Ductile iron pipe (DIP) is manufactured in a limited set of nominal laying lengths determined by international and regional standards and by logistical considerations. Under AWWA C151 (ANSI/AWWA C151/A21.51), standard laying lengths are 18 ft (5.49 m) or 20 ft (6.10 m) nominal. ISO 2531 specifies 6.0 m lengths (and 5.7 m for container shipments) for DN 80–2600 mm. European EN 545/598 typically mirror ISO with 6 m nominal lengths. Variations arise due to bell depth, joint type, and manufacturer capabilities, leading to actual laying lengths from 5.8–6.2 m or 17.5–20.5 ft depending on pipe diameter and pressure class.
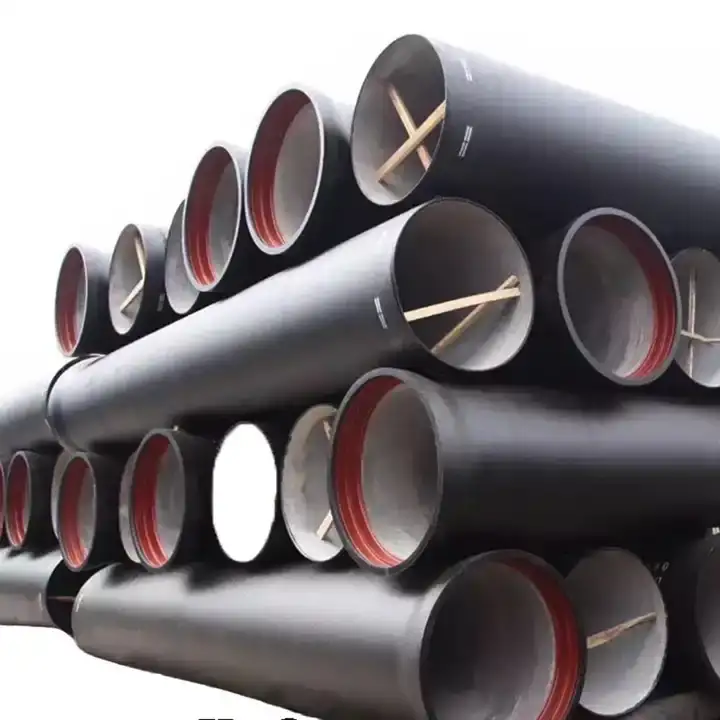
I. Introduction
Ductile iron pipe (DIP) is a centrifugally cast, spheroidal-graphite iron pipeline material widely used for potable water, wastewater, and industrial applications. Its notable advantages—high tensile strength, impact resistance, flexibility, and corrosion resistance—are codified in standards such as ANSI/AWWA C151/A21.51 in North America and ISO 2531 internationally. Properly manufactured lengths ensure uniform installation, minimize joint count, and optimize hydraulics; deviations can lead to increased field adjustments, additional couplings, and potential leakage points.
II. Standards Governing DIP Lengths
A. ANSI/AWWA C151/A21.51 (United States & Canada)
ANSI/AWWA C151/A21.51 establishes minimum requirements for centrifugally cast ductile iron pipe used in potable water or other liquids. Section 4 of C151/A21.51 specifies that DIP shall be furnished in nominal laying lengths of 18 ft or 20 ft, exclusive of bells. Actual laying length equals nominal length minus bell depth; larger diameters have deeper bells, shortening effective length slightly.
B. ISO 2531 (International)
ISO 2531:2009 sets global requirements for ductile iron pipes DN 40–DN 2600 мм, including dimensions, tolerances, and coatings. Clause 7.3 specifies nominal laying lengths of 6.0 m, with 5.7 m or 5.5 m provided for containerized shipment. Tolerances on laying length are ±50 mm.
C. EN 545 & EN 598 (Europe)
European standards EN 545 and EN 598 largely mirror ISO 2531 for ductile iron pipes in drinking water and sewage systems. Nominal lengths under EN range from 5.8–6.2 m, centered on 6 m, with tolerances similar to ISO. These standards classify pipes by pressure (PN 6–PN 25) and wall thickness, but do not alter laying length requirements.
III. Typical Nominal Lengths and Comparison Table
The following table summarizes standard nominal laying lengths under major standards:
Standard | Nominal Length(s) | Container/Alternate | Tolerance |
---|---|---|---|
ANSI/AWWA C151/A21.51 | 18 ft (5.49 m), 20 ft (6.10 m) | — | ±½ in (±12 mm) |
ISO 2531:2009 | 6.0 m | 5.7 m, 5.5 m | ±50 mm |
EN 545 / EN 598 | 6.0 m | — | ±50 mm |
GOST 5525 (Russia) | 5.5–6.5 m | — | ±50 mm |
Chinese GB/T 13295 | 6.0 m | — | ±50 mm |
Sources: ANSI/AWWA C151 Table 1; ISO 2531 Clause 7.3; EN 598 §4.2.
IV. Factors Affecting Standard Lengths
A. Bell Depth and Joint Profile
Bell depth increases with pipe diameter to accommodate gasket and joint restraint systems. For example, a 36-inch pipe bell may be 300 mm deep vs. 150 mm for a 4-inch pipe, reducing laying length accordingly.
B. Pressure Class & Wall Thickness
Heavier wall classes (e.g., Class K9, C30, etc.) entail greater pipe weight; some manufacturers limit laying length for ease of handling. Under ISO 2531, K9 (50 bar) and C30 (30 bar) classes may still be offered at 6.0 m, but handling equipment must match weight (up to 9 t per length for large diameters).
