Ductile iron pipes are known for their durability and strength, but like all materials exposed to moisture and environmental conditions, they are susceptible to corrosion. Corrosion can cause significant damage to the integrity of the pipe, leading to leaks, cracks, and eventual failure. To prevent this, an effective corrosion protection strategy is essential, and one of the most common methods is cathodic protection, which involves attaching an anode to the pipe.
This article will explore the process of attaching an anode to ductile iron pipes, the types of anodes used, why this protection method is necessary, and how to ensure the system functions optimally. We will also address common concerns and frequently asked questions related to anode attachment and corrosion prevention.
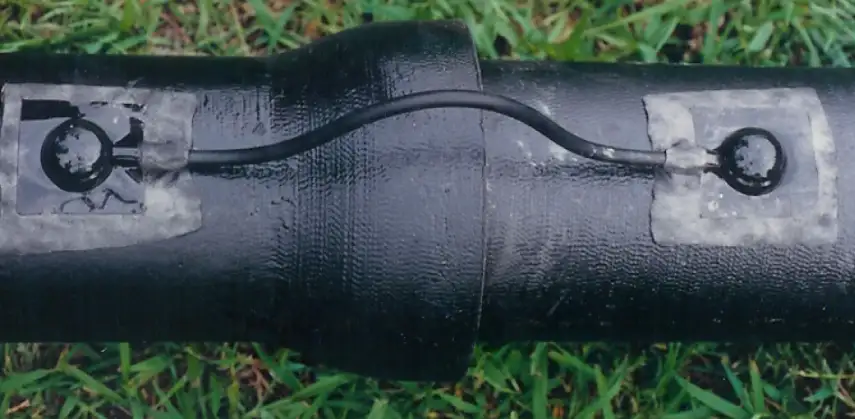
What is Cathodic Protection?
Cathodic protection is a method used to prevent the corrosion of metal structures by making the entire structure the cathode of an electrochemical cell. This is achieved by attaching a more easily corroded material (the anode) to the structure, which will corrode instead of the pipe. In the case of ductile iron pipes, the anode provides a sacrificial material that corrodes in place of the iron pipe.
Why Use Cathodic Protection on Ductile Iron Pipes?
-
Prevents Corrosion: The primary function of attaching an anode to ductile iron pipes is to prevent external corrosion caused by soil and moisture.
-
Extends Pipe Lifespan: By reducing the rate of corrosion, anode attachment significantly extends the operational life of the ductile iron pipe.
-
Cost-Effective Maintenance: Cathodic protection is a relatively low-cost method to protect infrastructure compared to full pipe replacement.
Types of Anodes Used for Ductile Iron Pipes
There are several types of anodes used in cathodic protection systems. The choice of anode depends on factors such as soil conditions, pipe diameter, and environmental factors. The most common anodes include:
1. Zinc Anodes
-
Pros: Zinc is an inexpensive and widely used material that provides good protection against corrosion.
-
Cons: Zinc anodes are not as effective in highly acidic or alkaline environments.
2. Magnesium Anodes
-
Pros: Magnesium anodes are particularly effective in soils with low resistivity and high moisture content.
-
Cons: Magnesium can corrode more quickly in alkaline soils, reducing its lifespan.
3. Aluminum Anodes
-
Pros: Aluminum anodes have a high current output and are effective in a wide range of soil conditions.
-
Cons: They are more expensive than zinc but are often used for larger installations where long-term protection is necessary.
4. Mixed Metal Oxide (MMO) Anodes
-
Pros: MMO anodes are long-lasting and require minimal maintenance.
-
Cons: These are more expensive and are typically used for large-scale, industrial applications.
Methods for Attaching an Anode to a Ductile Iron Pipe
The process of attaching an anode to a ductile iron pipe can be done in several ways. The most common methods include direct attachment to the pipe, installation of a test station, and installation of a sacrificial anode bed.
1. Direct Attachment Method
This is the most straightforward method, where the anode is directly connected to the ductile iron pipe using a conductive wire. The connection is made through a metallic clamp or bolted connection that ensures an electrically conductive bond between the anode and the pipe.
Steps:
-
Clean the Surface of the Pipe: Clean the area where the anode will be attached to ensure a good electrical connection. Use a wire brush or abrasive pad to remove any rust or debris.
-
Attach the Anode Clamp: Position the anode close to the pipe and secure it using a specialized anode clamp or a bolted connection.
