Ductile iron flanged fittings are critical components in high-pressure piping systems—widely used in water, wastewater, fire protection, and industrial applications.
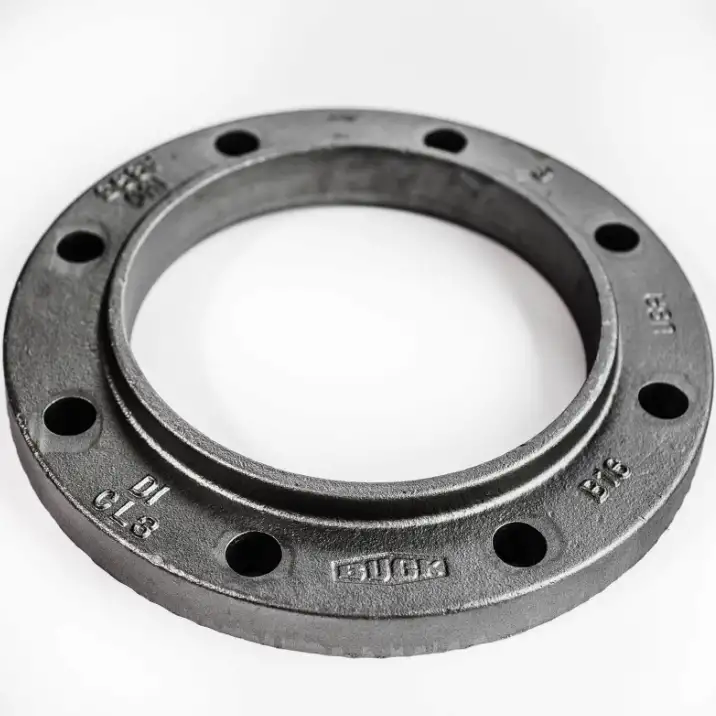
1. Material & Standard Specifications
Ductile iron flange fittings are produced according to stringent international standards to ensure mechanical integrity and interchangeability. Key specifications include:
-
AWWA C110/C153: Covers standard-weight and compact ductile iron fittings for flange dimensions, drilling patterns, and hydrostatic testing procedures .
-
EN 545 & EN 598: European standards defining dimensions, pressure classes (PN10, PN16, PN25), and material properties for ductile iron fittings .
-
ISO 2531 & ISO 7186: International standards specifying ductile iron pipe and fitting requirements—their mechanical performance, dimensional tolerances, and testing methods .
-
ASTM A536: Defines the required chemical composition and tensile strength (≥ 483 MPa for Grade 65-45-12) of ductile iron castings used in flanged fittings .
-
NSF/ANSI 61: Certifies internal linings (cement mortar, epoxy) for potable water applications, ensuring leachate limits are met .
Manufacturers often hold dual certifications (e.g., AWWA & EN) to serve global markets, with third-party validation by bodies like DVGW (Germany) and WRAS (UK) .
2. Flange Types & Drilling Patterns
Flanged ductile iron fittings connect via bolted flanges—critical for high-pressure and high-thrust services. Major flange types include:
2.1 Standard Drilling (AWWA/ANSI Class 150 & 300)
ANSI B16.1 Class 125 & Class 250 drilling patterns are often used on ductile iron, matching pump, valve, and pipe flanges in waterworks .
2.2 AWWA C110 (Class 150) vs. C153 (Class 350)
-
C110: Standard weight, thicker walls, heavier; used where higher strength is needed.
-
C153: Compact, thinner walls, lighter; ideal for retrofit and space-limited installations .
2.3 European PN Ratings (PN10, PN16, PN25)
PN-rated flanges per EN 1092-2 provide metric bolt circles and bolt sizes; PN16 correlates closely with ANSI Class 150 .
2.4 JIS & Other Regional Standards
Japanese JIS B2220 and other regional norms sometimes apply; careful specification avoids mismatches in bolt-hole patterns .
