Ductile iron (DI) and high-density polyethylene (HDPE) pipes are both widely used in potable water, wastewater, and industrial piping systems. Joining these two disparate materials requires specialized transition fittings, couplings, and installation practices to ensure leak-free, restrained, and durable connections.
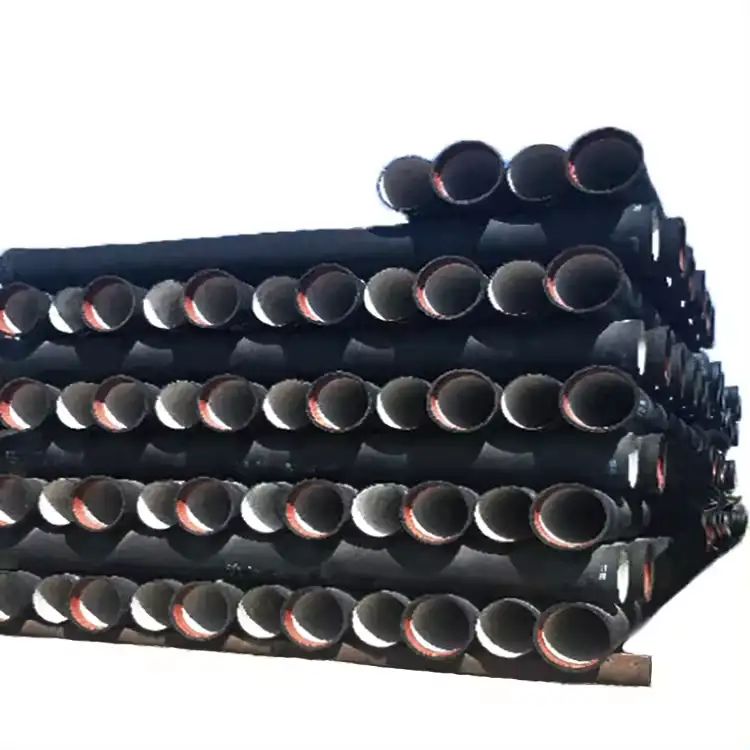
1. Introduction to Ductile Iron–HDPE Transition
Ductile iron pipe (DIP) has been a mainstay of water and wastewater distribution since the mid-20th century due to its high strength, impact resistance, and long service life (over 100 years in many cases). However, HDPE pipe has gained popularity over the past few decades for its corrosion resistance, flexibility, and ease of installation, especially in trenchless applications. In many retrofit or expansion projects, engineers must connect new HDPE segments to existing DI mains. Directly mating these dissimilar materials is non-trivial because of differences in stiffness, thermal expansion, and joint behavior. Transition fittings—often consisting of a DI-end bolted coupling and a HDPE end fusion/barb system—provide the mechanical and hydraulic integrity required in potable water and pressure applications.
2. Material Properties: Ductile Iron vs. HDPE
2.1 Ductile Iron
-
Composition & Manufacture: Ductile iron is cast from molten iron with added magnesium or cerium to produce spheroidal graphite nodules. Typical grades (ASTM A536 Grade 65-45-12) yield tensile strengths of 65,000 psi and elongation of 12%.
-
Mechanical Characteristics: High tensile strength, good fatigue resistance, and stiffness (Young’s modulus ≈ 200 GPa) make DI ideal for above-ground and buried applications subject to hydraulic surge.
-
Corrosion Protection: Cement-mortar lining plus external polyurethane or bituminous coatings extend service life; cathodic protection can also be applied.
2.2 HDPE
-
Composition & Grades: HDPE (commonly PE4710 or PE3408) is a polymer with high molecular weight, produced by compression or gas-phase processes. Typical hoop tensile strength is 3,000–4,500 psi, elongation >800%.
-
Mechanical Characteristics: Low stiffness (Young’s modulus ≈ 1 GPa) and high flexibility allow deflection around obstacles and vibration absorption, but require special restraint at rigid connections.
-
Chemical & Abrasion Resistance: Excellent resistance to corrosion, chemicals, and abrasion, making HDPE favorable for wastewater and corrosive environments.
3. Applicable Standards and Certifications
Proper connections must comply with internationally recognized standards to ensure safety and performance.
Standard | Material/Component | Key Requirements |
---|---|---|
AWWA C111/A21.11 | Mechanical Joints | MJ adapters, gaskets, restraint without external tie rods |
AWWA C219 | Bolt-type Couplings | Sleeve, gasket, bolts, torque requirements |
ASTM F714 | PE Pipe Specifications | Material designations, pressure ratings, hydrostatic testing |
ASTM D2609 | Electrofusion Fittings | Electrical characteristics, fusion parameters |
ISO 17165-1 | Ductile Iron Pipes | General requirements, testing, marking |
EN 12201 | HDPE Pipes for Water Supply | Dimensions, tolerances, pressure classes |
Each coupling or adapter must also meet potable-water certification (e.g., NSF/ANSI 61) and comply with local codes.
