ASTM A536 Grade 65-45-12 ductile iron typically undergoes annealing heat treatment to achieve its optimal balance of strength and ductility. This process involves heating the iron to 1,650–1,750°F (900–955°C), holding at temperature to transform the microstructure, then slowly cooling to reduce hardness and improve machinability. The result is a ferritic matrix with embedded graphite nodules, delivering the specified 65 ksi tensile strength, 45 ksi yield strength, and 12% elongation. This treatment ensures superior impact resistance and flexibility, making it ideal for pressure pipes, automotive components, and heavy machinery. Learn how heat treatment refines ductile iron for demanding industrial applications.
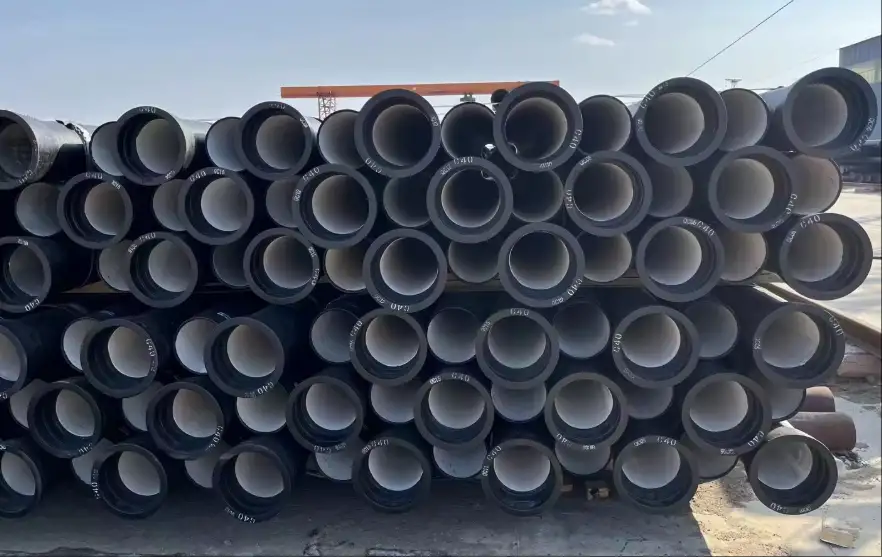
1. Introduction: Understanding ASTM A536 Grade 65-45-12
ASTM A536 is a widely recognized standard specification for ductile iron castings, and it includes various grades based on mechanical properties. One of the most commonly used grades is 65-45-12, which indicates specific tensile strength, yield strength, and elongation properties of the material. Heat treatment is a critical process for improving these mechanical properties, ensuring that ductile iron components meet the rigorous demands of various industrial applications.
2. What is Heat Treatment?
Heat treatment refers to a controlled process used to alter the physical and sometimes chemical properties of a material, typically metal. The purpose of heat treatment is to achieve the desired balance of hardness, strength, toughness, and ductility. For ductile iron, heat treatment can significantly improve its mechanical performance, making it suitable for more demanding applications.
The heat treatment process typically involves heating the material to a specific temperature, maintaining that temperature for a set period, and then cooling the material in a controlled manner. The goal is to enhance properties such as tensile strength, elongation, impact resistance, and wear resistance.
3. ASTM A536 Grade 65-45-12 Overview
Chemical Composition of ASTM A536 Grade 65-45-12
The chemical composition of ASTM A536 grade 65-45-12 ductile iron is designed to provide a balance of strength, flexibility, and resistance to wear. The typical composition includes:
Element | Range |
---|---|
Carbon (C) | 3.00% – 3.50% |
Silicon (Si) | 2.00% – 2.80% |
Manganese (Mn) | 0.50% – 1.00% |
Phosphorus (P) | Max 0.10% |
Sulfur (S) | Max 0.08% |
Magnesium (Mg) | 0.03% – 0.05% |
This composition, particularly the presence of magnesium, is crucial in forming the nodular graphite structure that gives ductile iron its unique properties.
Mechanical Properties of ASTM A536 Grade 65-45-12
-
Tensile Strength: 65 ksi (448 MPa)
-
Yield Strength: 45 ksi (310 MPa)
-
Elongation: 12%
These properties make ASTM A536 grade 65-45-12 suitable for a wide range of applications, especially in scenarios where a combination of strength and ductility is required.
4. The Importance of Heat Treatment for ASTM A536 Grade 65-45-12
Heat treatment is essential for optimizing the mechanical properties of ASTM A536 grade 65-45-12. While the material naturally possesses good strength and elongation, the heat treatment process helps to further enhance its performance.
Key benefits of heat treatment include:
-
Increased tensile strength: Heat treatment can improve the material’s ability to withstand stress and load.
-
Improved hardness: Controlled heating and cooling increase the hardness, making the material more resistant to wear and abrasion.
-
Enhanced toughness: The process improves the ability of the material to absorb energy without fracturing, which is especially important in high-impact applications.
5. Heat Treatment Process for ASTM A536 Grade 65-45-12
The heat treatment of ASTM A536 grade 65-45-12 generally involves the following stages:
Pre-Heating
Before the actual heat treatment process begins, the ductile iron is preheated to a lower temperature. This helps to reduce thermal shock and ensure uniform heating throughout the material. Pre-heating temperatures typically range from 500°F to 1000°F (260°C to 538°C).
