Austempered ductile iron (ADI) is a high-performance material that undergoes a specialized heat treatment known as the austempering process. This heat treatment process significantly enhances the mechanical properties of ductile iron, making it suitable for demanding applications that require high strength, wear resistance, and fatigue resistance. In this article, we will explore the details of ADI heat treatment, including its process, benefits, effects on material properties, and applications.
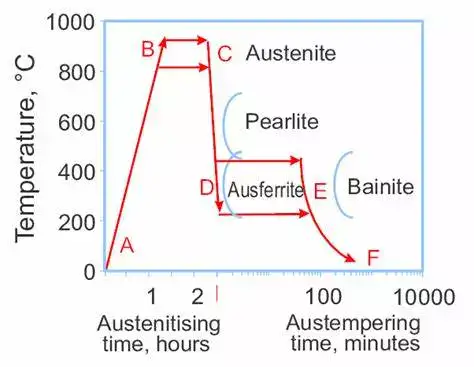
1. What is the Austempering Heat Treatment Process?
The austempering process is a heat treatment technique used to enhance the properties of ductile iron by transforming its microstructure. Unlike traditional heat treatment methods such as quenching and tempering, austempering produces a unique microstructure known as ausferrite—a combination of ferrite and martensite. This structure imparts high strength, toughness, and wear resistance to the material.
Key Steps in the Austempering Process:
-
Heating: Ductile iron is heated to an austenitizing temperature, typically around 800-900°C (1470-1650°F). At this temperature, the microstructure of the iron becomes fully austenitic, which is the first phase of the process.
-
Austenitizing: The iron is held at this temperature for a set period to allow the complete transformation to austenite.
-
Quenching: The material is then rapidly cooled, but unlike traditional quenching, it is done in a bath of molten salt or polymer, rather than water. This cooling process is slower than standard quenching, which helps to form the ausferrite microstructure.
-
Austenite Transformation: The result is a microstructure that consists of fine, evenly distributed ausferrite, which offers a balance of strength and toughness.
2. Importance of Temperature and Time Control in Austempering
The temperature and time parameters are critical factors in determining the final properties of austempered ductile iron. The following factors need to be carefully controlled:
-
Temperature Control: The temperature at which the material is held during the austenitizing phase significantly impacts the resulting microstructure. A higher temperature may lead to more austenite formation, while a lower temperature may result in a less refined structure.
-
Time Control: The length of time the material is held at austenitizing temperature affects the degree of transformation to austenite. Extended holding times can allow for a more complete transformation, but excessive times may cause unwanted grain growth, reducing strength.
Parameter | Effect on Material Properties |
---|---|
Temperature | Affects the formation of austenite and subsequent ausferrite. Higher temperatures generally result in higher toughness. |
Holding Time | Longer holding times allow for more complete transformation but may cause grain growth, impacting strength. |
Cooling Rate | Cooling in salt or polymer bath leads to a controlled cooling rate, ensuring uniform transformation to ausferrite. |
3. Advantages of Austempering Heat Treatment
The austempering process offers several key advantages that make it ideal for high-performance applications:
Increased Strength and Toughness
By transforming the microstructure into ausferrite, ADI exhibits excellent tensile strength and toughness, which are significantly higher than those of standard ductile iron. The material can withstand heavy loads and is less likely to fail under fatigue.
Improved Wear Resistance
The hardness of ADI is also significantly improved during the austempering process, making it highly resistant to wear. This is particularly beneficial in applications where friction and abrasion are common, such as gears, brake components, and heavy machinery.
Enhanced Fatigue Resistance
ADI exhibits excellent resistance to fatigue, which is critical for components subjected to cyclic loads. This makes it an ideal material for automotive suspension parts, crankshafts, and other components that experience repetitive stress.
Cost-Effective Performance
Compared to alternative materials such as steel, ADI offers a cost-effective solution for high-performance applications. The material’s combination of strength, toughness, and wear resistance makes it an attractive option for industries that require durable components but are concerned with material costs.
4. Effects of Heat Treatment on the Mechanical Properties of ADI
The heat treatment process of ADI significantly impacts its mechanical properties, particularly its hardness, tensile strength, and ductility.
-
Hardness: The austempering process increases the hardness of ductile iron, with values ranging from 40 HRC to 65 HRC depending on the grade.
-
Tensile Strength: Austempered ductile iron exhibits high tensile strength, which can reach up to 1,400 MPa in high-strength grades, making it suitable for high-load applications.
-
Ductility: Despite its high hardness, ADI maintains a relatively high level of ductility, which contributes to its toughness and resistance to brittle fracture.
