Ductile iron, a high-strength ferrous alloy, derives its unique properties from a carefully balanced chemical composition. Primarily composed of iron (Fe) with 3.2–4.1% carbon (C) and 1.8–3.2% silicon (Si), its microstructure is transformed by trace magnesium (Mg) or cerium (Ce), which convert brittle graphite flakes into resilient spheroidal graphite nodules. This “nodularization” process enhances ductility, toughness, and fatigue resistance. Additional elements like manganese (Mn) and copper (Cu) may refine strength and corrosion resistance.
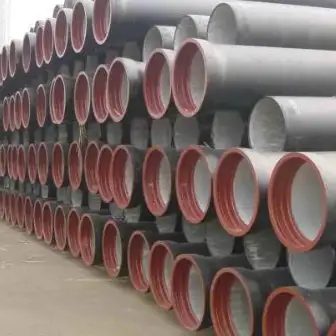
1. Overview of Ductile Iron
Ductile iron is a cast iron alloy known for its improved ductility and strength, which is achieved by adding small amounts of magnesium (Mg) during the casting process. This results in a material with a nodular graphite structure, as opposed to the flaky graphite found in traditional gray cast iron. The chemical composition of ductile iron is a key factor in this transformation.
Key Characteristics of Ductile Iron:
-
Ductility: The ability to withstand deformation under stress without breaking.
-
High Strength: Can withstand heavy loads and pressure.
-
Wear Resistance: Resistant to wear and abrasion.
-
Toughness: Can absorb energy without fracturing.
-
Corrosion Resistance: When alloyed properly, it offers excellent resistance to various environmental factors.
2. Chemical Composition of Ductile Iron
The chemical composition of ductile iron typically consists of iron, carbon, silicon, manganese, sulfur, phosphorus, and magnesium. The exact percentages of these elements can vary depending on the specific grade of ductile iron being produced.
Key Elements in Ductile Iron:
Element | Typical Range (%) | Role in Composition |
---|---|---|
Iron (Fe) | Balance | The primary element in ductile iron, forming the base of the alloy. |
Carbon (C) | 3.00 – 3.50 | Provides hardness and strength but must be carefully controlled. |
Silicon (Si) | 2.00 – 3.00 | Promotes fluidity during casting, aids in graphite formation. |
Manganese (Mn) | 0.30 – 1.00 | Improves strength, hardness, and wear resistance. |
Magnesium (Mg) | 0.03 – 0.06 | Crucial for the formation of nodular graphite, enhancing ductility. |
Sulfur (S) | ≤ 0.02 | Reduces the formation of unwanted sulfides that can impair strength. |
Phosphorus (P) | ≤ 0.05 | Imparts resistance to corrosion but in excess can make the material brittle. |
Breakdown of Key Elements:
-
Iron (Fe): The base metal in ductile iron, constituting the majority of the composition. It provides the structure of the alloy, allowing other elements to perform their specific functions.
-
Carbon (C): In ductile iron, carbon exists in the form of graphite. The carbon content needs to be controlled carefully. Too much carbon can lead to brittleness, while too little can result in lower strength.
-
Silicon (Si): Silicon is crucial for the formation of graphite in the alloy. It also helps to improve the fluidity of the molten iron, making it easier to cast into molds. Silicon also helps to improve corrosion resistance.
-
Manganese (Mn): Manganese is added to ductile iron to improve its strength and wear resistance. It helps to counteract the effects of sulfur, preventing the formation of harmful sulfides that could weaken the material.
-
Magnesium (Mg): Magnesium is the most critical element in the production of ductile iron. When added to molten iron, it causes the graphite to form in a nodular (spherical) shape, which significantly increases the material’s strength and ductility.
-
Sulfur (S): Sulfur is generally undesirable in cast iron as it can form brittle compounds. Therefore, it is kept to a minimum in ductile iron.
-
Phosphorus (P): Phosphorus is an alloying element that can improve the material’s resistance to corrosion. However, too much phosphorus can make the material brittle.
3. Types of Ductile Iron Grades and Their Composition
Ductile iron is available in different grades, each tailored for specific applications and performance requirements. These grades are defined based on their mechanical properties, such as tensile strength and elongation, which are influenced by the chemical composition.
Common Ductile Iron Grades:
Grade | Tensile Strength (psi) | Yield Strength (psi) | Elongation (%) | Typical Applications |
---|---|---|---|---|
Grade 60-40-18 | 60,000 | 40,000 | 18% | General engineering, valve bodies, pump housings |
Grade 80-55-06 | 80,000 | 55,000 | 6% | Automotive parts, heavy-duty machinery components |
Grade 100-70-03 | 100,000 | 70,000 | 3% | Heavy machinery, high-strength automotive components |
Grade 120-90-02 | 120,000 | 90,000 | 2% | High-performance applications, industrial components |
Each grade has a specific combination of elements that provides the right balance of strength, toughness, and ductility for the intended use.
4. The Role of Magnesium in Ductile Iron
Magnesium plays a pivotal role in the formation of ductile iron. It is added to molten iron in small quantities (typically between 0.03% and 0.06%) to produce a nodular graphite structure.
Why Magnesium is Crucial:
-
Graphite Nodule Formation: Magnesium promotes the formation of spherical graphite nodules, which is the defining feature of ductile iron. This nodular graphite structure gives ductile iron its superior strength and ductility compared to other types of cast iron.
