When comparing ductile iron and carbon steel for corrosion resistance, ductile iron generally offers superior protection in various environmental conditions, especially in water and sewer infrastructure applications. This resistance is attributed to its unique composition and microstructure, which includes graphite nodules, enhancing its mechanical properties and providing better durability against corrosive elements. While carbon steel is widely used due to its cost-effectiveness, it tends to corrode faster when exposed to moisture, chemicals, and aggressive environmental conditions. Thus, the choice between ductile iron and carbon steel depends on the specific corrosion-related requirements of a given project.
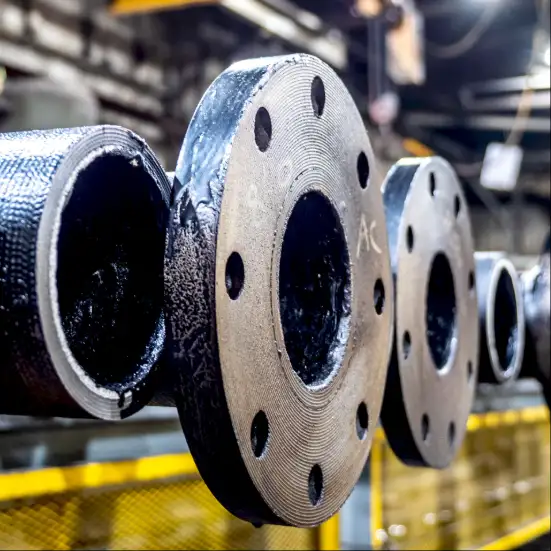
1. Corrosion Mechanisms: Ductile Iron vs. Carbon Steel
Corrosion in Ductile Iron:
Ductile iron is highly resistant to corrosion due to its unique combination of iron, carbon, and alloying elements. The corrosion resistance of ductile iron is mainly due to its microstructure, where graphite is present in spherical nodules. These nodules enhance the material’s strength and prevent the formation of large, brittle flakes of graphite, which are commonly found in gray cast iron. Ductile iron forms a protective oxide layer when exposed to water or moisture, preventing further corrosion.
Corrosion in Carbon Steel:
Carbon steel, on the other hand, is more susceptible to corrosion because of its relatively high carbon content and lack of alloying elements that prevent oxidation. The material is prone to rust when exposed to oxygen and moisture, forming iron oxide (rust), which deteriorates the steel over time. In acidic or salty environments, carbon steel corrodes much faster, which is why it is typically coated or treated with protective coatings to reduce its corrosion rate.
Comparison of Corrosion Mechanisms:
Property | Ductile Iron | Carbon Steel |
---|---|---|
Corrosion Resistance | Excellent resistance to corrosion in water, soil, and aggressive chemicals. | Prone to rusting when exposed to moisture and oxygen. |
Corrosion Protection | Forms a passive protective oxide layer. | Requires external coatings or galvanizing to prevent rust. |
Durability | Longer lifespan, especially in harsh environments. | Shorter lifespan unless coated or treated. |
Applications | Common in water and sewer systems, pipe fittings, and industrial machinery. | Used in construction, automotive, and machinery, often requiring coatings. |
2. Factors Affecting Corrosion Resistance in Ductile Iron and Carbon Steel
Environmental Factors:
The primary environmental factors affecting the corrosion resistance of both materials include moisture levels, temperature, and the presence of chemicals such as salts or acids. Ductile iron’s corrosion resistance is enhanced in environments where rust would typically form on carbon steel due to its naturally occurring oxide layer. Carbon steel, in contrast, requires protective coatings or galvanization to function effectively in similar environments.
Surface Coatings and Treatments:
Both ductile iron and carbon steel can benefit from coatings that enhance their corrosion resistance. However, ductile iron generally requires fewer treatments as it has a better innate corrosion resistance compared to carbon steel. Carbon steel, on the other hand, requires coatings such as zinc galvanization, epoxy coatings, or paint to prevent rust formation.
Soil and Water Conditions:
The impact of soil and water conditions also plays a crucial role in corrosion resistance. Ductile iron pipes, for example, perform exceptionally well in soil with high moisture levels, as the corrosion process slows significantly. In comparison, carbon steel pipes used in similar conditions will experience rapid rust formation unless coated.
3. Durability and Longevity of Ductile Iron and Carbon Steel
Ductile Iron:
Ductile iron is known for its long-lasting durability, especially in challenging environments. It is less likely to suffer from fatigue, cracking, or failure due to corrosion. This makes it an ideal material for pipes, fittings, and infrastructure exposed to water, sewerage, and other corrosive conditions. With proper maintenance, ductile iron can last up to 100 years or more, depending on the application.
