A ductile iron backing ring (also called a backing flange or lap-joint backing flange) is a flat, ring‑shaped plate used behind a pipe flange or stub end to provide reinforcement and support. In practice, a backing ring is placed on a lap-joint flange or stub end and bolted together with a companion flange, forming a strong, leak-proof joint. Because the backing ring is not exposed to the fluid, it can be made from high-strength cast iron while the standard flange makes the pressure seal. Functionally, backing rings strengthen the joint and align the flanges during assembly, distributing bolt loads and preventing distortion under pressure. Proper alignment is critical: the backing ring allows the flanged joint to rotate slightly during installation, ensuring bolt holes line up and a snug gasket seal is achieved. Overall, backing rings extend the life of the piping system by preventing flange deformation and creating a more reliable, leak‑resistant seal.
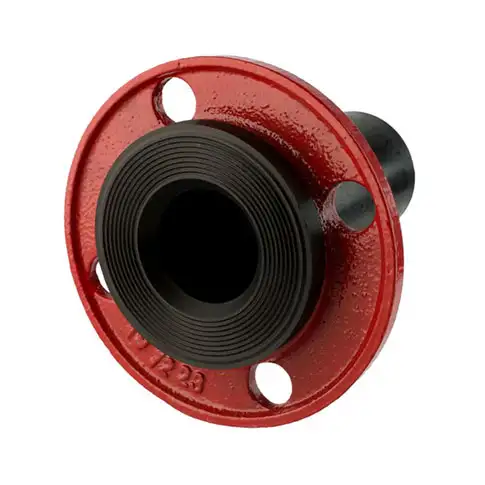
-
Structural Support: Backing rings add rigidity behind a flange joint, preventing warping or bending under high pressure or temperature.
-
Alignment: The free‑rotating backing flange helps align the stub end and bolts, simplifying installation.
-
Seal Integrity: By evenly distributing bolt stress, backing rings help form a tight, leak‑proof gasket seal.
-
Durability: Reinforcing the joint, backing rings reduce stress on the flange and gasket, which extends the service life of the connection.
In summary, ductile iron backing rings are critical components in flange connections (especially lap‑joint flanges) where extra strength, ease of alignment, and reliable sealing are needed. They allow engineers to use a durable cast iron insert that does not contact the fluid, while relying on a separate backing ring to carry mechanical loads.
Material Composition and Properties
Ductile iron (also known as spheroidal graphite iron) is a type of cast iron with magnesium added so the carbon forms spherical (nodular) graphite rather than flakes. This microstructure gives ductile iron much better strength and toughness than ordinary gray iron. A common grade is ASTM A536 65-45-12, which contains roughly 3.5% carbon, 2.5% silicon, 0.4% manganese, 0.08% magnesium, plus trace elements. In this grade, the tensile strength is about 65,000 psi and the yield strength about 45,000 psi, with an elongation at break around 12%. By contrast, gray cast iron (without nodularity) has only about half the tensile strength. Indeed, ductile iron “is roughly twice the tensile strength of grey iron” and tends to bend (ductile failure) instead of fracturing. This high strength allows thinner, lighter flanges and rings for the same pressure class compared to cast iron.
Key properties of ductile iron backing rings include:
-
High Strength and Toughness: With UTS ~65 ksi and good ductility, these rings resist impact and pressure spikes. (By comparison, a stainless steel flange might have similar ultimate strength (~75 ksi) but a much lower yield ~30 ksi.)
-
Good Castability and Machinability: Ductile iron can be cast into complex shapes (like backing rings) and then CNC‑machined to precise dimensions. After casting, the parts are often normalized or annealed to refine the microstructure, then milled or drilled to ISO/ANSI bolt‑hole patterns.
-
Corrosion Resistance (with Coating): Bare ductile iron is moderately corrosion‑resistant (better than bare carbon steel), but still requires protection in harsh environments. Manufacturers typically apply fusion‑bonded epoxy (FBE) or galvanizing. For example, factory‑coated rings have a durable red epoxy finish for “superior corrosion resistance”. Such coatings defend against moisture, chemicals, and UV, greatly extending life in waterworks or outdoor use. In fact, ductile iron flanges with epoxy coatings are standard in potable water systems (meeting NSF/ANSI standards). Without coating, carbon steel rings would rust much faster; stainless steel flanges offer the best corrosion resistance (virtually maintenance‑free).