3. Dimensional Data
The following table summarizes key dimensions for common nominal sizes of ductile iron flanged fittings (AWWA Class 150) :
Nominal Size | OD (mm) | Bolt Circle Dia. (mm) | No. of Bolts | Bolt Dia. (mm) | Flange Thickness (mm) |
---|---|---|---|---|---|
3″ | 104.8 | 165.1 | 4 | 19 | 19 |
4″ | 127.0 | 190.5 | 4 | 19 | 19 |
6″ | 177.8 | 241.3 | 8 | 19 | 22 |
8″ | 229.0 | 298.5 | 8 | 22 | 22 |
10″ | 279.4 | 362.0 | 8 | 22 | 25 |
12″ | 323.9 | 415.1 | 8 | 22 | 25 |
16″ | 406.4 | 533.4 | 12 | 22 | 28 |
24″ | 609.6 | 762.0 | 12 | 22 | 31 |
Table 1: AWWA Class 150 Flange Dimensions
4. Size Ranges & Tolerances
Ductile iron flanged fittings are manufactured in sizes from DN 80 (3″) up to DN 1200 (48″), with tolerances as follows :
-
OD Tolerance: ± 1 mm for DN 80–DN 300; ± 2 mm for DN 350–DN 1200.
-
Bolt Circle Tolerance: ± 1.5 mm.
-
Flange Face Flatness: ≤ 0.5 mm.
-
Bolt-Hole Positional Tolerance: ≤ 1 mm.
Such precision ensures interchangeability between suppliers and compatibility with mating components.
5. Pressure Classes & Ratings
Ductile iron flanged fittings are rated by pressure class:
-
ANSI Class 150: ≈ 150 psi (1.03 MPa) @ 38 °C; bolt circle per ANSI B16.1 .
-
ANSI Class 300: ≈ 300 psi (2.07 MPa) @ 38 °C; heavier walls and larger bolts .
-
AWWA C153 Class 350: ≈ 350 psi (2.41 MPa) @ 38 °C; compact design .
-
PN10–PN25: Metric classes roughly align, e.g., PN16≈Class 150, PN25≈Class 300 .
Higher classes require thicker walls and more bolts, increasing weight and cost.
6. Weight & Cost Comparison
Below is a typical weight and approximate list price comparison for Class 150 vs. Class 350 flanged bends (16″/DN400) in USD (per unit) :
Class | Weight (kg) | Price (≈ 2025) |
---|---|---|
150 | 85 | $750 |
350 | 70 | $820 |
Table 2: 16″ Flanged Bend Weight & Price — prices vary by region and order quantity.
7. Pricing Factors & Market Rates
Price drivers include:
-
Raw Material Costs: Pig iron and scrap prices fluctuate with commodity markets .
-
Coating/Lining: Epoxy adds $20–$50 per unit; cement mortar less expensive .
-
Quantity & Lead Time: Bulk orders (≥ 100 pcs) often secure 10–15 % discounts; rush jobs (> 2 week lead) incur premiums .
-
Custom Drilling & Machining: Non-standard bolt patterns add machining charges.
-
Logistics: Weighty items incur higher freight; clustering shipments reduces per-unit cost.
8. Installation & Maintenance Considerations
-
Gasket Selection: EPDM for potable water; Buna-N for oil; PTFE for chemicals .
-
Bolt Torque Values: Follow manufacturer’s spec (e.g., 175 Nm for 22 mm bolts) to ensure seal without flange distortion .
-
Alignment Tools: Use flange spreaders and drift pins to align bolt holes.
-
Periodic Re-torque: After 24 h and 6 months to compensate for gasket relaxation.
9. Selection Guide & Application Examples
9.1 Municipal Water
PN16 flanges with cement lining, push-on spigots—cost-effective and corrosion-resistant.
9.2 Fire Protection
Class 350 epoxy-lined flanges for high surge loads; NSF-61 compliant.
9.3 Industrial Chemicals
PTFE-lined flanges, ANSI Class 300 for aggressive fluids; mechanical joints for maintenance ease.
Common Questions & Answers
Q1: How do flange drilling patterns differ between ANSI and PN standards?
Flange drilling patterns define the bolt‐hole arrangement—bolt circle diameter, number of holes, and hole size—that secures two mating flanges together. In the United States, ANSI/ASME B16.1 (Class 125/150) and B16.42 (Class 150/300) govern ductile iron flange patterns, while European PN-rated flanges conform to EN 1092-2 (PN10, PN16, PN25, etc.). ANSI B16.1 Class 150 flanges for a 6″ nominal pipe size, for example, employ eight 19 mm bolt holes on a 241.3 mm bolt circle; by contrast, EN 1092-2 PN16 for DN 150 uses eight M16 holes on a 225 mm bolt circle.
Because the bolt circle diameters and hole diameters differ, an ANSI Class 150 flange will not physically mate with a PN16 flange of the same nominal size: the hole spacing and diameters simply do not align. This incompatibility extends across most classes—ANSI 300 (B16.42) vs. PN25 patterns also mismatch in both bolt circle and hole count.
