Installing underground ductile iron pipes requires precision to ensure long-term performance in water supply, sewage, and industrial applications. As a corrosion-resistant and high-strength solution, ductile iron pipes (DIP) are widely used in municipal and infrastructure projects due to their durability (50–100+ years) and compliance with ISO 2531, EN 545, and AWWA C151 standards.
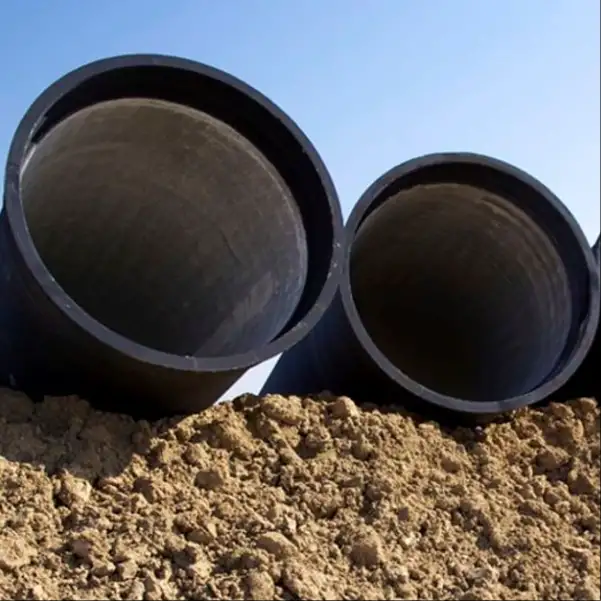
1. Trenching and Excavation
Proper trenching is the foundation of a successful DIP installation.
1.1 Trench Width and Depth
The trench must be wide enough to allow for proper pipe placement and joint assembly. According to DIPRA guidelines:
-
Trench Width: Should be at least the pipe’s outside diameter plus 16 inches.
-
Trench Depth: Must provide a minimum cover of 3 feet over the pipe to protect against surface loads.
These dimensions may vary based on soil conditions and load requirements.
1.2 Trench Bottom Preparation
The trench bottom should be smooth, free of rocks, and provide uniform support. If the native soil is unsuitable, a bedding layer of sand or gravel (minimum 4 inches) should be placed to provide a stable foundation .
2. Pipe Bedding and Backfilling
Proper bedding and backfilling are essential to maintain pipe alignment and prevent damage.
2.1 Bedding Material
Suitable bedding materials include:
-
Sand: Clean, well-graded sand provides excellent support.
-
Gravel: Rounded gravel with particle sizes between 1/4 and 1 inch.
-
Crushed Stone: Angular particles that interlock for stability.
The bedding should extend at least 4 inches below the pipe and up to the pipe’s springline .
2.2 Backfilling Procedures
Backfill in layers not exceeding 6 inches, compacting each layer to at least 90% Standard Proctor density. Avoid using large rocks or frozen materials that could damage the pipe.
3. Pipe Handling and Jointing
Proper handling and jointing ensure the integrity of the pipeline.
3.1 Handling Precautions
-
Lifting: Use slings or padded hooks; avoid chains that can damage the pipe coating.
-
Storage: Store pipes on flat surfaces with chocks to prevent rolling.
-
Inspection: Check for damage before installation; repair or replace as necessary.
3.2 Joint Types
Common joint types for underground DIP include:
-
Push-On Joints: Simplify installation; use a rubber gasket to seal.
-
Mechanical Joints: Provide flexibility and are suitable for areas requiring disassembly.
-
Flanged Joints: Used above ground; not recommended for underground installations due to rigidity.
4. Corrosion Protection
DIP is susceptible to corrosion; protective measures are necessary to extend service life.
4.1 Coatings and Linings
-
Cement-Mortar Lining: Standard for water applications; protects the interior surface.
-
Bituminous Coating: Applied to the exterior to prevent soil-side corrosion.
