Wrapping ductile iron pipe is a critical protective measure to prevent corrosion and extend its service life, especially in aggressive soil or high-moisture environments. Common protective wrapping methods include polyethylene encasement (ANSI/AWWA C105), V-Bio® enhanced polyethylene, or specialized coatings that create a barrier against electrochemical corrosion. Proper wrapping helps maintain structural integrity, reduces maintenance costs, and ensures compliance with AWWA standards for underground piping systems. Learn when and how to wrap ductile iron pipe to maximize durability in water, sewer, and industrial applications.
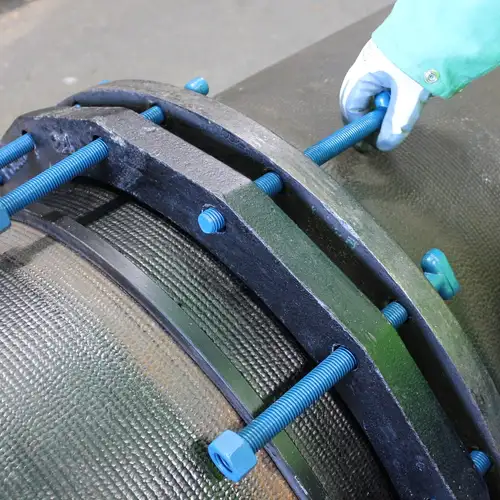
1. What is Ductile Iron Pipe?
Ductile iron pipe is a strong, flexible, and durable pipe material commonly used in water distribution systems, sewage systems, and industrial piping. Unlike traditional cast iron, which is brittle and prone to cracking, ductile iron pipe is designed to withstand high pressure and external stresses while maintaining its strength.
These pipes are ideal for use in areas that require resilience to internal pressure, soil movement, and heavy loads. Ductile iron pipes offer long-term reliability in a variety of applications, but even they need additional protection to extend their lifespan in certain environments.
2. The Need for Wrapping Ductile Iron Pipe
Protecting Against Corrosion
Corrosion is one of the most significant threats to ductile iron pipes, especially in underground environments. Even though ductile iron is more resistant to corrosion than traditional cast iron, it is still susceptible to rust when exposed to moisture, chemicals, and soil conditions. Wrapping the pipe with a protective material helps create a barrier between the pipe and the elements, preventing corrosion and extending the pipe’s service life.
Increasing Durability and Strength
Wrapping ductile iron pipes doesn’t just protect them from corrosion—it also adds an extra layer of physical protection. This can be particularly useful during installation, where pipes may experience abrasions or impacts. Wrapping materials also help the pipe withstand mechanical stresses, making it less likely to suffer from physical damage in challenging conditions.
Preventing Damage During Installation
During the installation of ductile iron pipes, physical damage from handling and transport can sometimes occur. Wrapping provides an additional cushion that minimizes the risk of scratches, dents, or cracks during the installation process. This ensures the pipe remains intact and functional after installation, reducing the likelihood of premature failure.
3. The Benefits of Wrapping Ductile Iron Pipe
Enhanced Corrosion Resistance
Corrosion is a slow process, but over time, it can lead to serious degradation of ductile iron pipes. Wrapping the pipes with corrosion-resistant materials, such as polyethylene (PE), creates an effective barrier that blocks water, oxygen, and chemicals from reaching the pipe surface. This dramatically reduces the chances of rust formation and ensures the pipe’s durability, particularly in areas with high moisture or chemical exposure.
Extending the Pipe’s Lifespan
By protecting against corrosion and physical damage, wrapping ductile iron pipes can significantly extend their lifespan. While unwrapped pipes might begin to corrode after 20 to 30 years, wrapped pipes can last up to 100 years, depending on the type of wrapping material used and the environmental conditions. This extended lifespan helps minimize the need for repairs and replacements, saving money in the long term.
Cost Savings in the Long Run
Although wrapping ductile iron pipes may add initial costs to the installation process, the long-term savings are considerable. With increased durability and corrosion resistance, wrapped pipes require fewer repairs, resulting in lower maintenance costs. Additionally, the extended lifespan reduces the need for costly replacements, offering significant cost savings over time.
4. Types of Wrapping Materials
Several materials are used to wrap ductile iron pipes, each offering specific advantages for different environments and applications.
Polyethylene (PE) Wrapping
Polyethylene is one of the most commonly used materials for wrapping ductile iron pipes. It is flexible, durable, and provides excellent protection against corrosion, moisture, and physical damage.
Advantages:
-
Strong resistance to corrosion and moisture.
-
Flexibility allows for easy installation.
-
Effective in harsh environments.
Disadvantages:
-
Can be more expensive than other options.
-
Not ideal for extreme temperature conditions.
Bituminous Coating
Bituminous coatings are an affordable option for protecting ductile iron pipes from corrosion. These coatings are usually applied directly to the pipe and can be wrapped with an additional protective layer.
Advantages:
-
Cost-effective compared to other materials.
-
Good protection against corrosion.
