When designing pipeline systems, managing thrust forces is critical to prevent joint separation and ensure long-term structural integrity. The Ductile Iron Pipe Research Association (DIPRA) Thrust Restraint Design method provides engineers with reliable solutions to counteract these forces using restrained joints, thrust blocks, and proper soil-pipe interaction.
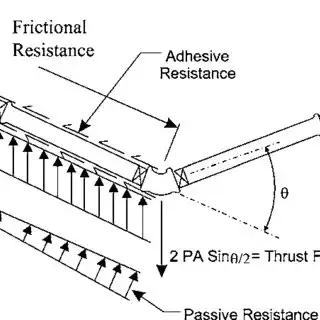
1. Introduction to Thrust Restraint in Ductile Iron Pipelines
Thrust restraint is a critical aspect of designing ductile iron pipelines, especially in pressurized systems. When the flow direction or cross-sectional area changes, such as at bends, tees, or reducers, the internal pressure generates forces that can cause joint separation if not properly restrained. The Ductile Iron Pipe Research Association (DIPRA) provides guidelines and tools to design effective thrust restraint systems, ensuring the structural integrity and longevity of the pipeline.
2. Understanding Thrust Forces and Their Implications
Thrust forces arise due to changes in the direction or size of the pipe, leading to an imbalance between the internal pressure and the resisting forces. These forces can result in:
-
Joint Separation: If not adequately restrained, the pressure can cause joints to separate, leading to leaks or failures.
-
Pipe Movement: Unrestrained pipes may shift, causing misalignment and potential damage to the system.
-
Structural Damage: Excessive thrust forces can compromise the surrounding soil and structures.
Proper thrust restraint ensures that these forces are effectively managed, maintaining the pipeline’s operational efficiency and safety.
3. DIPRA’s Thrust Restraint Design Methodology
DIPRA’s approach to thrust restraint design is based on conservative engineering principles and extensive research. The methodology involves:
-
Assessment of Thrust Forces: Calculating the magnitude and direction of thrust forces at various points in the pipeline.
-
Soil Interaction Analysis: Evaluating the soil’s ability to resist pipe movement through parameters like soil cohesion and friction angle.
-
Design of Restraint Systems: Selecting appropriate restraint methods, such as thrust blocks or restrained joints, based on the specific conditions.
-
Safety Factors: Incorporating safety factors to account for uncertainties and ensure a margin of safety in the design.
This comprehensive approach helps in designing robust thrust restraint systems tailored to the specific requirements of each project.
4. Key Components in Thrust Restraint Systems
Effective thrust restraint systems consist of several key components:
-
Thrust Blocks: Concrete structures placed against the pipe to resist thrust forces through bearing pressure.
-
Restrained Joints: Specially designed joints that prevent axial movement by interlocking pipe sections.
-
Anchor Blocks: Structures used to anchor the pipeline at critical points, preventing movement.
-
Tie Rods and Bolts: Mechanical devices that provide additional restraint by connecting pipe sections or components.
Each component plays a vital role in ensuring the pipeline’s stability and resistance to thrust forces.
5. Calculation Methods for Thrust Restraint
DIPRA provides tools and guidelines for calculating the required thrust restraint:
-
Thrust Force Calculation: Determining the force generated due to internal pressure and changes in direction or size.
-
Frictional Resistance: Calculating the resistance offered by the soil against pipe movement.
-
Required Length of Restraint: Determining the length of pipe that needs to be restrained to effectively counteract the thrust forces.
These calculations are essential for designing systems that can adequately handle the expected thrust forces.
6. Materials Used in Thrust Restraint Systems
The selection of materials for thrust restraint components is crucial for their performance and durability:
-
Ductile Iron: Known for its strength and ductility, making it ideal for restrained joints and fittings.
-
Concrete: Used in thrust blocks and anchor blocks for its compressive strength.
-
Steel: Employed in tie rods and bolts for additional restraint.
-
Polyethylene: Used for encasing ductile iron pipes to prevent corrosion.
Choosing the right materials ensures the longevity and reliability of the thrust restraint system.
7. Installation Techniques and Best Practices
Proper installation is critical for the effectiveness of thrust restraint systems:
-
Alignment: Ensuring that pipes are correctly aligned to prevent undue stress on joints.
-
Compaction: Properly compacting the soil around the pipe to enhance frictional resistance.
-
Placement of Thrust Blocks: Positioning thrust blocks at appropriate locations to effectively counteract thrust forces.
-
Inspection: Regularly inspecting the restraint systems during and after installation to ensure integrity.
Adhering to these practices helps in achieving a reliable and durable thrust restraint system.
8. Case Studies and Real-World Applications
Several projects have successfully implemented DIPRA’s thrust restraint design:
-
Urban Water Distribution System: Utilized restrained joints and thrust blocks to manage thrust forces in a densely populated area.
-
Industrial Complex Pipeline: Employed anchor blocks and tie rods to secure the pipeline against high-pressure conditions.
-
Rural Water Supply Project: Implemented thrust restraint systems in challenging soil conditions to ensure system stability.
These case studies demonstrate the practical application and effectiveness of DIPRA’s design methodology.
9. Common Challenges and Solutions
Designing and implementing thrust restraint systems can present challenges:
-
Variable Soil Conditions: Differing soil types can affect frictional resistance. Solution: Conduct thorough soil analysis and adjust design parameters accordingly.
-
Space Constraints: Limited space may hinder the installation of restraint components. Solution: Opt for compact restraint systems and innovative design solutions.
-
High Pressure Conditions: Elevated internal pressures can increase thrust forces. Solution: Use materials with higher strength and incorporate additional restraint measures.
Addressing these challenges ensures the reliability and safety of the pipeline system.
10. Frequently Asked Questions (FAQs)
Q1: What is the purpose of thrust restraint in ductile iron pipelines?
Thrust restraint is essential to counteract the thrust forces generated by changes in the direction or size of the pipeline. Without proper restraint, these forces can cause joint separation, pipe movement, and structural damage.
Q2: How does DIPRA assist in thrust restraint design?
DIPRA provides guidelines, design methodologies, and tools, such as the Thrust Restraint Calculator, to help engineers design effective thrust restraint systems tailored to specific project requirements.
Q3: What factors influence the design of thrust restraint systems?
Key factors include internal pressure, pipe size, soil properties, pipe alignment, and the type of fittings used. These factors determine the magnitude of thrust forces and the necessary restraint measures.
Q4: Can thrust restraint systems be retrofitted into existing pipelines?
Yes, thrust restraint systems can be added to existing pipelines during maintenance or upgrades. However, careful assessment of the current system’s condition and design is necessary to ensure compatibility and effectiveness.
Q5: What are the consequences of inadequate thrust restraint?
Insufficient thrust restraint can lead to joint separation, pipeline misalignment, leaks, and potential system failures. This underscores the importance of proper design and installation of restraint systems.
11. Conclusion
Thrust restraint is a fundamental aspect of ductile iron pipeline design, ensuring the system’s stability and longevity. By understanding the principles, methodologies, and best practices outlined by DIPRA, engineers can design and implement effective thrust restraint systems that safeguard the integrity of the pipeline infrastructure.
References:
- Ductile Iron Pipe Research Association (DIPRA) – Official Website
- ASTM F1185 – Standard Specification for Ductile Iron Fittings, 3 in. through 48 in. (75 mm through 1200 mm)
- National Academy of Sciences – Design and Installation of Ductile Iron Pipes and Fittings
- FEMA – Design and Installation of Thrust Restraint Systems
- Washington Suburban Sanitary Commission – Pipeline System Design