Identifying the differences between cast iron and ductile iron involves examining physical properties, microstructure, and performance characteristics. While both are iron-based alloys, ductile iron’s spherical graphite inclusions give it superior strength and flexibility compared to the flake graphite structure of traditional cast iron.
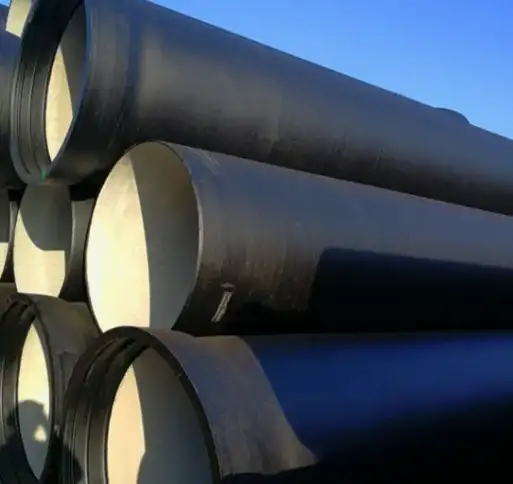
1. Introduction: Understanding Cast Iron and Ductile Iron
Iron, a material used for thousands of years in construction, engineering, and manufacturing, can be processed in different ways to achieve various properties. Among the most common forms of iron are cast iron and ductile iron. Although both are technically iron alloys, they differ significantly in composition, properties, and applications.
What is Cast Iron?
Cast iron refers to a group of iron-carbon alloys with a carbon content greater than 2%. The high carbon content makes cast iron easy to cast into molds, hence the name “cast” iron. This metal is known for its excellent castability, wear resistance, and ability to withstand high temperatures.
Types of Cast Iron:
-
Gray Cast Iron: The most common type, known for its graphite flake structure.
-
White Cast Iron: Characterized by a bright white fracture surface, typically used in applications requiring hardness.
-
Malleable Cast Iron: Heated and then cooled in a controlled process to make it more ductile.
-
Nodular Cast Iron (Ductile Iron): Cast iron with nodular graphite, offering superior strength and ductility.
What is Ductile Iron?
Ductile iron, often referred to as nodular cast iron or spheroidal graphite iron, is a type of cast iron that has been alloyed with small amounts of alloying elements like magnesium to promote the formation of spherical graphite structures. These spherical graphite particles improve the material’s strength, ductility, and toughness compared to traditional cast iron.
Properties of Ductile Iron:
-
Improved Ductility: Unlike traditional cast iron, ductile iron can bend and stretch under stress without breaking.
-
High Strength: Ductile iron has higher tensile strength, making it suitable for high-stress applications.
-
Better Fatigue Resistance: Due to its composition, ductile iron resists fatigue much better than gray cast iron.
2. Key Differences Between Cast Iron and Ductile Iron
Though both materials fall under the general category of “cast iron,” their physical, mechanical, and chemical properties vary significantly. Below is a detailed comparison of the two types of iron.
Property | Cast Iron | Ductile Iron |
---|---|---|
Graphite Structure | Flake-shaped graphite (gray cast iron) | Spherical graphite (nodular graphite) |
Tensile Strength | Lower strength compared to ductile iron | Higher tensile strength |
Ductility | Brittle and more prone to cracking | High ductility, can bend without breaking |
Fatigue Resistance | Poor fatigue resistance | Excellent fatigue resistance |
Machinability | Easier to machine due to brittleness | Slightly more difficult to machine, but still manageable |
Applications | Engine blocks, pipes, machinery parts | Auto parts, pipes, valves, heavy-duty applications |
Weight | Heavier in comparison due to brittleness | Lighter with higher strength-to-weight ratio |
3. Methods to Distinguish Cast Iron from Ductile Iron
Distinguishing cast iron from ductile iron can be challenging without the proper tools or knowledge. However, there are several methods to identify the differences, both visually and through testing.
Method 1: Visual Inspection
Cast Iron:
-
Fracture Surface: Gray cast iron, when fractured, exhibits a rough, gray surface with visible graphite flakes. These graphite flakes are responsible for the material’s brittle behavior.
-
Color: When broken, gray cast iron has a dull, gray appearance with visible inclusions of graphite.
Ductile Iron:
-
Fracture Surface: Ductile iron has a more shiny, ductile fracture surface with spherical graphite nodules visible under magnification.
-
Color: The breakage of ductile iron shows a smooth surface with minimal roughness and a shiny metallic color.
Method 2: Conducting a Bend Test
Ductile iron is more flexible than traditional cast iron. One of the easiest ways to distinguish the two materials is by performing a bend test.
-
Cast Iron: When subjected to a bending force, cast iron will break or crack almost immediately due to its brittleness.
-
Ductile Iron: Ductile iron will bend rather than crack or break, showing its superior flexibility.
Method 3: Magnetic Testing
Both cast iron and ductile iron are ferromagnetic, meaning they are attracted to magnets. However, ductile iron tends to have a stronger magnetic response due to its higher density and microstructure.
