Ductile iron pipes are integral components in modern water distribution systems due to their strength, durability, and versatility. The effectiveness of these systems largely depends on the quality and reliability of the joints connecting individual pipe sections. Understanding the different types of ductile iron pipe joints, their specifications, and proper installation techniques is crucial for ensuring the longevity and efficiency of water infrastructure.
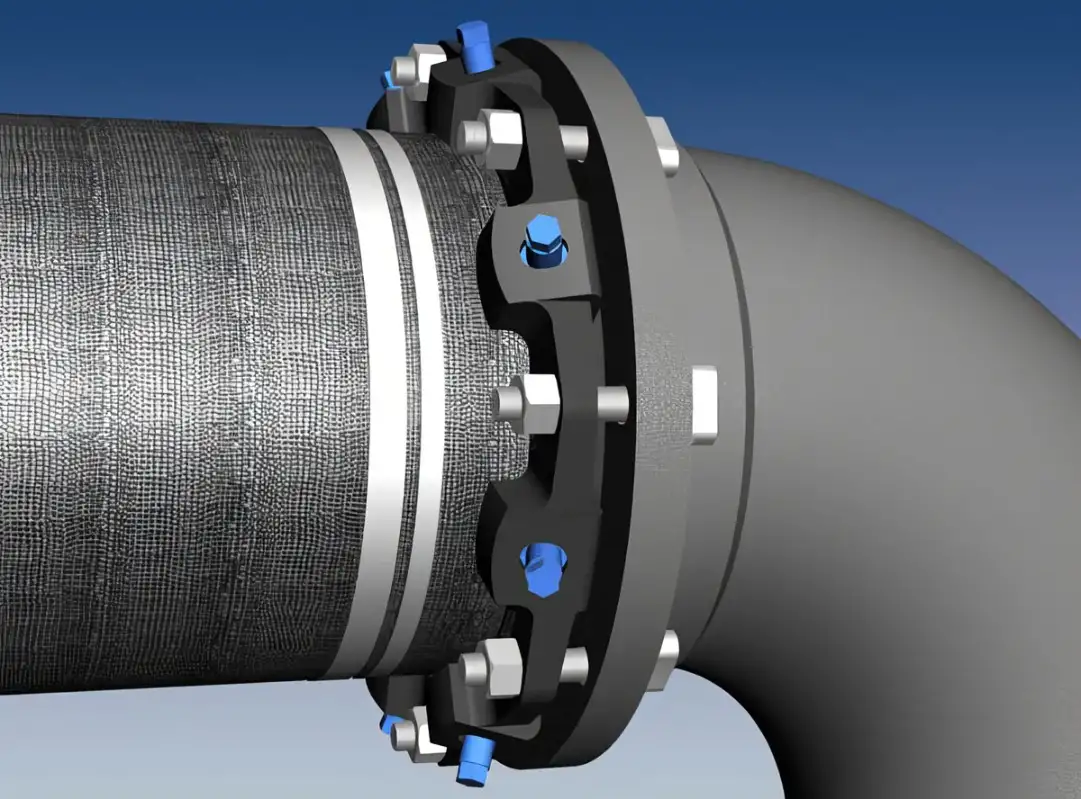
1. Overview of Ductile Iron Pipe Joints
Ductile iron pipe joints are designed to connect sections of ductile iron pipes, facilitating the transportation of water and other fluids. These joints must provide a secure, leak-proof connection that can withstand internal pressures, external loads, and environmental conditions.
Key Functions of Pipe Joints:
-
Sealing: Prevent leakage of fluids.
-
Alignment: Ensure proper alignment of connected pipe sections.
-
Flexibility: Allow for slight movements due to thermal expansion or ground settlement.
-
Strength: Withstand internal and external forces without failure.
2. Types of Ductile Iron Pipe Joints
2.1 Push-On Joints
Push-on joints are among the most commonly used joints in ductile iron piping systems. They consist of a bell end and a spigot end, with a rubber gasket seated in a groove in the bell. The spigot end is lubricated and pushed into the bell, compressing the gasket to form a watertight seal.
Advantages:
-
Ease of installation without special tools.
-
Suitable for underground applications.
-
Allow for limited angular deflection.
Limitations:
-
Not inherently restrained; may require thrust blocks or restrained joints in certain applications.
2.2 Mechanical Joints
Mechanical joints consist of a bell end, a spigot end, a rubber gasket, a gland, and bolts. The spigot end is inserted into the bell, and the gasket is compressed by the gland and bolts to create a seal.
Advantages:
-
Provide a strong, reliable connection.
-
Allow for angular deflection.
-
Easily disassembled for maintenance or repair.
Limitations:
-
Require more time and tools for installation compared to push-on joints.
2.3 Restrained Joints
Restrained joints incorporate mechanical features, such as locking devices or restraining rings, to prevent axial movement of the pipe sections. These joints are essential in areas subject to high water pressure or where thrust blocks are impractical.
Advantages:
-
Prevent movement under pressure.
-
Eliminate the need for thrust blocks.
