In modern water and sewer systems, connecting ductile iron fittings to PVC pipe is not only possible but common practice—offering strength, durability, and cost-effective installation. Specially designed push-on and mechanical joint ductile iron fittings accommodate the outside diameter (OD) of IPS-sized PVC pipe (e.g., C900) through transition gaskets or bell adapters, maintaining a leak-tight joint under pressures up to 16 bar. Installation procedures follow standard MJ (mechanical joint) or push-on methods, with beveled spigots, gland followers, and EPDM gaskets ensuring proper seal and flexibility. Compatibility is governed by standards such as AWWA C111/A21.11 and EN 12842, which define dimensional and performance requirements for ductile iron fittings used on PVC and other plastic pipes.
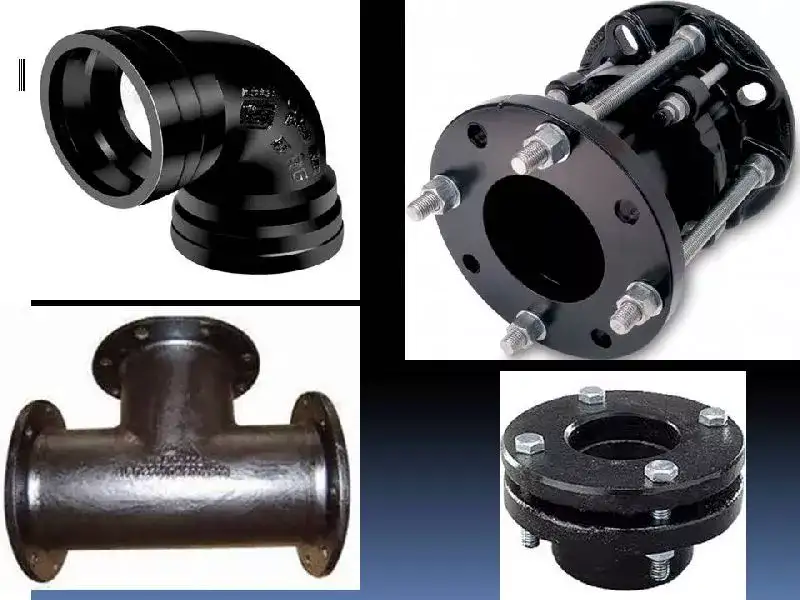
I. Introduction & Overview
Ductile iron fittings—manufactured to ASTM A536 Grade 65-45-12—offer superior mechanical strength compared to PVC fittings alone, making them ideal for high-stress underground water mains and industrial pipelines. PVC pipe (Schedule 40/80, C900) is lightweight, corrosion-resistant, and easy to handle, but its limited stiffness can be reinforced by ductile iron fittings at critical joints or branch connections. Transitioning between materials leverages the dimensional compatibility of IPS (Iron Pipe Size) PVC, whose OD matches that of ductile iron pipe, facilitating direct coupling without OD mismatch.
II. Compatibility & Standards
-
AWWA C111/A21.11: Defines push-on joints for ductile iron fittings, with gasket compression requirements that apply equally when connected to IPS PVC pipe.
-
EN 12842: Specifies ductile iron fittings for PVC-U or PE piping systems, including gasket and flange adapter dimensions.
-
ISO 2531: Governs ductile iron pipe dimensions, ensuring IPS PVC pipe ODs align with DI fitting bell sockets.
-
Harco PF147: Harco’s ductile iron push-on fittings are certified for use on IPS-sized PVC pipe and steel pipe in water mains and irrigation systems.
III. Types of Ductile Iron Fittings for PVC Pipe
Fitting Type | Description | Sizes (IPS) | Gasket Material | Standard |
---|---|---|---|---|
Push-On (SEB) | Deep-bell socket with transition gasket for IPS PVC; simple, quick installation using pipe bevel and push-in action | 2″–12″ | EPDM, SBR | AWWA C111/A21.11 |
Mechanical Joint | Gland follower, MJ gasket, and gland bolts clamp onto pipe OD; accommodates minor misalignment and axial movement | 3″–48″ | EPDM | AWWA C111/A21.11 |
Flange Adapter | An adapter ring bolts to ductile iron flange; rubber sleeve seals to PVC spigot; allows flange-to-flange connections | 4″–24″ | EPDM | EN 12842 |
Bell Adapter | Threaded or push-on bell that converts PVC plain end to a DI bell end for push-on coupling | 2″–12″ | EPDM, NBR | Manufacturer specific |
Restrained Fitting | MJ style with shear ring or retainer to resist axial thrust; used where thrust blocks are impractical | 4″–24″ | EPDM | AWWA C111/A21.11 |
Table 1. Comparison of ductile iron fitting types for PVC pipe.
