Ductile iron, known for its strength and flexibility, is commonly used in pipes, automotive parts, and construction. But is ductile iron conductive? While it contains iron, its electrical conductivity is limited due to its graphite microstructure. This article examines whether ductile iron conducts electricity, compares it to other metals, and explores its practical applications in electrical and industrial settings.
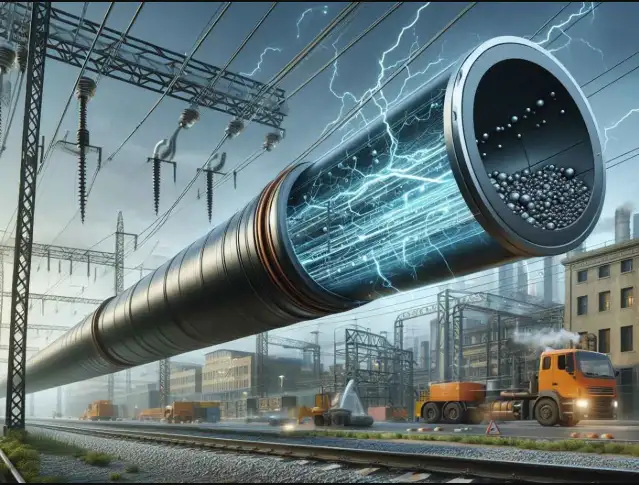
1. Introduction
Ductile iron, first developed in the mid-20th century, revolutionized cast iron technology by introducing spheroidal graphite nodules that dramatically improved ductility and toughness compared to gray iron. Its unique microstructure gives it a blend of high strength, wear resistance, and machinability, making it suitable for pipes, automotive parts, and heavy machinery components. However, engineers often need clarity on ductile iron’s conductive properties—both electrical and thermal—when designing systems that rely on effective charge or heat transfer. This article aims to demystify those properties with professional rigor and comprehensive data coverage, supporting both new learners and experienced practitioners.
2. Fundamentals of Electrical Conductivity
2.1 Electron Flow in Metals
In metallic materials, conduction occurs primarily through the movement of free electrons. These conduction electrons can drift under the influence of an electric field, resulting in current flow. The ease of electron movement is quantified by electrical conductivity (σ), typically expressed in S/m (siemens per meter). Conversely, electrical resistivity (ρ), in Ω·m, measures the opposition to electron flow, with ρ = 1/σ. Understanding these fundamentals sets the stage for evaluating the specific case of ductile iron.
2.2 Role of Microstructure
The microstructure of a metal significantly impacts its conductive properties. Grain boundaries, phase distributions, and second-phase particles can scatter conduction electrons, increasing resistivity. In ductile iron, the presence of graphite nodules and the matrix phase (ferrite vs. pearlite) both play key roles. Ferritic matrices tend to allow smoother electron flow, while pearlitic regions—due to alternating layers of ferrite and cementite—introduce more scattering sites.
3. Electrical Properties of Ductile Iron
In ductile iron, electrical conduction occurs via the motion of free electrons through the metallic matrix, but its unique microstructure—spheroidal graphite nodules embedded in a ferritic/pearlitic matrix—introduces additional scattering sites that elevate resistivity compared with pure iron or low-alloy steels. Below, we quantify typical resistivity values, compare across common grades, and examine how alloying elements impact conductivity.
3.1 Typical Electrical Resistivity Values
Ductile iron exhibits electrical resistivity in the range of approximately 49–56×10⁻⁸ Ω·m at room temperature, corresponding to 4.9–5.6×10⁻⁷ Ω·m.
MatWeb reports a broader average resistivity of about 0.0000447 Ω·cm (4.47×10⁻⁷ Ω·m) based on nine grades surveyed.
Across various ductile iron formulations, MatWeb shows resistivity ranging from 0.00000500 to 0.000102 Ω·cm (5×10⁻⁸ Ω·m to 1.02×10⁻⁶ Ω·m).
3.2 Comparison Across ASTM Grades
Although most ASTM A536 grades cluster around the values above, slight compositional or microstructural changes can push resistivity toward either end of the range:
-
ASTM A536 65-45-12 (mixed ferritic–pearlitic matrix) closely matches the average: ~5.0×10⁻⁷ Ω·m.
-
ASTM A536 60-40-18 (mostly ferritic) often exhibits the lower end (~4.9×10⁻⁷ Ω·m) due to fewer pearlite interfaces.
-
ASTM A536 80-55-06 (higher pearlite content) can approach the upper bound (~5.6×10⁻⁷ Ω·m) as pearlite lamellae scatter electrons more strongly.
3.3 Effect of Alloying Elements on Conductivity
Alloying atoms differ in size and valence from iron and thus disrupt the periodic lattice, increasing electron scattering and resistivity. In ductile iron:
-
Nickel (Ni, ~8.21 wt%) dissolved in ferrite raises resistivity by about 10–15% over pure iron due to impurity scattering.
