Ductile iron pipes are widely used in water and wastewater systems due to their strength and durability. Properly connecting these pipes is crucial to ensure leak-free and long-lasting installations. Various joint types are available, each suited for specific applications and installation conditions.
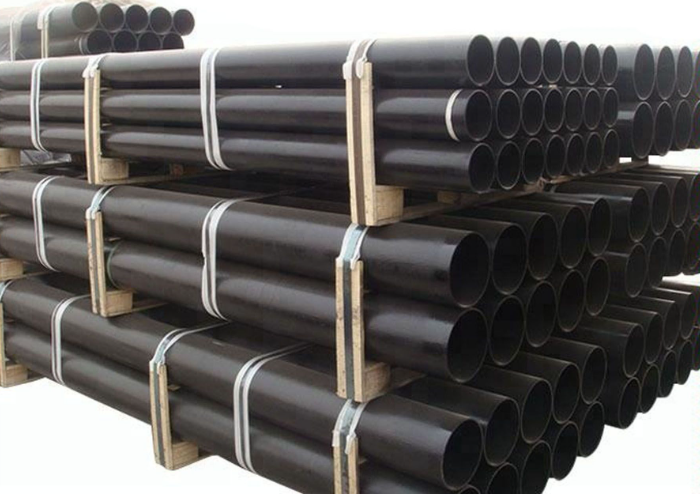
🔗 Common Ductile Iron Pipe Joint Types
1. Push-On Joints (Tyton® Joints)
-
Description: A bell-and-spigot joint where the spigot end is inserted into the bell, and a rubber gasket provides a watertight seal.
-
Advantages: Simple installation, no special tools required, and suitable for underground applications.
-
Limitations: Non-restrained; external thrust blocks or restraints are needed at bends and tees.
2. Mechanical Joints
-
Description: Consists of a bell with an integrally cast flange, a ductile iron gland, and a rubber gasket compressed by bolts.
-
Advantages: Provides a strong, flexible connection; suitable for above-ground and underground installations.
-
Limitations: Requires proper torque on bolts to ensure a secure seal.
3. Flanged Joints
-
Description: Flanges are bolted together with a gasket between them to create a tight seal.
-
Advantages: Allows for easy disassembly and is ideal for connections to valves and equipment.
-
Limitations: More expensive and requires precise alignment during installation.
4. Coupling Joints
-
Description: A sleeve that fits over the ends of two pipes, secured by bolts.
-
Advantages: Useful for connecting pipes of different materials or sizes.
-
Limitations: May not provide the same strength as other joint types.
📝 Step-by-Step Installation Guide
-
Preparation:
-
Ensure all pipe ends are clean and free from debris.
-
Lubricate gaskets and pipe ends as per manufacturer recommendations.
-
-
Assembly:
-
For push-on joints, insert the spigot end into the bell until the gasket is fully compressed.
-
For mechanical joints, align the pipe ends, insert the gasket, and secure the gland with bolts, tightening them evenly.
-
For flanged joints, align the flanges, place the gasket, and bolt them together in a crisscross pattern to ensure even pressure.
-
-
Inspection:
-
Check all joints for proper alignment and secure connections.
-
Ensure that gaskets are not pinched or damaged.
-
-
Backfilling:
-
Carefully backfill around the pipe, avoiding direct contact with sharp objects that could damage the pipe.
-
Compact the soil in layers to prevent settling.
-
📊 Comparison of Joint Types
Joint Type | Installation Complexity | Flexibility | Cost | Common Applications |
---|---|---|---|---|
Push-On | Low | Low | Moderate | Underground pipelines |
Mechanical | Moderate | High | High | Above-ground and underground |
Flanged | High | Low | High | Connections to valves/equipment |
Coupling | Low | Moderate | Low | Connecting different pipe materials |
❓ Frequently Asked Questions
Q1: Can I use push-on joints for all ductile iron pipe installations?
Push-on joints are suitable for most underground installations but are not recommended for areas with high seismic activity or where restrained joints are required.
Q2: How do I ensure a secure mechanical joint connection?
Ensure that the gasket is properly seated and that the gland is evenly tightened using the recommended torque specifications.
Q3: Are flanged joints suitable for underground use?
Flanged joints are generally not recommended for underground use due to their rigidity and potential for leakage under ground movement.
📺 Visual Installation Demonstrations
-
Standard Joint Installation for Natural Ductile Iron Pipe: A comprehensive guide on installing push-on joints.
-
How to Install Mechanical Joint Pipe and Fittings: Step-by-step instructions for mechanical joint installations.
📝 Conclusion
Selecting the appropriate joint type for ductile iron pipes is crucial for ensuring the integrity and longevity of your pipeline system. By understanding the advantages and limitations of each joint type and following proper installation procedures, you can achieve reliable and durable connections.
References:
- Ductile Iron Pipe – Wikipedia
- AWWA Standards for Ductile Iron Pipe and Fittings – American Water Works Association (AWWA)
- Common Ductile Iron Pipe Joint Types – National Pipe
- OSHA Guidelines on Pipe Installation Safety and Jointing
- Pipe Materials Used in Water Systems – United States Environmental Protection Agency (EPA)