IV. Connection Methods & Installation
-
Pipe Preparation:
-
Cut & Chamfer: PVC spigot cut square; chamfered per DI bevel guidelines to prevent gasket damage.
-
Beveling: When joining to DI bells or flange adapters, PVC is beveled shorter than DI spigots to seat fully against gasket.
-
-
Push-On Assembly (SEB):
-
Lubricate gasket; align pipe and push until seated against gasket ledge.
-
Confirm push-in depth via marking or dimension checks.
-
-
MJ Assembly:
-
Slide gland follower and gasket over pipe; insert spigot into fitting bell.
-
Hand-tighten gland nuts in a cross pattern; torque to manufacturer’s spec (e.g., 70 ft-lb for 4″).
-
-
Flange Adapter:
-
Bolt adapter to DI flange; insert PVC spigot through rubber sleeve; torque flange bolts per ANSI B16.1 patterns.
-
-
Restrained Fittings:
-
Follow MJ steps, then insert shear ring segments and retighten gland to rated torque for restraint.
-
V. Mechanical & Electrochemical Considerations
-
Differential Stiffness: DI fittings have higher stiffness (E ≈ 170 GPa) than PVC (E ≈ 3 GPa), necessitating joint flexibility to accommodate thermal and pressure-induced movement.
-
Corrosion Protection: External epoxy or fusion-bonded epoxy coatings on DI fittings prevent soil corrosion; internal DI surfaces often cement mortar lined, unaffected by PVC connection.
-
Galvanic Effects: Minimal risk, as PVC is non-conductive; ensure DI fittings use compatible metal hardware (stainless or zinc-plated bolts) to avoid dissimilar-metal corrosion.
VI. Performance & Applications
Ductile iron fittings on PVC pipe are widely used in:
-
Municipal Water Distribution: C900 PVC with DI fittings handles pressures up to 350 psi (24 bar) in long-run mains.
-
Irrigation Systems: Harco SEB fittings on IPS PVC in golf courses and turf irrigation offer quick maintenance and pipe movement allowance.
-
Sewer Force Mains: MJ restrained couplings connect PVC force mains to DI pump flanges and valve stacks, resisting thrust without concrete blocks.
VII. Selection Guide & Best Practices
-
Match OD: Verify PVC pipe OD with IPS tables; confirm DI fitting bell or MJ gasket sizing.
-
Pressure Rating: Select fitting rated ≥ 1.25 × system pressure; consider restrained style if thrust blocking is impractical.
-
Gasket Material: Use EPDM for potable water, NBR for oily or chemical environments.
-
Torque Control: Follow manufacturer’s torque sequence and retorque after 24 h of service to compensate for gasket creep.
-
Alignment: Maintain straight-in pipe entry; avoid side loading on flexible couplings.
-
Documentation: Retain installation records, including torque values, part numbers, and inspections, for warranty and maintenance tracking.
VIII. Maintenance & Troubleshooting
-
Leak Checks: Visual inspection at 24 h, then annually; look for seepage or wet spots around gasket clamp.
-
Gasket Replacement: EPDM gaskets have 20-year life; replace if hardened or cracked.
-
Corrosion Inspection: Check external DI coating; touch-up any damage with compatible epoxy.
-
Torque Verification: Re-torque gland nuts to spec if joint movement or subsidence occurs.
Issue | Possible Cause | Remedy |
---|---|---|
Leak at Joint | Under-torque, gasket misalignment | Retorque; reposition gasket; inspect bevel |
Coupling Slip | Insufficient restraint, axial thrust overload | Switch to restrained MJ coupling; add thrust block |
Corrosion | Damaged coating | Clean, coat, inspect regularly |
Difficult Assembly | Dirt in gasket groove, incorrect bevel | Clean bell/gasket; re-chamfer spigot |
Table 2. Common issues and corrective actions.
