When it comes to the selection of materials for underground pipelines, ductile iron pipes are one of the most commonly used materials due to their superior strength, durability, and corrosion resistance. A key factor in the installation and transportation of these pipes is their weight per foot, which can significantly impact the overall installation process, transportation logistics, and cost.
In this article, we will provide a detailed exploration of ductile iron pipe weight per foot, including how to calculate the weight, the factors that influence it, and how it compares to other types of pipes. We will also cover the different standards and specifications, as well as address frequently asked questions related to this important topic.
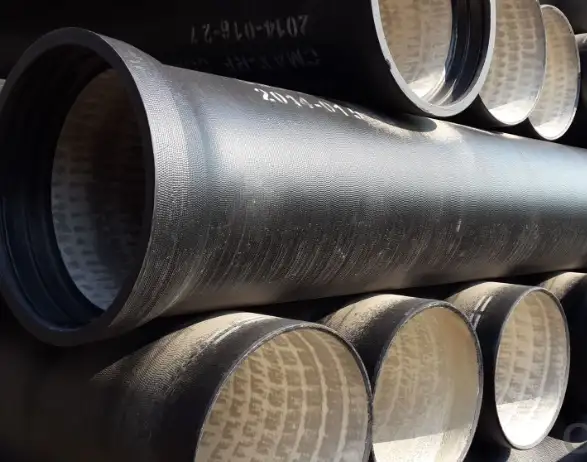
1. What is Ductile Iron Pipe?
Ductile iron pipes are a type of cast iron pipe that has been modified with the addition of magnesium, making the material more ductile and capable of withstanding higher levels of stress and impact. The primary use of ductile iron pipes is for the transportation of water, wastewater, and other fluids in various industrial, municipal, and infrastructure applications.
Key Features of Ductile Iron Pipes:
-
Ductility: Unlike traditional cast iron, ductile iron pipes are more flexible and can bend without breaking.
-
Corrosion Resistance: Ductile iron pipes are highly resistant to corrosion, particularly when coated with protective linings.
-
High Strength: These pipes are much stronger and can handle higher internal pressure, making them suitable for water distribution systems.
-
Longevity: Ductile iron pipes have a long service life, often lasting 100 years or more when properly installed and maintained.
Standard Specifications:
-
Diameter: Ductile iron pipes come in a wide range of diameters, from small pipes for residential systems to large pipes used in industrial applications.
-
Wall Thickness: The thickness of the wall can vary based on the pressure rating and application requirements.
-
Length: Pipes are typically sold in standard lengths, such as 18 or 20 feet.
2. Why is Weight Important in Ductile Iron Pipes?
The weight per foot of a ductile iron pipe is crucial for several reasons:
-
Transportation and Handling: Heavier pipes are more challenging to transport and handle. Knowing the weight per foot allows for better planning of logistics, including the use of cranes, forklifts, and other heavy machinery during installation.
-
Installation Costs: Heavier pipes often require more labor and specialized equipment for installation, which can increase overall project costs.
-
Pipe Strength and Durability: The weight of a pipe often correlates with its wall thickness, which directly affects its strength and pressure resistance. Pipes with thicker walls are usually heavier and better suited for high-pressure applications.
-
Structural Considerations: The weight of the pipe can impact the structural integrity of the pipeline. For example, underground pipelines must be able to withstand external loads such as soil pressure, traffic, and seismic forces.
3. Standard Weights for Ductile Iron Pipes
Ductile iron pipes are classified by their diameter and wall thickness, which determine their weight per unit length. Below is a table of typical ductile iron pipe weights per foot for various pipe sizes.
Pipe Size (inches) | Wall Thickness (inches) | Weight per Foot (lbs) |
---|---|---|
4 | 0.25 | 18.56 |
6 | 0.25 | 26.69 |
8 | 0.25 | 35.56 |
10 | 0.25 | 44.40 |
12 | 0.25 | 53.16 |
14 | 0.25 | 62.48 |
16 | 0.25 | 72.36 |
18 | 0.25 | 82.52 |
20 | 0.25 | 93.10 |
24 | 0.25 | 113.21 |
30 | 0.25 | 142.91 |
36 | 0.25 | 171.90 |
42 | 0.25 | 203.19 |
48 | 0.25 | 237.56 |
Notes:
-
The wall thickness typically ranges from 0.25 inches to 0.50 inches, depending on the pressure rating and the type of application.
-
The pipe weight increases as the diameter and wall thickness increase.
4. Factors Affecting the Weight of Ductile Iron Pipes
Several factors can influence the weight of ductile iron pipes, including:
-
Pipe Diameter: Larger pipes have more material and are naturally heavier. The weight increases significantly with the diameter.
-
Wall Thickness: Thicker walls add more weight to the pipe. For high-pressure applications, the wall thickness will be increased to ensure strength, resulting in a heavier pipe.
