The ductile iron casting process is a highly versatile and efficient method for producing durable, high-strength metal components used across industries such as automotive, construction, and manufacturing. Also known as nodular or spheroidal graphite iron casting, this technique involves adding magnesium or cerium to molten iron, transforming graphite into spherical nodules. This unique microstructure enhances mechanical properties like ductility, impact resistance, and fatigue strength. The process includes steps like pattern design, mold preparation, molten metal treatment, pouring, and post-casting finishing.
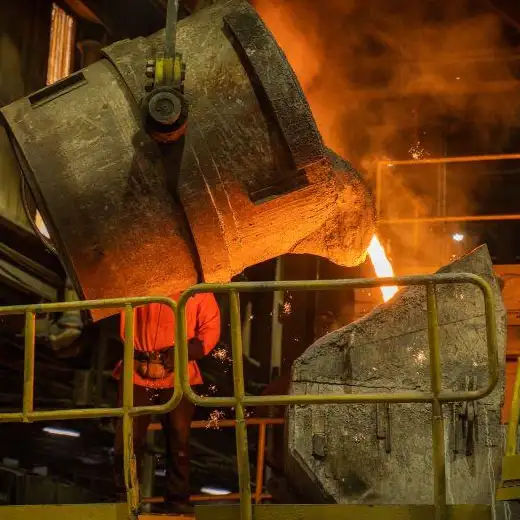
1. Introduction to Ductile Iron Casting
Ductile iron casting is a manufacturing process that produces castings with enhanced strength, ductility, and wear resistance. By adding elements like magnesium to molten iron, the graphite structure transforms from flake form to spherical nodules, imparting these desirable properties.
2. The History and Evolution of Ductile Iron Casting
The development of ductile iron began in the early 20th century. In 1943, Keith Dwight Millis and his colleagues discovered that adding small amounts of magnesium to molten iron could produce castings with improved mechanical properties. This breakthrough led to the widespread adoption of ductile iron in various industries.
3. Materials Used in Ductile Iron Casting
The primary material for ductile iron casting is pig iron, which is produced by smelting iron ore in a blast furnace. Other materials include:
-
Scrap Iron: Recycled iron from previous castings.
-
Alloying Elements: Magnesium, cerium, and other elements added to achieve desired properties.
-
Inoculants: Substances like ferrosilicon added to promote uniform graphite formation.
4. The Ductile Iron Casting Process
4.1 Melting and Alloying
The process begins by melting pig iron and scrap iron in an electric furnace. Alloying elements, particularly magnesium, are added to the molten iron to achieve the desired chemical composition.
4.2 Inoculation
Inoculation involves adding materials like ferrosilicon to the molten iron to promote the formation of graphite in the desired nodular shape. This step is crucial for achieving the mechanical properties of ductile iron.
4.3 Magnesium Treatment
Magnesium is added to the molten iron to convert the graphite from flake form to spherical nodules. This transformation enhances the strength and ductility of the castings.
4.4 Pouring and Molding
The molten iron is poured into molds made from sand, metal, or other materials. The mold design ensures that the casting solidifies in the desired shape.
4.5 Cooling and Solidification
After pouring, the castings are allowed to cool and solidify. The cooling rate is controlled to achieve the desired microstructure and mechanical properties.
5. Heat Treatment Processes
5.1 Annealing
Annealing involves heating the castings to a specific temperature and then slowly cooling them. This process relieves internal stresses and improves the ductility of the material.
5.2 Austempering
Austempering is a heat treatment process that enhances the mechanical properties of ductile iron. The castings are heated to a temperature where the austenite phase is stable and then rapidly cooled to transform the microstructure into bainite, resulting in improved strength and toughness.
6. Mechanical Properties of Ductile Iron
Ductile iron exhibits several advantageous mechanical properties:
-
Tensile Strength: Approximately 60,000 psi (414 MPa).
-
Yield Strength: Approximately 42,000 psi (290 MPa).
-
Elongation: Approximately 10-15%.
-
Impact Resistance: High, due to the spherical graphite structure.
These properties make ductile iron suitable for applications requiring high strength and toughness.
