Ductile iron pipes are generally not welded due to the material’s properties and the challenges associated with welding cast iron. While ductile iron is more flexible than traditional cast iron, it still presents difficulties in welding, such as the risk of cracking and the need for special procedures. Typically, ductile iron pipes are joined using mechanical methods like flanged connections, push-on joints, or restrained joints. In some cases, if welding is necessary, specialized techniques such as preheating the pipe and using specific welding rods designed for cast iron are required. However, welding is not the most common or recommended method for connecting ductile iron pipes.
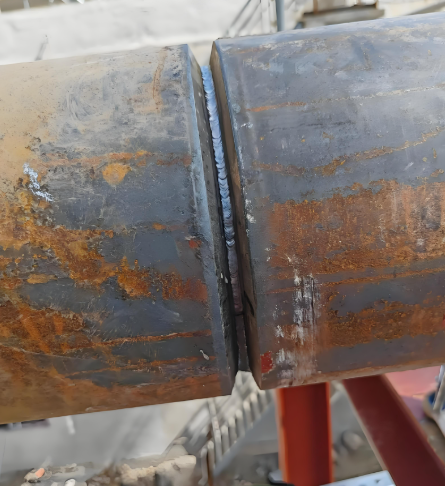
Why Welding Ductile Iron Pipes Is Possible (But Tricky)
Unlike brittle cast iron, ductile iron contains nodular graphite, which improves its ductility and weldability. However, its high carbon content (3–4%) and unique microstructure pose challenges:
-
Heat sensitivity: Rapid cooling can create hard, crack-prone zones.
-
Carbon migration: Excessive heat may weaken the joint.
-
Pre/post-heat requirements: Temperature control is critical.
Step-by-Step Guide to Welding Ductile Iron Pipes
1. Pre-Weld Preparation
-
Clean the surface with a grinder to remove rust, coatings, or debris.
-
Preheat the pipe to 500–1200°F (260–650°C) using a torch or furnace to minimize thermal stress.
2. Choosing the Right Welding Method
-
Shielded Metal Arc Welding (SMAW): Use nickel-based electrodes (e.g., ENi-CI) for better compatibility.
-
Gas Metal Arc Welding (GMAW): Requires 90% argon + 10% CO₂ gas and nickel-alloy filler wires.
-
Oxy-Acetylene Welding: Suitable for small repairs but demands skilled handling.
3. Welding Execution
-
Maintain short, intermittent welds to control heat input.
-
Peen (hammer) each weld layer to relieve stress.
-
Keep interpass temperatures below 400°F (204°C).
4. Post-Weld Treatment
-
Cool the pipe slowly in an insulating blanket or furnace.
-
Grind the weld to ensure a smooth finish.
Ductile Iron vs. Cast Iron: Welding Differences
Factor | Ductile Iron | Cast Iron |
---|---|---|
Weldability | Moderate (requires preheat) | Poor (prone to cracking) |
Filler Material | Nickel-based electrodes | Nickel or specialty alloys |
Common Applications | Pipe repairs, joints | Rarely welded; often replaced |
Common Mistakes to Avoid
-
Skipping Preheating: Leads to thermal shock and cracks.
-
Using Standard Electrodes: Carbon steel rods cause brittle joints.
-
Rapid Cooling: Creates hard zones; always cool gradually.
FAQs About Welding Ductile Iron Pipes
Q: Can I weld ductile iron to steel?
A: Yes, but use a nickel-based buffer layer to prevent carbon migration.
Q: How strong is a welded ductile iron joint?
A: Properly welded joints retain 80–90% of the pipe’s original strength.
Q: Is brazing a better alternative?
A: Brazing works for low-pressure systems but lacks the strength of fusion welding.
Key Takeaways
-
Ductile iron pipes can be welded with proper techniques and materials.
-
Preheat, nickel electrodes, and slow cooling are essential for success.
-
For critical applications, consult ASTM A674 or AWS D11.2 standards.
By following these guidelines, professionals and DIYers can achieve durable welds on ductile iron pipes, extending their service life while avoiding costly replacements.
References:
- Ductile Iron – Wikipedia
- ASTM A674 – Standard Practice for Fusion Welding of Ductile Iron Pipe and Fittings – ASTM International
- AWS D11.2 – Welding of Cast Iron – American Welding Society
- Welding Ductile Iron: Methods and Challenges – Weldero Industry Guide
- Welding, Cutting, and Brazing Safety – Occupational Safety and Health Administration (OSHA)