Ductile iron pipes are renowned for their strength, durability, and resistance to corrosion, making them a preferred choice in water distribution and industrial applications. While these pipes are commonly joined using methods like push-on joints, flanged connections, or mechanical joints, threading ductile iron pipes is also a viable option under certain conditions. This article delves into the process of threading ductile iron pipes, examining its feasibility, advantages, challenges, and best practices.
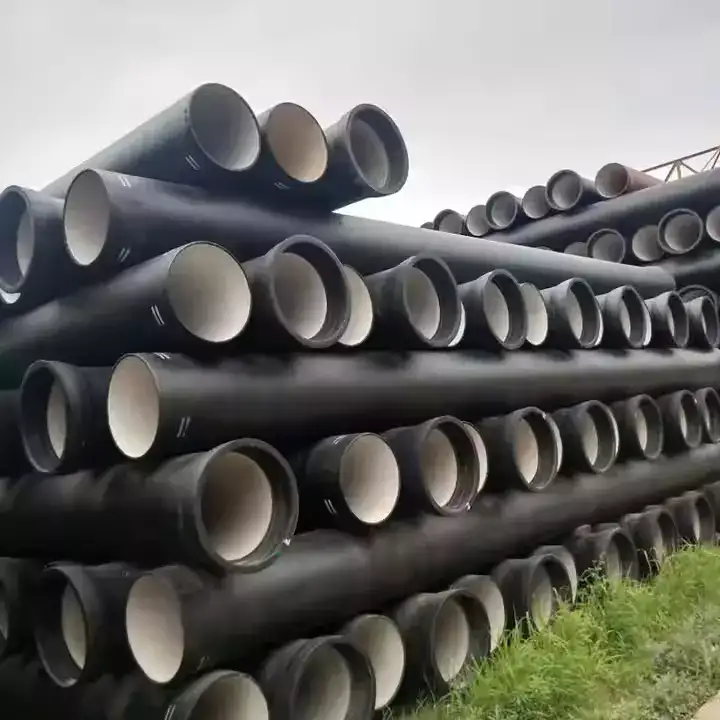
🔍 Understanding Ductile Iron Pipes
Ductile iron pipes are cast from ductile iron, a material that exhibits increased strength and flexibility compared to traditional cast iron. This enhancement is achieved by adding small amounts of magnesium to the iron, which alters the graphite structure from flakes to spheroids, improving its mechanical properties. These pipes are commonly used in applications requiring high strength and corrosion resistance, such as water and wastewater systems.
🧵 Threading Ductile Iron Pipe: Feasibility and Considerations
Threading ductile iron pipes is technically feasible, but several factors must be considered to ensure a successful and durable connection:
1. Pipe Wall Thickness
The wall thickness of the ductile iron pipe plays a crucial role in the threading process. Thicker walls provide more material for the threads, resulting in stronger connections. However, excessively thick walls may require specialized equipment and increased effort to achieve precise threading.
2. Pipe Diameter
The diameter of the pipe influences the threading process. Larger diameter pipes may require more powerful threading machines and specialized dies to accommodate the increased size. Additionally, larger pipes may necessitate more torque during threading, which can impact the quality of the threads if not properly managed.
3. Thread Type and Standards
The type of thread used is essential for ensuring compatibility with fittings and other components. Common thread types for ductile iron pipes include National Pipe Thread (NPT) and British Standard Pipe (BSP). Adhering to established standards ensures leak-tight connections and compatibility with other piping systems.
4. Threading Equipment
Utilizing appropriate threading equipment is vital for achieving high-quality threads. Manual pipe threaders are suitable for smaller diameter pipes, while power-driven machines are necessary for larger sizes. The choice of equipment should align with the pipe’s specifications and the required thread quality.
🛠️ Threading Process for Ductile Iron Pipes
The process of threading ductile iron pipes involves several key steps:
-
Preparation: Clean the pipe ends to remove any debris, corrosion, or coatings that could interfere with threading.