Moreover, the flange face style (flat face vs. raised face) can vary: ANSI flanges often use raised faces per B16.1, whereas European PN flanges may use flat faces with full‐face gaskets under EN 1092-2. Even when a bolt circle roughly aligns (e.g., PN16 vs. ANSI 150), differences in face design and tolerances necessitate adapters or bespoke drilling to ensure a leak‐tight seal.
In practice, piping specifications must explicitly state the standard (e.g., “AWWA C110 Class 150” or “EN 1092-2 PN16”) to prevent mismatches. Adapter flanges—flanges with dual drilling patterns—are sometimes used to transition between ANSI and PN systems, but these add cost and potential points of failure. Always verify bolt‐hole layout, bolt diameter, and flange face style before procurement and installation.
Q2: What factors influence the price of ductile iron flanged fittings?
The unit price of a ductile iron flanged fitting is driven by multiple interrelated factors, including raw material costs, manufacturing complexity, coating/lining, quantity, and logistics. Raw material—primarily pig iron and scrap—tracks global commodity markets; when steel mill bloom and scrap prices climb, so do casting prices. According to commodity indices, a 10 % rise in global scrap steel can translate to a 5–8 % increase in ductile iron fitting costs within two months.
Manufacturing complexity varies with size, pressure class, and special features. Larger diameters (e.g., 24″/DN 600+) require larger molds, more material, and longer machining cycles, increasing per-unit costs by up to 30 % over a 6″/DN 150 equivalent. Compact fittings (AWWA C153 Class 350) have thinner walls and more precise machining to meet compactness requirements, which can add 5–10 % premium over standard‐weight C110/C153 castings.
Surface treatment choices also affect price. Basic bituminous coatings add minimal cost (~$5–$10 per unit), whereas proprietary polyurethane finishes or NSF/ANSI 61-certified epoxy linings incur $20–$50 additional, depending on thickness and batch size.
Order quantity and lead time are powerful levers: bulk orders (≥ 100 pcs) typically qualify for 10–15 % volume discounts, whereas rush deliveries (< 2 weeks) carry 15–25 % surcharges to prioritize tooling and scheduling. Finally, logistics—heavy castings shipped internationally—can add 10–20 % to FOB price; consolidating shipments and using intermodal transport can mitigate freight costs.
In summary, the price you pay reflects a combination of metal markets, casting size/complexity, internal/external treatments, purchasing strategy, and transportation logistics. Specifying the correct combination of size, class, and coating in the RFQ—and ordering in strategic volumes with reasonable lead times—ensures you achieve the best pricing outcome.
Q3: What are the best practices for installing and torquing ductile iron flanged fittings?
Correct installation of ductile iron flanged fittings is essential for leak‐free performance and long‐term reliability. Gasket selection must match the service: EPDM gaskets for potable water, Buna-N for oils, and PTFE for aggressive chemicals . Always inspect gaskets for cuts or debris before assembly.
Bolt quality and lubrication matter: use high‐strength alloy bolts (ASTM A193 Grade B7 or equivalent) with lubricated threads to ensure accurate torque readings and consistent gasket compression. A study by United Water Products recommends lubricating both bolt threads and underside of heads with anti‐seize compound to reduce galling and ensure uniform load distribution.
Follow the star pattern tightening sequence: gradually snug all bolts to 30 % of final torque, then 60 %, then 100 % in three passes, always in a crisscross (star) pattern. This ensures even flange face contact and prevents gasket extrusion . Typical torque values—for instance, 175 Nm for 22 mm diameter bolts—are provided by the gasket manufacturer; never exceed flange face pressure limits indicated by ASME B16.1 or EN 1092-2.
Alignment tools such as drift pins and flange spreaders help center the spigot and socket, minimizing misalignment that can over‐stress flanges. After initial assembly, perform a hydrostatic test at 1.5× design pressure to verify seal integrity; retorque bolts to 100 % after the test pressure and again after 24 hours to compensate for gasket relaxation.
For long‐term maintenance, schedule periodic inspections: re‐torque heavy bolted joints at 6 months, check for corrosion on flanges and bolts, and replace gaskets every 5–10 years or if moisture ingress is detected. Proper training, following manufacturer instructions, and adhering to recognized standards (ASME B16.1, EN 1092-2) are the bedrock of flaw-free installation.
Q4: How do I select the proper gasket for ductile iron flanged connections?
