Flanges are integral components in piping systems, serving as connectors between pipes, valves, pumps, and other equipment. They are classified based on their pressure-temperature ratings, which determine the maximum pressure they can withstand at a specific temperature. Two commonly encountered flange classes are Class 125 and Class 150. Understanding the differences between these classes is crucial for selecting the appropriate flange for a given application.
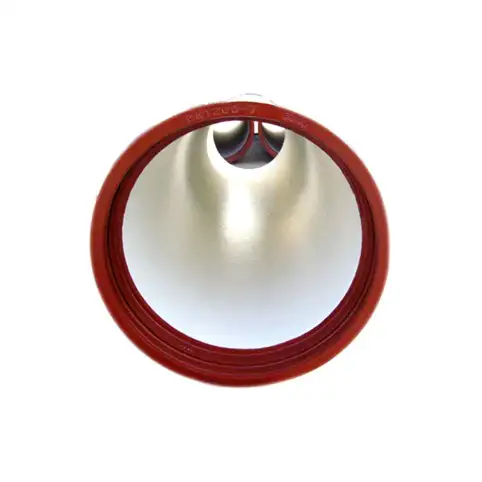
1. Flange Pressure Ratings Explained
The pressure rating of a flange indicates the maximum pressure it can handle at a specific temperature. It’s essential to note that the “Class” designation (e.g., Class 125 or Class 150) does not directly correspond to the pressure rating in psi. Instead, it represents a standard classification that, when combined with temperature, determines the flange’s pressure capacity.
Class 125 Flanges:
-
Pressure Rating: At ambient temperatures (approximately 100°F), Class 125 flanges are typically rated for 125 psi. However, this rating can vary based on material and specific standards.
-
Temperature Considerations: As temperature increases, the pressure rating decreases. For instance, at higher temperatures, the allowable pressure for Class 125 flanges diminishes.
Class 150 Flanges:
-
Pressure Rating: Class 150 flanges generally have a higher pressure rating than Class 125. For example, at ambient temperatures, they might be rated for 150 psi or more, depending on material and standards.
-
Temperature Considerations: Similar to Class 125, the pressure rating of Class 150 flanges decreases with rising temperatures.
Comparison Table:
Flange Class | Ambient Temperature Pressure Rating | Pressure Rating at Higher Temperatures |
---|---|---|
Class 125 | 125 psi | Decreases with temperature increase |
Class 150 | 150 psi | Decreases with temperature increase |
2. Material Composition and Strength
The material from which a flange is made significantly impacts its strength and pressure rating.
Class 125 Flanges:
-
Materials: Often made from cast iron, which offers good strength but is more brittle compared to other materials.
-
Strength: Suitable for moderate pressure applications but may not perform well under high-stress conditions.
Class 150 Flanges:
-
Materials: Typically constructed from stronger materials like ductile iron or carbon steel.
-
Strength: Provides higher tensile strength and is more resilient under varying pressure conditions.
Material Comparison Table:
Flange Class | Common Materials | Tensile Strength |
---|---|---|
Class 125 | Cast Iron | Moderate |
Class 150 | Ductile Iron, Carbon Steel | High |
3. Temperature Considerations
Temperature plays a pivotal role in determining the pressure rating of flanges.
-
Class 125 Flanges: As temperature increases, the pressure rating decreases. For instance, at higher temperatures, the material may soften, leading to a reduced ability to withstand pressure.
-
Class 150 Flanges: While temperature still affects pressure rating, Class 150 flanges are generally more resistant to temperature-induced pressure reductions due to their superior material properties.
Temperature vs. Pressure Rating Graph:
Note: A graph depicting the inverse relationship between temperature and pressure rating for both flange classes would be included here.
4. Design and Dimensional Differences
While both Class 125 and Class 150 flanges serve similar functions, their design and dimensions can differ.
-
Bolt Holes: The number and size of bolt holes may vary, affecting the flange’s compatibility with certain piping systems.
-
Face Type: Class 150 flanges might have a raised face, providing a better seal compared to the flat face of Class 125 flanges.
Dimensional Comparison Table:
Feature | Class 125 Flanges | Class 150 Flanges |
---|---|---|
Bolt Holes | Fewer, smaller | More, larger |
Face Type | Flat | Raised |
Thickness | Thinner | Thicker |
5. Applications and Industry Use Cases
The choice between Class 125 and Class 150 flanges often depends on the specific requirements of the application.
Class 125 Flanges:
-
Applications: Suitable for low to moderate pressure systems, such as water distribution networks and certain HVAC systems.
-
Industries: Commonly used in municipal water systems and residential plumbing.
Class 150 Flanges:
-
Applications: Ideal for higher pressure systems, including industrial piping, chemical processing, and oil & gas pipelines.
-
Industries: Widely used in petrochemical, power generation, and manufacturing industries.
Application Comparison Table:
Application Type | Class 125 Flanges | Class 150 Flanges |
---|---|---|
Water Distribution | Yes | Yes |
HVAC Systems | Yes | Yes |
Industrial Piping | No | Yes |
Chemical Processing | No | Yes |
Oil & Gas Pipelines | No | Yes |
6. Installation and Maintenance Considerations
Proper installation and maintenance are crucial for ensuring the longevity and performance of flanges.
-
Class 125 Flanges: Due to their material properties, they may require more frequent inspections and maintenance to prevent failures.
-
Class 150 Flanges: Their robust construction allows for longer intervals between maintenance checks, but they still require regular inspections to ensure integrity.
Maintenance Frequency Comparison Table:
Flange Class | Recommended Inspection Interval |
---|---|
Class 125 | More frequent |
Class 150 | Less frequent |
7. Cost Analysis
Cost is often a deciding factor when choosing between flange classes.
-
Class 125 Flanges: Generally more affordable due to the use of less expensive materials and simpler designs.
-
Class 150 Flanges: Higher initial cost but may offer better long-term value due to their durability and suitability for high-pressure applications.
Cost Comparison Table:
Flange Class | Initial Cost | Long-Term Value |
---|---|---|
Class 125 | Lower | Moderate |
Class 150 | Higher | Higher |
8. Frequently Asked Questions (FAQs)
Q1: Can Class 125 and Class 150 flanges be used interchangeably?
Answer: While both flange classes serve similar functions, they are not always interchangeable. The pressure rating, material strength, and design differences can affect their performance in certain applications. It’s essential to consult with industry standards and professionals before making substitutions.
Q2: How does temperature affect the pressure rating of flanges?
Answer: As temperature increases, the material properties of the flange can change, leading to a decrease in its ability to withstand pressure. This is why pressure ratings are often specified at a standard temperature, typically around 100°F.
Q3: Are there specific industries that prefer Class 150 flanges over Class 125?
Answer: Yes, industries such as oil & gas, chemical processing, and power generation often require the higher pressure ratings and material strength offered by Class 150 flanges for their high-pressure systems.
Q4: What factors should be considered when choosing between Class 125 and Class 150 flanges?
Answer: Considerations include the operating pressure and temperature of the system, the material compatibility, the flange dimensions, and the specific requirements of the application.
Q5: Can the pressure rating of a flange be increased?
Answer: The pressure rating is primarily determined by the flange’s material and design. While certain modifications might enhance performance, it’s crucial to adhere to established standards and consult with professionals before attempting to alter pressure ratings.
Q6: Where can I find more detailed specifications for Class 125 and Class 150 flanges?
Answer: Detailed specifications can be found in the ASME B16.1 and ASME B16.5 standards, which provide comprehensive information on flange dimensions, materials, and pressure-temperature ratings.