Disadvantages:
-
Requires regular maintenance and reapplication.
-
May not be as flexible as other materials.
Epoxy and Synthetic Coatings
Epoxy and other synthetic coatings offer superior resistance to both corrosion and extreme temperatures. These materials are commonly used in applications where pipes are exposed to aggressive chemical environments.
Advantages:
-
Excellent resistance to chemicals and high temperatures.
-
Long-lasting protection.
Disadvantages:
-
High upfront cost.
-
Requires specialized application techniques.
5. Methods of Wrapping Ductile Iron Pipe
There are two primary methods for wrapping ductile iron pipes: manual wrapping and automated wrapping systems.
Manual Wrapping
Manual wrapping involves workers applying the wrapping material by hand around the pipe. This method is commonly used for smaller projects or when pipes are installed in areas where automation is not feasible.
Advantages:
-
Cost-effective for smaller projects.
-
Flexible and adaptable to different pipe sizes.
Disadvantages:
-
Labor-intensive.
-
Can result in uneven application if not done properly.
Automated Wrapping
Automated wrapping systems use machines to apply wrapping materials efficiently and consistently. This method is ideal for large-scale projects and ensures that the wrapping is applied evenly across the entire length of the pipe.
Advantages:
-
Fast and efficient.
-
Ensures consistent application.
Disadvantages:
-
Higher initial investment for equipment.
-
Requires skilled operators.
6. Factors to Consider Before Wrapping
Before deciding to wrap ductile iron pipes, several factors must be considered to ensure the wrapping method and material are suitable for the project.
Soil Type and Environmental Conditions
Soil conditions, such as high moisture content, salinity, or acidity, can accelerate corrosion. Wrapping is particularly important in these environments, as it provides an effective barrier against these environmental factors. Areas with heavy traffic or seismic activity may also require extra protection to prevent physical damage to the pipes.
Pipe Size and Use
The size of the pipe and the type of fluid it carries can influence the wrapping choice. Larger pipes or those carrying high-pressure water may need more robust wrapping materials to ensure their durability under stress. Additionally, pipes used in specialized applications (such as chemical transport) may require specific protective coatings.
7. Industry Standards and Guidelines for Wrapping Ductile Iron Pipe
Several industry standards help ensure that ductile iron pipes are properly wrapped and protected from corrosion.
-
ISO Standards: International standards for materials and installation methods, including corrosion protection.
-
AWWA Standards: American Water Works Association guidelines for the installation of ductile iron pipes and the use of wrapping materials.
-
ASTM Standards: American Society for Testing and Materials guidelines for pipe coatings, including those used for corrosion protection.
These standards provide specific instructions on the types of materials and techniques that should be used to wrap ductile iron pipes, ensuring that the pipes perform well over their intended lifespan.
8. Frequently Asked Questions (FAQs)
1. Why is corrosion a concern for ductile iron pipes?
Corrosion weakens the pipe, leading to leaks, cracks, and even complete failure. Although ductile iron is resistant to corrosion, prolonged exposure to moisture, soil chemicals, and oxygen can still cause it to rust over time. Wrapping the pipe helps protect it from these elements and extend its life.
2. How long does wrapped ductile iron pipe last?
Wrapped ductile iron pipes can last up to 100 years, depending on the wrapping material and environmental factors. Proper wrapping greatly reduces the effects of corrosion and physical damage, allowing the pipe to perform reliably for decades.
3. Is wrapping necessary for all ductile iron pipes?
While not always essential, wrapping is highly recommended for ductile iron pipes buried underground or exposed to harsh environmental conditions. In areas with low moisture and no risk of physical damage, wrapping may not be required.
4. How do I select the best wrapping material for my needs?
The best material depends on factors like soil conditions, moisture levels, pipe size, and environmental exposure. Polyethylene wrapping is widely used due to its balance of durability and cost, while synthetic coatings may be necessary for extreme environments.
5. What are the risks of not wrapping ductile iron pipes?
Without wrapping, ductile iron pipes are more susceptible to corrosion, leading to leaks and potential failure. Additionally, physical damage from handling and installation can result in weakened pipes. Wrapping provides protection against both corrosion and mechanical damage, ensuring long-term performance.
9. Conclusion
Wrapping ductile iron pipes is an essential step in ensuring their durability, longevity, and reliability. By selecting the right wrapping materials and methods, you can significantly reduce the risk of corrosion, mechanical damage, and other environmental stresses. Whether for a large-scale infrastructure project or smaller installations, wrapping offers substantial benefits in terms of cost savings, reduced maintenance, and extended pipe life. Following industry standards and best practices for wrapping will help safeguard your ductile iron pipes, ensuring they perform well for many years.
References:
- American National Standards Institute (ANSI) – ANSI/AWWA C105
- American Water Works Association (AWWA) Standards
- ASTM International – Standards for Coatings
- International Organization for Standardization (ISO) – Materials and Installation Methods
- U.S. Environmental Protection Agency (EPA) – Corrosion Prevention Guidelines