Ductile iron piping systems rely on a variety of connection methods—each engineered for specific pressures, environments, and installation requirements. This guide covers ten principal connection types (flanged, mechanical joint, push-on, grooved, threaded, welded, restrained, fusion-bonded, cement-mortar lined, and gasketed couplings), detailing material properties, design standards, installation procedures, performance characteristics, and cost drivers.
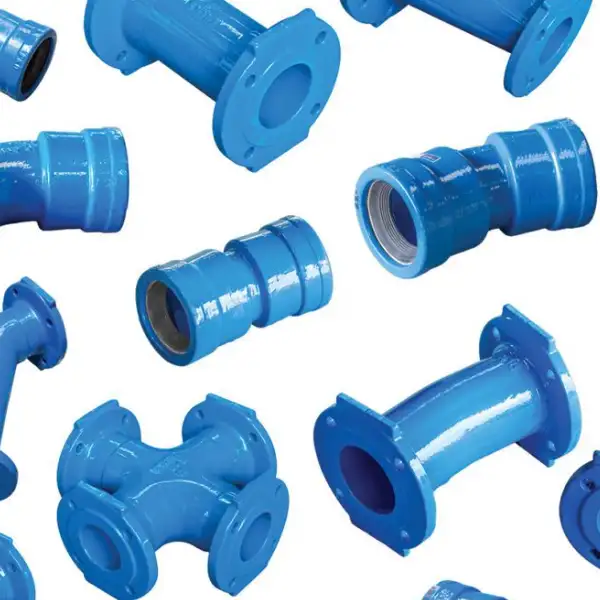
1. Flanged Connections
1.1 Overview
Flanged connections consist of a flat sealing face bolted to a matching flange on pipe or fitting, using gaskets to achieve a leak-tight seal.
1.2 Standards & Dimensions
-
ANSI/AWWA C110/A21.10 governs Class 125 and Class 250 ductile-iron flanges from 2″ to 64″.
-
ASME B16.1 covers Class 125/250 cast-iron flanges, ensuring interchangeability in process piping.
Class | Pressure Rating | Bolt Circle Dia. (4″) | Hole Dia. | No. Holes |
---|---|---|---|---|
125 | 150 psi | 7.50″ | 0.625″ | 4 |
250 | 250 psi | 8.50″ | 0.688″ | 4 |
Table 1: Comparison of Class 125 vs. Class 250 Flange Drilling
1.3 Materials & Gaskets
Gasket materials include EPDM, nitrile, and compressed fiber, selected per fluid compatibility and temperature.
2. Mechanical Joint (MJ) Connections
2.1 Design Principles
Mechanical Joint connections use a gland and rubber gasket to create a seal between the pipe spigot and fitting bell, bolted via a gland ring.
2.2 Standards
-
ANSI/AWWA C111/A21.11 covers MJ joints for sizes 3″–64″, rated up to 350 psi for smaller sizes and 250 psi for larger.
-
ANSI/AWWA C153/A21.53 specifies wall thickness for grooved MJ fittings.
2.3 Installation Steps
-
Clean and lubricate gasket and spigot per manufacturer guidelines.
-
Position gland and hand-tighten bolts evenly.
-
Torque bolts in star pattern to specified ft-lb.
Size Range | Max Pressure | Bolt Torque (in fully assembled MJ) |
---|---|---|
3″–24″ | 350 psi | 75–125 ft-lb |
30″–48″ | 250 psi | 100–150 ft-lb |
Table 2: MJ Connection Torque & Pressure Ratings
3. Push-On (Tyton/Fastite) Joints
3.1 Joint Types
-
Tyton®: Recessed gasket in bell; simple push-in installation.
-
Fastite®: Variations in gasket shape for enhanced restraint.
3.2 Standards & Performance
-
Governed by ANSI/AWWA C111/A21.11 for sizes 3″–64″; non-restrained joint rated 150 psi (standard).
-
Typical leakage allowance: <0.05 gal/min per joint at 2× working pressure.
3.3 Advantages & Limitations
-
Advantages: Rapid installation, low cost, self-lubricating gaskets.
-
Limitations: No inherent restraint—requires thrust blocking or external restraints under certain conditions.
Feature | Push-On Joint |
---|---|
Pressure Rating | 150 psi |
Restraint | External (thrust blocks) required |
Installation | <2 min per joint |
Table 3: Push-On Joint Characteristics
4. Grooved (Victaulic-Style) Connections
4.1 Grooved Coupling Basics
Grooved connections use a coupling housing and rubber gasket engaging grooves on pipe ends to form a sealed joint.
4.2 Standards
-
ANSI/AWWA C606 for ductile-iron grooved fittings.
-
ANSI/AWWA C110/A21.10 dimensions for end-to-end and end-to-face.
4.3 Performance
-
Pressure rated up to 350 psi (3″–36″) with standard Victaulic couplings.
-
Allows angular deflection (up to 7°) and axial movement (±3 mm).
Size Range | Max Pressure | Deflection | Axial Movement |
---|---|---|---|
3″–36″ | 350 psi | 7° | ±3 mm |
Table 4: Grooved Connection Performance
5. Threaded (NPT) Connections
5.1 Overview
Threaded ductile-iron fittings utilize NPT (National Pipe Thread) per ASME B1.20.1 for sizes up to 4″, with taper threads to achieve seal.
5.2 Standards
-
ASME B16.3 for threaded cast-iron fittings (up to 4″).
-
ASME B16.14 for tapped-flange fittings.
5.3 Installation & Sealing
-
Use PTFE tape or pipe dope on male threads to prevent leaks.
-
Tighten to hand-tight plus 3–4 turns using pipe wrench.
