Ductile iron fittings are essential components in waterworks systems and pipelines, providing reliable connections and ensuring the structural integrity of the entire network. The AWWA C110 standard, set by the American Water Works Association (AWWA), defines the specifications and performance characteristics for ductile iron fittings used in water distribution systems. These fittings are known for their strength, durability, and ability to withstand high-pressure conditions.
In this guide, we will explore the AWWA C110 standard in detail, covering the specifications, benefits, and applications of ductile iron fittings, as well as common installation practices and maintenance considerations.
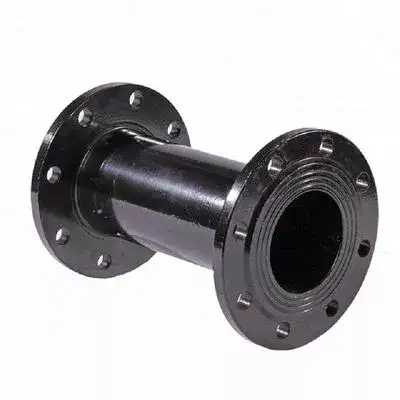
1. What is the AWWA C110 Standard?
The AWWA C110 standard specifies the design, material requirements, dimensions, and testing procedures for ductile iron fittings used in water distribution systems. These fittings are primarily used to connect pipes, valves, and other components in waterworks applications. The standard ensures that the fittings meet rigorous performance criteria to handle the stresses imposed by water pressure and environmental factors.
Key Components of AWWA C110:
-
Material Specifications: Ductile iron fittings must be made from high-quality ductile iron, which is known for its excellent strength-to-weight ratio and resistance to corrosion.
-
Pressure Ratings: The fittings must meet certain pressure ratings, ensuring they can handle typical water distribution system pressures.
-
Dimensional Standards: The AWWA C110 standard defines the exact dimensions and tolerances for each type of fitting, ensuring compatibility with other system components.
Specification | Detail |
---|---|
Material | Ductile iron |
Pressure Rating | 250 psi minimum (depending on size and application) |
Design | Full body, bell-and-spigot, or mechanical joint designs |
Testing Requirements | Hydrostatic, pressure testing, and visual inspection |
2. Types of AWWA C110 Ductile Iron Fittings
Ductile iron fittings come in a variety of shapes and sizes, each suited for specific applications in water distribution systems. Some common types of fittings included in the AWWA C110 standard are:
-
Elbows: Used to change the direction of pipes in a pipeline system.
-
Tees: Used to create branches in a pipeline, connecting a main pipeline to a secondary pipeline.
-
Reducers: Used to connect pipes of different diameters.
-
Couplings: Used to join two pipes of the same diameter or connect different types of pipe joints.
-
Caps: Used to close the end of a pipeline.
-
Flanges: Used for joining pipes with bolts or other mechanical fasteners.
Fitting Types and Their Applications:
Fitting Type | Application |
---|---|
Elbow | Changes the direction of the pipeline |
Tee | Provides branching in a pipeline |
Reducer | Connects pipes of different diameters |
Coupling | Joins two pipes together or connects pipe joints |
Cap | Closes the end of a pipeline |
Flange | Joins pipe ends with bolts or mechanical fasteners |
3. Advantages of AWWA C110 Ductile Iron Fittings
The use of ductile iron fittings, specifically those adhering to the AWWA C110 standard, provides numerous advantages over other types of materials, such as cast iron or plastic fittings.
Key Advantages:
-
Strength and Durability: Ductile iron fittings are designed to withstand high pressure and stress, making them ideal for water distribution systems.
-
Corrosion Resistance: Ductile iron has excellent resistance to corrosion, particularly when coated with protective layers like cement mortar lining or epoxy coatings.
-
Shock Absorption: Ductile iron’s flexibility allows it to absorb shock loads, making it suitable for areas prone to seismic activity or fluctuating pressures.
-
Long Service Life: These fittings offer a longer service life than many other types of fittings, reducing maintenance costs and downtime.
4. Material Properties of Ductile Iron in AWWA C110 Fittings
Ductile iron is a key material used in AWWA C110 fittings, and its unique properties contribute to the high performance of the fittings.
Material Characteristics:
-
Tensile Strength: Ductile iron has a higher tensile strength compared to traditional cast iron, typically in the range of 60,000 to 100,000 psi.
-
Ductility: Ductile iron’s ability to bend without breaking makes it highly resistant to fractures under stress.
-
Workability: Ductile iron is easier to cast and machine compared to other materials, which helps reduce production costs.
-
Fatigue Resistance: Ductile iron fittings perform well under cyclic loading, making them suitable for areas with fluctuating water pressures.