-
Coatings and Linings: Many ductile iron pipes are coated or lined with materials such as cement mortar or epoxy to enhance their corrosion resistance. These coatings add extra weight to the pipe.
-
Pipe Length: While standard pipe lengths are usually 18 or 20 feet, custom lengths can be ordered, which can affect the total weight when considering the shipment of multiple pipes.
-
Alloying Materials: In some cases, the addition of alloying materials such as manganese or chromium can affect the pipe’s density and, consequently, its weight.
5. How to Calculate the Weight of Ductile Iron Pipe per Foot
The weight of a ductile iron pipe can be calculated using the following formula:
Weight per Foot (lbs)=π×Do×T×ρ
Where:
-
D_o = Outer diameter of the pipe (in inches)
-
T = Wall thickness (in inches)
-
ρ = Density of ductile iron, typically around 0.26 lbs/in³
-
π = 3.14159
This formula provides an estimation of the pipe’s weight based on its physical dimensions and the material’s density. It is important to note that the actual weight may vary depending on factors such as coatings or additional materials.
6. Comparison with Other Pipe Materials
Below is a comparison of ductile iron pipes with other common materials used in piping systems, such as steel, PVC, and HDPE pipes, based on their typical weight per foot.
Pipe Material | Diameter (inches) | Wall Thickness (inches) | Weight per Foot (lbs) |
---|---|---|---|
Ductile Iron | 12 | 0.25 | 53.16 |
Steel | 12 | 0.25 | 70.00 |
PVC | 12 | 0.25 | 9.25 |
HDPE | 12 | 0.25 | 11.50 |
Key Takeaways:
-
Ductile iron is much heavier than PVC and HDPE pipes, which makes it more suitable for high-pressure and heavy-duty applications.
-
Steel pipes are heavier than ductile iron, but they are generally used in more specific applications requiring higher strength and durability.
7. Applications of Ductile Iron Pipes
Ductile iron pipes are primarily used for the transportation of water and wastewater, but they are also used in a variety of other applications, including:
-
Municipal Water Supply: Ductile iron pipes are commonly used in water distribution systems due to their high strength and corrosion resistance.
-
Sewer and Wastewater Systems: The durability and resistance to corrosion make ductile iron pipes ideal for handling wastewater.
-
Industrial Applications: Ductile iron pipes are also used for transporting other fluids such as chemicals, oils, and gases in industrial settings.
-
Irrigation: Ductile iron pipes are used in large-scale irrigation systems where pressure and strength are critical.
8. Advantages and Disadvantages of Ductile Iron Pipes
Advantages:
-
Durability: Long lifespan, often exceeding 100 years.
-
Corrosion Resistance: Superior protection against corrosion and external environmental factors.
-
Strength: Ability to withstand high pressure and external loads.
-
Ductility: Flexible enough to handle external forces without breaking.
Disadvantages:
-
Weight: Ductile iron pipes are heavier than other pipe materials, making them more difficult to handle and install.
-
Cost: They are more expensive than plastic alternatives such as PVC or HDPE.
-
Handling Challenges: Due to their weight, special equipment is often required for installation.
9. Frequently Asked Questions (FAQ)
1. What is the weight of a 12-inch ductile iron pipe per foot?
A typical 12-inch ductile iron pipe with a standard wall thickness of 0.25 inches weighs approximately 53.16 lbs per foot. This weight can vary depending on the specific pipe’s coating, length, and wall thickness.
2. How do you calculate the weight of ductile iron pipes?
The weight of ductile iron pipes is calculated by using the formula that factors in the pipe’s outer diameter, wall thickness, and the material’s density. The formula is:
Weight per Foot (lbs)=π×Do×T×ρ
3. Why is the weight of ductile iron pipes important?
The weight per foot of ductile iron pipes affects transportation, installation, and cost. Knowing the weight helps with logistics, handling, and ensuring the right equipment is used during installation.
4. How do ductile iron pipes compare to other materials in terms of weight?
Ductile iron pipes are significantly heavier than PVC and HDPE pipes. This added weight makes them more suitable for high-pressure systems, while lighter materials like PVC are better for low-pressure, residential, or irrigation systems.
5. Can ductile iron pipes be used for high-pressure applications?
Yes, ductile iron pipes are ideal for high-pressure applications due to their strength and ability to withstand internal pressure. The weight of the pipes, combined with their thick walls, makes them perfect for handling high-volume and high-pressure systems.
6. What factors can affect the weight of ductile iron pipes?
The weight of ductile iron pipes can be affected by factors such as diameter, wall thickness, pipe length, and coatings. These elements determine the pipe’s overall weight, which directly impacts transportation, installation, and handling during construction.
10. Conclusion
Understanding the weight of ductile iron pipes is essential for anyone involved in the planning, installation, or maintenance of piping systems. By knowing the weight per foot and the factors that influence it, professionals can make informed decisions when selecting pipe materials for specific applications.