Ductile iron fittings are essential components in piping systems, offering a combination of strength, durability, and flexibility. Used in a wide range of applications including water distribution, sewage systems, and industrial pipelines, ductile iron fittings provide the foundation for secure and reliable connections. Their ability to withstand high pressure and corrosion makes them ideal for long-term use in demanding environments.
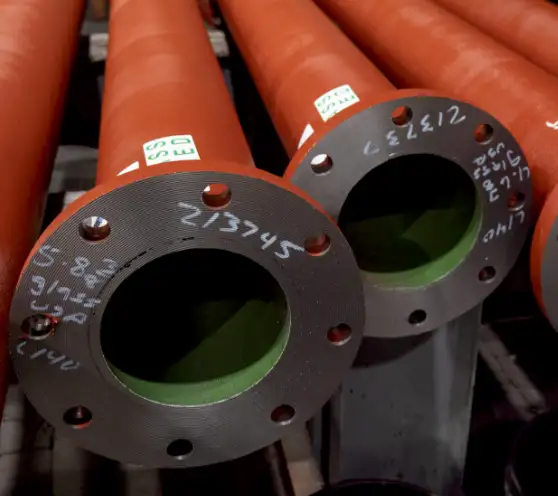
1. What Are Ductile Iron Fittings?
Ductile iron fittings are piping components made from ductile iron, a type of cast iron known for its superior strength and flexibility. These fittings are designed to connect pipes and equipment in a variety of systems, such as municipal water systems, sewage systems, and industrial pipes. The ductile iron material offers greater flexibility than traditional cast iron, which makes these fittings less likely to crack or break under stress.
The strength and durability of ductile iron fittings are enhanced by their casting process, which involves adding small amounts of alloying elements like magnesium to the molten iron to promote the formation of spheroidal graphite structures. This creates a material that combines the benefits of both cast iron and steel, with higher strength and improved impact resistance.
2. Key Types of Ductile Iron Fittings and Their Dimensions
Ductile iron fittings come in a variety of types and sizes to suit different applications. Below, we will detail the most common types of ductile iron fittings and their typical dimensions.
2.1. Elbows
Elbows are used to change the direction of a pipeline, typically at 45° or 90° angles. The dimensions of ductile iron elbows are determined by the size of the connected pipe, and they are available in a variety of angles depending on the system’s requirements.
-
Dimensions: Elbows are typically available in sizes ranging from 1 inch to 24 inches in diameter, but custom sizes are also available for specialized projects.
Type | Angle | Common Sizes | Material | Use |
---|---|---|---|---|
90° Elbow | 90° | 2”, 4”, 6”, 8”, 10” | Ductile Iron | Standard pipeline direction change |
45° Elbow | 45° | 2”, 3”, 4”, 6”, 8” | Ductile Iron | Moderate direction change in systems |
Reducing Elbow | Varies | 4”x2”, 6”x4”, 10”x6” | Ductile Iron | Connecting pipes of different sizes |
Size (in.) |
O.D. (in.) |
B.C. (in.) |
T (in.) |
Bolt Hole Diameter (in.) |
Bolts | |
---|---|---|---|---|---|---|
No. Per Joint |
Size (in.) |
|||||
3 | 7.50 | 6.00 | 0.75 | 3/4 | 4 | 5/8 × 2 1/2 |
4 | 9.00 | 7.50 | 0.94 | 3/4 | 8 | 5/8 × 3 |
6 | 11.00 | 9.50 | 1.00 | 7/8 | 8 | 3/4 × 3 1/2 |
8 | 13.50 | 11.75 | 1.12 | 7/8 | 8 | 3/4 × 3 1/2 |
10 | 16.00 | 14.25 | 1.19 | 1 | 12 | 7/8 × 4 |
12 | 19.00 | 17.00 | 1.25 | 1 | 12 | 7/8 × 4 |
14 | 21.00 | 18.75 | 1.38 | 1 1/8 | 12 | 1 × 4 1/2 |
16 | 23.50 | 21.25 | 1.44 | 1 1/8 | 16 | 1 × 4 1/2 |
18 | 25.00 | 22.75 | 1.56 | 1 1/4 | 16 | 1 1/8 × 5 |
20 | 27.50 | 25.00 | 1.69 | 1 1/4 | 20 | 1 1/8 × 5 |
24 | 32.00 | 29.50 | 1.88 | 1 3/8 | 20 | 1 1/4 × 5 1/2 |
30 | 38.75 | 36.00 | 2.12 | 1 3/8 | 28 | 1 1/4 × 6 1/2 |
36 | 46.00 | 42.75 | 2.38 | 1 5/8 | 32 | 1 1/2 × 7 |
42 | 53.00 | 49.50 | 2.62 | 1 5/8 | 36 | 1 1/2 × 7 1/2 |
48 | 59.50 | 56.00 | 2.75 | 1 5/8 | 44 | 1 1/2 × 8 |
54 | 66.25 | 62.75 | 3.00 | 2 | 44 | 1 3/4 × 8 1/2 |
60 | 73.00 | 69.25 | 3.12 | 2 | 52 | 1 3/4 × 9 |
641 | 80.00 | 76.00 | 3.38 | 2 | 52 | 1 3/4 × 9 |
2.2. Tees
Tees are used to branch off from a main pipeline, creating a ‘T’ shape. Ductile iron tees are designed to handle pressure while allowing fluid to be diverted to other parts of the system.
