The choice between cast iron and ductile iron valve bodies is crucial for industries that require durable, reliable, and cost-effective solutions. Understanding the differences in mechanical properties, manufacturing methods, and performance characteristics will help engineers, buyers, and decision-makers select the appropriate material for specific applications. This guide provides an in-depth comparison of both materials, addressing common concerns and offering detailed insights into their respective advantages and limitations.
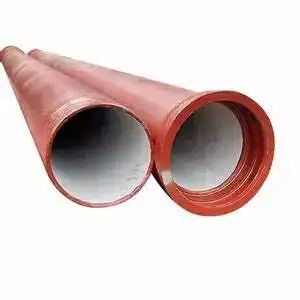
What is Cast Iron?
Cast iron, an iron-carbon alloy with a high carbon content, has been used for centuries in the manufacturing of valves, pumps, and other industrial components. The material is cast into molds in a molten state, then cooled and solidified to form a strong and rigid structure.
-
Composition: Cast iron typically contains 2-4% carbon, along with silicon, manganese, sulfur, and phosphorus.
-
Properties: Cast iron is known for its good wear resistance, high fluidity in casting, and excellent machinability. However, it is brittle and can fracture under impact.
-
Applications in Valve Bodies: Cast iron valves are commonly used in water and gas applications where high impact resistance is not a primary requirement.
-
Advantages:
-
Cost-effective for mass production
-
Good wear resistance
-
Easy to machine and shape
-
-
Limitations:
-
Brittle and susceptible to fractures
-
Less ductility and toughness compared to ductile iron
-
What is Ductile Iron?
Ductile iron, also known as nodular cast iron or spheroidal graphite iron, is a form of cast iron that has been modified by adding small amounts of magnesium. This addition results in a material that has improved ductility, making it more flexible and resistant to breaking.
-
Composition: Ductile iron contains a similar base composition to cast iron but with the addition of magnesium, which allows the graphite to form as nodules rather than flakes.
-
Properties: Ductile iron offers superior strength, toughness, and resistance to corrosion, making it a highly versatile material for valve bodies.
-
Applications in Valve Bodies: Ductile iron valves are used in a wider range of industries, including water, oil, and gas, where high strength and impact resistance are essential.
-
Advantages:
-
Excellent tensile strength and elongation
-
High fatigue and impact resistance
-
Corrosion-resistant in various environments
-
-
Limitations:
-
Higher production cost compared to cast iron
-
Requires specialized casting techniques
-
Mechanical Properties Comparison: Cast Iron vs Ductile Iron
Tensile Strength:
-
Cast iron typically has a lower tensile strength than ductile iron. Cast iron ranges from 150 to 300 MPa, while ductile iron can exceed 500 MPa. This makes ductile iron more suitable for applications that require high stress tolerance.
Yield Strength:
-
Ductile iron has a higher yield strength, often ranging from 300 to 450 MPa, compared to cast iron’s typical 150 to 250 MPa.
Impact Resistance:
-
Cast iron is brittle and prone to fracture under impact, whereas ductile iron has better resistance to impact forces, thanks to its spherical graphite structure.
Hardness and Durability:
-
Ductile iron tends to be harder and more durable than cast iron, especially in environments where wear and tear are significant.
Property | Cast Iron | Ductile Iron |
---|---|---|
Tensile Strength | 150–300 MPa | 500–700 MPa |
Yield Strength | 150–250 MPa | 300–450 MPa |
Impact Resistance | Low (brittle) | High (tough) |
Hardness | Moderate | High |
Durability | Low in harsh conditions | High in harsh conditions |
Manufacturing Process: Cast Iron vs Ductile Iron
The manufacturing processes for both cast iron and ductile iron involve casting, but the materials differ significantly in their production techniques.
Casting Techniques:
-
Cast Iron: Cast iron is typically produced through sand casting or permanent mold casting. It is easier and cheaper to cast but less adaptable to complex designs.