C. Material and Manufacturing Process
Centrifugal casting vs. static casting can influence overall straightness and length tolerances. Modern centrifugal lines maintain ±5 mm straightness over 6 m, ensuring joints align properly.
D. Transportation & Container Constraints
For export via standard shipping containers, lengths are reduced to 5.7 m or 5.5 m to fit 20 ft containers, per McWane and various ISO suppliers.
V. Regional & Manufacturer Variations
A. North America
Most U.S. and Canadian producers conform strictly to AWWA C151. However, some smaller diameters (≤8 in) are often stocked at 18 ft only, while larger diameters default to 20 ft.
B. Europe
European mills (e.g., Saint-Gobain PAM) supply 6 m lengths, occasionally offering 5.9 m or 6.1 m variants to optimize material yield from casting lines.
C. Asia & Australia
ISO 2531 is widely adopted; Indian, Chinese, and Australian mills generally produce 6 m lengths, bundling DN 100–DN 300 pipes in bundles and shipping DN 350+ in bulk.
D. Custom & On-Request Lengths
Special orders can request non-standard lengths (e.g., 12 m for long-span installations) with spool welding, though these incur significant premiums and scheduling delays.
VI. Transportation, Handling, and Storage
DIP lengths are typically handled by gantry cranes or side loaders; 6.0 m lengths require staging yards with ≥8 m clear working space. Road transport of 6 m lengths demands semi-trailers; oversize permits are rarely needed. For container shipping, lengths ≤5.7 m fit 20 ft containers, optimizing freight cost per ton. Proper racking and blocking protect pipe and lining during transit.
VII. Custom Lengths and Splicing Options
When project constraints demand non-standard lengths, contractors may:
-
Order shorter nominal lengths (e.g., 3.0 m) for tight urban projects.
-
Use ductile iron couplings (AWWA C219) to splice multiple 6 m segments.
-
Specify field-welded steel or fabricated ductile iron for lengths >12 m, though welding may require specialized pre-heat and heat-treatment procedures.
Custom lengths generally add 10–20% premium and extend lead times by 4–8 weeks.
VIII. Six In-Depth FAQs
1. Why are ductile iron pipe lengths standardized at 6 m or 20 ft?
Standardization simplifies logistics, storage, and installation processes. ISO 2531 and AWWA C151 specify these lengths to balance manufacturing efficiency and handling convenience. Longer lengths reduce joint count, improving hydraulics and reducing potential leak points, but increase handling difficulty and transport costs. Conversely, shorter lengths ease handling but increase joint labor and coupling costs. The chosen nominal lengths represent an optimal compromise based on decades of industry practice and infrastructure performance data.
2. How does bell depth variation impact actual laying length?
Bell depth—the extension beyond spigot end to accommodate gasket and joint restraint—varies by diameter. A 4 in pipe may have a bell depth of 75 mm, whereas a 36 in pipe can reach 300 mm. Thus, a nominal 6 m length may yield an effective laying length of 5.7 m for large diameters. Accurate project surveying must account for these differences to ensure pipe fit without unintended gaps.
3. Can I get 12 m ductile iron pipe in a single piece?
Standard manufacturing lines do not cast lengths >6 m. For lengths >6 m, two 6 m segments are mechanically joined using AWWA C219 couplings or flanged adapters. Field-welded steel or fabricated ductile iron assemblies are possible but costly, requiring specialized welding, heat treatment, and non-destructive testing to maintain material properties. Such solutions usually exceed 30% in premium over standard lengths and extend delivery by several weeks.
4. How does shipping container size affect pipe length options?
Standard 20 ft (6.10 m) containers cannot accommodate 6.0 m pipes without overhang. To fit, manufacturers cut pipes to 5.7 m or 5.5 m for container shipping. This reduction aids bundling and lashing, protects bells from damage, and reduces freight costs. Buyers should confirm container-length options when importing.
5. What tolerances should I expect on laying length?
Under AWWA C151, laying-length tolerance is ±½ in (±12 mm) over 18 ft or 20 ft nominal. ISO 2531 and EN 545 specify ±50 mm on 6.0 m lengths. These tolerances ensure field joints align properly when pipes are installed end to end.
6. How do regional standards differ for DIP lengths?
North America strictly follows AWWA C151 with 18 ft/20 ft lengths. Europe and most ISO countries use 6 m lengths under ISO 2531 and EN 545/598. Russia’s GOST 5525 allows 5.5–6.5 m to suit local casting lines. China’s GB/T 13295 aligns with ISO at 6.0 m. Project managers must confirm local standard to avoid procurement mismatches.
References:
- ANSI/AWWA C151/A21.51 – Ductile Iron Pipe Standard | American Water Works Association (AWWA)
- ISO 2531:2009 – Ductile Iron Pipes, Fittings, Accessories and Their Joints for Water Applications | International Organization for Standardization (ISO)
- EN 545 – Ductile Iron Pipes, Fittings and Accessories for Water Pipelines | European Committee for Standardization (CEN)
- Ductile Iron Pipe – Wikipedia Overview of Materials, Standards and Applications
- GOST 5525-2012 – Ductile Iron Pipes Dimensions and Specifications | Russian Federal Agency on Technical Regulating and Metrology