Ductile iron castings, prized for strength and ductility, can nonetheless exhibit a variety of defects—ranging from porosity and shrinkage cavities to inclusions and misruns—that compromise mechanical performance and service life. These defects arise from metallurgical factors (e.g., carbon equivalent, inoculation practice), process issues (e.g., gating design, sand system quality), and handling errors (e.g., poor mold assembly). Effective management requires systematic classification, detection (visual, ultrasonic, resonant acoustic), prevention (process control, mold maintenance), and, when necessary, repair techniques (welding, machining, grinding).
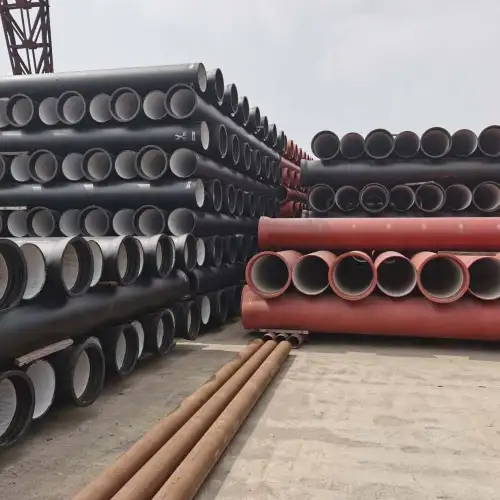
I. Classification of Ductile Iron Casting Defects
Casting defects in ductile iron fall into five main categories:
-
Gas Porosity – Spherical or irregular voids caused by dissolved gases.
-
Shrinkage Defects – Cavities or sub-surface shrinkage due to solidification contraction.
-
Mold Material Defects – Sand inclusions, scabs, and parting line shifts from poor mold quality.
-
Pouring Metal Defects – Misruns, cold shuts, and soldering from improper pouring temperature or gating design.
-
Metallurgical Defects – Inclusions, hard spots, or carbides from poor melt chemistry or inoculation.
Each category encompasses specific defect types that require tailored detection and prevention strategies.
II. Causes and Mechanisms
1. Gas Porosity
Occurs when hydrogen or other gases exceed solubility during solidification, forming bubbles.
-
Sources: Moisture in sand, hydrogen pick-up in melt, lubricant decomposition.
-
Mechanism: As temperature drops, gas solubility decreases, nucleating voids at dendrite arms.
2. Shrinkage Cavities
Solidification contraction without adequate feeding leads to internal cavities.
-
Contributors: Insufficient risering, poor gating design, high freezing range.
-
Metallurgical Influence: Carbon equivalent and inoculation level affect freezing range and feeding.
3. Mold Material Defects
Sand inclusions, scabbing, and shelling from degraded mold face or high permeability.
-
Sand Inclusion: Broken sand grains dislodged into melt.
-
Scabbing: Blister-like detachments when mold face gas escapes poorly.
4. Pouring Metal Defects
-
Misruns: Incomplete filling due to low pouring temperature or slow flow.
-
Cold Shuts: Fusion lines where metal streams fail to fuse.
-
Soldering: Metal adheres to mold cavity walls.
5. Metallurgical Defects
Non-metallic inclusions (oxides, slag) and carbides from melt contaminants and inadequate deoxidation.
III. Detection and Inspection Methods
Method | Defects Detected | Pros | Cons |
---|---|---|---|
Visual Inspection | Surface cracks, misruns | Fast, low cost | Misses subsurface defects |
Magnetic Particle | Surface/near‐surface cracks | Sensitive for ferromagnetics | Requires clean surface |
Ultrasonic Testing | Internal porosity, shrinkage | Deep penetration | Couplant needed, skill‐dependent |
Radiography | Porosity, inclusions | Permanent record | Expensive, safety concerns |
Resonant Acoustic | Global integrity | 100% coverage | Setup cost |
Metallography | Microstructure, inclusions | Definitive analysis | Destructive |
Table 1. Overview of non-destructive and metallurgical inspection methods.
IV. Prevention Strategies
1. Melt Control
-
Degassing: Rotary degassing to remove hydrogen.
-
Deoxidation & Inoculation: Proper silicon, magnesium, and inoculant addition to refine graphite and reduce shrinkage.
2. Mold and Core Quality
-
Sand Selection: Uniform grain size, controlled moisture.
-
Binder Control: Optimum resin and catalyst to avoid scabbing and erosion.
-
Maintenance: Replace worn patterns and repair mold defects promptly.
3. Gating and Risering
-
Optimized Design: Promote directional solidification and proper feeding.
-
Simulation Tools: Use casting simulation software to identify hot spots and shrink risk.
4. Pouring Practices
-
Temperature Control: Maintain within tight ±10 °C window to avoid misruns and cold shuts.
-
Clean Melt Surface: Skim off dross and slag before pouring.
V. Repair and Remediation
Welding Techniques
-
Argon‐Arc Welding: For non-structural defects; minimal heat input to avoid graphite spheroid damage.
-
Specialty Welding Rods: Ni-Fe based for compatibility with ductile iron.
Mechanical Repair
-
Grinding & Filing: Remove flash, smooth misruns.
-
Plugging & Brazing: Seal porosity with braze alloys; reduce fatigue risk.
Coating and Sealing
-
Epoxy Fillers: For non‐critical surface cavities.
-
Metal Spray: Nickel or bronze for dimension restoration.
VI. Impact on Mechanical Properties
Subsurface shrinkage and gas porosity reduce tensile strength, elongation, and fatigue life. A 1% porosity level can drop elongation by up to 20% and fatigue limit by 30%. Inclusions act as crack initiation sites under cyclic loading.