Austenitizing
Austenitizing is the process of heating the ductile iron to a temperature at which the iron becomes austenitic (usually between 1600°F to 1700°F or 871°C to 927°C). This allows the iron to undergo a phase transformation, making it more malleable and easier to manipulate during subsequent cooling processes.
Quenching
After austenitizing, the material is rapidly cooled, or quenched, in water, oil, or air. This rapid cooling helps to lock in the desired microstructure, increasing hardness and tensile strength. Quenching is critical in achieving the necessary strength for industrial applications.
Tempering
Tempering involves reheating the material to a lower temperature (typically between 600°F and 1000°F or 316°C to 538°C) after quenching. This process reduces brittleness and improves toughness while maintaining a high level of hardness and strength.
6. Impact of Heat Treatment on Mechanical Properties
The heat treatment process has a direct impact on the following mechanical properties:
Tensile Strength
Heat treatment increases the tensile strength of ASTM A536 grade 65-45-12, allowing it to withstand higher levels of stress without failure. This is especially important in applications such as water pipelines, industrial machinery, and automotive components.
Yield Strength
The yield strength, or the stress at which the material starts to deform permanently, is also increased through heat treatment. This makes the material more resistant to deformation under load.
Elongation and Toughness
The elongation, or the material’s ability to stretch before breaking, is influenced by the tempering stage of heat treatment. While the quenching process increases hardness, tempering helps to maintain a balance between strength and ductility. A well-tempered ductile iron can absorb more energy before fracturing, which is crucial in high-impact environments.
7. Heat Treatment and Corrosion Resistance
While heat treatment primarily affects the mechanical properties of ductile iron, it also has an indirect effect on corrosion resistance. During the heat treatment process, the material’s surface may undergo changes that help to reduce its susceptibility to corrosion. However, additional protective coatings or surface treatments may be required for applications in highly corrosive environments, such as underground pipelines or marine applications.
8. Comparing Heat Treatment with Other Ductile Iron Grades
Here’s a comparison of ASTM A536 grade 65-45-12 with other common ductile iron grades:
Grade | Tensile Strength (ksi) | Yield Strength (ksi) | Elongation (%) | Common Applications |
---|---|---|---|---|
65-45-12 | 65 | 45 | 12 | Water pipes, sewage systems |
80-55-06 | 80 | 55 | 6 | Heavy machinery, automotive |
100-70-03 | 100 | 70 | 3 | Structural components, industrial |
60-40-18 | 60 | 40 | 18 | Light-duty engineering applications |
As the table shows, different grades offer different balances of tensile strength, yield strength, and elongation, which influence their suitability for specific applications. Heat treatment can further optimize these properties for demanding environments.
9. Applications of ASTM A536 Grade 65-45-12 After Heat Treatment
After undergoing heat treatment, ASTM A536 grade 65-45-12 ductile iron is suitable for use in a variety of industrial and infrastructure applications, including:
-
Piping systems for water, sewage, and gas.
-
Automotive components like gears, crankshafts, and other critical parts.
-
Heavy machinery parts that require both high strength and toughness.
-
Structural components in construction and infrastructure projects.
10. Frequently Asked Questions (FAQs)
1. How does heat treatment affect the performance of ASTM A536 grade 65-45-12?
Heat treatment significantly enhances the mechanical properties of ASTM A536 grade 65-45-12. By controlling the heating and cooling rates, heat treatment increases tensile strength, yield strength, and hardness, making the material more suitable for high-stress applications. Additionally, it helps balance toughness and ductility, allowing the material to withstand both high loads and impacts.
2. What is the role of quenching in heat treatment?
Quenching is a critical step in the heat treatment process that involves rapid cooling of the material after austenitizing. This process hardens the material by preventing the formation of soft microstructures and promoting the formation of martensite. Quenching increases tensile strength but can make the material more brittle, which is why tempering is often performed afterward to restore toughness.
3. Can heat treatment improve the corrosion resistance of ductile iron?
While heat treatment can slightly improve the corrosion resistance of ductile iron, it is not a substitute for protective coatings or other surface treatments. Ductile iron, particularly after heat treatment, still needs additional protection in highly corrosive environments, such as underground or marine applications, to ensure long-term durability.
4. How does heat treatment influence the elongation of ASTM A536 65-45-12?
The elongation of ASTM A536 65-45-12 can be impacted by the heat treatment process, specifically during tempering. While quenching increases strength and hardness, tempering improves ductility and elongation. The final elongation percentage, which is 12% for this grade, indicates the material’s ability to stretch before breaking, making it suitable for applications where flexibility is necessary.
5. What industries commonly use heat-treated ASTM A536 grade 65-45-12?
Industries that require materials with high strength, toughness, and durability commonly use heat-treated ASTM A536 grade 65-45-12. This includes sectors like water and sewage infrastructure, automotive manufacturing, heavy machinery, construction, and agricultural equipment.
11. Conclusion: The Value of Heat Treatment in ASTM A536 Grade 65-45-12
Heat treatment is essential for optimizing the performance of ASTM A536 grade 65-45-12 ductile iron. By enhancing its tensile strength, yield strength, elongation, and toughness, heat treatment makes this grade of ductile iron suitable for a wide range of industrial and infrastructure applications. Understanding the heat treatment process and its effects on material properties ensures that engineers and manufacturers can choose the appropriate material for specific applications, thereby maximizing the durability and reliability of their products.