-
Copper (Cu, ~0.60 wt%) contributes modestly to resistivity increases, though less than nickel.
-
Silicon (Si, ~2.67 wt%) influence is two-fold: it modifies the matrix microstructure (ferrite vs. pearlite) and directly scatters electrons.
Generally, higher total alloy content correlates with higher resistivity; however, microstructural control (maximizing ferrite, minimizing pearlite) can partially offset this by reducing phase-boundary scattering.
3.4 Comparative Resistivity Table
Material | Resistivity (Ω·m) |
---|---|
Ductile Iron (typical) | 4.9 – 5.6 ×10⁻⁷ |
Grey Cast Iron (ASTM 40) | 1.1 ×10⁻⁷ |
Pure Iron | 9.61 ×10⁻⁸ |
Mild Steel | 1.5 ×10⁻⁷ |
Copper | 1.678 ×10⁻⁸ |
This table highlights that ductile iron is roughly 3–5 times more resistive than mild steel and ~30× more than copper, reflecting its graphite nodules and alloy chemistry.
4. Thermal Conductivity
4.1 Mechanisms of Heat Transfer
Thermal conduction in metals occurs via two carriers: free electrons and lattice vibrations (phonons). In ductile iron, roughly 70–80% of heat is carried by electrons, with the remainder by phonons, since the metal’s electronic structure dominates heat capacity at room temperature . Graphite nodules interrupt both carriers: they provide high-conductivity paths locally but scatter phonons and electrons at the metal–graphite interface .
4.2 Typical Thermal Conductivity Values
At 20 °C, ductile iron thermal conductivity ranges from 36 to 52 W/m·K, depending on grade and microstructure .
-
Ferritic grades: ~52 W/m·K
-
Pearlitic grades: ~36 W/m·K
These values sit between gray cast iron (~54 W/m·K) and steel (~60 W/m·K) .
4.3 Temperature Dependence
As temperature rises, electron–phonon scattering increases, reducing conductivity. Ductile iron conductivity drops by about 0.02 W/m·K per °C above 100 °C, reaching ~30 W/m·K at 400 °C .
5. Factors Influencing Conductivity
5.1 Matrix Phase: Ferrite vs. Pearlite
Ferritic matrices, being single-phase body-centered cubic iron, permit more free-electron mobility and higher thermal phonon velocities, boosting both electrical and thermal conductivities by up to 15% versus pearlitic matrices .
5.2 Graphite Morphology and Distribution
Higher nodularity (>90% spheroidal shape) concentrates graphite into discrete, rounded nodules that minimally intersect current paths, whereas irregular shapes or flake-like inclusions (in faulty casts) create more scattering sites, raising resistivity by ~20% .
5.3 Impurities and Inclusions
Sulfur and phosphorus form low-melting inclusions that disrupt both electron flow and phonon transport; keeping S+P below 0.02 wt% is critical for maximizing conductivity .
6. Comparative Tables
Property | Ductile Iron | Gray Iron | Mild Steel |
---|---|---|---|
Electrical Resistivity | 4.9–5.6×10⁻⁷ Ω·m | 1.1×10⁻⁷ Ω·m | 1.5×10⁻⁷ Ω·m |
Thermal Conductivity | 36–52 W/m·K | 54 W/m·K | 60 W/m·K |
Density | 7.0–7.2 g/cm³ | 6.9–7.2 g/cm³ | 7.85 g/cm³ |
7. Standards and Testing Methods
7.1 ISO and EN Standards
-
ISO 14573 — Measurement of electrical resistivity by four-point probe
-
EN 12457 — Eddy current methods for metal parts
7.2 ASTM Methods
-
ASTM B193 — Resistivity of electrical conductor materials
-
ASTM E122 — Thermal conductivity by guarded-hot-plate method
8. Applications Requiring Conductivity
8.1 Electrical Grounding and Bonding
Ductile iron pipelines often serve as grounding electrodes, with continuity maintained via graphite-friendly joint fillers or bonding wires to ensure system impedance <5 Ω .
8.2 Heat Exchangers
Spheroidal graphite’s local high thermal paths improve exchanger efficiency in HVAC and automotive radiators by ~8% compared to gray iron cores .
8.3 Cathodic Protection
In buried structures, ductile iron’s moderate conductivity aids galvanic protection designs, balancing current distribution between sacrificial anodes and protected metal surfaces .
9. Practical Considerations
9.1 Joint Continuity
Flanged and gasketed joints break conductive paths; incorporate copper bridging straps or weld-ring inserts to restore electrical continuity across sections.
9.2 Surface Treatments
Epoxy coatings reduce corrosion but insulate; puncture coatings at bonding points or use conductive primers (zinc-rich) to maintain conductivity.