Property | Before Austempering | After Austempering |
---|---|---|
Hardness | 20-40 HRC | 40-65 HRC |
Tensile Strength | 400–600 MPa | 600–1400 MPa |
Ductility | High | Moderate to High (depends on grade) |
5. Types of Austempered Ductile Iron Grades
Austempered ductile iron is classified into different grades based on the hardness and tensile strength achieved during the heat treatment process. The primary grades include:
-
Grade 1 (600–800 MPa tensile strength, 40–50 HRC): Commonly used for applications such as automotive components and industrial machinery.
-
Grade 2 (800–1000 MPa tensile strength, 50–55 HRC): Suitable for heavier applications like suspension components, axles, and gears.
-
Grade 3 (1000–1200 MPa tensile strength, 55–60 HRC): Often used in performance-oriented components where both strength and wear resistance are crucial.
-
Grade 4 (1200–1400 MPa tensile strength, 60–65 HRC): Ideal for highly demanding applications such as high-performance gears, bearings, and heavy machinery.
Grade | Tensile Strength (MPa) | Hardness (HRC) | Applications |
---|---|---|---|
Grade 1 | 600–800 | 40–50 | Automotive, industrial components |
Grade 2 | 800–1000 | 50–55 | Axles, gears, suspension parts |
Grade 3 | 1000–1200 | 55–60 | Performance gears, heavy machinery |
Grade 4 | 1200–1400 | 60–65 | High-performance components |
6. Applications of Austempered Ductile Iron
Austempered ductile iron is used in a wide variety of industries due to its excellent mechanical properties, which make it suitable for a range of applications:
-
Automotive Industry: Suspension components, crankshafts, gears, and other high-strength components.
-
Mining and Construction: Equipment such as crushers, excavator teeth, and heavy-duty machinery parts.
-
Power Generation: Components for turbines, gears, and bearings.
-
Heavy Machinery: Parts that need to withstand high loads, such as axles, housings, and drive shafts.
7. Factors Affecting the Success of Austempering Heat Treatment
Several factors influence the outcome of the austempering process, including:
-
Material Composition: The amount of carbon and other alloying elements in the ductile iron affects its response to austempering and the final mechanical properties.
-
Cooling Rate: The rate at which the material cools after austenitizing impacts the transformation to ausferrite and, consequently, the hardness and strength of the final product.
-
Austempering Time and Temperature: As mentioned earlier, careful control of temperature and holding time is critical to achieving the desired microstructure.
8. Common Problems and Solutions in Austempering
Despite its benefits, the austempering process can present challenges in some cases:
-
Incomplete Transformation: Inadequate quenching may result in incomplete transformation to ausferrite, which can reduce the material’s strength and toughness. To address this, ensure proper control of cooling rates.
-
Cracking or Warping: Improper cooling can lead to residual stresses, which may cause warping or cracking. The use of uniform and controlled cooling methods can help mitigate these issues.
9. Common Questions About Austempered Ductile Iron Heat Treatment
Q1: What are the benefits of using ADI over traditional cast iron?
ADI offers significant advantages over traditional cast iron, including improved strength, wear resistance, and fatigue resistance. These benefits make ADI ideal for high-performance applications where traditional cast iron would not suffice.
Q2: How does the austempering process affect the cost of ADI?
While the austempering process adds an extra step to production, the enhanced properties of ADI often result in cost savings in the long term. The material’s durability and performance can reduce the need for frequent replacements or repairs.
Q3: Is ADI more difficult to machine than regular ductile iron?
ADI can be more challenging to machine than regular ductile iron due to its increased hardness. However, with the proper tools and techniques, machining ADI is manageable, and the material’s benefits often outweigh the machining challenges.
Q4: How does the heat treatment process affect ADI’s fatigue resistance?
The austempering process enhances the fatigue resistance of ADI by creating a microstructure that resists the formation of cracks under cyclic stress. This makes it ideal for components that undergo repetitive loading, such as suspension parts in vehicles.
Q5: Can the hardness of ADI be customized for different applications?
Yes, by adjusting the austempering parameters, such as temperature and cooling rate, manufacturers can customize the hardness of ADI to suit specific application requirements.
Q6: What industries benefit most from ADI’s heat treatment?
ADI is particularly beneficial in industries such as automotive, mining, heavy machinery, and power generation, where high strength, wear resistance, and fatigue resistance are crucial.
Conclusion
Austempered ductile iron’s heat treatment process transforms ductile iron into a high-performance material with enhanced mechanical properties. By carefully controlling the temperature, time, and cooling rate during the austempering process, manufacturers can create a material that offers superior strength, wear resistance, and fatigue resistance. These benefits make ADI an ideal choice for a wide range of demanding applications in industries such as automotive, mining, and heavy machinery.