4. Connection Methods Overview
4.1 Flange Adapters
Flange adapters bolt to a DI backing flange and provide a standard flange face to mate with a HDPE flange stub end.
-
Installation:
-
Machine and weld or clamp a flange onto HDPE stub end.
-
Align stub end flange to DI backing flange; insert gasket.
-
Bolt per ANSI B16.1 or EN 1092 patterns.
-
-
Advantages:
-
Fully restrained, dismantlable, and can accommodate misalignment.
-
Suitable for large-diameter or buried applications where traction is critical.
-
-
Considerations:
-
Requires precise flange machining or specialized HDPE flange joints; cost is moderate to high.
-
4.2 Mechanical (Bolted) Transition Couplings
Products such as JCM Series 212 or Gruvlok FIG-7307 employ a DI ductile-iron sleeve with gasket(s) and bolts to compress onto both pipe ends.
-
Construction: DI outer sleeve, EPDM gasket, carbon-steel bolts.
-
Methods:
-
Plain-end DI on one side, grooved or plain HDPE on the other.
-
Multi-barb HDPE end or grooved adaptor for coupling retention.
-
-
Advantages:
-
Quick installation, no fusion required.
-
Accommodates limited angular deflection (3–5°).
-
-
Limitations:
-
Belted restraint relies on gasket friction; not fully restrained against surge unless backed by Megalug® segments.
-
4.3 Restrained Megalug® Couplings
A Megalug® flange is attached to the DI side, and bolts clamp gaskets into a solid sleeve to resist axial pull-out.
-
Mechanism: Lug assemblies bite into DI pipe barrel, transferring thrust forces into sleeve and gasket.
-
Standards: Meets AWWA C222 for restrained joints.
-
Use Case: Critical for large diameters where surge forces or thermal movement can cause separation.
4.4 Electrofusion Fittings
Electrofusion adapters with built-in heater coils allow welding HDPE directly to a DI-faced adaptor.
-
Procedure:
-
Clean pipe surfaces, insert HDPE into the fitting.
-
Clamp and connect to electrofusion control unit.
-
Apply specified voltage and time per ASTM D2609.
-
Cool under clamp pressure.
-
-
Advantages:
-
Homogeneous joint, no mechanical parts.
-
Excellent for chemical or gas lines where leak-proof integrity is paramount.
-
-
Drawbacks:
-
Requires specialized equipment and trained personnel; slow cycle.
-
4.5 Socket/Barb Transitions
PVC or DI sockets machined with multi-level barbs allow radial compression joints directly into HDPE.
-
Manufacturers: Poly-Cam Series 732 uses hydraulically pressed multi-barb system.
-
Performance: Provides leak-free radial compression; limited axial restraint (use additional restraint devices).
5. Comparative Table of Connection Methods
Method | Axial Restraint | Installation Speed | Equipment Needed | Max Pressure Rating | Cost Estimate | Suitable Diameters |
---|---|---|---|---|---|---|
Flange Adapter | Full (bolted) | Moderate | Valve-handling, flange jacks | 150–250 psi | High | 4″–72″ |
Mechanical Transition | Moderate (friction) | Fast | Wrench/breaker bar | 150 psi | Medium | 2″–24″ |
Restrained Megalug® | Full (lugs) | Moderate | Wrench, torque wrench | 150–350 psi | Medium-High | 4″–60″ |
Electrofusion | N/A (homogeneous) | Slow | Electrofusion welder | 200–250 psi | High | 1″–24″ |
Socket/Barb | Low | Fast | Hydraulic press | 100 psi | Low-Medium | 1″–8″ |
6. Design Considerations and Engineering Analysis
6.1 Hydraulic & Surge Analysis
When connecting DI (rigid) to HDPE (flexible), differences in wave speed and damping can cause pressure transients that stress joints. Proper selection of restrained couplings or surge dampeners is critical.
6.2 Thermal Expansion
HDPE exhibits thermal expansion ≈ 0.2% per 10 °C; a 24″ segment can change length by 0.048″ over a 10 °C swing. Transition joints must tolerate differential movement without overstressing gaskets.
6.3 Corrosion & Cathodic Protection
Galvanic compatibility between iron and HDPE is generally good, but DI may still require cathodic protection in aggressive soils. Ensure transition fittings maintain coating continuity or use dielectric isolators if needed.
7. Installation Best Practices
-
Alignment & Support: Ensure both pipe ends are clean, cut square, and supported to avoid misalignment or deflection.
