SAE J434 is a standard developed by the Society of Automotive Engineers (SAE) that specifies the mechanical properties, microstructure requirements, and hardness ranges for ductile (nodular) iron castings used primarily in automotive and allied industries. Ductile iron, known for its excellent strength and ductility, is a preferred material in applications requiring durability and resistance to impact.
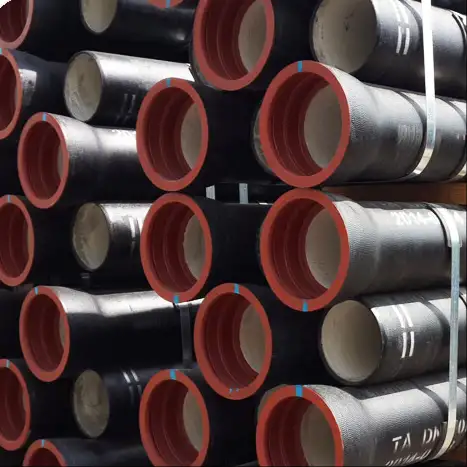
1. Material Composition and Microstructure
Ductile iron is characterized by the presence of spheroidal graphite nodules in its microstructure, which imparts enhanced mechanical properties compared to gray iron. The typical composition includes:
-
Carbon: 3.5–3.9%
-
Silicon: 2.2–2.8%
-
Manganese: 0.1–0.3%
-
Magnesium: 0.03–0.05%
-
Phosphorus and Sulfur: Kept to minimal levels to maintain ductility
The spheroidal graphite structure is achieved through the addition of nodulizing agents like magnesium during the casting process.
2. SAE J434 Grades and Mechanical Properties
SAE J434 defines several grades of ductile iron, each with specific mechanical properties suited for various applications.
Grade | Tensile Strength (MPa) | Yield Strength (MPa) | Elongation (%) | Brinell Hardness (HBW) | Microstructure |
---|---|---|---|---|---|
D400 (D4018) | 400 | 275 | 18 | 143–170 | Ferritic |
D450 (D4512) | 450 | 310 | 12 | 156–217 | Ferritic-Pearlitic |
D500 (D5006) | 500 | 345 | 6 | 187–229 | Ferritic-Pearlitic |
D550 (D5504) | 550 | 380 | 4 | 217–269 | Pearlitic-Ferritic |
D700 (D7003) | 700 | 450 | 3 | 241–302 | Pearlitic |
D800 | 800 | 480 | 2 | 255–311 | Pearlitic or Tempered Martensite |
Note: The mechanical properties are measured on separately cast test pieces of varying thickness as per the standard.
3. Applications of SAE J434 Ductile Iron
Due to its excellent mechanical properties, SAE J434 ductile iron is widely used in various industries:
-
Automotive Industry: Engine components, suspension parts, and brake systems.
-
Industrial Machinery: Gears, pulleys, and housings.
-
Agricultural Equipment: Plowshares, tractor parts, and irrigation components.
-
Construction: Manhole covers, pipes, and fittings.
4. Heat Treatment and Processing
Heat treatment processes are applied to ductile iron to achieve desired mechanical properties:
-
Annealing: Reduces hardness and improves ductility.
-
Normalizing: Refines grain structure and enhances strength.
-
Quenching and Tempering: Increases hardness and strength for high-stress applications.
It’s important to note that any heat treatment should be agreed upon between the manufacturer and the purchaser, as per SAE J434 guidelines.
5. Comparison with Other Standards
SAE J434 ductile iron grades can be compared with ASTM A536 grades:
SAE J434 Grade | ASTM A536 Equivalent |
---|---|
D400 (D4018) | 60-40-18 |
D450 (D4512) | 65-45-12 |
D500 (D5006) | 70-50-05 |
D550 (D5504) | 80-55-06 |
D700 (D7003) | 100-70-03 |
Note: While there are similarities, it’s essential to refer to each standard’s specific requirements for accurate comparisons.
6. Advantages of Using SAE J434 Ductile Iron
-
High Strength-to-Weight Ratio: Provides structural integrity without excessive weight.
-
Excellent Ductility: Allows for deformation without fracture, essential in dynamic applications.
-
Good Machinability: Facilitates manufacturing processes like drilling and milling.
-
Cost-Effective: Offers a balance between performance and cost compared to other materials like steel.
7. Design Considerations
When designing components using SAE J434 ductile iron, consider the following:
-
Section Thickness: Thicker sections may require different grades to ensure uniform properties.
-
Stress Analysis: Evaluate the component’s load conditions to select the appropriate grade.
-
Corrosion Resistance: While ductile iron has good corrosion resistance, additional coatings may be necessary for harsh environments.
Frequently Asked Questions (FAQs)
Q1: What is the primary difference between SAE J434 ductile iron and gray iron?
A: The main difference lies in the graphite structure. Ductile iron has spheroidal graphite nodules, providing enhanced ductility and strength, whereas gray iron contains flake graphite, which makes it more brittle.
Q2: Can SAE J434 ductile iron be welded?
A: Welding ductile iron is challenging due to its graphite content, which can lead to cracking. However, with proper preheating and post-weld heat treatment, welding is possible for certain applications.
Q3: How does heat treatment affect the properties of SAE J434 ductile iron?
A: Heat treatment can significantly alter the mechanical properties of ductile iron. For instance, annealing can increase ductility, while quenching and tempering can enhance strength and hardness. The specific effects depend on the treatment parameters and the initial microstructure of the iron.
Q4: What are the considerations for machining SAE J434 ductile iron?
A: Ductile iron’s machinability is influenced by its microstructure. Ferritic grades are easier to machine, while pearlitic grades may require more robust tooling. Proper selection of cutting tools and parameters is essential for efficient machining.
Q5: Is SAE J434 ductile iron suitable for high-temperature applications?
A: Ductile iron can withstand moderate temperatures, but prolonged exposure to high temperatures may degrade its mechanical properties. For high-temperature applications, materials specifically designed for such conditions are recommended.
Q6: How does the choice of SAE J434 grade affect the performance of a component?
A: Selecting the appropriate grade ensures that the component meets the required mechanical properties for its intended application. For example, D400 is suitable for applications requiring high ductility, while D800 is chosen for high-strength requirements.
References:
- SAE J434 Standard – Society of Automotive Engineers (SAE)
- Ductile Iron – Wikipedia
- ASTM A536 Standard Specification for Ductile Iron Castings – ASTM International
- ISO 1083:2011 – Spheroidal Graphite Cast Irons — Classification
- National Institute of Standards and Technology (NIST) – Materials Measurement Laboratory