Ductile iron valves are integral components in various industrial and municipal applications, such as water treatment plants, sewage systems, and chemical processing facilities. Understanding the pressure rating of these valves is crucial for ensuring system integrity, safety, and compliance with industry standards. The pressure rating indicates the maximum internal pressure a valve can withstand under specified conditions without failure.
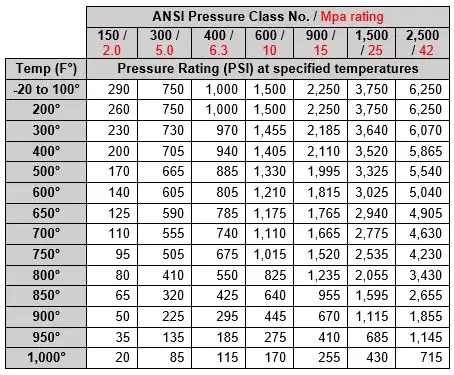
1. Understanding Pressure Ratings
1.1 Definition of Pressure Rating
The pressure rating of a valve refers to the maximum internal pressure it can handle during normal operation. This rating is determined based on factors like material strength, design, and applicable standards.
1.2 Units of Measurement
Pressure ratings are commonly expressed in pounds per square inch (psi) or bar. In the United States, psi is predominantly used, while bar is more common in Europe and other regions.
1.3 Importance of Pressure Ratings
Selecting a valve with an appropriate pressure rating is essential to prevent failures that could lead to system downtime, safety hazards, or environmental damage.
2. Ductile Iron Valve Pressure Classes
Ductile iron valves are categorized into different pressure classes, each indicating the maximum pressure the valve can handle.
2.1 Common Pressure Classes
Pressure Class | Max Pressure (psi) | Max Pressure (bar) | Standard |
---|---|---|---|
Class 150 | 150 | 10.34 | ANSI B16.1 |
Class 250 | 250 | 17.24 | ANSI B16.1 |
Class 300 | 300 | 20.68 | ANSI B16.1 |
PN10 | 145 | 10.00 | ISO 7005-2 |
PN16 | 230 | 16.00 | ISO 7005-2 |
PN25 | 365 | 25.00 | ISO 7005-2 |
PN40 | 580 | 40.00 | ISO 7005-2 |
2.2 Factors Affecting Pressure Ratings
Several factors influence the pressure rating of ductile iron valves:
-
Material Composition: Ductile iron has superior tensile strength compared to gray iron, allowing for higher pressure ratings.
-
Valve Design: The structural design, including wall thickness and reinforcement, impacts the valve’s ability to withstand internal pressures.
-
Temperature: Higher temperatures can reduce the material strength, thereby lowering the pressure rating.
-
Flange Rating: The pressure rating of the valve flanges must align with the valve body to ensure overall system integrity.
2.3 Pressure-Temperature Relationship
As temperature increases, the pressure rating of ductile iron valves decreases. For instance, a Class 150 valve rated at 150 psi at 100°F may only handle 100 psi at 400°F. It’s essential to consult specific pressure-temperature charts for accurate ratings at varying temperatures.
3. Standards and Specifications
Various standards govern the pressure ratings of ductile iron valves:
-
ANSI B16.1: Specifies pressure-temperature ratings for cast iron valves and flanges.
-
ISO 7005-2: Provides guidelines for flanged valves made of cast iron and ductile iron.
-
AWWA C515: Pertains to resilient wedge gate valves made of ductile iron for waterworks service.
-
ASTM A395: Standard specification for ferritic ductile iron pressure-retaining castings for use in piping systems.
4. Applications of Ductile Iron Valves
Ductile iron valves are utilized in various applications:
-
Water Distribution Systems: Used to control water flow and pressure in municipal water networks.
-
Sewage and Wastewater Treatment: Regulate the flow of sewage and treated water.
-
Chemical Processing: Control the flow of chemicals in industrial processes.
-
Fire Protection Systems: Ensure adequate water supply and pressure for fire suppression.
5. Maintenance and Inspection
Regular maintenance and inspection are crucial to ensure the longevity and reliability of ductile iron valves:
-
Visual Inspections: Check for signs of corrosion, wear, or damage.
-
Functional Testing: Verify the valve operates correctly under pressure.
-
Lubrication: Ensure moving parts are adequately lubricated to prevent seizing.
-
Pressure Testing: Conduct hydrostatic tests to confirm the valve’s pressure rating.
6. Frequently Asked Questions (FAQs)
6.1 What is the difference between ductile iron and gray iron valves?
Ductile iron valves are made from a material that has improved tensile strength and ductility compared to gray iron. This enhancement allows ductile iron valves to handle higher pressures and resist cracking under stress.
6.2 How do I determine the appropriate pressure class for my application?
The appropriate pressure class depends on factors such as the system’s operating pressure, temperature, and the specific requirements of the application. It’s essential to consult with engineers and refer to relevant standards to select the correct pressure class.
6.3 Can ductile iron valves be used in high-temperature applications?
While ductile iron valves can withstand moderate temperatures, their pressure rating decreases as temperature increases. For high-temperature applications, it’s crucial to consult pressure-temperature charts and consider alternative materials or valve designs.
6.4 What are the consequences of exceeding a valve’s pressure rating?
Exceeding a valve’s pressure rating can lead to valve failure, system leaks, or catastrophic damage. It’s essential to operate valves within their specified pressure limits to ensure safety and system integrity.
6.5 How often should ductile iron valves be inspected?
The frequency of inspections depends on factors like the valve’s criticality, operating conditions, and manufacturer recommendations. Regular inspections help identify potential issues early and prevent unexpected failures.
Conclusion
Understanding the pressure rating of ductile iron valves is essential for ensuring the safe and efficient operation of piping systems. By considering factors such as material properties, design standards, and application requirements, engineers can select the appropriate valves to meet system demands. Regular maintenance and adherence to industry standards further enhance the reliability and longevity of these critical components.