When selecting materials for piping systems, engineers and project managers often face the decision between High-Density Polyethylene (HDPE) and Ductile Iron (DI) pipes. Both materials have distinct properties, advantages, and limitations that make them suitable for specific applications.
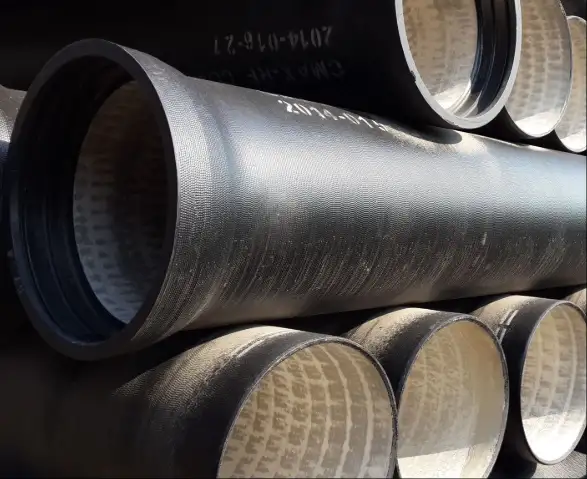
1. Overview of HDPE and DI Pipes
HDPE Pipes:
High-Density Polyethylene (HDPE) is a thermoplastic polymer known for its high strength-to-density ratio. HDPE pipes are lightweight, flexible, and resistant to various chemicals and environmental conditions. They are commonly used in water distribution, gas pipelines, and industrial applications.
DI Pipes:
Ductile Iron (DI) pipes are made from ductile cast iron, which is characterized by its spheroidal graphite structure. This composition provides enhanced strength and ductility compared to traditional cast iron. DI pipes are widely used in potable water systems, sewage systems, and fire protection systems.
2. Material Composition and Manufacturing
HDPE Pipes:
-
Composition: Made from high-density polyethylene resin.
-
Manufacturing Process: Extrusion molding, followed by cooling and cutting to desired lengths.
-
Standards: Manufactured according to ASTM D3035 and ISO 4427 standards.
DI Pipes:
-
Composition: Made from ductile cast iron with added alloying elements like magnesium.
-
Manufacturing Process: Centrifugal casting or sand casting.
-
Standards: Manufactured according to AWWA C151 and ASTM A536 standards.
3. Mechanical Properties
Property | HDPE Pipe | DI Pipe |
---|---|---|
Tensile Strength | 3,500–4,000 psi | 42,000 psi |
Yield Strength | 2,000–2,500 psi | 30,000 psi |
Modulus of Elasticity | 0.4–0.6 x 10⁶ psi | 17 x 10⁶ psi |
Impact Resistance | High | Very High |
Flexibility | High | Moderate |
Note: Values are approximate and can vary based on specific grades and conditions.
4. Hydraulic Performance
HDPE Pipes:
-
Smooth Interior Surface: Reduces friction losses and enhances flow efficiency.
-
Hazen-Williams C-Factor: Approximately 150, indicating excellent flow characteristics.
DI Pipes:
-
Interior Lining: Typically cement-mortar lined to reduce friction and prevent corrosion.
-
Hazen-Williams C-Factor: Ranges from 130 to 150, depending on the condition of the lining.
5. Corrosion Resistance
HDPE Pipes:
-
Intrinsic Resistance: Naturally resistant to corrosion from chemicals, acids, and bases.
-
No Need for Coatings: Eliminates the need for external coatings or linings.
DI Pipes:
-
Potential for Corrosion: Susceptible to corrosion if protective coatings are damaged or degrade over time.
-
Protective Coatings: Require internal and external coatings, such as cement-mortar lining and polyethylene encasement, to prevent corrosion.
6. Installation Methods
HDPE Pipes:
-
Joining Techniques: Butt fusion welding, electrofusion, and mechanical fittings.
-
Installation Considerations: Requires specialized equipment and trained personnel.
DI Pipes:
-
Joining Techniques: Push-on joints with rubber gaskets, flange joints, and mechanical joints.
-
Installation Considerations: Easier to assemble and disassemble; however, handling requires care due to weight.
7. Cost Analysis
HDPE Pipes:
-
Material Cost: Generally lower than DI pipes.
-
Installation Cost: Potentially higher due to specialized equipment and labor.
-
Maintenance Cost: Lower over the lifespan due to corrosion resistance and reduced need for repairs.
DI Pipes:
-
Material Cost: Higher due to the cost of raw materials and manufacturing processes.
-
Installation Cost: Lower, as traditional installation methods are well-established.
-
Maintenance Cost: Higher over time due to potential corrosion and the need for protective coatings.
8. Environmental Impact
HDPE Pipes:
-
Recyclability: Fully recyclable, contributing to a circular economy.
-
Energy Consumption: Lower energy requirements during manufacturing compared to DI pipes.
DI Pipes:
-
Recyclability: Made from recycled iron scrap, promoting resource conservation.