Gasket material and design directly impact sealing performance, chemical compatibility, and service life. Elastomeric gaskets (EPDM, NBR/Buna-N) are common for water and mild chemical services: EPDM offers broad resistance to chlorine and UV, operating from -40 °C to +120 °C; Buna-N handles hydrocarbon oils up to +80 °C but degrades in ozone and ketones .
For acidic or aggressive fluids, PTFE (Teflon®) gaskets provide excellent chemical resistance and a wide temperature range (-200 °C to +260 °C), but require higher seating loads and may cold‐flow under sustained pressure unless supported by metal core designs. Spiral‐wound gaskets—alternating metal and filler—are ideal for high‐pressure Class 300 or PN25 services; they offer resilience to thermal cycling but cost 3–5× more than simple elastomeric rings.
When selecting a gasket, match its type (flat ring, full‐face, ring‐type joint) to flange face design: flat gaskets pair with flat faces; ring-type gaskets require ring-joint grooves. Check the seating stress requirements: gasket datasheets specify the bolt load needed to compress the filler material and achieve a seal; ensure your bolting scheme (bolt size, number, torque) attains this load without over‐stressing flanges.
Also consider gasket thickness: thicker gaskets accommodate flange face irregularities but may extrude under pressure. Standard thicknesses range from 1.5 mm to 3 mm; specialty services may need 5 mm or composite designs. Consult EN 1514-1 or ASME B16.21 for dimension and tolerance guidelines. Lastly, verify certifications (NSF/ANSI 61 for potable water, FDA for food) and consult the gasket manufacturer for compatibility with your fluid’s pH, temperature, and particulate content.
Q5: Can ANSI/ASME flanges be interchanged with ISO/EN flanges on ductile iron fittings?
In general, ANSI/ASME and ISO/EN flanges are not directly interchangeable due to differences in bolt circle diameters, bolt hole sizes, hole counts, and flange face designs. ANSI/ASME B16.1 Class 150 for a 4″ flange uses a 190.5 mm bolt circle with four 19 mm holes, whereas EN 1092-2 PN16 for DN 100 specifies a 185 mm bolt circle with four M16 holes; these mismatches prevent direct mating without adapters or custom drilling.
Flange face styles also differ: ASME flanges often have raised faces (RF), while EN flanges may use flat faces (FF) with full‐face gaskets, affecting gasket choice. Even if bolt circles align, differences in tolerances (e.g., bolt‐hole positional tolerance ±1 mm for EN vs. ±0.5 mm for ANSI) can lead to misalignment and gasket shear.
To connect ANSI to ISO systems, specialized transition flanges or dual‐pattern flanges are manufactured with one face drilled to ANSI and the opposite to ISO standards; these incur added cost (typically 20–30 % premium) and require careful quality control to ensure both patterns meet their respective dimensional standards.
Alternatively, some engineers use stub ends with lap joint flanges: the stub end welds to the pipe, and the loose flange (designed to EN or ANSI) slides over and bolts up. This approach isolates the flange pattern from the pipe and facilitates future changes, but requires additional welding and inspection. In all cases, specifying the exact drilling pattern and standard in procurement documents is critical to avoid mismatches, delays, and costly rework.
Q6: What maintenance practices maximize the service life of ductile iron flanged fittings?
Routine maintenance extends the operational lifespan of ductile iron flanged fittings by preventing corrosion, joint leakage, and mechanical degradation. External coatings—bituminous, epoxy, or polyurethane—should be visually inspected annually; any coating damage or blistering must be repaired within 30 days to prevent soil‐side corrosion. For buried systems, stray current surveys and cathodic protection checks are advisable every 3–5 years to ensure adequate corrosion mitigation.
Internally, perform periodic flushing to remove sediment and biofilm; stagnant zones promote microbiologically influenced corrosion (MIC). Maintaining water pH between 6.8 and 8.5 reduces corrosive potential. Where aggressive waters exist, inspect inside surfaces via CCTV or pigging operations every 5 – 10 years; consider epoxy recoating if interior roughness exceeds design limits.
Bolt tension relaxation is another concern: elastomeric gaskets can creep under sustained load, reducing sealing pressure. Retorque flange bolts to 100 % of the specified torque after initial service and again at 6 months; thereafter, inspect bolt torque annually, retightening as needed to the recommended values (e.g., 175 Nm for 22 mm bolts) .
Finally, maintain detailed service records—installation date, test pressures, torque logs, coating inspections—to enable condition‐based maintenance and predict component replacement timing. By combining proactive inspection, timely coating repair, bolt re‐torquing, and fluid chemistry management, fittings can routinely exceed 50 years of trouble‐free service in municipal and industrial pipelines.