5. Common Applications of AWWA C110 Ductile Iron Fittings
AWWA C110 ductile iron fittings are commonly used in various infrastructure projects where water, sewage, and industrial piping systems are involved. The versatility of these fittings makes them suitable for a wide range of applications:
-
Water Distribution Systems: These fittings are essential in municipal water supply networks for connecting pipes, valves, and other components.
-
Wastewater Treatment Plants: Ductile iron fittings are used to connect various parts of the wastewater treatment systems.
-
Industrial Applications: Some industries use ductile iron fittings in their piping systems for transporting liquids, chemicals, or gases.
-
Fire Protection Systems: The strength and durability of these fittings make them ideal for use in fire hydrants and sprinkler systems.
Popular Applications:
Application | Usage |
---|---|
Water Distribution | Connecting pipes, valves, and hydrants |
Wastewater Treatment | Connecting treatment plant components |
Industrial Piping | Transporting chemicals, liquids, gases |
Fire Protection | Hydrant systems, sprinkler connections |
6. Installation of AWWA C110 Ductile Iron Fittings
Proper installation of AWWA C110 ductile iron fittings is critical to ensuring the longevity and performance of the entire piping system. Installation guidelines typically include the following steps:
-
Preparation: Ensure that the pipes and fittings are clean and free of debris.
-
Alignment: Properly align the fittings with the adjacent pipes to avoid stresses on the joints.
-
Jointing: For mechanical joints, ensure the gaskets are properly lubricated and placed, while flanged joints must be tightened evenly.
-
Inspection: After installation, perform a hydrostatic test to ensure there are no leaks or weaknesses.
7. Testing and Quality Control for AWWA C110 Fittings
Quality control and testing are critical steps in the production of AWWA C110 ductile iron fittings. The fittings must undergo several tests to ensure they meet the stringent requirements set by the AWWA standard.
Common Tests:
-
Hydrostatic Testing: Fittings are subjected to internal pressure to ensure they can withstand the expected operating pressures.
-
Dimensional Inspection: A comprehensive inspection ensures that the fittings conform to the dimensional standards outlined in the AWWA C110 specification.
-
Visual Inspection: This test identifies any surface defects, such as cracks, pinholes, or other imperfections.
-
Impact Testing: This test measures the ability of the fittings to withstand impact forces.
8. Common Challenges and Solutions in AWWA C110 Fittings
Like all engineering materials, ductile iron fittings face certain challenges. Addressing these challenges ensures that the fittings perform optimally in the field.
Challenges:
-
Corrosion: Although ductile iron has excellent corrosion resistance, certain environments (e.g., aggressive soils or acidic water) can cause corrosion.
-
Installation Errors: Improper alignment and jointing can lead to leaks or failures.
-
Cost Considerations: Ductile iron fittings are generally more expensive than plastic alternatives, though they offer greater durability and strength.
Solutions:
-
Corrosion Protection: Coatings like cement mortar lining, epoxy, or bituminous coatings can be applied to improve resistance.
-
Training and Proper Installation: Proper installation practices and training for contractors can mitigate alignment and jointing errors.
-
Cost-Benefit Analysis: While ductile iron fittings are more expensive, their longer lifespan often results in lower maintenance and replacement costs.
9. Common Questions About AWWA C110 Ductile Iron Fittings
Q1: What is the maximum pressure rating for AWWA C110 ductile iron fittings?
AWWA C110 ductile iron fittings generally have a minimum pressure rating of 250 psi, but this can vary depending on the size and design of the fitting. Larger fittings may have a higher pressure rating.
Q2: How does ductile iron compare to cast iron for water distribution fittings?
Ductile iron is more flexible and stronger than cast iron, providing better resistance to cracking under stress. Cast iron, while still durable, is more brittle and prone to fracture under certain conditions.
Q3: Are AWWA C110 ductile iron fittings suitable for high-temperature applications?
Ductile iron fittings can handle moderately high temperatures, but for extremely high-temperature environments, materials like stainless steel may be more appropriate.
Q4: How do I maintain AWWA C110 ductile iron fittings?
Regular inspection for corrosion, checking for leaks, and ensuring proper alignment during installation are key aspects of maintaining these fittings. Also, applying protective coatings can extend their service life.
Q5: Can AWWA C110 fittings be used in underground pipelines?
Yes, AWWA C110 ductile iron fittings are commonly used in underground pipelines due to their strength and resistance to corrosion, especially when coated with protective materials.
Q6: What environmental factors affect the lifespan of AWWA C110 ductile iron fittings?
Soil conditions, water chemistry, and exposure to chemicals can affect the lifespan of ductile iron fittings. Coatings and proper installation can mitigate these effects.
Conclusion
AWWA C110 ductile iron fittings are a crucial component in modern water distribution systems. With their superior strength, durability, and resistance to corrosion, they offer a long-lasting solution for connecting pipes in various applications. By understanding the specifications, advantages, and proper installation techniques, engineers and contractors can ensure the optimal performance of their systems for years to come.