In the world of engineering and manufacturing, ductile iron and cast steel are two of the most commonly used materials for producing strong, durable components. Both materials are used in a variety of industrial applications, but they have different properties, advantages, and limitations. Understanding the difference between ductile iron and cast steel is essential for selecting the right material for specific applications.
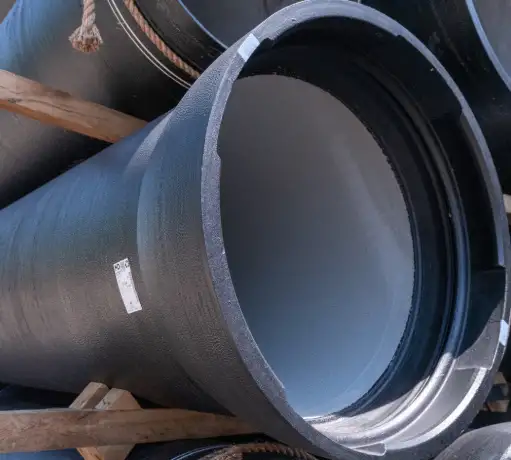
What is Ductile Iron?
Ductile iron, also known as nodular cast iron or spheroidal graphite iron, is a type of cast iron that is designed to be more durable and ductile compared to traditional grey cast iron. The addition of magnesium to the molten iron causes the graphite to form in spherical shapes rather than flakes. This results in improved mechanical properties, particularly in terms of strength, toughness, and ductility.
Key Characteristics of Ductile Iron:
-
Spheroidal Graphite Structure: The graphite in ductile iron forms nodules (spheres) rather than flakes, which helps to prevent the iron from being brittle.
-
High Strength: Ductile iron has significantly higher tensile strength and yield strength compared to traditional cast iron.
-
Improved Toughness: The nodular graphite structure enhances the material’s ability to withstand shock and impact, making it more suitable for high-stress applications.
-
Good Castability: Like other forms of cast iron, ductile iron is easy to cast into complex shapes and components.
Common Uses of Ductile Iron:
-
Automotive components such as crankshafts, suspension parts, and engine blocks.
-
Infrastructure applications like water pipes, sewer systems, and manhole covers.
-
Heavy-duty machinery components, such as gears and brackets.
What is Cast Steel?
Cast steel refers to a group of carbon and alloy steels that are produced through the casting process. Unlike cast iron, which is composed primarily of iron and carbon, cast steel has a higher concentration of steel and a lower carbon content. The casting process allows cast steel to be molded into various shapes, offering a versatile material for many industrial applications.
Key Characteristics of Cast Steel:
-
Composition: Cast steel is made primarily of iron and carbon, with alloying elements such as manganese, chromium, and nickel often added to enhance specific properties.
-
Higher Strength: Cast steel generally offers higher tensile strength and impact resistance than most forms of cast iron, making it ideal for structural components and load-bearing parts.
-
Ductility and Toughness: Due to its steel content, cast steel is more ductile and tougher than cast iron, allowing it to withstand bending, stretching, and other forms of stress.
-
Versatility: Cast steel can be alloyed with various elements to meet the requirements of specific applications, such as heat resistance or corrosion resistance.
Common Uses of Cast Steel:
-
Structural components for bridges and buildings.
-
Components in heavy machinery, including gears, shafts, and bearings.
-
Parts in the aerospace, automotive, and defense industries, such as turbine blades and military equipment.
Chemical Composition of Ductile Iron vs. Cast Steel
The chemical composition of ductile iron and cast steel plays a crucial role in determining their mechanical properties and suitability for various applications. Below is a comparison of their typical compositions:
Element | Ductile Iron | Cast Steel |
---|---|---|
Carbon (C) | 3.0–4.0% | 0.1–0.6% |
Silicon (Si) | 2.0–3.0% | 0.2–1.0% |
Manganese (Mn) | 0.5–1.0% | 0.5–1.5% |
Sulfur (S) | 0.08% max | 0.05–0.15% |
Phosphorus (P) | 0.1–0.2% | 0.05–0.1% |
Nickel (Ni) | 0.0–0.1% | 0.5–5.0% |
Chromium (Cr) | 0.0–0.1% | 0.5–2.0% |
Key Differences in Composition:
-
Ductile Iron: High carbon content (typically around 3.0–4.0%) and a significant amount of silicon to promote graphite formation.
-
Cast Steel: Much lower carbon content (0.1–0.6%), with higher amounts of alloying elements like manganese, nickel, and chromium to improve mechanical properties such as strength and corrosion resistance.
Mechanical Properties Comparison
The mechanical properties of ductile iron and cast steel differ significantly due to their composition. While both materials are strong and durable, cast steel generally offers better strength, toughness, and versatility.
Property | Ductile Iron | Cast Steel |
---|---|---|
Tensile Strength | 400–900 MPa | 400–1,100 MPa |
Yield Strength | 300–700 MPa | 350–1,000 MPa |
Elongation | 3–5% | 10–30% |
Hardness | 170–230 HB | 180–300 HB |
Impact Strength | Moderate | High |
Fatigue Strength | High | Very High |
Key Takeaways:
-
Tensile Strength: Cast steel typically has higher tensile strength, making it better suited for high-load applications.
