Ductile iron pipes are known for their durability and corrosion resistance, but do they need a tracer wire for detection? While ductile iron is ferromagnetic and can sometimes be located with traditional methods, tracer wires are often recommended for precise underground utility mapping. This article explains when and why tracer wires are used with ductile iron pipes, compares detection methods, and highlights best practices for installation and compliance with industry standards.
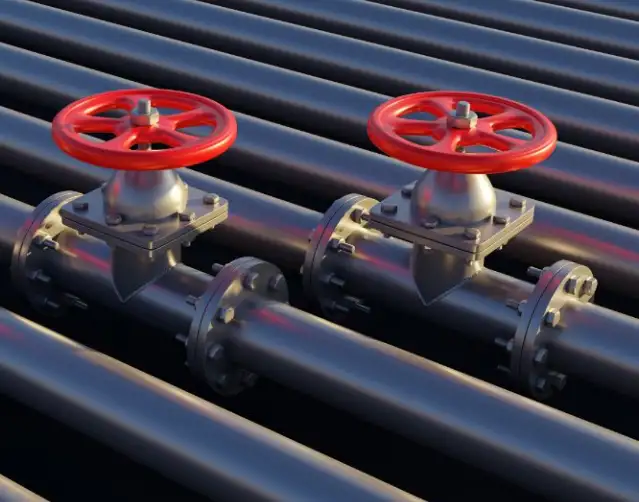
1. Introduction
Ductile iron pipes are widely used in water and wastewater infrastructure due to their strength, durability, and resistance to corrosion. However, when it comes to locating these underground utilities, the question arises: Is tracer wire necessary for ductile iron pipes?
2. What Is Tracer Wire?
Tracer wire is a conductive wire installed alongside underground utilities to facilitate their detection using electromagnetic locating equipment. It serves as a guide for utility locators, enabling them to identify the exact location of buried pipes and cables without the need for excavation. Tracer wire is typically made of copper or copper-clad steel and is insulated to prevent corrosion.
3. Ductile Iron Pipe Overview
Ductile iron pipes are manufactured by adding small amounts of alloying elements to molten iron, resulting in a material with improved mechanical properties compared to traditional cast iron. These pipes are commonly used for potable water distribution, sewage systems, and fire protection lines. They are known for their strength, impact resistance, and longevity.
4. Electrical Conductivity of Ductile Iron
Ductile iron is not a perfect conductor of electricity. While it does conduct electricity to some extent, the rubber-gasketed joints commonly used in ductile iron pipe installations introduce electrical resistance, making the pipe electrically discontinuous. This discontinuity can complicate the use of the pipe as a reliable conductor for locating equipment signals.
5. Necessity of Tracer Wire for Ductile Iron Pipes
Given the electrical discontinuity of ductile iron pipes, relying solely on the pipe for location detection is not advisable. Tracer wire provides a continuous conductive path that can be reliably detected using electromagnetic equipment. Therefore, installing tracer wire alongside ductile iron pipes enhances the accuracy and efficiency of underground utility locating.
6. Industry Standards and Regulations
Various standards and regulations govern the installation of tracer wire with ductile iron pipes. For instance, the City of Waterloo specifies that tracer wire should be taped to the top center of the pipe at 6.0-meter intervals and before and after any valve or fitting. Additionally, all wire dead-end locations must be properly terminated to ensure effective locating.
7. Installation Practices and Guidelines
Proper installation of tracer wire is crucial for its effectiveness. Best practices include:
-
Continuous Installation: Tracer wire should be installed continuously without splices, except at designated access points.
-
Secure Attachment: The wire should be securely fastened to the pipe at regular intervals to prevent movement.
-
Proper Termination: Dead-end locations should be properly terminated to maintain signal continuity.
-
Avoiding Interference: Tracer wire should not be connected to existing foreign or conductive utilities to prevent signal interference.
8. Advantages of Using Tracer Wire
The use of tracer wire with ductile iron pipes offers several benefits:
-
Enhanced Locate Accuracy: Provides a reliable signal for locating equipment.
-
Cost-Effective: Reduces the need for extensive excavation to locate utilities.
-
Compliance with Regulations: Meets industry standards and local regulations.
-
Safety: Helps prevent accidental damage to underground utilities during excavation.
9. Challenges and Considerations
While tracer wire is beneficial, there are challenges to consider:
-
Installation Complexity: Requires careful planning and execution to ensure proper installation.
-
Maintenance: Needs periodic inspection and maintenance to ensure functionality.
-
Environmental Factors: Soil conditions and moisture levels can affect the performance of tracer wire.
10. Case Studies and Real-World Applications
Case studies demonstrate the importance of tracer wire in utility detection:
-
Urban Infrastructure Projects: In densely populated areas, tracer wire has been instrumental in accurately locating water and sewer lines, minimizing disruption during construction projects.
-
Rural Installations: In rural settings, where utility mapping may be less precise, tracer wire ensures that utility lines can be located efficiently, reducing the risk of accidental damage.
11. Frequently Asked Questions (FAQs)
11.1 Is tracer wire required for all ductile iron pipe installations?
While not always mandatory, installing tracer wire with ductile iron pipes is considered best practice to facilitate accurate location detection and comply with industry standards.
11.2 Can ductile iron pipes be located without tracer wire?
It is challenging to locate ductile iron pipes accurately without tracer wire due to their electrical discontinuity and the limitations of relying solely on the pipe’s conductivity.
11.3 What are the consequences of not installing tracer wire?
Failing to install tracer wire can lead to difficulties in locating underground utilities, increasing the risk of accidental damage during excavation and potentially violating local regulations.
11.4 Are there alternatives to tracer wire for locating ductile iron pipes?
Alternatives include using ground-penetrating radar (GPR) or acoustic methods; however, these technologies may not be as reliable or cost-effective as using tracer wire.
11.5 How often should tracer wire systems be inspected?
Tracer wire systems should be inspected periodically, especially after significant weather events or construction activities, to ensure they remain intact and functional.
11.6 What materials are commonly used for tracer wire?
Common materials for tracer wire include copper, copper-clad steel, and aluminum, each offering different levels of conductivity and durability.
12. Conclusion
While ductile iron pipes offer numerous advantages in terms of strength and durability, their electrical properties necessitate the use of tracer wire for effective location detection. Adhering to industry standards and best practices ensures that these utilities can be accurately and safely located, minimizing the risk of accidental damage and enhancing the efficiency of maintenance and repair operations.
References:
- ASTM D6113 – Standard Guide for Installation of Tracer Wire with Underground Utilities
- US Bureau of Reclamation – Tracer Wire and Utility Locating
- Tracer Wire Systems – Overview and Benefits
- FEMA – Tracer Wire and Its Role in Utility Detection
- Municipal Accountability – Tracer Wire Guidelines for Water and Sewer Utilities