Welding ductile iron to steel is feasible when proper metallurgical practices are followed, particularly through the use of nickel-based filler metals that accommodate the high carbon content of ductile iron and minimize the formation of brittle phases . Critical steps include rigorous surface preparation, controlled preheat (typically 500–1200 °F or 260–650 °C), and post-weld heat treatment (commonly 400 °C for 2 h) to relieve residual stresses and prevent cracking. Common welding processes—SMAW, GMAW, and GTAW—are all suitable when paired with the right consumables (e.g., ENiFe-CI, ENi-Cl electrodes) and procedural controls, yielding sound joints with satisfactory tensile strength and toughness.
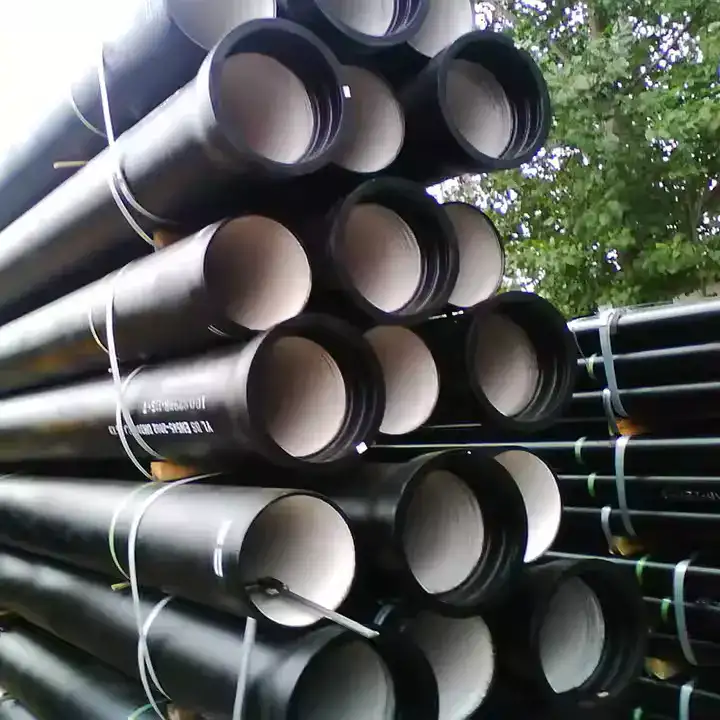
1. Introduction
Ductile iron, also known as spheroidal graphite iron, contains graphite in nodular form, granting it superior strength and toughness compared to gray iron. Steel, by contrast, has lower carbon content and a different microstructure, leading to distinct thermal expansion and solidification behaviors. Welding these two materials requires bridging their metallurgical differences to avoid hot and cold cracking.
2. Metallurgical Challenges
2.1 Carbon and Thermal Expansion
Ductile iron’s higher carbon (3.2–3.6 %) and silicon (1.8–3.0 %) contents promote carbide formation, while steel’s lower carbon (< 0.5 %) yields ferrite-pearlite microstructures. Differential thermal expansion—approximately 11–12 µε/°C for ductile iron versus 12 µε/°C for steel—can generate tensile stresses in the heat-affected zone (HAZ), risking cold cracking.
2.2 Crack Sensitivity
Rapid cooling of the weld and surrounding HAZ can form hard, brittle martensite in ductile iron, leading to microcracks. Nickel-based fillers dilute carbon and prevent martensite formation, promoting a more ductile weld zone.
3. Welding Methods and Filler Metals
Several arc-welding processes are effective for joining ductile iron to steel when using appropriate consumables:
Process | Filler Metal | Advantages | Typical Application |
---|---|---|---|
SMAW | ENiFe-CI (FM Ni-55), ENi-Cl | All-position, good ductility | Field repairs |
GMAW | Nickel-based wires (600, 601) | High deposition rate | Production welding |
GTAW | Solid nickel rods (Alloy 800/800HT) | Precise control, low dilution | Thin sections, precision |
Note: ENiFe-CI electrodes are widely recommended for their ability to accommodate impurity levels and prevent carbide precipitation. ENi-Cl offers good crack resistance but lower tensile strength, making it suitable for non-critical repairs.
4. Preheat and Interpass Temperature Control
-
Preheat Temperature:
-
Typical: 500–1200 °F (260–650 °C) for ductile iron to slow cooling and minimize thermal gradients.
-
For mixed ductile iron–steel joints, 500–650 °F (260–345 °C) is often sufficient to prevent cracking in both materials.
-
-
Interpass Temperature:
-
Maintain above 300 °F (150 °C) between passes to avoid abrupt cooling, which can lead to hydrogen-induced cracking.
-
5. Post-Weld Heat Treatment (PWHT)
Post-weld heating further relieves residual stresses and tempers the HAZ:
-
Recommended Regime: 400 °C (752 °F) for 2 hours, with two heating passes, balances stress relief with productivity.
-
Effects: Reduces hardness, improves ductility, and mitigates cold cracking risks.
-
Standards Reference: PWHT requirements per AWS D10.11 and relevant ASTM guidelines.
6. Welding Procedure
-
Surface Preparation:
-
Remove all rust, scale, paint, and contaminants to ensure fusion. Clean with wire brushing, grinding, or chemical cleaning.
-
-
Tack Welding & Peening:
-
Use small tack welds to align components; peen each weld pass lightly to relieve stresses and prevent crack initiation.
-
-
Controlled Heat Input:
-
Low heat input procedures (e.g., short arc length in GMAW) minimize HAZ width and reduce stress concentration.
-
-
Sequential Passes:
-
Alternate welding sides to balance distortions; allow interpass temperature to remain above minimum threshold.
-
7. Applications and Limitations
-
Ideal Applications: Repair of ductile iron pump casings, valve bodies, or flanged couplings where mechanical fastening is impractical.
-
Limitations: Critical structural components may be better replaced or joined mechanically, as weld zones rarely match base-metal strength in high-grade (120 ksi) ductile iron.
8. FAQ
Q1: Can you weld ductile iron directly to steel without filler?
A: No; filler metal (nickel-based) is essential to buffer carbon migration and prevent brittle martensite.
Q2: What preheat temperature is required?
A: Typically 500–650 °F (260–345 °C) for ductile iron–steel joints to control cooling rate.
Q3: Which filler metal offers the best crack resistance?
A: ENiFe-CI (FM Ni-55) provides superior resistance to carbide formation and cracking.
Q4: Is post-weld heat treatment mandatory?
A: Highly recommended; 400 °C for 2 h reduces residual stress and hardness in the HAZ.
Q5: Are there safety concerns?
A: Yes—adequate ventilation, proper personal protective equipment (PPE), and hydrogen-control measures are critical to minimize fume exposure and cracking risks.