-
Ductile Iron: Ductile iron requires a more complex process known as “nodularizing,” where magnesium is added to the molten iron to change the structure of the graphite.
Heat Treatment:
-
Ductile iron may undergo heat treatments, such as annealing, to further enhance its mechanical properties, including improving its tensile strength and toughness.
-
Cast iron generally does not undergo such treatments as it is already brittle and does not require further strengthening.
Cost Considerations:
-
Cast iron is less expensive to produce due to its simpler manufacturing process, while ductile iron’s advanced production methods make it costlier.
Environmental Impact:
-
Both materials have environmental impacts due to energy use in casting, but ductile iron’s longer lifespan and lower failure rates often make it a more sustainable choice in the long run.
Corrosion Resistance: How Cast Iron and Ductile Iron Differ
Cast Iron:
Cast iron is prone to corrosion, especially when exposed to water and acidic environments. The graphite flakes in cast iron can act as weak points, leading to more rapid corrosion.
Ductile Iron:
Ductile iron, with its nodular graphite structure, offers superior corrosion resistance compared to cast iron. The spherical graphite form helps minimize the internal defects that can promote corrosion, making it more suitable for aggressive environments, such as underground installations.
Applications in Harsh Environments:
-
Cast Iron: Best for applications in dry or less corrosive environments.
-
Ductile Iron: Ideal for applications exposed to water, chemicals, or extreme temperatures.
Performance and Reliability in Valve Systems
Cast Iron Valve Performance:
Cast iron valves are generally reliable for lower-pressure systems. However, their brittleness and susceptibility to impact make them less suitable for high-stress or critical applications.
Ductile Iron Valve Performance:
Ductile iron valves outperform cast iron valves in high-pressure systems due to their superior strength, impact resistance, and fatigue tolerance.
Maintenance and Longevity:
Ductile iron valves tend to have a longer lifespan and lower maintenance requirements than cast iron valves, making them a better investment for demanding applications.
Cost vs Performance:
Although ductile iron valves are more expensive, their increased performance and longevity justify the higher upfront costs.
Choosing the Right Valve Material: Factors to Consider
-
Pressure and Temperature Requirements: If your system operates under high pressure or extreme temperatures, ductile iron is the better choice.
-
Environmental Conditions: Ductile iron offers superior corrosion resistance, making it ideal for outdoor or underwater applications.
-
Budget Considerations: Cast iron is a more affordable option for less demanding applications.
-
Specific Valve Applications: Consider the specific fluid and pressure conditions your valve will face when selecting the material.
Common FAQs
1. What is the main difference between cast iron and ductile iron valve bodies?
Cast iron is a more brittle material, suitable for low-pressure applications, while ductile iron is tougher and offers better performance in high-pressure, high-stress environments due to its superior strength and flexibility.
2. Why is ductile iron more expensive than cast iron?
Ductile iron requires a more advanced manufacturing process, including the addition of magnesium to alter its structure. This process is more complex and costly than the simpler casting methods used for cast iron.
3. How does the corrosion resistance of ductile iron compare to cast iron?
Ductile iron offers better corrosion resistance due to its nodular graphite structure, making it more suitable for environments exposed to water, chemicals, and high humidity. Cast iron is more prone to corrosion, especially when exposed to water.
4. Can cast iron valves be used in high-pressure systems?
Cast iron valves are generally not recommended for high-pressure systems because of their brittleness. Ductile iron valves, on the other hand, offer higher tensile and yield strength, making them more suitable for such applications.
5. What is the lifespan of a ductile iron valve compared to a cast iron valve?
Ductile iron valves typically have a longer lifespan due to their enhanced durability and resistance to impact and corrosion. Cast iron valves tend to wear out faster, especially under harsh conditions.
6. Are ductile iron valves more reliable than cast iron valves?
Yes, ductile iron valves are more reliable, especially in critical applications where strength, flexibility, and corrosion resistance are key factors. Cast iron valves may fail more easily under high stress or impact.