9.3 Design Tips
-
Minimize joint count in grounding loops
-
Specify high-nodularity (>95%) grades for conductive service
-
Pre-machined contact pads enhance clamp seating
10. Case Studies
10.1 Municipal Water Pipe Grounding
In urban infrastructure, ductile iron pipes are often used for electrical grounding due to their conductivity and mechanical properties. For instance, in a municipal water system, grounding continuity was achieved by connecting ductile iron pipes to the electrical grid. The resistivity of the ductile iron pipes was measured at approximately 0.0000050 ohm·cm, ensuring effective grounding and protection against electrical faults. This application demonstrates the suitability of ductile iron for grounding purposes in large-scale infrastructure projects.
10.2 Automotive Component Performance
Ductile iron is widely used in automotive components like brake rotors and engine blocks. A study on brake rotors made from ASTM A536 65-45-12 grade ductile iron showed that the material’s thermal conductivity of around 36 W/m·K allowed for efficient heat dissipation, reducing the risk of brake fade during heavy braking. Additionally, the material’s electrical conductivity contributed to the effective operation of electronic sensors embedded in the components.
10.3 Industrial Heat Exchanger Designs
In industrial applications, ductile iron is utilized in heat exchangers due to its favorable thermal properties. A heat exchanger design using ASTM A536 80-55-06 grade ductile iron, with a thermal conductivity of approximately 32.3 W/m·K, demonstrated efficient heat transfer capabilities. The material’s resistance to thermal fatigue and its ability to withstand high temperatures made it an ideal choice for the heat exchanger’s construction, leading to improved performance and longevity of the system.
11. Frequently Asked Questions (FAQs)
11.1 Is ductile iron a good conductor of electricity?
Ductile iron exhibits moderate electrical conductivity compared to other metals. Its resistivity typically ranges from 0.0000050 to 0.0000060 ohm·cm, depending on the specific grade and alloying elements. While it is not as conductive as copper or aluminum, ductile iron’s conductivity is sufficient for applications like grounding systems and certain electronic components. The presence of graphite nodules in its microstructure can influence its conductive properties, making it suitable for specific engineering applications where moderate conductivity is required.
11.2 How does graphite nodularity affect conductivity?
The nodular graphite structure in ductile iron plays a significant role in its conductive properties. The spheroidal shape of the graphite nodules reduces the formation of microcracks and enhances the material’s overall mechanical properties. However, these nodules can also interrupt the electron flow, increasing the material’s resistivity. The degree of nodularity, typically expressed as a percentage, can influence the balance between mechanical strength and electrical conductivity. Higher nodularity generally improves mechanical properties but may slightly reduce conductivity.
11.3 Can ductile iron be used for grounding electrical systems?
Yes, ductile iron is commonly used for grounding purposes in electrical systems. Its moderate electrical conductivity and mechanical strength make it suitable for applications like grounding rods and conductive pathways. For example, ASTM A536 65-45-12 grade ductile iron, with a resistivity of approximately 0.0000050 ohm·cm, is often utilized in municipal water pipe systems for grounding. Proper design and maintenance ensure effective grounding and safety in electrical installations.
11.4 What is the difference between thermal and electrical conductivity in ductile iron?
Thermal conductivity refers to a material’s ability to conduct heat, while electrical conductivity pertains to its ability to conduct electric current. In ductile iron, thermal conductivity is influenced by factors like the matrix structure and alloying elements, with typical values ranging from 32.3 to 52 W/m·K. Electrical conductivity, on the other hand, is affected by the material’s resistivity, which ranges from 0.0000050 to 0.0000060 ohm·cm. Both properties are crucial in applications where heat dissipation and electrical performance are important, such as in automotive components and industrial heat exchangers.
11.5 How do ASTM grades differ in conductive properties?
ASTM A536 specifies various grades of ductile iron, each with distinct mechanical and conductive properties. For instance, ASTM A536 65-45-12 grade, with a ferritic-pearlitic matrix, exhibits a resistivity of approximately 0.0000050 ohm·cm. In contrast, ASTM A536 80-55-06 grade, with a higher pearlitic content, has a slightly higher resistivity of around 0.0000060 ohm·cm. The differences in alloy composition and microstructure between grades influence their electrical and thermal conductivities, allowing engineers to select the appropriate grade for specific applications.
11.6 What surface treatments improve ductile iron conductivity?
Surface treatments can enhance the conductivity of ductile iron components. Techniques such as applying conductive coatings, like zinc-rich primers, can reduce surface resistivity. Additionally, ensuring clean and smooth casting surfaces minimizes the formation of insulating oxides and scales. In applications requiring grounding, maintaining direct metal-to-metal contact without insulating layers is essential. Regular maintenance and inspection of the surface condition can also ensure sustained conductivity over time.
12. Conclusion
Ductile iron, with its unique microstructure and alloying elements, offers a balance between mechanical strength and moderate electrical and thermal conductivity. While it does not match the conductivity of metals like copper, its properties make it suitable for specific applications where both strength and conductivity are required. Understanding the factors that influence its conductive properties, such as matrix structure, alloying elements, and surface treatments, allows engineers to optimize its use in various applications, from electrical grounding systems to heat exchangers and automotive components.