7. Applications of Ductile Iron Castings
Ductile iron castings are used in various industries:
-
Automotive: Engine components, suspension parts, and brake rotors.
-
Construction: Pipes, manhole covers, and structural components.
-
Agriculture: Tractor parts and other machinery components.
-
Mining: Wear-resistant parts for mining equipment.
8. Advantages of Ductile Iron Over Other Materials
Ductile iron offers several advantages:
-
Enhanced Strength and Ductility: The spherical graphite structure provides improved mechanical properties.
-
Wear Resistance: Suitable for applications subjected to abrasive conditions.
-
Castability: Can be molded into complex shapes.
-
Cost-Effectiveness: Offers a balance between performance and cost.
9. Quality Control in Ductile Iron Casting
Quality control is essential to ensure the desired properties of ductile iron castings:
-
Chemical Analysis: Ensures the correct composition of the molten iron.
-
Mechanical Testing: Verifies the strength, ductility, and other properties.
-
Visual Inspection: Detects surface defects and inconsistencies.
-
Dimensional Measurement: Ensures the castings meet the specified dimensions.
10. Environmental Considerations and Sustainability
Ductile iron casting is an environmentally friendly process:
-
Recyclability: Ductile iron can be recycled without significant loss of properties.
-
Energy Efficiency: Modern furnaces and processes reduce energy consumption.
-
Reduced Emissions: Advanced technologies minimize harmful emissions during production.
11. Future Trends in Ductile Iron Casting
The ductile iron casting industry is evolving:
-
Additive Manufacturing: 3D printing technologies are being explored for mold production.
-
Advanced Alloys: Development of new alloying elements to enhance properties.
-
Automation: Increased use of robotics and automation in the casting process.
12. Frequently Asked Questions (FAQs)
1. What is ductile iron casting?
Ductile iron casting is a manufacturing process that involves adding elements like magnesium to molten iron to produce castings with enhanced strength, ductility, and wear resistance. The process includes melting and alloying, inoculation, magnesium treatment, pouring and molding, and cooling and solidification.
2. How does the addition of magnesium affect the properties of cast iron?
The addition of magnesium to molten iron causes the graphite to form in spherical nodules rather than the typical flake shape. This transformation significantly improves the strength and ductility of the cast iron, making it more suitable for demanding applications.
3. What are the common applications of ductile iron castings?
Ductile iron castings are used in various industries, including automotive (engine components, suspension parts), construction (pipes, manhole covers), agriculture (tractor parts), and mining (wear-resistant parts for mining equipment). Their versatility makes them ideal for applications requiring high strength and toughness.
4. What are the advantages of ductile iron over other materials?
Ductile iron offers several advantages:
-
Enhanced Strength and Ductility: The spherical graphite structure provides improved mechanical properties.
-
Wear Resistance: Suitable for applications subjected to abrasive conditions.
-
Castability: Can be molded into complex shapes.
-
Cost-Effectiveness: Offers a balance between performance and cost.
5. How is quality control maintained in ductile iron casting?
Quality control in ductile iron casting involves:
-
Chemical Analysis: Ensures the correct composition of the molten iron.
-
Mechanical Testing: Verifies the strength, ductility, and other properties.
-
Visual Inspection: Detects surface defects and inconsistencies.
-
Dimensional Measurement: Ensures the castings meet the specified dimensions.
These measures ensure that the final product meets the desired specifications and performance standards.
6. What are the environmental benefits of ductile iron casting?
Ductile iron casting is environmentally friendly due to:
-
Recyclability: Ductile iron can be recycled without significant loss of properties.
-
Energy Efficiency: Modern furnaces and processes reduce energy consumption.
-
Reduced Emissions: Advanced technologies minimize harmful emissions during production.
These factors contribute to a more sustainable manufacturing process.
Conclusion
Ductile iron casting is a versatile and efficient manufacturing process that produces castings with superior mechanical properties. By understanding the process, materials, and applications, industries can leverage ductile iron to meet their specific needs. Continuous advancements in technology and quality control further enhance the capabilities and sustainability of ductile iron casting.