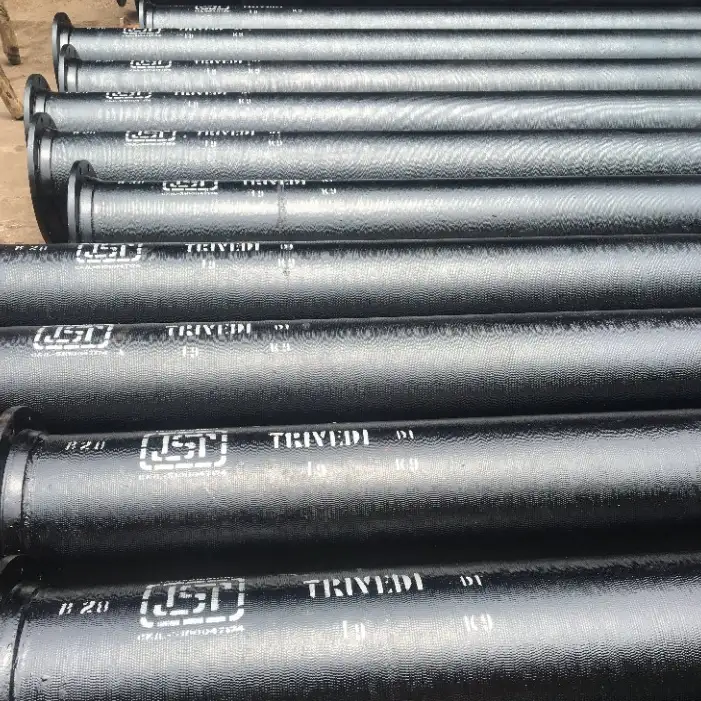
Ductile iron pipes are made from cast iron that has been treated to enhance its mechanical properties. This treatment results in a pipe that is not only stronger and more flexible than traditional cast iron but also less prone to cracking. This makes ductile iron pipes highly reliable for both underground and above-ground installations.
1. What Is Ductile Iron?
Ductile iron is a form of cast iron that contains graphite in the form of spheroids or nodules, rather than flakes. This structure imparts ductility and increased strength to the material. The key components in ductile iron include:
-
Carbon (3-4%): The primary element responsible for the material’s strength and hardness.
-
Silicon (1.5-2.5%): Improves the material’s fluidity during casting.
-
Manganese (0.2-0.6%): Enhances the strength of the alloy and helps in the formation of graphite.
-
Magnesium: The key element that gives ductile iron its unique nodular structure.
These elements, combined with a heat treatment process, give ductile iron its exceptional characteristics—strength, toughness, and the ability to withstand high pressure and stress. These properties make ductile iron the ideal material for water and sewer pipes, as well as for a variety of industrial uses.
2. AWWA Standards for Ductile Iron Pipes
The American Water Works Association (AWWA) sets the standard for manufacturing and testing ductile iron pipes. These standards ensure that pipes meet certain mechanical, physical, and chemical properties, making them suitable for use in water systems. The primary AWWA standards related to ductile iron pipes include:
-
AWWA C151: Standard for ductile iron pipes, specifying wall thickness and other mechanical properties.
-
AWWA C110: Standard for ductile iron fittings, used to connect pipe segments.
-
AWWA C153: Standard for compact fittings made of ductile iron.
-
AWWA C111: Standard for rubber gaskets used to seal joints in ductile iron piping systems.
These standards ensure the reliability, strength, and longevity of ductile iron pipes used in water and wastewater systems.
3. Manufacturing Process of Ductile Iron Pipes
The manufacturing process of ductile iron pipes is a highly controlled procedure that ensures the quality and consistency of each pipe. The key stages of the manufacturing process include:
-
Casting: The raw materials are melted and poured into molds. The casting process is usually centrifugal, which ensures that the walls of the pipe are thick and uniform.
-
Heat Treatment: After casting, the pipes are heat-treated to further enhance their strength and ductility. This process involves heating the pipes to a specific temperature and then cooling them rapidly.
-
Coating: Ductile iron pipes are often coated to prevent corrosion. Common coatings include cement-mortar, epoxy, and bituminous coatings, which help protect the pipes from external corrosion.
-
Testing: Each pipe is subjected to rigorous testing to ensure it meets the required specifications. Tests include pressure testing, bend testing, and sometimes corrosion resistance testing.
4. Types of Ductile Iron Pipes
Ductile iron pipes are available in various types depending on their intended use and environmental conditions. The most common types of ductile iron pipes include:
-
Pressure-Rated Pipes: These pipes are designed to withstand high internal pressures, typically used in water distribution and fire protection systems.