VII. Quality Control & Standards
-
ASTM A536: Specifies tensile and elongation requirements, with allowable defect levels.
-
ISO 1083: Defines ductile iron grades, nodularity, and graphite count.
-
Customer Specs: Many OEMs require radiographic or ultrasonic acceptance criteria per ASTM E446.
VIII. Case Studies
-
Pipe Fittings: A municipal foundry reduced shrinkage defects by 70% after gating redesign and simulation.
-
Pump Housings: Implementation of rotary degassing cut porosity rejects from 8% to 1%.
-
Automotive Brake Calipers: Use of RAM inspection enabled 100% testing, eliminated field failures.
IX. Emerging Technologies & Digitalization
-
Real-Time Monitoring: Thermocouples and infrared cameras detect hot spots.
-
AI Defect Recognition: Machine-vision for rapid visual inspection.
-
Digital Twin: Simulates entire casting process to optimize feed system and minimize defects.
YouTube Tutorial
*Common casting defects in ductile iron and how to detect them.*
Six Common Questions
1. How does nodularity affect defect susceptibility in ductile iron?
Graphite nodularity directly influences shrinkage and porosity. High nodularity (> 90%) promotes uniform solidification and reduces freezing range, minimizing shrinkage cavities. Conversely, poor nodularity creates continuous graphite networks that act as crack initiation sites and exacerbate gas entrapment. Inoculation practice—timing, composition, and cooling rate—must be optimized to achieve ideal spheroidal graphite morphology, balancing mechanical properties with defect resistance. Foundries monitor nodularity via metallographic analysis of sectioned samples, aiming for 6–8 nodules per mm² and a graphite shape factor > 0.8. Proper inoculation reduces the magnitude and frequency of shrinkage defects, while excessive inoculant can lead to carbide formation and hot tears. Hence, nodularity control is pivotal in defect prevention.
2. Why is gating design critical to preventing shrinkage in ductile iron?
Effective gating systems ensure directional solidification, feeding hot spots last and permitting molten metal to compensate for volumetric contraction. Inadequate gating—such as undersized sprues or poor riser placement—leaves sections isolated and starved, leading to internal cavities and piping defects. Simulation tools (e.g., MAGMASOFT, ProCAST) model solidification sequences, highlighting areas prone to shrinkage. By adjusting runner cross-sections, adding chills, or repositioning risers, designers can guide the solidification front to flow inward from desired feed locations. Well-designed gating not only prevents shrinkage but also reduces turbulence and dross entrainment, mitigating both metallurgical and mold-related defects.
3. How do non-metallic inclusions form, and how are they detected?
Non-metallic inclusions—primarily oxides and slag—originate from reactions between molten iron and furnace lining, ladle refractories, or tramp elements. Poor melt handling, inadequate deoxidation, or excessive turbulence during transfer exacerbate inclusion formation. These inclusions weaken ductile iron’s fatigue performance by acting as micro-crack initiation sites under cyclic loads. Detection methods include metallographic sectioning, where polished samples reveal inclusion type, size, and distribution, and ultrasonic testing, which flags clusters of inclusions as scattering zones. Real-time spectroscopic analysis of melt chemistry helps minimize inclusion precursors, while inclusion filters (e.g., ceramic foam) physically trap non-metallic particles before pouring.
4. When is repair welding appropriate for ductile iron defects?
Repair welding addresses defects that compromise surface integrity but are outside critical load-bearing zones. Ideal for sealing pinholes, small blowholes, and scabs, welding must use low-heat input processes (e.g., TIG or argon-arc) and specialized Ni-Fe rods to match ductile iron’s coefficient of thermal expansion and avoid graphite damage. Pre-heating to 200–350 °C and post-weld heat-treatment at 550 °C for 1–2 hours relieve residual stresses and restore ductility. Welding is unsuitable for large internal cavities or defects in high-stress regions; such parts are better remelted or structurally re-designed. Successful repair welding requires skilled welders, rigorous NDT verification (ultrasonic or radiography), and adherence to welding codes (e.g., AWS D10.11).
5. How do foundries balance productivity with defect reduction?
High throughput demands can conflict with defect prevention—faster cycles risk insufficient feeding and higher porosity. Leading foundries implement real-time process monitoring: thermocouples track mold temperatures, and infrared sensors detect hot spot locations, enabling immediate adjustments. Automated molding lines ensure consistent sand compaction and mold assembly, reducing human error in mold defects. Statistical Process Control (SPC) charts track key parameters (pour temperature, inoculant addition, sand moisture), with alarms for out-of-spec events. While slight cycle time increases may occur, overall yield improvements and lower scrap rates (below 3%) justify the investment.
6. What emerging technologies will redefine defect management?
Artificial Intelligence (AI) in visual inspection uses machine-vision to classify surface defects in real time, achieving > 95% detection accuracy and reducing manual inspection labor. Digital twins simulate every pour, updating parameters based on live sensor data to predict and prevent defects before they occur. Additive manufacturing of mold cores allows complex internal cooling channels that minimize hot spots and shrinkage. Blockchain traceability attaches defect data to each casting’s digital record, enabling root cause analysis across the supply chain. These advances promise to push scrap rates toward zero while boosting foundry productivity.
References:
- ASTM A536 – Standard Specification for Ductile Iron Castings
- ISO 1083:2004 – Spheroidal graphite cast irons — Classification
- Casting Defects – Wikipedia Overview of Casting Defects
- AWS D10.11 – Recommended Practices for Welding Cast Iron
- Nuclear Regulatory Commission – Radiographic Testing and Inspection Methods