-
Measuring and Marking: Measure and mark the pipe to ensure accurate and consistent thread lengths.
-
Lubrication: Apply a suitable cutting oil or lubricant to reduce friction and heat during the threading process.
-
Thread Cutting: Using the appropriate threading machine and die, cut the threads onto the pipe ends.
-
Inspection: Inspect the threads for uniformity, depth, and cleanliness to ensure they meet the required standards.
-
Cleaning and Protection: Clean the threaded areas to remove any residual cutting oil and apply protective coatings if necessary to prevent corrosion.
⚠️ Challenges in Threading Ductile Iron Pipes
While threading ductile iron pipes is feasible, several challenges may arise:
-
Brittleness: Ductile iron’s brittleness can lead to cracking if excessive force is applied during threading.
-
Thread Integrity: Ensuring the threads are clean, uniform, and free from defects is crucial for a secure connection.
-
Equipment Compatibility: Not all threading machines and dies are suitable for ductile iron; using incompatible equipment can result in poor-quality threads.
-
Corrosion Resistance: Threaded areas may be more susceptible to corrosion if not properly protected, compromising the system’s integrity.
✅ Best Practices for Threading Ductile Iron Pipes
To achieve optimal results when threading ductile iron pipes, consider the following best practices:
-
Use Appropriate Equipment: Select threading machines and dies designed for ductile iron to ensure compatibility and quality.
-
Apply Adequate Lubrication: Use high-quality cutting oils to reduce friction and heat, prolonging tool life and improving thread quality.
-
Ensure Proper Alignment: Align the pipe and threading equipment accurately to prevent misaligned threads and potential leaks.
-
Inspect Threads Thoroughly: Regularly inspect the threads for defects and uniformity to maintain connection integrity.
-
Protect Threaded Areas: Apply protective coatings or wraps to threaded areas to prevent corrosion and extend the lifespan of the connection.
📊 Comparison: Threaded vs. Flanged Connections for Ductile Iron Pipes
Feature | Threaded Connections | Flanged Connections |
---|---|---|
Installation | Requires precise threading; moderate time | Requires bolting; longer installation |
Disassembly | Easier for smaller pipes | Easier for larger pipes |
Pressure Rating | Suitable for low to medium pressure | Suitable for high-pressure systems |
Cost | Generally lower | Generally higher |
Corrosion Resistance | Depends on protective measures | Depends on flange material and gasket |
📹 Related Video
For a visual demonstration of threading ductile iron pipes, watch the following video:
❓ Frequently Asked Questions (FAQs)
1. Can ductile iron pipes be threaded?
Yes, ductile iron pipes can be threaded. However, the process requires careful consideration of factors such as pipe wall thickness, diameter, and the use of appropriate threading equipment to ensure a secure and durable connection.
2. What are the advantages of threading ductile iron pipes?
Threading provides a reliable and leak-tight connection, especially suitable for smaller diameter pipes or applications requiring frequent disassembly. It also offers flexibility in connecting various fittings and components.
3. What challenges might arise when threading ductile iron pipes?
Challenges include the material’s brittleness, which can lead to cracking if excessive force is applied, and ensuring the threads are clean and uniform to maintain connection integrity.
4. How can I ensure the quality of threads on ductile iron pipes?
Use appropriate threading equipment designed for ductile iron, apply adequate lubrication during the threading process, and thoroughly inspect the threads for defects and uniformity.
5. Are there alternatives to threading for joining ductile iron pipes?
Yes, alternatives include flanged connections, push-on joints, and mechanical joints. The choice depends on factors such as pipe size, pressure requirements, and the need for disassembly.
6. How can I protect threaded areas on ductile iron pipes from corrosion?
Apply protective coatings or wraps to threaded areas to prevent corrosion. Regular inspection and maintenance are also essential to ensure the longevity of the connections.