-
Non-Pressure Pipes: Typically used for gravity-based wastewater systems or irrigation lines, these pipes are designed for lower pressure environments.
-
Cement-Mortar Lined Pipes: These pipes have an inner cement coating to prevent corrosion from water contact.
-
Epoxy-Coated Pipes: These pipes are coated with epoxy resin to provide additional protection against internal corrosion.
Each type of pipe is designed to provide maximum durability and performance in specific environments, ensuring the longevity of the piping system.
5. Pressure Ratings for Ductile Iron Pipes
Pressure ratings are an essential consideration when selecting ductile iron pipes. The pressure rating determines the maximum pressure the pipe can withstand without failing. Ductile iron pipes are available in various pressure classes:
-
Class 150: Suitable for low-pressure systems, typically used in residential and small commercial applications.
-
Class 250: Ideal for medium-pressure systems, such as municipal water supply networks.
-
Class 350: Designed for high-pressure systems, typically used in larger infrastructure projects and industrial systems.
The appropriate pressure class should be selected based on the expected pressure within the system to ensure the safety and reliability of the pipes.
6. Applications of Ductile Iron Pipes
Ductile iron pipes are used in a wide variety of applications, including:
-
Water Distribution Systems: Ductile iron pipes are commonly used in municipal water supply systems due to their strength, corrosion resistance, and longevity.
-
Wastewater Systems: These pipes are highly resistant to the corrosive effects of sewage and are ideal for use in sewer lines and treatment facilities.
-
Fire Protection Systems: Ductile iron pipes are often used for fire protection due to their high pressure ratings and reliability.
-
Industrial and Mining Applications: Their ability to withstand high pressures and resist corrosion makes ductile iron pipes suitable for a wide range of industrial uses.
7. Pricing of Ductile Iron Pipes
The price of ductile iron pipes varies depending on several factors, including size, pressure rating, coating, and quantity. Typically, ductile iron pipes can cost between $10 and $50 per foot, but prices can be higher for larger diameters or special coatings.
Factors influencing pricing include:
-
Pipe Size: Larger diameter pipes are more expensive due to the increased material requirements.
-
Pressure Class: Higher pressure-rated pipes require more material and stronger manufacturing processes, making them more expensive.
-
Coating: Pipes with additional coatings, such as epoxy or cement-mortar, tend to be priced higher due to the additional materials and processes involved.
8. Ductile Iron Pipe Fittings
Fittings are an essential component of ductile iron piping systems, allowing for changes in direction, size, or function. Common types of ductile iron fittings include elbows, tees, reducers, and flanges. These fittings must also meet AWWA standards for durability and pressure rating.
9. Benefits of Using Ductile Iron Pipes
The benefits of using ductile iron pipes in modern infrastructure are numerous:
-
Strength and Durability: Ductile iron pipes are highly resistant to cracking and can withstand high pressures, making them ideal for use in water and sewer systems.
-
Corrosion Resistance: Ductile iron is highly resistant to corrosion, especially when coated, ensuring long-term performance even in harsh environments.
-
Sustainability: Ductile iron pipes are recyclable and have a long lifespan, reducing the need for frequent replacements.
-
Cost-Effectiveness: Although initially more expensive than some alternatives, ductile iron pipes provide a long-lasting, reliable solution that reduces maintenance and replacement costs over time.
10. Frequently Asked Questions
1. What is the difference between ductile iron and cast iron pipes?
Ductile iron pipes have a much higher tensile strength and flexibility compared to traditional cast iron pipes, making them less prone to breakage under pressure or stress. They are often used in high-pressure applications and are more durable overall.
2. How are ductile iron pipes installed?
Installation of ductile iron pipes involves careful alignment, proper sealing of joints, and pressure testing to ensure the system is leak-free. Specialized machinery is often used to move and position large pipes.
3. How do I determine the right size of ductile iron pipe for my project?
Choosing the right pipe size depends on the volume of fluid being transported and the pressure requirements. Typically, larger diameter pipes are used for municipal systems, while smaller pipes are used in residential settings.
4. Are ductile iron pipes suitable for corrosive environments?
Yes, ductile iron pipes are often coated to protect them from corrosive environments. Epoxy and cement coatings are commonly used to enhance their resistance to internal and external corrosion.
5. How long do ductile iron pipes last?
Ductile iron pipes can last over 100 years with proper maintenance, making them a highly cost-effective choice for water and wastewater systems.
6. Are ductile iron pipes environmentally friendly?
Yes, ductile iron pipes are recyclable and have a long service life, reducing the environmental impact compared to pipes that require frequent replacements.