Connecting concrete pipe to ductile iron pipe requires proper alignment, sealing, and joint restraint to ensure a leak-free and durable transition. Common methods include using flexible couplings, adapter rings, or mechanical joint fittings designed for dissimilar materials.
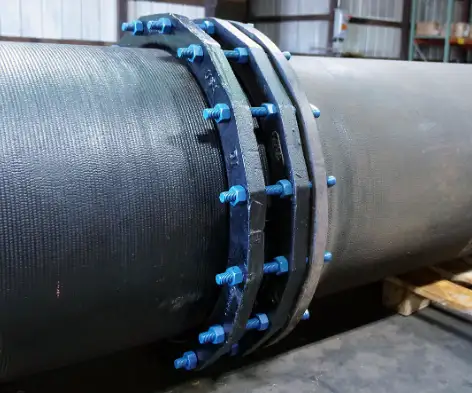
1. Introduction to Concrete and Ductile Iron Pipes
What are Concrete Pipes?
Concrete pipes are a type of pipe used for carrying water, sewage, or other fluids in a variety of civil engineering applications. They are commonly used in stormwater drainage systems, sewage systems, and large-diameter pipes for water distribution. Concrete pipes are known for their strength and durability, especially in areas where the pipes are exposed to high levels of pressure or external forces.
What are Ductile Iron Pipes?
Ductile iron pipes are made from cast iron but with a treatment that gives them greater flexibility and strength. These pipes are widely used in water distribution systems, gas lines, and other applications where the pipes need to handle pressure while being resistant to corrosion. Ductile iron is typically preferred for its resilience, longevity, and ease of installation.
Why Connect Concrete Pipes to Ductile Iron Pipes?
In many water, sewer, and stormwater systems, it is necessary to connect concrete pipes with ductile iron pipes. This combination allows engineers to take advantage of the strengths of both materials: concrete pipes provide durability and strength, while ductile iron pipes offer flexibility and resistance to corrosion. Effective connections are essential for seamless operation, avoiding leaks, and maintaining the integrity of the infrastructure.
2. Key Factors to Consider Before Connecting Concrete and Ductile Iron Pipes
Pipe Size and Specifications
Before connecting concrete and ductile iron pipes, it is crucial to ensure that both pipes are of compatible sizes and specifications. Pipe diameter, wall thickness, and length should match, as well as the internal pressure rating. If the pipes are not compatible, you may need to adjust or use transition couplings that allow for a proper fit.
Pressure Requirements and Flow Considerations
The connection method should also take into account the pressure and flow rates expected in the system. Ductile iron pipes can handle higher pressures compared to concrete pipes, so understanding the specific demands of the pipeline will guide the selection of connection methods.
Material Compatibility
Concrete and ductile iron pipes have different material properties, including expansion rates and resistance to corrosion. Choosing a suitable connection method (such as flexible couplings or mechanical joints) that accommodates these differences is essential for a long-lasting and secure connection.
Environmental Factors (Soil, Water, etc.)
Consideration of environmental factors such as soil composition, moisture levels, and water chemistry is essential. Concrete pipes are susceptible to external corrosion from certain chemicals, and ductile iron pipes can corrode in aggressive soil conditions if not properly protected. Understanding these environmental challenges will help guide the appropriate connection methods and materials.
3. Connection Methods for Concrete Pipe and Ductile Iron Pipe
Direct Connection (Mechanical Joints)
One of the most common methods of connecting concrete and ductile iron pipes is through the use of mechanical joints. These joints are typically made using bolts and gaskets that compress around the pipe ends to form a tight seal. The main advantage of this method is its reliability and ease of installation.
Flanged Connections
Flanged connections are another common method, especially for pipes that are under high pressure. This method involves attaching a flange to the end of each pipe and then bolting them together. Flanged connections are particularly useful in situations where the pipes may need to be disassembled for maintenance.
Transition Couplings
Transition couplings are specially designed connectors used to join pipes of different materials, such as concrete and ductile iron. These couplings are designed to accommodate the differences in pipe material, providing a secure and leak-proof connection.
Flexible Couplings
Flexible couplings are used to connect pipes of different materials and sizes. They provide a flexible yet durable connection that can withstand soil movement and seismic activity. Flexible couplings are ideal for situations where pipes experience shifting or slight misalignments.
Grouted Joints
In some cases, a grouted joint may be used. This involves filling the space between the pipes with grout to form a secure bond. Grouted joints are typically used when a high level of water-tightness is required.
4. Step-by-Step Guide to Connecting Concrete Pipe to Ductile Iron Pipe
Preparing the Pipes
-
Clean the pipe ends to remove any dirt, debris, or corrosion.
-
Inspect the pipe ends to ensure they are free from cracks or other defects that may affect the connection.
Installing the Connection
-
Select the appropriate connection method based on the pipe sizes and the application.
-
Fit the coupling or joint to the pipe ends.
-
Secure the connection using the appropriate fasteners, gaskets, or bolts.
Securing the Connection
-
Tighten the bolts or fasteners evenly to ensure a uniform seal.
-
Check for leaks by applying pressure to the system and looking for signs of water seepage.
Testing the Joint
-
Test the joint by performing a pressure test to ensure the integrity of the connection.
