Proper installation is crucial for the longevity and performance of ductile iron pipes. But is there a specific code governing their laying process? Yes, international and national standards, such as ISO 10804, AWWA C600, and IS 8329 (in India), provide detailed guidelines for ductile iron pipe installation.
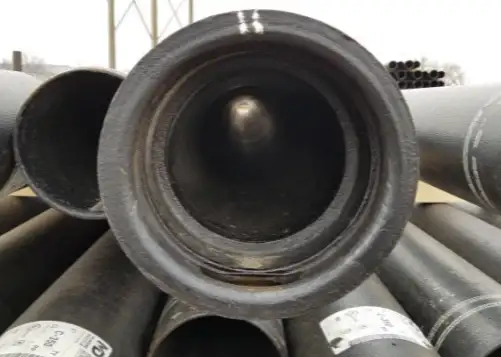
1. Introduction
Ductile iron pipes are a cornerstone of modern water and wastewater infrastructure due to their strength, durability, and resistance to corrosion. Proper installation is crucial to ensure the longevity and functionality of these pipelines. Adhering to established codes and standards during the laying process is essential for achieving optimal performance and compliance with regulatory requirements.
2. Overview of Ductile Iron Pipes
Ductile iron pipes are manufactured by adding small amounts of alloying elements to molten iron, resulting in a material with improved mechanical properties compared to traditional cast iron. These pipes are commonly used for potable water distribution, sewage systems, and fire protection lines. They are known for their strength, impact resistance, and longevity.
3. Importance of Adhering to Laying Codes
Adhering to established codes and standards during the laying of ductile iron pipes ensures:
-
Structural Integrity: Proper installation techniques prevent damage to the pipes and joints.
-
Safety: Compliance with codes minimizes the risk of accidents and failures.
-
Regulatory Compliance: Meeting local and international standards ensures legal compliance.
-
Operational Efficiency: Correct installation practices facilitate maintenance and repairs.
4. Key Codes and Standards for Ductile Iron Pipe Laying
ANSI/AWWA C600
The American National Standards Institute (ANSI) and the American Water Works Association (AWWA) developed the C600 standard, titled “Installation of Ductile-Iron Mains and Their Appurtenances.” This standard provides comprehensive guidelines on the installation of ductile iron pipelines, covering aspects such as:
-
Trenching: Specifications on trench dimensions and bedding materials.
-
Pipe Handling: Guidelines on lifting, lowering, and placing pipes to prevent damage.
-
Jointing: Instructions on the proper assembly of pipe joints to ensure leak-proof connections.
-
Backfilling: Recommendations on backfill materials and compaction to support the pipeline.
IS 12288
The Bureau of Indian Standards (BIS) developed IS 12288, titled “Code of Practice for Use and Laying of Ductile Iron Pipes.” This code provides guidelines specific to the Indian context, addressing factors such as:
-
Route Selection: Criteria for selecting the optimal route for pipeline installation.
-
Pipe Laying: Methods for laying pipes in various terrains, including urban and rural settings.
-
Jointing Techniques: Best practices for joining pipes to ensure leak-free connections.
-
Testing: Procedures for pressure testing and leak detection.
EN 545
The European Standard EN 545, titled “Ductile Iron Pipes, Fittings, Accessories and Their Joints for Water Pipelines,” provides specifications for the design, manufacture, and installation of ductile iron pipelines in Europe. Key aspects include:
-
Material Specifications: Requirements for the composition and mechanical properties of ductile iron.
-
Coatings: Standards for internal and external coatings to prevent corrosion.
-
Jointing Systems: Specifications for various jointing methods, including push-on and flanged joints.
-
Testing and Inspection: Guidelines for quality control and acceptance testing.
5. Installation Best Practices
To ensure the successful laying of ductile iron pipes, the following best practices should be observed:
-
Proper Trenching: Ensure trenches are of adequate depth and width to accommodate the pipe and provide sufficient cover.
-
Pipe Handling: Use appropriate lifting equipment and techniques to prevent damage to the pipes during transportation and installation.
-
Joint Assembly: Follow manufacturer instructions for joint assembly to achieve leak-proof connections.
-
Backfilling: Use suitable backfill materials and compact them in layers to provide uniform support to the pipeline.
-
Testing: Conduct pressure tests to verify the integrity of the installed pipeline.
6. Common Challenges and Solutions
Challenge 1: Uneven Bedding
Solution: Ensure that the trench bottom is level and free from debris before laying the pipe. Use suitable bedding materials to provide uniform support.
Challenge 2: Improper Jointing
Solution: Follow manufacturer guidelines for joint assembly and use the recommended jointing materials to ensure leak-proof connections.
Challenge 3: Inadequate Backfilling
Solution: Use suitable backfill materials and compact them in layers to provide uniform support and prevent settlement.
Challenge 4: Lack of Testing
Solution: Conduct pressure tests at specified intervals to verify the integrity of the installed pipeline.
7. Case Studies
Case Study 1: Urban Water Distribution
In a major metropolitan area, adherence to ANSI/AWWA C600 ensured the successful installation of a ductile iron water distribution system. Proper trenching, jointing, and testing procedures resulted in a reliable and durable pipeline.
Case Study 2: Rural Sewerage System
In a rural setting, following IS 12288 guidelines facilitated the efficient laying of a ductile iron sewerage system. Proper route selection and jointing techniques minimized disruptions and ensured system integrity.
Case Study 3: Industrial Fire Protection
In an industrial complex, compliance with EN 545 standards ensured the installation of a ductile iron fire protection system capable of withstanding high pressures and providing reliable service.
8. Frequently Asked Questions (FAQs)
8.1 What is the purpose of the ANSI/AWWA C600 standard?
The ANSI/AWWA C600 standard provides comprehensive guidelines for the installation of ductile iron mains and their appurtenances, ensuring structural integrity, safety, and regulatory compliance.
8.2 How does IS 12288 differ from other standards?
IS 12288 is tailored to the Indian context, addressing factors such as route selection, jointing techniques, and testing procedures specific to India.
8.3 Why is adherence to EN 545 important?
Adhering to EN 545 ensures that ductile iron pipelines meet European standards for material composition, coatings, jointing systems, and testing, resulting in reliable and durable infrastructure.
8.4 What are the consequences of not following these codes?
Failure to adhere to established codes can result in pipeline failures, safety hazards, regulatory non-compliance, and increased maintenance costs.
8.5 How can contractors ensure compliance with these codes?
Contractors can ensure compliance by familiarizing themselves with the relevant codes, following manufacturer guidelines, and conducting regular inspections and tests during installation.
8.6 Are there any updates to these standards?
Standards are periodically reviewed and updated to reflect advancements in materials, technology, and best practices. Contractors should stay informed about the latest revisions to ensure ongoing compliance.
9. Conclusion
Adhering to established codes and standards is crucial for the successful laying of ductile iron pipes. By following guidelines such as ANSI/AWWA C600, IS 12288, and EN 545, contractors can ensure the installation of reliable, durable, and safe pipelines that meet regulatory requirements and serve the needs of communities effectively.
References:
- ANSI/AWWA C600 – Installation of Ductile-Iron Mains and Their Appurtenances
- ISO 10804 – Ductile Iron Pipes for Water Supply
- Bureau of Indian Standards (BIS) – IS 12288: Code of Practice for Use and Laying of Ductile Iron Pipes
- EN 545 – Ductile Iron Pipes, Fittings, Accessories and Their Joints for Water Pipelines
- FEMA – Fire Protection and Ductile Iron Pipe Systems