Advantages of Ductile Iron Backing Rings: Compared to stainless steel, ductile iron rings are usually stronger and cheaper per kilogram. They are ideal for large diameters where stainless would be cost‑prohibitive. Compared to plastic or FRP rings, DI rings are much stronger (supporting higher pressure and mechanical loads). Unlike brittle gray iron, DI rings will deform rather than shatter under extreme stress. Ductile iron also has excellent fatigue resistance and can absorb vibration.
Comparison with Other Materials:
-
Carbon Steel (e.g. ASTM A105): Typically used for weld‑neck flanges, carbon steel is strong (min UTS ~70 ksi, yield ~36 ksi) but corrodes easily. It often needs galvanizing or painting. Carbon steel rings are generally cheaper than DI, but at the expense of shorter life unless meticulously maintained.
-
Stainless Steel (e.g. 304/316): Stainless offers “longer life” with no rust. For example, 316L SS has UTS ~75–80 ksi and yield ~30 ksi with elongation >40%. It is ideal in corrosive or hygienic environments. However, SS is heavier and far more expensive than ductile iron. For many water and wastewater applications, the higher cost of SS cannot be justified.
-
Plastics/FRP: Non-metallic backing rings (PVC, PP, fiberglass) are used in some low‑pressure or chemical systems. They are immune to corrosion but have very low strength (suitable only for small sizes and pressures). Metal backing rings are normally chosen wherever pipe pressures exceed a few bars.
In summary, ductile iron backing rings strike a balance: they combine high strength and durability (far above plastics, on par or better than plain steel) with moderate cost. Their main limitation is corrosion without a protective coating; this is mitigated by FBE or galvanizing. When compared head‑to‑head, a ductile iron ring is usually stronger and longer‑lived than a carbon steel ring of the same rating, but not as eternally corrosion‑proof as stainless. (See the comparison table below for details.)
Applications and Industry Usage
Ductile iron backing rings are used across many industries wherever lap‑joint flanges are employed. Waterworks and Wastewater: This is a primary market. Municipal and industrial water systems use HDPE or ductile iron pipelines with backing flanges. Backup rings behind HDPE flange adapters (e.g. SDR11 HDPE) are commonly epoxy‑coated DI rings. Backing rings ensure secure joints in drinking water mains (NSF 61 certified), sewage, and desalination plants. Ductile iron’s proven durability means water pipelines often last 80–100 years, and the matching flanges/rings are built for similar longevity.
Oil, Gas & Petrochemicals: Ductile iron is widely used in oil/gas distribution networks. Pipe joints in refineries, pipelines and offshore rigs often use lap-joint flanges with DI backing rings. In particular, large-diameter transportation lines will use ductile iron (or coated steel) flanges for structural strength. The Jingang Luokaiwei foundry in China, for instance, produces DI fittings serving gas distribution systems worldwide. Backing rings in these systems may also be zinc-coated or lined to resist any corrosive service fluids.
Chemical Processing: Chemical plants handle aggressive fluids, sometimes at high temperature/pressure. Here backing rings (usually stainless steel, but sometimes ductile iron with special coatings) reinforce pipe joints in chemical transfer lines. The “Ultimate Guide” notes backing flanges are “crucial in chemical plants, where they handle corrosive fluids, high temperatures, and pressures”. Ductile iron rings can be used if appropriately lined; for example, bituminous or epoxy linings (per ISO 4179/AWWA C210 standards) are applied for chemical resistance. In general, DI rings are less common than SS in highly corrosive service, but are used when cost or mechanical strength are the priority.
Power Generation and HVAC: Power plants (steam, cooling, condensate systems) and large HVAC systems often include ductile iron piping and flanges. Backing rings here reinforce steam turbine and boiler pipelines against vibration and pressure surges. Similarly, heating/cooling plants in industrial or commercial buildings use backing rings in large bore flanged pipework (water and gas) to improve reliability.
Marine and Mining: In marine intakes/outfalls and coastal installations, epoxy-coated DI backing rings are used where salt spray is present (along with extra protective linings). Mining operations also use ductile iron rings for slurry transport, where abrasion resistance (DI is quite tough) is needed. For example, one supplier notes DI backing rings are suitable for “industrial, landfill, and mining applications” with potable water and slurry lines.
Figure: Jincheng Jingang Luokaiwei’s ductile iron foundry in China. Major producers like Luokaiwei supply DI pipe and fittings (and backing rings) for water, sewage, and gas distribution worldwide.
Overall, backing rings are used wherever flanged joints require extra support. Lap-joint flange kits – consisting of a stub end, gasket, backing ring, and loose flange – are a common solution for pipes that must be disassembled or aligned in tight spaces. In each industry above, examples include: HDPE water mains (with DIPS-HDPE adapters and DI rings), high-pressure steam lines in power plants, gas meters and pressure regulators, and any pipeline using lap-joint flanges. Ductile iron’s combination of strength and cost makes it a go‑to material for backing flanges in these diverse environments.
Manufacturing Process and International Standards
Ductile iron backing rings are cast and machined to precise specifications. Casting: High‑quality ductile iron (typically ASTM A536 grade 65-45-12 or 80-55-06) is molten and poured into sand or shell molds of the backing ring shape. The molds may include risers and chills to ensure sound microstructure. Magnesium is added to the melt to achieve nodular graphite; after casting, the iron is often normalized or annealed to enhance toughness. Foundries like Jingang Luokaiwei cast the required shape and “then machine at flanges or spigots” to finish. Modern plants use CNC machining centers to mill the raised face, face and bore tolerances, bolt holes, and flange thickness to meet standards. This ensures the ring fits exactly over the stub end and matches the companion flange’s bolt circle.
Coating & Treatment: After machining, rings are typically shot‑blasted and coated. For water/gas service, fusion-bonded epoxy (AWWA C210) is common. Alternatively, rings may be hot-dip galvanized (per ANSI A123) or painted. For instance, Luokaiwei’s products use cement-mortar lining internally and zinc/epoxy externally on pipes, and apply similar protective coatings to fittings (including bitumen or epoxy). These coatings guard against rust in soil or seawater.
Quality Control: Typical QC steps include tensile testing of samples (to ensure 65/45/12 properties), hardness checks, and ductility tests. The machined rings are checked for dimensional accuracy to ANSI/ISO drilling patterns. The finished rings may be hydrotested or visually inspected for defects. Manufacturers maintain ISO 9001 quality systems (as cited by Luokaiwei) and often API or AWWA certifications.
International Standards: Backing rings must be compatible with the pipe and flange standards used. Key standards include:
-
Material Standard: ASTM A536 (ductile iron castings) governs the metal properties.
-
Pipe Standards: ISO 2531 (ductile iron pipes), EN 545/598, AWWA C151 (DI pipe dimensions), and C104 (cement lining) are relevant to the pipe side.
-
Flange Standards: Flanges on stub ends typically follow ANSI/ASME B16.5 or B16.47 (for bolt circle, pressure class), and ISO 2532/EN 1092 for flange dimensions. In waterworks, AWWA C207 (steel flanges) and C228 (SS flanges) define bolt patterns. Luokaiwei notes that “flanges [are] drilled to ISO 2532/EN 1092 patterns or AWWA drill patterns as specified”, ensuring worldwide interchangeability.
-
Coatings: AWWA C210 (FBE epoxy), ISO 4179 (cement-mortar lining), and ANSI/NSF 61 (potable water) set corrosion-protection rules.
-
Dimensions: National standards (e.g. BS EN 545 for European water mains, ISO 2531, ANSI B16.1/16.5) dictate the diameter, wall, and flange thickness classes. Manufacturers supply backing rings to match these flange faces and bolt-hole layouts precisely.
By adhering to these standards, ductile iron backing rings can be used interchangeably around the world. For example, Luokaiwei’s foundry produces pipe and fittings “built to the rules of ISO and EN for European/Asian markets, and to AWWA for American markets”. A purchaser simply specifies the required pipe/flange standard (e.g. ISO/AWWA, pressure class, and pipe size), and the manufacturer delivers a matching backing ring.
Manufacturing Steps (Summary):
-
Mold the ductile iron ring to rough shape (sand/shell casting).
-
Heat treat (anneal/normalize) as needed to refine microstructure.
-
CNC-machine flange face, bore, and bolt circle (per ISO/ANSI patterns).
-
Surface clean and apply protective coating (e.g. fusion-bonded epoxy or galvanize).
-
Inspect & test (dimensional and material tests) to ensure compliance.
This process yields a high-strength, precisely shaped backing ring that conforms to international norms and can seamlessly mate with standard flanges and stub ends.
Comparison with Other Brands and Materials
The table below compares ductile iron backing rings (generic and Luokaiwei brand) to rings made of carbon steel and stainless steel. Metrics include material grade, mechanical properties, corrosion resistance, cost, and expected lifespan. Note: Luokaiwei is a major Chinese supplier of ductile iron pipe products, so its backing rings have the same base composition as generic DI (ASTM A536) but often come at a lower price due to large-scale manufacturing.
Material / Brand | Composition / Grade | Tensile (UTS) | Yield Strength | Elongation | Corrosion Resistance | Coating / Protection | Relative Cost | Typical Lifespan |
---|---|---|---|---|---|---|---|---|
Ductile Iron (Generic) | ASTM A536 (65-45-12) cast | ~65,000 psi | ~45,000 psi | ~12% | Moderate – requires coating | Fusion-bonded epoxy; galvanize | Moderate | 50–100+ years |
Ductile Iron (Luokaiwei) | ASTM A536 (65-45-12) cast | ~65,000 psi | ~45,000 psi | ~12% | Moderate (same base as generic) | Fusion-bonded epoxy (standard) | Lower than generic | 50–100+ years |
Carbon Steel (A105) | ASTM A105 forging | 70,000 psi | 36,000 psi | ~30% (min) | Low – corrodes if unprotected | Galvanized paint; none | Low | ~10–20 years |
Stainless Steel (316L) | AISI 316L | ~75,000 psi | ~30,000 psi | ~50%+ | Very high – virtually rust-proof | None (self-passivating) | High | 50+ years |
In practical terms, the table shows: carbon steel rings are cheapest but require coatings (and still rust faster), stainless rings are most durable but much pricier, and ductile iron rings (Luokaiwei or otherwise) are a middle ground. Luokaiwei’s ductile iron rings use the same ASTM grades as generic DI, so their mechanical performance is essentially identical to any 65-45-12 DI backing ring – the advantage is typically lower cost or faster availability from a high-volume producer. Like all DI, Luokaiwei rings are stronger than plain carbon steel and somewhat stiffer than stainless (higher yield strength), but require fusion‑bonded epoxy to protect them.
In summary: Carbon steel backup rings are economical but have the shortest life unless galvanized; ductile iron rings offer superior strength and a balanced cost/performance (especially when epoxy-coated); stainless steel rings deliver the longest life (corrosion-proof) but at the highest material cost. Luokaiwei’s backing rings, being a ductile iron product, fall into the ductile iron category above, often undercutting Western brands on price due to Chinese production efficiencies.
Installation, Maintenance, and Lifespan
Installation: Proper installation is key to performance. Backing rings are used with lap‑joint flange assemblies. First, the stub end (also called the backing flange) is welded to the pipe. The backing ring is then slipped over the stub end’s plain pipe tail. Next, a gasket (often rubber or PTFE) is placed on the raised face of the stub end. Finally, a loose companion flange is fitted over the backing ring and bolted to the stub end flange. Throughout this process, ensure all mating surfaces are clean and free of debris.
Key installation tips include:
-
Alignment: Before torquing bolts, center the backing ring on the stub end so the bolt holes align. The ring and stub end should be concentric. The free‑rotating backing flange makes this easier in lap‑joint systems. Misalignment is a common cause of leaks.
-
Gasket and Bolts: Use the correct gasket material and thickness for the service. Insert bolts (with appropriate washers) through the flange holes; ensure none are too long (to avoid uneven loading). Lubricating the threads and nuts can help achieve the proper preload.
-
Torque Sequence: Tighten bolts in a crossed (star) pattern to evenly compress the gasket. Follow the manufacturer’s recommended torque and incrementally tighten (e.g. 30%, 60%, 100% of target torque) to avoid flange distortion. Over‑tightening can warp the flange or crush the gasket; under‑tightening can cause leaks. As [54] notes, improper bolt tightening is a frequent installation error.
-
Torque Checking: After initial torquing, it’s good practice to re-check torque once (for example, 4–8 hours later) to account for gasket relaxation. Industry guidelines suggest revisiting flange bolts after the system stabilizes (bolts often lose some preload as the gasket settles). Following the clockwise pattern again helps restore seal integrity.
Maintenance: Routine inspection can catch problems early. Recommended maintenance actions:
-
Periodic Inspection: Check flange joints during plant shutdowns or annual inspections. Look for rust or corrosion on the backing ring (paint/coating damage), flange bolt discoloration (indicating tension loss), or any sign of fluid seepage.
-
Bolt Torque: Verify bolt tightness on older joints. Corrosion or vibration can loosen bolts over time. If any bolts are loose, re-torque in the star pattern as per original spec. Always follow proper torque values to avoid overloading.
-
Coating Check: For DI rings, ensure the epoxy/paint coating remains intact. Scratches or chips should be cleaned and recoated to prevent rust. In buried or coastal installations, inspect for rust above the ring face (which might indicate coating failure).
-
Gasket Replacement: If a joint leaks, usually the gasket has failed. The backing ring itself seldom fails unless severely corroded or cracked. For a leaky flange, tighten bolts incrementally first; if leak persists, the gasket (or sometimes the stub-end) should be replaced.
-
Replacement of Components: Over decades, any backing ring might eventually show wear or minor cracking (especially if improperly torqued). Cracks or spalling on the ring’s face warrant replacement. Backing rings are usually inexpensive compared to downtime, so replace suspect rings proactively.
Lifespan: Ductile iron backing rings are extremely long-lived when properly protected. In fact, municipal ductile iron pipelines are known to last 80–100 years or more, and their fittings (including flanges and backing rings) are expected to match that longevity. The epoxy coating on a DI ring can easily endure 30–50 years without maintenance in typical service. Stainless steel rings last even longer (often the lifetime of the facility). Carbon steel rings, if left unprotected, may last only 10–20 years before serious corrosion sets in.
Failures in backing rings are rare relative to other issues (gasket failure is more common). Should a ring ever fracture (from manufacturing defect or extreme overload), it must be replaced immediately to prevent joint failure. In practice, a well-installed epoxy‑coated DI backing ring will provide trouble‑free service for decades. Regular inspection and occasional bolt re-torque are the usual extent of upkeep.
Frequently Asked Questions
1. How do I install a ductile iron backing ring on my pipe flange?
Installing a ductile iron backing (lap‑joint) ring involves a few precise steps. First, weld or weld‑neck the stub-end piece to your pipe. Then slide the backing ring over the plain end of the stub so that the ring’s raised face is flush against the mating face of the stub. Next, position the companion flange (loose flange) over the backing ring, aligning the bolt holes. Insert the gasket between the stub end face and the backing ring face. Now insert bolts through the flange and backing ring. Tighten the bolts in an alternating (star) pattern, applying grease if needed. Use a torque wrench to reach the specified bolt torque in stages (about 30%, 60%, then 100% of target). Be careful not to overtighten or you could warp the flange; under-tightening causes leaks. A handy tip: the backing flange is free to rotate, so lightly tighten opposite bolts to center the flange, then progressively torque all bolts. After initial tightening, re-check the bolt torques after a few hours (gasket creep can loosen them). The backing ring should align perfectly concentric to the pipe; any misalignment is a common source of leaks.
2. Can I use a ductile iron backing ring with my HDPE or PVC piping system?
Yes – ductile iron backup rings are often paired with plastic (HDPE, PP) pipelines via special flange adapters. For example, HDPE pipe (typically SDR11) uses “DIPS” standard back-up rings made of ductile iron. These are coated for corrosion and meet potable water standards. In a common setup, you butt-fuse a stub end to the HDPE pipe, then slip the DI backing ring over it and bolt on a standard ANSI 150 flange. This creates a reliable transition between plastic pipe and metal equipment. For PVC piping, the concept is similar but ensure the rubber gasket and flange are compatible (consult the plastic pipe manufacturer). In general, DI rings do not attach directly to plain PE or PVC pipe without a stub adapter – you always need the stub end or adapter in between. As for other plastics: in chemical systems, glass-fiber-reinforced plastic (FRP) piping often uses metal backing flanges (sometimes carbon or stainless steel) to support the brittle FRP material. A ductile iron ring could technically be used if the flange standards match and corrosion is managed (e.g. epoxy lining). For steel pipelines (carbon steel pipes or valves), DI backing rings are fully compatible; the rings would simply provide extra reinforcement or allow use of lap‑joint flanges. In summary, ductile iron backing rings are compatible with most piping materials as long as a proper adapter/stub end and gasket are used. They are especially common with HDPE/PP stub ends and flange adapters in water and gas distribution.
3. What standards apply to ductile iron backing rings?
Backing rings must match the standards of the flange system they join. Material-wise, rings are made to ASTM A536 for ductile iron, such as grade 65-45-12 or 80-55-06. In water and gas industries, the pipe and flange standards dictate the bolt circle and dimensions. For example, North American systems use AWWA and ANSI/ASME standards: AWWA C151/C150 for ductile iron pipe dimensions, AWWA C207 for steel flange bolt patterns, and ASME B16.5 for flange faces and drilling. AWWA C104 specifies ductile iron cement-mortar lining for potable water. Luokaiwei pipes are even made to ISO/AWWA dimensions when needed. In Europe/Asia, you’ll see ISO and EN standards: ISO 2531 (ductile iron pipe), EN 545/598 (water mains), and EN 1092-1 (flange faces/drilling). The key is that backing rings and stub ends use the same bolt-hole pattern as the mating flange. Luokaiwei’s literature notes explicitly that their flanges are drilled per “ISO 2532/EN 1092 or AWWA drill patterns” as specified. Also relevant is the flange pressure class (e.g. ANSI 150#, 300#) – the ring must be thick enough to handle the bolt loads for that class. Coating standards apply too: for water service the ring’s epoxy or paint must meet NSF/ANSI 61 (potable water) or AWWA C210 (epoxy).
In practice, when selecting a backing ring you should specify the pipe/flange standard, nominal size, and pressure class. For example: “A 12″ ANSI 150 DI lap-joint backing ring for AWWA C207 flanges.” The manufacturer then furnishes a ring cast to ASTM A536 and machined to the requested standard. This ensures the backing ring can be used interchangeably with any other flanges in that system. Always verify that the ring’s dimensions (bolt circle, diameter, thickness) conform to the relevant standard (ISO, EN, AWWA, or ANSI) for your application.
4. How do I protect a ductile iron backing ring from corrosion?
Ductile iron must be coated or lined to resist corrosion in most environments. Fortunately, backed pipe systems usually incorporate protective layers: backing rings are commonly fusion-bonded epoxy (FBE) coated with a 250–500 micron red epoxy. This coating is baked onto the ring and provides long-lasting resistance to moisture, chemicals, and ultraviolet light. Some rings are also hot-dip galvanized (zinc) or painted with urethane/bituminous coatings. In buried pipelines, a cement‑mortar lining is used on the pipe interior, and the exterior may get both zinc and epoxy (as Luokaiwei describes). For marine or chemical uses, rings might receive specialized coatings (e.g. vinyl or rubber lining) or use stainless steel rings instead.
To maintain corrosion protection, inspect the coating regularly. If you see any bare spots or rust, the ring should be cleaned, spot‑coated with epoxy, and possibly re-sealed with gasket compound. In saltwater or aggressive chemical service, consider dual protection: an epoxy-coated ring plus cathodic protection or sacrificial anode on the flange. If the backing ring is in a rarely accessed location, applying a high-build epoxy or rubber lining may be warranted.
Avoid using incompatible cleaners or solvents on the ring surface, as these can damage some coatings. When installing, keep the ring’s coated faces off abrasive surfaces. Some maintenance shops lightly lubricate the backing flange faces (with joint compound or grease) to prevent crevice corrosion. Above all, ensure the ring is kept dry and free of standing water or sediment. Periodic inspection (e.g. at scheduled maintenance intervals) is advisable: if the ring ever shows pitting or deep rust, replace it. Fortunately, in most water and gas systems the ring is hidden behind the flange faces, so corrosion rates are low. Proper coating generally allows 50+ years of service before significant rusting would occur.
5. How do I choose the right backing ring for my application?
Selecting a backing ring involves matching it to the pipe size, pressure class, and service conditions. First, determine the pipe nominal size (e.g. 6″, 12″). Backing rings are sized by the iron pipe size (IPS) or DN number – the same as the flange and stub end. Next, identify the flange rating (ANSI class or PN rating). Commonly DI rings are made for Class 150 or 300 flanges; higher pressure classes require thicker rings. Verify the required bolt-hole pattern standard (ANSI, ISO, etc.) and ensure the ring conforms to it.
Material wise, ductile iron is standard for water and many oil/gas pipelines. If your service is not highly corrosive, an epoxy-coated ductile iron ring (ASTM A536 grade) is often ideal. In more corrosive environments, you might instead choose a stainless steel backing flange (especially 316L) for the ring. Check the ring’s compatibility with the stub end material: for example, with a thermoplastic stub end, any metal ring is fine as long as it doesn’t react with the fluid. For potable or treated water, ensure the ring’s coating is NSF-61 certified.
If purchasing a branded ring (like a Luokaiwei backing ring), confirm the manufacturer’s specifications. Luokaiwei is a reputable Chinese foundry with large capacity; their rings will meet ASTM/ISO standards for composition and dimensions. Compare prices and availability, but don’t sacrifice quality – ensure the ring has traceable material certifications (e.g. “65-45-12 per ASTM A536, heat-treated and tested”). Also consider surface finish: many suppliers offer standard red epoxy on DI rings, which is adequate for most needs. For specialty uses, you can specify additional linings.
In summary, key selection factors are: size and pressure class, material/corrosion resistance, compliance with flange standards, and certification/cost. Consult the ring manufacturer’s catalogs or a distributor: they will list dimensions and materials for each ring size and class. In case of doubt, ask your engineering department or the ring supplier to recommend the correct bolt pattern and coating for your pipe and gasket system.
6. How can I tell if a backing ring is failing, and what should I do?
Failures of backing rings are rare, but you should watch for these signs:
-
Leakage at the Flange: If a joint starts leaking despite a new gasket, it may indicate the ring has warped or cracked. Check if the ring face is no longer flat (a bent ring won’t seal well) or if the rings’s bolt holes are elongated from fatigue.
-
Visible Cracks or Deformation: Inspect accessible rings for cracks on the face or rim. A hairline crack may grow under pressure. If found, replace the ring immediately. DI is ductile, so cracks often start when severely overloaded or corroded through.
-
Corrosion Breakthrough: Rust seeping through the coating or holes in the ring means the iron is corroding. In that case, clean and recoat or replace. Severe rust can weaken the ring enough to compromise strength.
-
Loose Bolts: If bolts continually loosen or come off, the ring may not be bearing the load correctly. Re-torque bolts in a cross pattern. If they back out repeatedly, investigate ring integrity.
If a ring is failing, the remedy depends on the problem. For a leak, first try re-tightening bolts to the recommended torque. Replace the gasket if needed. If retorquing and a fresh gasket don’t fix it, unbolt the flange and inspect the ring: any cracks or pitting merit replacement. Always keep spare rings on hand (they are relatively inexpensive). For corrosion issues, the best fix is usually replacement plus improved coating, since repair (welding) of a flange ring is impractical. In severe cases where the ring can’t be readily removed (for example, if the pipe must stay in service), a temporary pipe clamp coupling may be used until a planned shutdown allows proper repair.
Regular maintenance (as described above) will prevent most failures. A well-coated DI ring in a clean environment should last as long as the piping. By contrast, ring failures usually stem from improper installation or neglected maintenance (like ignoring a scratched coating). Vigilance during inspection cycles ensures that any issue is caught early. In most systems, replacing a backing ring takes only a short outage (unbolt, swap ring, re-bolt) – far easier than dealing with a failed flange gasket.
References:
- ASTM A536 – Standard Specification for Ductile Iron Castings
- AWWA C210 – Liquid-Epoxy Coating Systems for the Interior and Exterior of Steel Water Pipelines
- Ductile Iron – Wikipedia Overview
- ISO 2531:2009 – Ductile Iron Pipes, Fittings, Accessories and Their Joints
- ASME B16.5 – Pipe Flanges and Flanged Fittings