-
Lubrication: Use manufacturer-approved EPDM lubricant on gaskets and barbs.
-
Bolt Torque: Adhere to torque charts; uneven torquing can cause leaks or gasket extrusion.
-
Testing: Perform hydrostatic and leak tests per AWWA C600 standards after installation.
-
Documentation: Record joint numbers, torque values, and test pressures for QA/QC.
8. Maintenance and Troubleshooting
-
Periodic Inspection: Check for external corrosion at exposed metal parts and inspect gasket condition.
-
Leak Response: Minor leaks at couplings can often be stopped by retorquing bolts evenly.
-
Joint Replacement: Severely damaged transition couplings should be replaced; keep spare kits on site.
-
Record Keeping: Maintain an asset management log with installation dates, joint types, and any maintenance performed.
FAQs
1. What are the main advantages of using a mechanical transition coupling versus a flange adapter?
Mechanical transition couplings, such as the JCM Series 212 or Gruvlok FIG-7307, employ a ductile-iron sleeve with EPDM gaskets and bolted compression joints. They offer rapid installation—generally requiring only standard wrenches—and no specialized equipment like fusion welders. These couplings provide moderate axial restraint through gasket friction and can accommodate a limited degree of angular deflection (typically 3–5° per joint), making them ideal for tight work spaces or when slight misalignment exists. Their cost is moderate, balancing material and labor expenses favorably for small to medium diameter pipes (2″–24″). However, because gasket friction alone may not resist high thrust forces—especially during water hammer events—mechanical couplings often need supplemental restraint devices (e.g., Megalug® units) when used on larger diameters or in surge-prone systems.
Flange adapters, on the other hand, deliver full axial restraint through their bolted joint configuration and conform to ANSI B16.1 or EN 1092 bolt patterns. They are fully dismantlable, making future disassembly or repairs straightforward. The primary trade-off is cost and complexity: HDPE stub-ends must be machined or fabricated to accommodate flanges, requiring precise alignment and more labor during installation. Flange adapters are best suited for large-diameter pipelines (≥ 24″) and buried applications where high thrust loads must be safely transferred to pipe supports or concrete anchors.
Overall, mechanical couplings excel for speed and flexibility on smaller diameters, while flange adapters provide superior restraint and maintenance access for larger, high-pressure pipelines.
2. How does electrofusion compare with mechanical couplings in HDPE to DI connections?
Electrofusion fittings create a homogeneous weld between the HDPE pipe and a transition adapter, which often includes a spun or machined ductile-iron input sleeve. The fitting contains embedded electrical heating coils; when energized (typically 40 V), these coils melt the interface between fitting and pipe, forming a continuous, monolithic joint upon cooling. This process yields exceptional leak resistance and eliminates mechanical components (gaskets or bolts) that can degrade over time. Electrofusion is especially valuable in gas distribution or chemical service applications, where absolute joint integrity is paramount.
In contrast, mechanical couplings rely on gasket compression and bolted pressure to seal and restrain the joint. Installation speed is higher because no specialized electrical fusion equipment is needed—only basic tools such as torque wrenches. Mechanical couplings are also more forgiving of minor pipe surface imperfections and can be installed in cold weather without altering procedures. However, they incorporate metal components (sleeves and bolts) that may require periodic inspection and retorquing over the pipeline’s lifetime.
Electrofusion requires trained operators, certified fusion machines, and strict cleaning/preparation of pipe surfaces to avoid voids. Fusion cycle times (heating + cooling) can range from 10 to 30 minutes per joint, reducing productivity on large projects. Mechanical couplings can be installed in a few minutes each, making them preferable for high-volume installations or repairs where equipment availability is limited.
Ultimately, electrofusion delivers superior joint homogeneity and long-term reliability at higher up-front cost and lower installation speed, while mechanical couplings offer economical, rapid field assembly with proven performance when properly restrained.
3. What factors determine the selection of a transition fitting for ductile iron to HDPE?
Selecting the optimal transition fitting involves balancing hydraulic, mechanical, and economic considerations. Key factors include:
-
Pressure Class & Surge Potential
Pipelines subject to high working pressures (≥ 150 psi) or frequent transient events (water hammer) require fully restrained fittings (e.g., flange adapters or Megalug® couplings) to resist axial forces and prevent joint separation. -
Pipe Diameter & Ground Conditions
Large-diameter (> 24″) buried mains benefit from flange adapters that transfer thrust to anchors or bedding. In cohesive soils where deflection is minimal, mechanical couplings may suffice for smaller diameters. -
Installation Speed & Equipment
Emergency repair scenarios often favor mechanical couplings for their rapid deployment. Planned installations with longer lead times can accommodate electrofusion’s greater cycle time in exchange for homogeneous joints. -
Corrosion Considerations
In aggressive soils, dielectric isolators or non-metallic transitions (e.g., PVC socket-barb fittings) can prevent galvanic or stray current corrosion at the interface. -
Maintenance Access
When future disassembly is anticipated—such as valve or meter connections—flange adapters offer the best accessibility through standard bolted joints. -
Cost Constraints
Project budgets that cannot absorb high-cost fusion equipment may prefer mechanical couplings or socket/barb systems, provided axial loads are managed.