Carbon Steel:
While carbon steel is strong and can withstand considerable mechanical stress, it does not match ductile iron’s longevity in terms of corrosion resistance. The formation of rust over time leads to the deterioration of the material, which can significantly reduce its strength and structural integrity. With proper coating and maintenance, carbon steel can last 30-50 years, but its lifespan is heavily dependent on external factors.
Comparison of Durability:
Material | Durability | Lifespan (Under Normal Conditions) |
---|---|---|
Ductile Iron | High durability, excellent corrosion resistance. | 100 years or more with proper maintenance. |
Carbon Steel | Susceptible to corrosion, requires coatings. | 30-50 years with maintenance. |
4. Corrosion Resistance in Different Applications
Water and Sewer Systems:
Ductile iron is the preferred material for water and sewer systems, primarily because of its ability to withstand the harsh conditions these systems face. Whether buried in the ground or exposed to water, ductile iron pipes exhibit superior resistance to rust and degradation compared to carbon steel. Furthermore, the material’s ability to endure external and internal pressures ensures its dominance in water utility systems.
Industrial and Construction Uses:
In industries like construction and automotive, carbon steel is commonly used, but its lack of corrosion resistance often necessitates coatings. For example, carbon steel pipes are often coated with protective layers when used in environments with high moisture or chemical exposure. Ductile iron, while more durable, is not as widely used in industries where lightweight, flexible materials are preferred.
5. Economic Considerations: Cost of Ductile Iron vs. Carbon Steel
Material Costs:
Ductile iron is generally more expensive than carbon steel due to the manufacturing process and its superior corrosion resistance. However, the higher initial cost of ductile iron is offset by its longer lifespan and lower maintenance costs. Carbon steel, being cheaper, requires ongoing treatment to maintain its integrity in corrosive environments.
Maintenance and Lifecycle Costs:
While the upfront cost of carbon steel may be lower, its maintenance costs over time can add up, particularly in environments that are prone to rust and corrosion. On the other hand, ductile iron, though more expensive initially, requires less frequent maintenance and has a longer life cycle, leading to overall cost savings in the long term.
6. Best Practices for Preventing Corrosion in Both Materials
For Ductile Iron:
-
Proper installation techniques should be used to avoid mechanical stress, which can lead to cracks and damage.
-
Use of coatings such as cement mortar or epoxy can further improve the material’s resistance to aggressive environments.
-
Routine inspections and maintenance to ensure that the protective oxide layer remains intact.
For Carbon Steel:
-
Apply corrosion-resistant coatings like galvanization, powder coating, or epoxy to protect against rust.
-
Regular maintenance and inspections are essential to detect early signs of corrosion and prevent further damage.
-
Use in combination with corrosion inhibitors in water and industrial applications to extend the material’s lifespan.
Frequently Asked Questions (FAQs)
1. What is the primary difference between ductile iron and carbon steel in terms of corrosion resistance?
Ductile iron has a higher corrosion resistance than carbon steel due to its microstructure and natural oxide layer that forms when exposed to moisture. Carbon steel, on the other hand, is more susceptible to rusting and requires external coatings for protection.
2. Can carbon steel be used in water systems without protection against corrosion?
No, carbon steel should always be coated or treated when used in water systems to prevent rust formation. Without protective coatings, it will corrode rapidly, especially in moist or saline environments.
3. How long does ductile iron last compared to carbon steel?
Ductile iron can last up to 100 years or more with minimal maintenance, whereas carbon steel typically lasts 30-50 years, depending on environmental conditions and coating quality.
4. Is it cost-effective to use ductile iron despite its higher initial cost?
Yes, despite the higher initial cost, ductile iron proves to be more cost-effective in the long run due to its superior corrosion resistance, lower maintenance costs, and extended lifespan compared to carbon steel.
5. What are the common applications for ductile iron and carbon steel?
Ductile iron is commonly used in water and sewer systems, where corrosion resistance is critical, while carbon steel is widely used in construction, automotive, and industrial applications, often requiring protective coatings to extend its life in corrosive environments.
References:
Corrosion Control and Resistance of Ductile Iron Pipe – DIPRA
Corrosion Behavior of Carbon Steel – NACE International
EPA Guidelines on Corrosion Protection for Pipelines
Ductile Iron Pipe Standards and Performance – AWWA