-
Ductility: Cast steel’s higher elongation and impact resistance make it more ductile than ductile iron.
-
Impact Strength: Cast steel is generally more resistant to impact and shock loading compared to ductile iron.
Manufacturing Processes of Ductile Iron and Cast Steel
Both ductile iron and cast steel are produced through casting, but the specific processes differ due to their composition and material properties.
Ductile Iron Manufacturing Process:
-
Melting: The raw iron is melted in a furnace, along with alloys like silicon and carbon.
-
Magnesium Addition: Magnesium is added to the molten metal to convert the graphite structure from flakes to nodules.
-
Casting: The molten ductile iron is poured into molds to form the desired shape.
-
Cooling and Solidifying: After casting, the material is allowed to cool and solidify before being machined into finished parts.
Cast Steel Manufacturing Process:
-
Melting: Steel scrap or iron is melted in an electric arc furnace or induction furnace, along with alloying elements (manganese, nickel, chromium, etc.).
-
Pouring and Casting: The molten steel is poured into molds, similar to ductile iron.
-
Heat Treatment: Cast steel may undergo heat treatment processes such as annealing, quenching, or tempering to improve its mechanical properties.
-
Machining: After cooling, the cast steel is machined to achieve the desired final shape and specifications.
Applications of Ductile Iron and Cast Steel
Both materials are used extensively in industrial applications, but their distinct properties make them suitable for different types of components.
Applications of Ductile Iron:
-
Automotive Industry: Engine blocks, suspension components, and crankshafts.
-
Infrastructure: Pipes for water and sewage systems, manhole covers, and stormwater drains.
-
Heavy Machinery: Gears, brackets, and housings for construction and mining equipment.
Applications of Cast Steel:
-
Structural Components: Bridges, beams, and frames in buildings.
-
Heavy Machinery: Parts like gears, shafts, and bearings used in manufacturing equipment and power plants.
-
Aerospace and Defense: Components such as turbine blades and military-grade parts that require high strength and resistance to impact.
Advantages and Disadvantages
Advantages of Ductile Iron:
-
Good Castability: Easier to cast into complex shapes than steel.
-
High Wear Resistance: Suitable for applications where wear resistance is important.
-
Moderate Cost: Generally more affordable than cast steel.
Disadvantages of Ductile Iron:
-
Lower Strength: Less strong than cast steel.
-
Limited Ductility: While it is more ductile than traditional cast iron, it is not as ductile as cast steel.
Advantages of Cast Steel:
-
High Strength and Toughness: Superior mechanical properties make cast steel ideal for high-load applications.
-
Versatility: Can be alloyed to meet specific requirements (e.g., heat resistance, corrosion resistance).
Disadvantages of Cast Steel:
-
More Expensive: The manufacturing process is more expensive, and the material itself costs more.
-
Lower Wear Resistance: Generally, cast steel is not as wear-resistant as ductile iron.
Frequently Asked Questions (FAQ)
1. Which is stronger: ductile iron or cast steel?
Cast steel is generally stronger than ductile iron. Cast steel has a higher tensile strength, ranging from 400 to 1,100 MPa, whereas ductile iron typically ranges from 400 to 900 MPa. This makes cast steel more suitable for high-load applications and structural components.
2. Is ductile iron more cost-effective than cast steel?
Yes, ductile iron is generally more cost-effective than cast steel. The manufacturing process for ductile iron is simpler, and the material itself is less expensive, making it a good choice for applications where high strength is not the primary requirement.
3. What is the main difference in the chemical composition of ductile iron and cast steel?
The main difference lies in the carbon content and the presence of alloying elements. Ductile iron has a higher carbon content (3.0–4.0%) and silicon (2.0–3.0%) to promote the formation of nodular graphite. Cast steel, on the other hand, has a lower carbon content (0.1–0.6%) and higher amounts of alloying elements like manganese, nickel, and chromium to improve strength and ductility.
4. Can ductile iron be used in structural applications?
While ductile iron is strong and tough, it is generally not used for structural applications that require the highest strength and toughness. Cast steel is typically preferred for structural components such as beams, frames, and load-bearing parts.
5. How does the heat treatment process affect cast steel?
Heat treatment processes such as quenching, tempering, and annealing are often used to enhance the mechanical properties of cast steel. These processes can increase tensile strength, hardness, and resistance to impact, making cast steel suitable for demanding applications.
6. Can ductile iron be used in aerospace applications?
Ductile iron is generally not used in aerospace applications, as it lacks the strength and heat resistance required for high-performance components like turbine blades. Cast steel, on the other hand, is used in certain aerospace applications due to its superior mechanical properties.
Conclusion
In conclusion, both ductile iron and cast steel are versatile materials with distinct properties that make them suitable for different applications. Ductile iron is cost-effective, highly wear-resistant, and ideal for casting complex shapes. Cast steel, on the other hand, offers superior strength, toughness, and ductility, making it ideal for high-load, structural, and high-performance applications. Understanding the differences between these two materials will help you select the right one for your project, ensuring the best performance and cost-effectiveness.