By evaluating these parameters against system requirements, engineers can specify transition fittings that optimize performance, reliability, and life-cycle cost.
4. How do you perform a pressure test on a newly installed DI–HDPE transition joint?
After completing installation of any DI–HDPE transition joint—whether mechanical coupling, flange adapter, or electrofusion—the joint must be hydrostatically tested per AWWA C600 (Installation of Ductile-Iron Water Mains) or relevant local standards. The procedure generally follows these steps:
-
System Preparation
-
Isolate the section under test using upstream and downstream shutoff valves.
-
Remove air by venting at high points to avoid pressure measurement errors.
-
-
Test Pressure Application
-
Gradually apply water pressure to 1.5× the working pressure (but not exceeding gasket or fitting rating).
-
Use a calibrated pump and gauge; record pressure at 5-minute intervals for a minimum 30-minute holding period.
-
-
Monitoring
-
Observe the joint visually for leaks (drips, weeping) at bolt flanges, coupling ends, and fusion beads.
-
Monitor pressure drop: a loss greater than 5% indicates potential leakage or system leakage elsewhere.
-
-
Documentation
-
Record start/end pressures, ambient temperature, and any retorquing performed.
-
Tag the joint with a test pass date and inspector initials.
-
-
Post-test Inspection
-
After depressurization, inspect gaskets for bulging or extrusion.
-
Tighten bolts per torque chart if minor weeping occurs, then retest localized.
-
Proper testing validates seal integrity and restraint performance, ensuring the transition will function reliably under service conditions.
5. Can a socket/barb transition fitting provide adequate axial restraint?
Socket/barb transition fittings—such as Poly-Cam Series 732—use a multi-level barb system pressed into the HDPE pipe, creating a radial-compression joint. The ductile-iron sleeve on the opposite side often features a plain or grooved end for connection to the DIP. These fittings excel at leak-free sealing without mechanical bolts, but inherently provide minimal axial restraint: the barb friction force depends on the number of barbs and the hydraulic press interference fit.
For low-pressure (<100 psi) gravity or non-surge applications, socket/barb adapters may suffice. However, in pressurized or surge scenarios, additional restraint (e.g., tie rods, Megalug® clamps) is mandatory to prevent joint pull-out under thrust loads. Engineers should calculate peak thrust forces (F = internal pressure × cross-sectional area) and compare against the barb friction capacity to determine if supplemental anchorage—concrete thrust blocks or mechanical restraints—is required.
In summary, socket/barb fittings offer speed and simplicity but cannot be considered fully restrained without supplemental measures in most pressure-pipe installations.
6. What maintenance practices extend the life of DI–HDPE transition joints?
Long-term reliability of DI–HDPE transition joints depends on proper initial installation and proactive maintenance:
-
Regular Visual Inspections
Inspect exposed fittings for signs of corrosion, gasket aging (hardening or cracking), or bolt loosening. Retorque bolts annually to compensate for gasket creep-relaxation. -
Electrical Continuity Checks
Perform holiday testing at the coupling area to detect pinholes in coatings that could lead to external corrosion. Use dielectric boots or insulating gaskets if stray currents are an issue. -
Monitoring Pressure Transients
Install pressure loggers near critical transition joints to identify abnormal spikes; address surge protection (air chambers, surge vessels) if repeated transients occur. -
Environmental Controls
Ensure that buried joints have adequate bedding and backfill compaction to prevent soil settlement and point loading on fittings. -
Spare Parts & Training
Maintain an on-site inventory of replacement gaskets, bolting hardware, and fusion fittings. Train maintenance crews in proper retorquing sequences and use of fusion equipment.
By combining routine inspection, monitoring, and maintenance staff competency, pipeline operators can minimize unplanned outages and maximize service life of mixed-material connections.
References:
- American Water Works Association (AWWA) Standards – Official Website
- ASTM F714 – Standard Specification for Polyethylene (PE) Plastic Pipe (SDR-PR) Based on Outside Diameter
- ISO 17165-1: Ductile Iron Pipes, Fittings and Accessories – General Requirements
- EN 12201 – Plastic piping systems for water supply, and for drainage and sewerage under pressure — Polyethylene (PE)
- NSF/ANSI 61 – Drinking Water System Components – Health Effects