-
Dimensions: Typically available in diameters ranging from 2 inches to 24 inches, with various branch sizes.
Type | Dimensions | Material | Use |
---|---|---|---|
Equal Tee | 2”x2”, 4”x4”, 6”x6” | Ductile Iron | Branching off main pipeline equally |
Reducing Tee | 6”x4”, 10”x6”, 12”x8” | Ductile Iron | Branching with different diameters |
2.3. Couplings
Couplings are used to connect two sections of pipe. They are available in a wide range of sizes to match the diameter of the pipes being connected.
-
Dimensions: Common sizes range from 1 inch to 12 inches in diameter, but custom sizes are available for larger pipes.
Type | Dimensions | Material | Use |
---|---|---|---|
Standard Coupling | 2”, 4”, 6”, 8” | Ductile Iron | Connecting two similar pipes |
Reducing Coupling | 6”x4”, 10”x6” | Ductile Iron | Connecting pipes of different sizes |
2.4. Flanges
Flanges are used to connect pipes to other system components, such as valves, pumps, or other piping systems. Ductile iron flanges are typically used in applications requiring a robust and leak-proof connection.
-
Dimensions: Standard flange sizes range from 2 inches to 24 inches in diameter. Flange thicknesses and bolt patterns vary based on the pipe’s operating pressure.
Type | Dimensions | Material | Use |
---|---|---|---|
Flat Flange | 2” to 24” | Ductile Iron | Securing pipe connections to equipment |
Slip-on Flange | 4” to 12” | Ductile Iron | Allows for easy connection of pipes |
2.5. Caps
Caps are used to seal the ends of pipes. They are essential for isolating sections of the pipeline during maintenance or installation processes.
-
Dimensions: Available in sizes ranging from 2 inches to 24 inches in diameter.
Type | Dimensions | Material | Use |
---|---|---|---|
End Cap | 2”, 4”, 6”, 8”, 10” | Ductile Iron | Sealing open ends of pipes |
3. Standards for Ductile Iron Fittings Dimensions
Ductile iron fittings are manufactured according to several international standards to ensure their reliability and compatibility across different applications. Some of the most recognized standards for ductile iron fittings include:
3.1. ANSI/ASME Standards
The American National Standards Institute (ANSI) and the American Society of Mechanical Engineers (ASME) set standards for ductile iron fittings used in waterworks and industrial applications. ANSI/AWWA C110 and C153 are commonly cited standards for ductile iron fittings.
3.2. ISO Standards
The International Organization for Standardization (ISO) sets global standards for ductile iron fittings. ISO 2531, for example, covers the specifications for ductile iron pipes and fittings used in water and sewage systems.
3.3. AWWA Standards
The American Water Works Association (AWWA) provides guidelines for ductile iron fittings used in municipal water systems, focusing on factors like material strength, pressure resistance, and corrosion prevention.
4. Benefits of Ductile Iron Fittings
Ductile iron fittings offer several key benefits that make them ideal for a range of industrial and municipal applications:
4.1. Strength and Durability
Ductile iron fittings are incredibly strong, able to withstand high-pressure environments and resist wear and tear over time. This makes them ideal for use in demanding applications like water and gas distribution.
4.2. Corrosion Resistance
Ductile iron’s inherent corrosion resistance is enhanced by coatings such as epoxy or galvanization, providing a long service life in environments exposed to moisture and chemicals.
4.3. Flexibility
Unlike traditional cast iron, ductile iron has improved flexibility, making it less prone to cracking or breaking under stress. This is particularly important in seismic zones or areas subject to shifting ground.
4.4. Cost-Effectiveness
While ductile iron fittings may have a higher initial cost than some alternatives, their long lifespan and low maintenance requirements often make them a more cost-effective solution in the long term.
5. Frequently Asked Questions (FAQs)
1. What are the most common materials used for ductile iron fittings?
The most common materials used for ductile iron fittings are carbon steel and stainless steel. Carbon steel offers strength and durability, while stainless steel provides enhanced corrosion resistance, especially for systems in highly corrosive environments.
2. How do I choose the right size ductile iron fitting for my project?
The right size fitting depends on the diameter of the pipes in your system, as well as the pressure and temperature requirements. It is essential to consult the fitting manufacturer’s specifications and industry standards to ensure compatibility.
3. What is the difference between ductile iron and cast iron fittings?
While both ductile iron and cast iron are used in piping systems, ductile iron has superior tensile strength and flexibility compared to cast iron. This makes ductile iron less likely to crack or break under stress.
4. How are ductile iron fittings installed?
Ductile iron fittings are typically installed using mechanical methods such as bolting or welding, depending on the type of fitting. For some applications, gaskets and O-rings are used to create a secure, leak-proof connection.
5. Are ductile iron fittings resistant to corrosion?
Yes, ductile iron fittings are highly resistant to corrosion, especially when coated with epoxy or other protective coatings. They can be used in a variety of environments, including those with high moisture or chemicals.
Conclusion
Ductile iron fittings are an integral part of modern piping systems, offering unmatched strength, flexibility, and corrosion resistance. Understanding their dimensions, types, standards, and installation methods is essential for ensuring that your piping system operates effectively and reliably. Whether you’re working on municipal water systems, sewage treatment plants, or industrial pipelines, selecting the right ductile iron fittings is crucial for long-term performance and safety.