-
Epoxy Coatings: Used in aggressive environments for enhanced protection .
4.2 Polyethylene Encasement
Wrapping the pipe with polyethylene film provides an additional barrier against corrosive soils. The V-Bio® enhanced film includes a corrosion inhibitor and antimicrobial additive for improved performance .
5. Standards and Specifications
Adhering to established standards ensures the quality and safety of the installation.
5.1 Relevant Standards
Standard | Description |
---|---|
ANSI/AWWA C600 | Installation of Ductile Iron Water Mains and Their Appurtenances |
ANSI/AWWA C104/A21.4 | Cement-Mortar Lining for DIP |
ANSI/AWWA C105/A21.5 | Polyethylene Encasement for DIP |
ANSI/AWWA C111/A21.11 | Rubber-Gasket Joints for DIP |
Following these standards helps ensure a durable and reliable pipeline .
Frequently Asked Questions (FAQs)
Q1: What is the minimum cover required for underground ductile iron pipes?
A1: The minimum cover, or the distance from the top of the pipe to the ground surface, is typically 3 feet. This depth protects the pipe from surface loads and environmental factors. However, local regulations and specific project requirements may dictate different cover depths. It’s essential to consult with local authorities and project specifications to determine the appropriate cover for your installation.
Q2: Can ductile iron pipes be used in corrosive soil conditions?
A2: Yes, ductile iron pipes can be used in corrosive soils when proper protective measures are taken. Applying external coatings, such as bituminous or epoxy coatings, and using polyethylene encasement can significantly reduce corrosion risk. The V-Bio® enhanced polyethylene film offers additional protection with its corrosion inhibitor and antimicrobial properties. Conducting a soil analysis before installation helps determine the necessary protective measures.
Q3: How are ductile iron pipes joined underground?
A3: Underground ductile iron pipes are commonly joined using push-on or mechanical joints. Push-on joints utilize a rubber gasket to create a seal when the spigot end is inserted into the bell end. Mechanical joints involve a gasket, gland, and bolts to secure the connection. Flanged joints are generally not recommended for underground use due to their rigidity and susceptibility to stress. Proper joint assembly ensures leak-free and durable connections.
Q4: What are the consequences of improper backfilling around ductile iron pipes?
A4: Improper backfilling can lead to several issues, including pipe misalignment, deflection, or even failure. Using unsuitable materials, such as large rocks or frozen soil, can damage the pipe’s exterior. Inadequate compaction may result in voids, leading to settlement and stress on the pipe. Following recommended backfilling procedures, including using appropriate materials and compacting in layers, is crucial for the pipeline’s integrity and longevity.
Q5: Are there specific standards for the installation of ductile iron pipes?
A5: Yes, several standards govern the installation of ductile iron pipes. The ANSI/AWWA C600 standard provides guidelines for the installation of ductile iron water mains and their appurtenances. Other relevant standards include ANSI/AWWA C104/A21.4 for cement-mortar lining, ANSI/AWWA C105/A21.5 for polyethylene encasement, and ANSI/AWWA C111/A21.11 for rubber-gasket joints. Adhering to these standards ensures a safe, reliable, and long-lasting pipeline system.
For a visual demonstration of ductile iron pipe installation, you may find the following video helpful:
References:
- ISO 2531: Ductile Iron Pipes, Fittings, Accessories and Their Joints for Water Applications — Requirements and Test Methods (ISO Official)
- EN 545: Ductile Iron Pipes, Fittings, and Their Joints for Water Pipelines — Requirements and Test Methods (European Committee for Standardization)
- AWWA Standards for Ductile Iron Pipe and Fittings, including C151, C600, C104, C105, and C111 (American Water Works Association)
- DIPRA Guidelines for Ductile Iron Pipe Installation — Recommended Practices (Ductile Iron Pipe Research Association)
- Ductile Iron Pipe — Overview of Properties, Applications, and Standards (Wikipedia)