-
Energy Consumption: Higher energy requirements during manufacturing due to the casting process.
9. Applications
HDPE Pipes:
-
Water Distribution: Suitable for potable and non-potable water systems.
-
Gas Distribution: Ideal for natural gas pipelines.
-
Industrial Applications: Used in chemical processing and slurry transport.
DI Pipes:
-
Water Distribution: Widely used in municipal water systems.
-
Sewer Systems: Common in wastewater collection and treatment.
-
Fire Protection: Preferred for fire hydrant and sprinkler systems.
10. Maintenance and Longevity
HDPE Pipes:
-
Service Life: Can exceed 100 years with proper installation and maintenance.
-
Maintenance: Requires minimal maintenance due to resistance to corrosion and scaling.
DI Pipes:
-
Service Life: Typically 50–100 years, depending on environmental conditions and maintenance.
-
Maintenance: Regular inspections and maintenance are necessary to address corrosion and ensure longevity.
11. Comparison Table
Feature | HDPE Pipe | DI Pipe |
---|---|---|
Material | High-Density Polyethylene | Ductile Cast Iron |
Tensile Strength | 3,500–4,000 psi | 42,000 psi |
Yield Strength | 2,000–2,500 psi | 30,000 psi |
Corrosion Resistance | Excellent | Moderate to High |
Installation Method | Butt Fusion, Electro Fusion | Push-on Joints, Flanges |
Maintenance | Low | Moderate to High |
Service Life |
|
50–100 years |
Cost | Lower Material, Higher Install | Higher Material, Lower Install |
12. Frequently Asked Questions (FAQs)
Q1: Which pipe material is more cost-effective in the long term?
While HDPE pipes may have a higher initial installation cost due to specialized equipment and labor, their lower maintenance requirements and longer service life often make them more cost-effective over time. DI pipes, on the other hand, may have lower initial costs but can incur higher maintenance expenses due to corrosion and the need for protective coatings. Therefore, HDPE pipes can offer better value in the long term.
Q2: Can HDPE pipes be used for high-pressure applications?
Yes, HDPE pipes can be used for high-pressure applications; however, their pressure ratings are generally lower than those of DI pipes. The pressure rating of HDPE pipes depends on factors such as pipe diameter, wall thickness, and material grade. For extremely high-pressure systems, DI pipes may be preferred due to their higher hydrostatic design basis.
Q3: Are HDPE pipes suitable for use in seismic zones?
Yes, HDPE pipes are highly suitable for installation in seismic zones due to their inherent flexibility and ability to absorb ground movements. This characteristic makes them an ideal choice for areas prone to earthquakes, as they can withstand ground shifts without cracking or breaking. The flexibility of HDPE pipes allows them to bend and adapt to ground movements, reducing the risk of damage during seismic events. Additionally, HDPE pipes can be installed using trenchless methods, further minimizing the disruption to the surrounding environment during installation.
Q4: How does the pressure rating of HDPE compare to DI pipes?
Ductile Iron (DI) pipes generally have higher pressure ratings compared to High-Density Polyethylene (HDPE) pipes. The pressure rating of a pipe is a critical factor in determining its suitability for various applications, especially in systems that require the transportation of fluids under high pressure. DI pipes are designed to handle higher internal pressures, making them suitable for applications such as fire protection systems and high-pressure water distribution networks. On the other hand, HDPE pipes, while offering excellent performance in many applications, have lower pressure ratings and are more suitable for low to medium-pressure systems.
Q5: What are the environmental impacts of HDPE and DI pipes?
Both HDPE and DI pipes have environmental considerations that influence their selection for specific applications. HDPE pipes are made from a recyclable material, contributing to sustainability efforts. However, they can be susceptible to UV degradation if not properly protected, which can limit their outdoor use without additional coatings or protective measures. DI pipes, while durable and strong, are made from metal and can be subject to corrosion over time, especially if protective coatings are damaged. Both materials require proper maintenance and consideration of environmental factors to ensure their longevity and minimize environmental impact.
Conclusion
In conclusion, the choice between HDPE and DI pipes depends on various factors, including the specific requirements of the project, environmental considerations, and budget constraints. HDPE pipes offer advantages in flexibility, corrosion resistance, and ease of installation, making them suitable for a wide range of applications. DI pipes, with their higher pressure ratings and strength, are ideal for high-pressure systems and areas where durability is paramount. Understanding the differences between these materials is crucial for making informed decisions that align with the project’s objectives and environmental considerations.
References:
- High-Density Polyethylene (HDPE) – Wikipedia
- ASTM D3035 – Standard Specification for Polyethylene (PE) Pipes for Water Distribution
- AWWA C151 – Standard for Ductile-Iron Pipe, Centrifugally Cast
- ISO 4427 – Plastics piping systems for water supply – Polyethylene (PE) pipes
- ASTM A536 – Standard Specification for Ductile Iron Castings