Size (in) | Pressure Rating | Thread Spec | Sealant |
---|---|---|---|
½″–4″ | 150 psi | ½″–4″ NPT | PTFE / Pipe Dope |
Table 5: Threaded Connection Data
6. Welded Connections
6.1 Butt-Weld & Socket-Weld
-
Socket-weld: Pipe inserted into fitting socket, fillet welded.
-
Butt-weld: End-preparation and full-penetration weld (butt-welding less common on ductile iron due to cracking risk).
6.2 Welding Procedures
-
Preheat Surface to 350–450 °F; grind to bright metal and remove oxides.
-
Use low-hydrogen electrodes and post-weld heat treatment to avoid brittleness.
7. Restrained Joints
7.1 Thrust Restraint Methods
-
Mechanical Restraint: Integral wedges or external glands.
-
Push-On Restraint Glands: EF-Type (Restrained TYTON®) up to 350 psi.
7.2 Standards
-
ANSI/AWWA C111/A21.11 permits modifications (e.g., restraint rings) if performance criteria met.
8. Fusion-Bonded Epoxy (FBE) Connections
8.1 Coating & Lining
-
Internal: Cement-mortar per ANSI/AWWA C104/A21.4 for potable water resilience.
-
External: FBE coatings for corrosion protection in aggressive soils.
8.2 Impact on Joint Type
-
FBE doesn’t change connection type but adds curing and thickness considerations during installation.
9. Cement-Mortar Lined Connections
9.1 Purpose
Cement lining reduces corrosion and prevents bacterial growth; mandatory for potable services.
9.2 Joint Compatibility
-
Compatible with all mechanical, push-on, and flanged joints; thickness 0.01–0.03 in.
10. Gasketed Couplings
10.1 Double-Gasket Couplings
Used for quick repairs—two gaskets allow coupling with damaged pipe sections.
10.2 Connection & Standards
-
ANSI/AWWA C219 covers couplings up to 24″; rated 200–350 psi.
Six Commonly Asked Questions (FAQs)
1. How do I select the right connection type for my project?
Answer: Selection depends on pressure requirements, pipeline movement, and service conditions. For example, flanged connections (Class 125/250) suit accessibility and high-temperature applications (up to 350 °F with proper gaskets), whereas push-on joints (ANSI/AWWA C111) excel in rapid underground installation but require thrust restraint. Mechanical joints (MJ; ANSI/AWWA C111) offer high-pressure ratings and simple assembly. Grooved couplings (ANSI/AWWA C606) provide flexibility and movement compensation, ideal for seismic zones. Threaded connections (ASME B16.3) are limited to ≤4″ and lower pressures. Welded joints offer permanent, high-integrity connections but demand skilled labor and post-weld heat treatment. Cost considerations include labor, fittings price, and long-term maintenance.
2. What are the corrosion protection strategies for ductile-iron joints?
Answer: Internal cement-mortar lining per ANSI/AWWA C104 prevents corrosion and biofilm; external corrosion protection includes asphaltic coating (AWWA C110), FBE coatings, and cathodic protection systems. Gasket materials must resist soil chemicals and ozone. Grooved couplings and mechanical joints often have factory-applied primers. Proper joint assembly (cleaning, lubrication) prevents coating damage.
3. How do restrained joints differ from non-restrained?
Answer: Non-restrained joints (push-on, flanged without restraint) rely on thrust blocks in the trench. Restrained joints incorporate mechanical features—such as TYTON® restraint rings or grooved coupling wedges—to absorb thrust forces internally. This allows installation in confined spaces or high-pressure zones without extensive concrete anchorage. Design per AWWA C111 modifications ensures joint integrity under surge events.
4. What maintenance is required for different connection types?
Answer:
-
Flanged: Check bolt torque annually; inspect gaskets for hardening; recoat exposed metal.
-
MJ: Retighten gland bolts yearly; replace gaskets if swelling or extrusion observed.
-
Push-on: Monitor for displacement; ensure thrust blocks remain intact.
-
Grooved: Inspect coupling bolts and gasket; replace if deformation noted.
-
Threaded: Rarely used in buried mains; check for leakage at fittings above ground.
-
Welded: Inspect welds via NDT after extreme events; maintain cathodic protection.
5. How does pressure rating influence joint choice?
Answer: Joints must match system maximum working pressure plus surge allowance. Flanged and grooved joints can handle up to 350 psi; MJ up to 350 psi (≤24″); push-on limited to 150 psi unless restrained variants are used. Threaded fittings usually limited to 150 psi for ≤4″. System designers should consider transient pressures and select joint types accordingly, applying surge analysis per AWWA.
6. What are common failure modes and how to mitigate them?
Answer:
-
Gasket extrusion: Use correct thickness/material and torque sequence.
-
Joint separation under surge: Employ restrained variants or proper thrust blocks.
-
Corrosion at joint interfaces: Ensure complete coating coverage and use sacrificial anodes.
-
Bolt corrosion: Use stainless or protected bolts; apply anti-seize compound.
-
Grooved coupling loosening: Inspect and retorque per Victaulic guidelines.
References:
- American Water Works Association (AWWA) Standards Overview – Authoritative source for ductile iron pipe and fitting standards including ANSI/AWWA C110, C111, C104, C153, C606, and C219.
- ASME Codes and Standards – Official site for ASME B16 series standards, covering flanges, threaded fittings, and pipe connections.
- Ductile Iron Pipe – Wikipedia – Well-referenced summary of ductile iron pipe materials, joints, and coatings with links to standards and specifications.
- United States Environmental Protection Agency (EPA) – Regulatory guidelines for potable water system materials and corrosion control, including cement mortar lining and coatings.
- Victaulic Pipe Joining Systems Overview (Victaulic) – Industry-leading manufacturer reference for grooved coupling technology, performance, and standards compliance.