-
Inspect the joint regularly for any signs of wear or leaks over time.
5. Tools and Materials Required
Essential Tools for Pipe Installation
-
Pipe wrenches
-
Torque wrench
-
Mechanical joint tools
-
Leveling tools
-
Pressure testing equipment
Materials for Connection
-
Gaskets
-
Flexible couplings
-
Transition couplings
-
Grout
-
Lubricants
Pipe Preparation Equipment
-
Wire brushes
-
Sandpaper
-
Pipe cutter (if needed)
6. Common Challenges in Connecting Concrete and Ductile Iron Pipes
Misalignment Issues
Misalignment during installation can lead to improper connections that may cause leaks or failures. Ensuring that both pipe ends are properly aligned is essential to a secure connection.
Material Compatibility Challenges
Ductile iron and concrete have different material properties, which can lead to issues if the wrong connection method is used. Transition couplings or flexible joints can help accommodate these differences.
Leakage Risks
Leakage is a common issue when connecting pipes, especially if the connection is not tight enough or the materials are incompatible. Ensuring the correct pressure rating and sealant materials can mitigate this risk.
Soil and Environmental Influences
Soil movement, temperature fluctuations, and water exposure can all affect the integrity of the connection. Proper sealing and corrosion-resistant materials can help reduce these risks.
7. Safety Considerations
Worker Safety
Safety should always be the top priority. Workers should use proper personal protective equipment (PPE), including gloves, goggles, and steel-toe boots. Additionally, proper lifting techniques should be employed when handling large pipes.
Environmental Safety
Ensure that any waste materials, such as grout or old gaskets, are disposed of properly to avoid environmental contamination.
Proper Handling of Materials and Tools
Ensure that tools and materials are handled with care to prevent injury or damage.
8. Testing and Quality Control for Pipe Connections
Pressure Testing
Pressure testing ensures that the connection can withstand the expected load and pressure levels without failure.
Visual Inspection
A thorough visual inspection of the joint and surrounding areas is necessary to identify any potential issues early on.
Ultrasonic and X-ray Inspection
For critical applications, ultrasonic or X-ray inspection can be used to check the internal integrity of the connection.
9. Maintenance and Long-term Care
How to Maintain the Connection
Routine inspection and maintenance should be conducted to check for leaks, corrosion, and signs of wear. Gaskets and couplings may need to be replaced periodically.
Ensuring Longevity of the Connection
Applying anti-corrosion coatings and using high-quality gaskets can help extend the lifespan of the connection.
Monitoring for Signs of Wear and Tear
Inspect the joints regularly for signs of damage or wear, especially after severe weather or ground movement.
10. Cost Considerations for Connecting Concrete and Ductile Iron Pipes
Material Costs
The cost of materials will depend on the type of connection method used and the size of the pipes. Ductile iron pipes and transition couplings tend to be more expensive than concrete pipes alone.
Labor Costs
Labor costs can vary based on the complexity of the connection and the type of joint used. Typically, more labor-intensive connections such as flanged or grouted joints will increase installation costs.
Maintenance and Repair Costs
Proper maintenance and regular inspections can help avoid costly repairs in the future.
11. Frequently Asked Questions (FAQs)
Q1: What’s the best method to connect concrete and ductile iron pipes?
Answer: The best method depends on factors like pipe size, pressure requirements, and environmental conditions. Mechanical joints are a reliable choice, but transition couplings or flexible couplings may also be necessary for more complex installations.
Q2: How do I prevent leaks when connecting these two types of pipes?
Answer: Leaks can be prevented by ensuring that the pipes are properly aligned and that the connection is tightly secured using the appropriate gaskets or sealants. Additionally, conducting pressure tests after installation will help identify any leaks early on.
Q3: Are there any special coatings needed for concrete and ductile iron pipe connections?
Answer: Yes, depending on the environmental conditions, special coatings such as epoxy coatings or anti-corrosion wraps may be necessary to protect the pipes and the connection from corrosion.
Q4: How long should a concrete and ductile iron pipe connection last?
Answer: With proper installation and maintenance, a well-executed connection between concrete and ductile iron pipes can last for several decades. Regular inspections will ensure its longevity.
Q5: Can the connection fail due to soil movement?
Answer: Yes, soil movement can lead to stress on the pipe connection. Using flexible couplings or grouted joints can help accommodate ground shifts and reduce the risk of failure.
Q6: How often should these connections be inspected?
Answer: Connections should be inspected regularly, particularly after extreme weather events or ground shifts. Annual inspections are recommended, but more frequent checks may be necessary in areas with unstable soil or aggressive environments.
12. Conclusion
Connecting concrete pipes to ductile iron pipes is a critical task that requires careful planning, proper materials, and the right techniques. By following the best practices outlined in this guide, you can ensure a strong, leak-free, and long-lasting connection between these two materials.
References:
- ASTM AWWA C111/C115 – Rubber-Gasket Joints for Ductile-Iron Pressure Pipe and Fittings
- U.S. Environmental Protection Agency (EPA) – Drinking Water Distribution Systems
- CDC NIOSH – Worker Safety and Health in Pipe Installation and Maintenance
- Wikipedia – Ductile Iron Pipe
- Water Research Foundation – Piping Materials and Jointing Techniques