-
Improved Toughness: The nodules of graphite in ductile iron help absorb energy during impact, making the material less prone to fracturing.
-
Enhanced Wear Resistance: Ductile iron’s ability to resist wear is also enhanced by the presence of magnesium, making it ideal for applications involving friction and abrasion.
5. How the Chemical Composition Affects the Properties of Ductile Iron
The chemical composition of ductile iron directly influences its mechanical properties and performance in different applications.
Impact on Key Properties:
-
Strength: The carbon content and the formation of graphite nodules are crucial factors in determining the strength of ductile iron. Higher carbon content generally leads to greater hardness but may decrease ductility if not balanced correctly.
-
Ductility: The presence of magnesium and the nodular graphite structure significantly improve ductility. This allows ductile iron to undergo deformation under stress without fracturing, a feature that is essential in applications where shock absorption is critical.
-
Wear Resistance: Manganese and silicon contribute to improved wear resistance. The alloy’s ability to resist abrasion makes it suitable for high-wear environments, such as in pumps and automotive components.
-
Corrosion Resistance: The silicon content plays a major role in enhancing the corrosion resistance of ductile iron. Additionally, phosphorus can improve resistance to corrosion but in excess can compromise mechanical properties.
6. Manufacturing Process and Chemical Composition Control
The production of ductile iron requires precise control over the chemical composition. The process involves melting scrap iron in a furnace, followed by adding alloying elements such as magnesium, manganese, and silicon to achieve the desired properties.
Key Process Steps:
-
Melting: Iron scrap is melted in a furnace. During this stage, the primary goal is to ensure a uniform melt and achieve the right composition.
-
Magnesium Addition: Magnesium is added to the molten iron in a controlled manner, often using a process called “inoculation,” where small amounts of magnesium alloy are introduced to modify the graphite structure.
-
Casting: The molten iron is poured into molds to form the desired shape. The cooling rate and mold design also influence the final composition and properties of the material.
-
Heat Treatment: After casting, the ductile iron may undergo heat treatment to optimize its mechanical properties, including its hardness and toughness.
7. Common Applications of Ductile Iron
Ductile iron is used in a wide range of applications due to its versatility and excellent mechanical properties.
Typical Applications Include:
-
Water and Sewerage Pipes: Ductile iron is commonly used in the construction of pipes for water and sewage systems due to its strength and corrosion resistance.
-
Automotive Components: Engine blocks, crankshafts, and differential cases are often made from ductile iron because of its high strength-to-weight ratio.
-
Heavy Machinery: Parts such as gears, bearings, and housings that are subjected to high stress are often manufactured from ductile iron.
Frequently Asked Questions (FAQs)
1. What is the difference between ductile iron and gray cast iron in terms of chemical composition?
Ductile iron and gray cast iron are both forms of cast iron but differ significantly in their chemical composition and resulting properties. The key difference lies in the amount of magnesium added to ductile iron, which causes the graphite to form in spherical nodules rather than flake-like structures as seen in gray cast iron. This nodular graphite structure gives ductile iron its superior strength and ductility, making it more suitable for high-stress applications. Gray cast iron, on the other hand, is more brittle and is typically used for applications where strength is less critical.
2. How does the carbon content in ductile iron affect its properties?
Carbon is one of the most important elements in cast iron, including ductile iron. In ductile iron, carbon is present as graphite, which influences the material’s hardness and strength. Higher carbon content generally increases hardness but can reduce ductility if not properly balanced. In ductile iron, the carbon content must be carefully controlled to ensure a balance between strength and ductility. Too much carbon can lead to brittleness, while too little can result in lower strength.
3. Can the chemical composition of ductile iron be modified for specific applications?
Yes, the chemical composition of ductile iron can be tailored to meet the requirements of specific applications. For example, increasing the manganese content can enhance wear resistance, while higher silicon levels can improve fluidity and corrosion resistance. The addition of other elements like copper or nickel can further modify the properties of ductile iron for specialized uses, such as in highly corrosive environments or high-temperature applications.
4. 4. What role does sulfur play in the composition of ductile iron?
Sulfur is generally undesirable in ductile iron because it can form sulfides that lead to brittleness and reduce the material’s mechanical properties. For this reason, the sulfur content in ductile iron is carefully controlled, and it is usually kept to a maximum of 0.02%. Excessive sulfur can impair the material’s strength and ductility, making it more prone to cracking or failure under stress.
5. Why is phosphorus included in ductile iron?
Phosphorus is often included in ductile iron in small amounts (typically less than 0.05%) because it helps to improve the material’s resistance to corrosion. However, too much phosphorus can make the material brittle and prone to failure under mechanical stress. Therefore, the phosphorus content must be balanced to provide corrosion resistance without compromising the iron’s strength and ductility.
6. What are the different grades of ductile iron based on chemical composition?
Ductile iron is available in several grades, which are classified based on their mechanical properties, such as tensile strength and elongation. The chemical composition of these grades varies slightly to achieve the desired performance. For instance, Grade 60-40-18 has lower tensile strength compared to Grade 100-70-03, but it offers better elongation. The composition is optimized for the intended application, whether it’s for general engineering, heavy machinery, or automotive parts.