IX. Cost Analysis & Lifecycle Considerations
While PVC pipe is cost-effective, the addition of ductile iron fittings increases joint cost by 20–40% compared to all-PVC systems. However, DI fittings deliver lower maintenance and longer service life in high-stress zones, offering life-cycle cost savings over 30 years. Budget allocation should factor in installation labor savings versus savings from reduced repair downtime.
YouTube Installation Tutorial
*Step-by-step guide on installing mechanical joint ductile iron fittings on PVC pipe.*
Six Common Questions
1. What are the key dimensional checks when using ductile iron fittings on PVC pipe?
Before assembly, verify that the PVC pipe’s OD matches the IPS standard (e.g., 4″ = 4.5″ OD). Use calipers to measure spigot OD, and compare to the DI fitting’s gasket size chart. Check bell depth with a depth gauge to ensure proper gasket engagement. Finally, confirm chamfer angle (typically 22.5°) aligns with manufacturer bevel specs. These checks prevent leaks and ensure full mechanical performance under pressure.
2. Can non-IPS PVC pipe (e.g., metric PVC-U) be used with ductile iron fittings?
Non-IPS PVC-U pipe (metric OD) requires transition couplings with adjustable gaskets or reducers. EN 12842 compliant DI fittings offer stepped bores or insert rings to accommodate DN 80–DN 600 PVC-U sizes. Always confirm compatibility via manufacturer data; do not improvise with standard IPS fittings, as OD mismatches can cause gasket blow-out.
3. How does temperature variation affect DI-PVC joints?
PVC contracts/expands at ~ 0.06 mm/°C per meter, while DI’s thermal expansion is ~ 0.12 mm/°C per meter. At a 30 °C swing over 50 m, PVC moves ~ 90 mm; DI moves ~ 180 mm. Joint flexibility from MJ couplings accommodates this differential without stressing the gasket. For long runs, include expansion loops or flexible coupling sections every 100 m to mitigate thermal loads.
4. Are ductile iron fittings compatible with all PVC pressure classes (e.g., C900, C905)?
Ductile iron fittings are compatible with C900 (DR 14), C905 (DR 11) PVC pipe, and SDR PR ratings, as long as IPS OD is consistent. Pressure class differences do not affect OD; ensure joint gasket and fitting pressure rating meet or exceed pipe class (e.g., C905 @ 250 psi).
5. What maintenance is required for DI-PVC transition joints?
Inspect joints visually every 12 months and after seismic or ground-settlement events. Clean exterior, check for corrosion coating damage, and retorque glands to original spec. Replace EPDM gaskets every 15–20 years based on UV and chemical exposure. Maintain records of torque values and part numbers for efficient future service.
6. Can MJ ductile iron fittings on PVC pipe be reused if disassembled?
Yes—provided gaskets are undamaged and the bell and spigot faces are clean and free of nicks. Retorque the gland nuts lightly to reestablish gasket seat. For push-on SEB fittings, inspect gasket for deformation; replace if out of round > 2 mm. Avoid reusing couplings that have been in high-load or emergency service without inspection.
References:
- AWWA C111/A21.11 Standard for Ductile-Iron and Gray-Iron Fittings – American Water Works Association official standards for mechanical joint and push-on joints for ductile iron fittings.
- EN 12842: Ductile Iron Fittings for PVC and PE Pipes – European Committee for Standardization specification on ductile iron fittings used with PVC and polyethylene pipes.
- Ductile Iron Pipe (Wikipedia) – Overview of ductile iron pipe standards, mechanical properties, and typical applications including compatibility with plastic pipes.
- ISO 2531: Ductile Iron Pipes, Fittings, Accessories, and Their Joints for Water or Gas Applications – International Organization for Standardization specifications for dimensions and joints of ductile iron pipes.
- U.S. EPA Drinking Water Standards and Regulations – Regulatory framework and material compatibility considerations for potable water systems including ductile iron and PVC pipe usage.