-
Suitable for high-pressure applications.
Limitations:
-
Installation may require specialized tools and expertise.
2.4 Flanged Joints
Flanged joints involve connecting two pipe ends using flanges, which are bolted together with a gasket in between to create a seal.
Advantages:
-
Allow for easy disassembly.
-
Suitable for high-pressure systems.
-
Provide a rigid connection.
Limitations:
-
Require precise alignment during installation.
-
Bolting can be time-consuming.
2.5 Grooved and Shouldered Joints
Grooved and shouldered joints use a grooved pipe end and a coupling with a gasket to form a seal. The coupling is tightened over the gasket, creating a secure connection.
Advantages:
-
Quick installation.
-
Allow for some flexibility.
-
Suitable for seismic applications.
Limitations:
-
May not be suitable for all pressure ratings.
3. Comparison of Ductile Iron Pipe Joint Types
Joint Type | Ease of Installation | Flexibility | Disassembly | Suitable for High Pressure | Common Applications |
---|---|---|---|---|---|
Push-On Joint | High | Limited | No | No | Underground water lines |
Mechanical Joint | Moderate | High | Yes | Yes | Water treatment facilities |
Restrained Joint | Low | Low | No | Yes | High-pressure systems |
Flanged Joint | Moderate | Low | Yes | Yes | Industrial applications |
Grooved/Shouldered Joint | High | Moderate | Yes | Moderate | Seismic zones, quick repairs |
4. Standards and Specifications
Ductile iron pipe joints must conform to various standards to ensure quality and compatibility:
-
ANSI/AWWA C111/A21.11: Rubber-Gasket Joints for Ductile-Iron Pressure Pipe and Fittings.
-
ANSI/AWWA C110/A21.10: Ductile-Iron and Gray-Iron Fittings for Water.
-
ANSI/AWWA C115/A21.15: Flanged Ductile-Iron Pipe with Ductile-Iron or Gray-Iron Threaded Flanges.
-
ANSI/AWWA C606: Grooved and Shouldered Joints.
These standards provide guidelines for the design, manufacture, and installation of ductile iron pipe joints, ensuring interoperability and safety.
5. Installation Practices
Proper installation of ductile iron pipe joints is essential for system integrity:
-
Preparation: Inspect pipe ends and gaskets for damage.
-
Lubrication: Apply lubricant to gaskets to facilitate assembly.
-
Alignment: Ensure proper alignment of pipe sections.
-
Assembly: Follow manufacturer instructions for joint assembly.
-
Testing: Conduct pressure tests to verify joint integrity.
Adhering to these practices minimizes the risk of leaks and system failures.
6. Maintenance and Inspection
Regular maintenance and inspection prolong the life of ductile iron pipe joints:
-
Visual Inspections: Check for signs of corrosion or damage.
-
Leak Detection: Monitor for unexplained water loss.
-
Gasket Replacement: Replace gaskets showing signs of wear.
-
Pressure Testing: Regularly test system pressure to ensure joint integrity.
Implementing a routine maintenance schedule helps in early detection of issues and prevents costly repairs.
7. Common Issues and Troubleshooting
Issue | Possible Causes | Solutions |
---|---|---|
Leaking joints | Damaged gaskets, misalignment | Replace gaskets, realign pipes |
Corrosion | Exposure to moisture, chemicals | Apply protective coatings |
Joint displacement | High internal pressure | Install restrained joints |
Difficulty in disassembly | Rusted bolts, gasket adhesion | Use appropriate tools, lubricate |
Addressing these issues promptly ensures the longevity and reliability of the piping system.
8. FAQs
Q1: What is the difference between a push-on joint and a mechanical joint?
Push-on joints are simpler to install, requiring no special tools, and are commonly used in underground applications. Mechanical joints, on the other hand, offer higher flexibility and are often used in above-ground installations or where future disassembly is anticipated.
Q2: Can push-on joints handle high-pressure applications?
While push-on joints are designed to handle standard pressure ratings, they may not be suitable for high-pressure systems without additional measures, such as thrust blocks or restrained joints.
Q3: How do restrained joints differ from other joint types?
Restrained joints incorporate features that prevent axial movement, making them ideal for high-pressure applications or areas where thrust blocks are impractical.
Q4: Are flanged joints suitable for underground installations?
Flanged joints are typically used in above-ground applications due to their rigid nature and the need for precise alignment. They are not commonly used in underground installations.
Q5: What maintenance is required for ductile iron pipe joints?
Regular inspections for signs of wear or damage, monitoring for leaks, and periodic pressure testing are essential for maintaining the integrity of ductile iron pipe joints.
References:
- ANSI/AWWA C111/A21.11 – Rubber-Gasket Joints for Ductile-Iron Pressure Pipe and Fittings
- ANSI – American National Standards Institute
- AWWA – American Water Works Association Standards
- ISO 2531: Ductile Iron Pipes and Fittings – Requirements and Test Methods
- Engineering Toolbox – Ductile Iron Pipe Joints and Their Applications