Attaching flanges to ductile iron pipes is a fundamental process in various industries, including water treatment, HVAC, and industrial applications. Proper flange attachment ensures secure and leak-proof connections, facilitating efficient fluid and gas transportation. This comprehensive guide delves into the methods, standards, tools, and best practices for attaching flanges to ductile iron pipes.
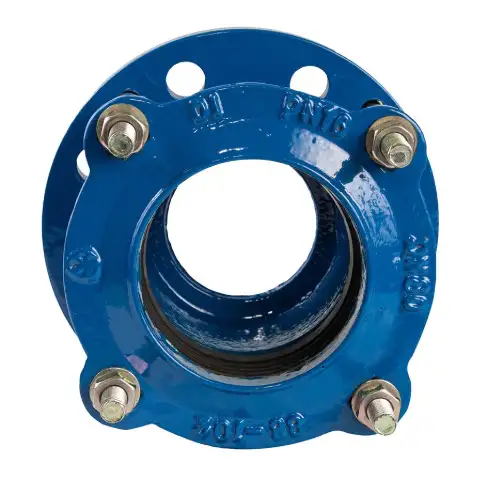
1. Introduction to Ductile Iron Pipes and Flanges
Ductile iron pipes are widely used in infrastructure projects due to their strength, durability, and flexibility. Flanges are mechanical components that allow for the connection of pipes, valves, and other equipment. Attaching flanges to ductile iron pipes is essential for creating secure and maintainable joints.
2. Flange Attachment Methods
Threaded Flanges
Threaded flanges are screwed onto the external threads of a pipe. This method is suitable for smaller pipes and allows for easy disassembly.
Welded Flanges
Welded flanges are attached by welding the flange directly to the pipe. This method provides a strong and permanent connection, ideal for high-pressure applications.
Flange Adapters
Flange adapters are mechanical devices that connect a pipe to a flange. They are particularly useful when transitioning between different pipe materials or sizes.
3. Standards and Specifications
ANSI B16.1
This standard covers cast iron flanges and flanged fittings for use in pressure systems. It specifies dimensions, tolerances, and materials.
AWWA C110/C115
These standards are developed by the American Water Works Association and pertain to ductile iron and gray iron fittings. They provide guidelines for design, materials, and testing.
EN 1092
This European standard specifies requirements for flanges and their joints, including dimensions, materials, and pressure-temperature ratings.
4. Materials and Coatings
Ductile Iron
Ductile iron is the primary material used for pipes and fittings. It offers high tensile strength and resistance to impact and fatigue.
Corrosion Protection
To enhance durability, ductile iron pipes and flanges are often coated with materials like epoxy or bituminous coatings to prevent corrosion.
5. Tools Required for Flange Attachment
-
Pipe Wrench: For gripping and turning the pipe.
-
Torque Wrench: To apply precise torque to bolts.
-
Pipe Cutter or Saw: For cutting the pipe to the required length.
-
Cleaning Tools: Wire brushes and cloths for cleaning pipe ends.
-
Measuring Instruments: Calipers and tape measures for accurate measurements.
6. Step-by-Step Flange Attachment Process
-
Preparation: Clean the pipe ends to remove any dirt, rust, or debris.
-
Alignment: Align the flange with the pipe, ensuring bolt holes are properly matched.
-
Insertion of Bolts: Insert bolts through the flange holes and hand-tighten nuts onto them.
-
Tightening: Using a torque wrench, tighten the bolts in a crisscross pattern to ensure even pressure.
-
Inspection: Check for any misalignments or gaps and adjust as necessary.
7. Quality Control and Inspection
Regular inspections are crucial to ensure the integrity of flange connections. Check for signs of leakage, corrosion, or mechanical damage. Pressure testing may be conducted to verify the seal.
8. Common Challenges and Solutions
-
Misalignment: Ensure proper alignment of flange holes before tightening bolts.
-
Corrosion: Apply appropriate coatings and conduct regular inspections.
-
Over-tightening: Use a torque wrench to apply the correct amount of torque to bolts.
9. Maintenance and Longevity
Regular maintenance, including cleaning and inspection, can extend the life of flange connections. Replace gaskets and bolts as needed to maintain a secure seal.
10. Frequently Asked Questions (FAQs)
Q1: What is the difference between threaded and welded flanges?
A1: Threaded flanges are screwed onto the pipe, allowing for easy disassembly. Welded flanges are welded directly to the pipe, providing a permanent and strong connection.
Q2: Can flange adapters be used with all types of pipes?
A2: Flange adapters are versatile and can be used to connect pipes of different materials and sizes, provided the correct adapter is selected.
Q3: How do I determine the correct flange size for my pipe?
A3: Measure the outer diameter of the pipe and match it with the flange size. Refer to standards like ANSI B16.1 or AWWA C110/C115 for specific dimensions.
Q4: What materials are commonly used for flange gaskets?
A4: Common materials include rubber, graphite, and PTFE. The choice depends on the application and operating conditions.
Q5: How often should flange connections be inspected?
A5: Inspections should be conducted regularly, at least annually, or more frequently in high-stress applications.
Q6: What should I do if I notice a leak at a flange connection?
A6: First, tighten the bolts to the specified torque. If the leak persists, inspect the gasket for damage and replace it if necessary.
For a visual demonstration of the flange attachment process, you may find the following video helpful: