Drilling and tapping ductile iron pipe is a critical task in a variety of pipeline applications, including water supply systems, wastewater systems, and industrial piping. Ductile iron pipes offer a balance between strength, flexibility, and longevity, making them ideal for high-pressure systems. Proper drilling and tapping techniques are essential to ensure that these pipes maintain their integrity and performance. In this comprehensive guide, we’ll explore all aspects of drilling and tapping ductile iron pipes, including methods, tools, sizes, pricing, and best practices.
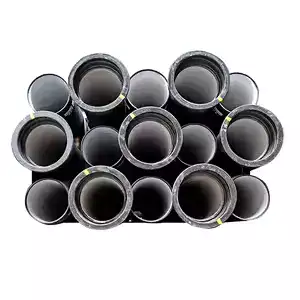
1. Understanding Ductile Iron Pipes
Ductile iron pipes are made from cast iron that has been treated with alloys to improve its strength, durability, and flexibility. These pipes are designed to withstand high pressures and harsh environmental conditions. They are used extensively in water distribution systems, sewage systems, and industrial applications.
Key Properties:
-
Strength: Ductile iron is five times stronger than traditional cast iron.
-
Flexibility: It can bend and withstand external stresses without breaking.
-
Longevity: With proper maintenance, ductile iron pipes can last up to 100 years.
-
Corrosion Resistance: They are often coated with materials like cement mortar, epoxy, or polyurethane to prevent corrosion, particularly in water systems.
Applications:
-
Municipal Water Supply Systems
-
Wastewater Systems
-
Industrial Water and Gas Systems
-
Fire Protection Systems
2. The Importance of Drilling and Tapping
Drilling and tapping ductile iron pipes are essential techniques used to create branch connections and install valves, hydrants, or other system components. These processes allow for the addition of service lines or the installation of mechanical equipment without the need to shut down the entire pipeline system. This is particularly valuable in high-demand systems where downtime must be minimized.
Why Drilling and Tapping are Necessary:
-
Non-disruptive: These processes allow for adding branches or fittings to a live pipeline without significant downtime.
-
Flexibility in System Design: Drilling and tapping give engineers the ability to design systems with greater flexibility for future expansion.
-
Cost-Efficiency: It is more cost-effective to tap existing pipes than to install new lines or create additional connections.
3. Tools and Equipment for Drilling and Tapping Ductile Iron Pipes
Drilling and tapping ductile iron pipes require specific tools to ensure proper operation and safety. The right equipment allows for precise cuts, avoiding pipe damage and ensuring a strong seal.
Essential Tools:
-
Tapping Machines: These are used to cut threads into the pipe and install valves or service lines. They typically feature adjustable settings for different pipe sizes and materials.
-
Drills: Heavy-duty drills are used to create the initial hole in the pipe before tapping. These must be powerful enough to drill through ductile iron.
-
Cutting Tools: Special cutting tools like carbide-tipped bits are used to achieve clean cuts without damaging the pipe.
-
Tapping Inserts: These are used to create the threads in the drilled hole, allowing fittings to be installed securely.
-
Pipe Stands and Clamps: These hold the pipe steady during drilling and tapping to ensure accurate work.
Recommended Tools for Drilling and Tapping Ductile Iron Pipes:
-
Greenlee Tapping Machines
-
Ridgid Drilling Equipment
-
Wachs Valve Operators
-
Barber-Colman Equipment
4. Step-by-Step Guide to Drilling and Tapping
Step 1: Prepare the Pipe
Ensure that the ductile iron pipe is properly secured in place. Clean the area to be tapped, removing any debris or dirt that could interfere with the drilling process.
Step 2: Mark the Drilling Point
Accurately mark the location on the pipe where you intend to drill and tap. Ensure this spot aligns with the design of your system.
Step 3: Drill the Pipe
Using a heavy-duty drill and the appropriate drill bit, carefully drill a hole into the ductile iron pipe. Take your time to maintain control of the drill to ensure the hole is round and free of cracks.
Step 4: Tap the Hole
Once the hole is drilled, use a tapping machine to cut threads into the hole. Make sure to use the correct size tapping insert based on the size of the service line or valve you are installing.
Step 5: Install the Fitting
After the threads are cut, install the appropriate fitting (e.g., valve, tee, or hydrant) into the tapped hole. Tighten the fitting securely to avoid leaks.
Step 6: Pressure Test the Installation
Perform a pressure test to check the integrity of the connection. This ensures that there are no leaks and that the tap is securely sealed.
5. Best Practices for Drilling and Tapping Ductile Iron Pipes
To achieve the best results when drilling and tapping ductile iron pipes, follow these best practices:
Best Practices:
-
Use the Right Tools: Always use equipment specifically designed for ductile iron pipes.
-
Ensure Accurate Measurements: Double-check measurements to ensure the tap is made in the correct spot.
-
Avoid Over-tightening: When installing the fitting, be careful not to over-tighten the bolts, as this can damage the threads or pipe.
-
Work Slowly and Steadily: Take your time during the drilling and tapping process to avoid rushing and making mistakes.
-
Use Lubrication: Apply lubricant to the drill bit and tapping tool to reduce friction and heat, preventing wear and tear on the tools.
6. Sizing Considerations for Drilling and Tapping
When drilling and tapping ductile iron pipes, the size of the hole and the size of the fitting are critical. The hole size must be large enough to accommodate the fitting but not so large that it weakens the pipe.
Factors to Consider:
-
Pipe Diameter: The larger the diameter of the pipe, the larger the drill and tapping machine required.
-
Thread Size: The thread size must match the fitting you are installing. Ensure you use the correct taps for the service lines or valves.
-
Pressure Requirements: Higher pressure systems may require thicker walls or specialized drilling techniques.
Table: Common Sizes for Drilling and Tapping Ductile Iron Pipes
Pipe Diameter | Drill Size (inches) | Tapping Size (inches) | Common Applications |
---|---|---|---|
4 inches | 1 inch | 1/2 inch | Residential water systems |
6 inches | 1 1/2 inches | 1 inch | Industrial water lines |
8 inches | 2 inches | 1 1/2 inches | Commercial buildings, municipal systems |
12 inches | 3 inches | 2 inches | High-pressure distribution systems |
7. Pressure Ratings and Standards for Tapping Ductile Iron Pipes
Pressure ratings are a crucial factor when tapping ductile iron pipes. The pipe’s pressure rating should match the demands of the system. The American Water Works Association (AWWA) and other regulatory bodies provide standards for pressure ratings.
Common Pressure Ratings:
-
AWWA C151 (Ductile Iron Pipe Standard): Specifies pressure ratings for different pipe classes.
-
Pressure Class: Ductile iron pipes typically come in pressure classes ranging from 150 psi to 350 psi, depending on the application.
Ensure that the tapping process does not compromise the pipe’s ability to handle its rated pressure.
8. Costs of Drilling and Tapping Ductile Iron Pipes
The cost of drilling and tapping ductile iron pipes depends on various factors, such as the pipe size, the complexity of the job, and the location of the project. The installation of specialized fittings, valves, or service lines can increase the overall cost.
Cost Breakdown:
-
Equipment Rental: Tapping machines can cost between $500 and $3,000 depending on the size and brand.
-
Labor Costs: Skilled labor for drilling and tapping ductile iron pipes typically costs $50 to $100 per hour.
-
Material Costs: Fittings, gaskets, and valves can range from $5 to $200 depending on the size and type.
Total Project Costs: For a typical installation, expect costs between $500 and $2,500 per connection, depending on the factors listed above.
9. Troubleshooting Common Issues in Drilling and Tapping
Despite the best planning, problems can arise during the drilling and tapping process. Here are some common issues and solutions:
-
Problem: Pipe Cracking
Solution: Use a slower drill speed and apply consistent pressure to prevent overloading the pipe. -
Problem: Misalignment of the Hole
Solution: Ensure that the pipe is securely clamped and that the drill is properly aligned before starting. -
Problem: Leaks Around the Fitting
Solution: Check that the fitting threads are properly cut and that the gasket is in good condition. Tighten the fitting according to specifications.
10. Maintenance and Inspection Post-Drilling and Tapping
Regular inspection is essential to ensure that the tapped hole maintains its integrity and the system functions as expected.
Maintenance Tips:
-
Monitor for Leaks: Regularly check the area around the tapped fitting for any signs of leakage.
-
Pressure Testing: Periodically test the pipe under pressure to ensure that no weaknesses have developed in the tapped area.
-
Corrosion Protection: Consider applying additional corrosion protection if the tapped area is exposed to aggressive environments.
11. Frequently Asked Questions (FAQs)
1. Can I drill and tap ductile iron pipes without shutting off the water supply?
Yes, you can drill and tap ductile iron pipes without shutting off the water supply by using special tools designed for live tapping. This is typically done with a saddle or tapping machine.
2. What is the maximum pressure rating for ductile iron pipes?
Ductile iron pipes are available in pressure ratings ranging from 150 psi to 350 psi or more, depending on the application and the pipe class.
3. How do I prevent leaks when tapping ductile iron pipes?
Ensure that the drilled hole is clean and smooth before tapping. Use the correct size tapping tool and threads, and ensure that gaskets are used and properly installed.
4. What size hole do I need to drill for a 6-inch ductile iron pipe?
For a 6-inch ductile iron pipe, you would typically drill a hole that is 1 1/2 inches in diameter, depending on the type of fitting you are installing.
5. How often should I inspect tapped ductile iron pipes?
It’s a good practice to inspect tapped ductile iron pipes at least once a year, especially in high-pressure or corrosive environments.
6. Can I use PVC fittings on ductile iron pipes?
Yes, PVC fittings can be used with ductile iron pipes, but you need to ensure the proper sealing materials and connectors are used to prevent leaks.