Method 4: Chemical Composition Analysis
By analyzing the chemical composition, you can accurately identify whether the material is cast iron or ductile iron. The key element to look for is magnesium.
-
Ductile Iron: Magnesium is added in small amounts (around 0.03-0.05%) to the molten iron to create the nodular graphite structure.
-
Cast Iron: Lacks significant amounts of magnesium and has higher levels of silicon.
This can be tested using a spectrometer or other analytical equipment.
4. Advantages of Ductile Iron Over Cast Iron
Ductile iron has several advantages over traditional cast iron, making it the preferred choice for many engineering applications. These benefits are primarily due to its improved mechanical properties.
Increased Strength and Toughness
Ductile iron is known for its excellent tensile strength, which is significantly higher than that of gray cast iron. This makes ductile iron suitable for high-stress applications, such as in the automotive and heavy-duty industries.
Better Durability and Fatigue Resistance
The spherical graphite structure in ductile iron increases its resistance to fatigue. It can withstand repeated stress and vibrations without cracking or failing, making it ideal for use in infrastructure such as pipelines, valves, and machinery parts.
Improved Ductility
The high ductility of ductile iron allows it to bend or stretch without breaking, making it much more flexible than cast iron. This property is particularly useful in applications that require impact resistance or those exposed to harsh conditions.
5. Common Applications of Cast Iron and Ductile Iron
Applications of Cast Iron:
-
Engine Blocks: Traditionally used in car engines for their ease of casting and good vibration dampening.
-
Pipes: Commonly used for sewer lines and water mains due to its high resistance to wear.
-
Machine Parts: Used for heavy machinery and parts that need to resist wear but not flexibility.
Applications of Ductile Iron:
-
Automotive Components: Ductile iron is increasingly used for high-performance car parts, including crankshafts, gears, and suspension components.
-
Pipes: Used in applications where high strength and resistance to corrosion are required, such as for water mains, sewage systems, and gas pipelines.
-
Valves and Fittings: Because of its high tensile strength and ductility, ductile iron is used in high-stress valve and fitting components.
-
Heavy Machinery: Used in parts like gears and housings for machinery exposed to high mechanical stress.
6. Frequently Asked Questions (FAQs)
Q1: Can ductile iron be welded like cast iron?
Answer: Ductile iron can be welded, but it requires specialized techniques and pre-heating processes to avoid cracking. Cast iron, on the other hand, is more challenging to weld due to its brittleness and tendency to form cracks during the welding process. The primary difficulty in welding ductile iron lies in controlling the cooling rate, which can cause the formation of brittle phases in the material if not managed properly.
Welding ductile iron usually requires pre-heating the part to prevent the rapid cooling that could cause the material to crack. The welding process should also involve using specific filler materials designed for ductile iron to ensure a strong bond.
Additional Tips:
-
For cast iron, it’s often better to use brazing or a similar process instead of welding.
-
When welding ductile iron, ensure the heat source is controlled, and post-weld heat treatment may be necessary.
Q2: Why is ductile iron preferred over cast iron in certain applications?
Answer: Ductile iron is preferred over cast iron in applications where flexibility, strength, and durability are essential. The spherical graphite structure in ductile iron provides superior resistance to cracking, better impact resistance, and greater fatigue strength, which makes it ideal for use in high-stress situations. For example, in automotive applications, ductile iron is used for parts like crankshafts and suspension components, which experience significant forces and vibrations.
In contrast, cast iron’s brittleness makes it prone to cracking under stress, which limits its use in such demanding applications. The higher tensile strength of ductile iron also means it can handle heavier loads without deforming, providing better performance in pipes, valves, and heavy-duty machinery.
In Summary:
-
Ductile iron is more versatile and reliable for applications where the material will be exposed to stresses or vibrations.
-
Cast iron remains suitable for applications where high wear resistance is more important than flexibility.
Q3: How do I determine whether a pipe is made of cast iron or ductile iron?
Answer: The best way to determine whether a pipe is made of cast iron or ductile iron is to look for markings on the pipe or perform a visual inspection. Ductile iron pipes are often marked with “DI” or similar notations. If the markings are not visible, a break test or magnetic test may be necessary to distinguish the two materials.
Conducting a Break Test:
-
Cast Iron: Will fracture and break under stress, creating a sharp, brittle fracture.
-
Ductile Iron: Will bend before breaking, offering more resilience under stress.
Magnetic Test:
-
Cast Iron: More brittle and slightly weaker magnetic response.
-
Ductile Iron: Stronger magnetic attraction due to its higher density and more uniform composition.
7. Video Tutorial
Watch this YouTube video to see step-by-step methods for distinguishing cast iron from ductile iron, including visual inspection techniques, break tests, and more:
Conclusion
Distinguishing cast iron from ductile iron is essential for selecting the right material for various industrial, automotive, and infrastructural applications. By understanding the key differences in their composition, properties, and applications, you can make more informed decisions when working with these materials.