-
Connect the Wire: Connect a conductive wire from the anode to the pipe, ensuring the wire is firmly attached to both the anode and the pipe.
2. Installation of Test Station
A test station is a device used to monitor the effectiveness of the cathodic protection system. The anode is connected to the pipe through the test station, allowing for regular testing and monitoring of the protection system.
Steps:
-
Install Test Stations: Test stations are installed along the pipeline at specific intervals.
-
Connect the Anode: The anode is connected to the test station through the conductive wire.
-
Monitor the System: Regular testing is done at the test stations to ensure the anode is functioning correctly and providing the necessary protection.
3. Sacrificial Anode Bed
In cases where a large number of pipes need to be protected, sacrificial anode beds may be used. This involves the placement of several anodes in the ground near the pipe, connected to it via a network of wires.
Steps:
-
Excavate a Trench: A trench is dug along the pipeline to place the anodes.
-
Place the Anodes in the Trench: Several anodes are placed in the trench, typically spaced at regular intervals.
-
Connect the Anodes to the Pipe: A conductive wire is run from the anodes to the ductile iron pipe to establish the cathodic protection system.
Factors Affecting the Attachment Process
Several factors can influence the effectiveness of attaching an anode to a ductile iron pipe, including:
-
Soil Composition: The type of soil around the pipe can affect the anode’s ability to protect the pipe. Soils with high resistivity (such as dry, sandy soils) may require more anodes or more powerful anodes.
-
Pipe Coating: The type of coating on the ductile iron pipe (e.g., cement mortar, epoxy) can impact how effectively the anode is connected to the pipe. Some coatings may need to be removed to ensure good electrical contact.
-
Pipe Size and Depth: Larger pipes or those buried deeper underground may require different installation methods or a more robust cathodic protection system.
-
Environmental Conditions: Wet, salty, or chemically active environments can significantly affect the lifespan of the anode and its connection to the pipe.
Comparing Anode Attachment Methods
Method | Advantages | Disadvantages |
---|---|---|
Direct Attachment | Simple to implement; cost-effective | May not be suitable for large-scale projects |
Test Station Installation | Allows for regular monitoring of the system; ensures long-term protection | More complex installation; requires periodic checks |
Sacrificial Anode Bed | Suitable for large-scale projects; high protection output | Higher initial cost; more complex installation process |
6 Frequently Asked Questions (FAQs)
1. How do I know if my ductile iron pipe needs cathodic protection?
Corrosion can be difficult to detect until it causes significant damage. However, if you notice leaks, rust, or cracks along the pipeline, these are indicators that the pipe may be corroding. Cathodic protection is highly recommended in areas with high moisture content or aggressive soil conditions.
2. What happens if I don’t install an anode on a ductile iron pipe?
Without cathodic protection, ductile iron pipes are vulnerable to corrosion, which can lead to premature failure, leaks, and expensive repairs. Corrosion can compromise the structural integrity of the pipe, reducing its lifespan by decades.
3. Can I use any type of anode for ductile iron pipes?
Not all anodes are suitable for ductile iron pipes. The choice of anode depends on environmental factors such as soil resistivity and the size of the pipe. Zinc, magnesium, and aluminum are the most commonly used anodes, but each has specific applications.
4. How long does the anode last?
The lifespan of an anode depends on several factors, including the type of anode, the environmental conditions, and the amount of corrosion the system needs to protect against. Zinc anodes typically last 3-5 years, while aluminum anodes can last longer, up to 10 years or more.
5. How do I monitor the effectiveness of the cathodic protection system?
Monitoring is typically done via test stations installed along the pipeline. These stations allow for regular testing of the pipe’s voltage and current, helping to ensure that the system is functioning correctly and the pipe is protected from corrosion.
6. Can I install an anode myself, or do I need a professional?
While some smaller-scale installations can be done by experienced individuals, it is generally recommended to hire a professional corrosion engineer or contractor. Installing cathodic protection requires specialized knowledge to ensure the system is effective and safe.
Conclusion
Attaching an anode to a ductile iron pipe is an effective and essential step in preventing corrosion and extending the lifespan of the pipe. Understanding the different methods of attachment, the types of anodes, and the factors that affect the protection process is crucial for ensuring the system works as intended. By following the correct installation procedures and monitoring the system regularly, you can protect your ductile iron pipes from corrosion and minimize the need for costly repairs or replacements.