In the world of piping systems, understanding the differences in terminology and classification is crucial for engineers, procurement specialists, and infrastructure planners. Two terms that often come up are IPS (Iron Pipe Size) and ductile iron pipe. Although they are related, they address different aspects of pipe design and selection.
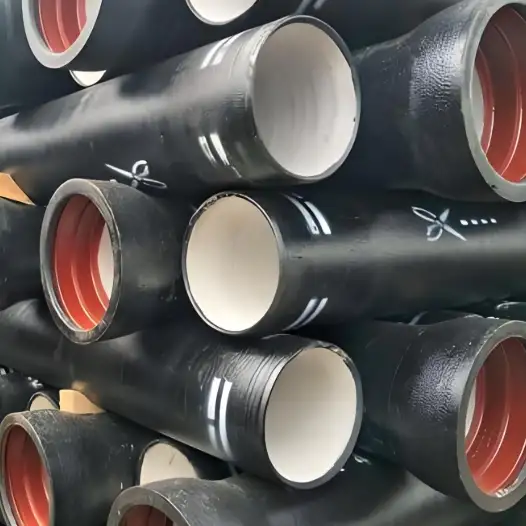
1. Understanding IPS (Iron Pipe Size)
Definition and Background
-
IPS as a Sizing Standard:
IPS stands for Iron Pipe Size, which is a nominal sizing system historically used to designate pipe dimensions in the United States. It establishes standardized measurements for the internal and external diameters of pipes, regardless of the material used. -
Application Across Materials:
The IPS system is widely applied not only to metal pipes—including cast iron, steel, and ductile iron—but also to other materials, ensuring compatibility and simplified design calculations when connecting various components in a piping network.
Key Characteristics of IPS
-
Nominal Sizing:
The IPS designation provides a “nominal” pipe size—a size that approximately represents the internal diameter while standardizing dimensions even if actual measurements differ slightly based on manufacturing tolerances. -
Historical and Regional Use:
Although IPS is primarily used in North America, it has been largely supplanted by modern sizing standards (such as SDR and metric systems) in many regions. However, legacy systems and design documentation may still reference IPS.
2. Understanding Ductile Iron Pipe
Definition and Material Composition
-
Ductile Iron Pipe Explained:
Ductile iron pipe is a type of pipe made from ductile iron—a material known for its excellent strength, ductility (ability to deform without breaking), and corrosion resistance. Compared to traditional cast iron, ductile iron exhibits improved flexibility and fracture toughness. -
Manufacturing Advances:
Advances in metallurgy and manufacturing processes (such as centrifugal casting and precise rolling) have elevated ductile iron as the material of choice for critical infrastructure projects, including water distribution, wastewater management, and industrial piping.
Performance and Standards
-
Mechanical Advantages:
Ductile iron pipes are celebrated for their ability to withstand high pressures and provide longevity in demanding conditions. Their enhanced properties allow for more aggressive fluid transport while reducing susceptibility to cracking. -
Global Standards and Grading:
International standards (like ISO 2531, EN 545, ASTM A536, and AWWA specifications) govern the production and testing of ductile iron pipes. These standards help maintain consistency in wall thickness, pressure ratings, and mechanical strength across different regions.
Data Table – Comparison of Key Properties:
Property | Ductile Iron Pipe | Traditional Cast Iron Pipe |
---|---|---|
Material Toughness | High ductility and strength | Brittle, less flexible |
Corrosion Resistance | Superior, often lined or coated | Varies with treatment |
Pressure Handling | High-pressure capability | Lower pressure ratings |
Standard Compliance | ISO, EN, ASTM, AWWA | Older, less stringent |
Table Note: Actual performance can vary based on manufacturing practices and additional treatments such as cement mortar lining or polymer coatings.
3. Key Differences Between IPS and Ductile Iron Pipe
Although both terms are closely associated with piping systems, the differences lie in their focus:
Sizing vs. Material
-
IPS:
Refers to the standard for designating pipe dimensions. It is essentially a sizing system that applies to a variety of pipe materials, providing a common reference for engineers. -
Ductile Iron Pipe:
Describes a specific type of pipe made from ductile iron. Its superior mechanical properties, particularly in terms of strength and ductility, set it apart from other materials.
Standardization and Application
-
IPS Standard:
Originally developed to standardize pipe dimensions, IPS ensures consistent fittings and connections across different types of metal pipes. It remains relevant for legacy systems and design references. -
Ductile Iron Standards:
Ductile iron pipes are produced under modern, rigorous standards (ISO 2531, EN 545, ASTM A536, and AWWA classes) that not only cover dimensional accuracy but also mechanical performance, pressure rating, and durability.
Impact on System Design
-
Using IPS:
When designing a piping network, IPS values help ensure that all interconnected components (valves, flanges, couplings) match in nominal size, even if the actual internal diameters vary slightly. -
Choosing Ductile Iron Pipe:
The decision to use ductile iron typically centers on performance requirements such as load-bearing capacity, resistance to shock and corrosion, and longevity in aggressive environments. These pipes may be specified by both their material grade (e.g., 60-40-18, 80-55-06) and by IPS (or other sizing standards) to ensure compatibility in the system.
4. Real-World Examples
Case Study: Municipal Water Distribution Upgrade
A mid-sized city in North America decided to upgrade its aging water distribution network. The engineering team chose ductile iron pipes due to their high pressure ratings and durability. Although the design drawings referenced IPS sizes for interoperability, the selection process focused on modern ductile iron grades, which met stringent AWWA and ASTM standards.
Outcomes:
-
Improved System Reliability: Reduced downtime and lower maintenance costs.
-
Seamless Integration: Existing components referenced by IPS dimensions were readily compatible with the new pipes.
Case Study: Industrial Piping in Europe
In an industrial setting requiring robust cooling systems, ductile iron pipes were preferred for their exceptional performance under high thermal and mechanical stresses. While the sizing was defined in metric or SDR terms (as opposed to IPS), the underlying material properties made ductile iron the optimum choice for high-temperature operations.
Outcomes:
-
Enhanced Operational Safety: The superior ductility and toughness minimized the risk of catastrophic failure.
-
Regulatory Compliance: The installation conformed to EN 545 standards, ensuring long-term reliability and compliance with local regulations.
In summary, IPS and ductile iron pipe address different aspects of piping system design. IPS is a standardized sizing system that ensures compatibility across various materials, while ductile iron pipe refers to a specific, high-performance product renowned for its superior strength, ductility, and resistance to corrosion.
References:
- Iron Pipe Size (IPS) – Wikipedia
- ISO 2531: Ductile Iron Pipes, Fittings, Accessories and Their Joints for Water Applications – International Organization for Standardization
- ASTM A536 – Standard Specification for Ductile Iron Castings – ASTM International
- AWWA Standards for Ductile Iron Pipe and Fittings – American Water Works Association
- EN 545: Ductile Iron Pipes, Fittings, and Their Joints for Water Pipelines – European Committee for Standardization (CEN)