When discussing materials used in construction, automotive, or manufacturing industries, ductile iron is often mentioned due to its remarkable strength, flexibility, and durability. But a common question arises: Is ductile iron an alloy? The answer to this question requires a deep understanding of the material’s composition, properties, and the way it differs from other forms of iron.
In this article, we will thoroughly examine whether ductile iron qualifies as an alloy, its chemical makeup, the role of alloying elements, and how it compares to other types of iron, such as gray cast iron and steel. We will also explore its uses, advantages, and applications in various industries, providing expert insights and clarifications for those unfamiliar with the material.
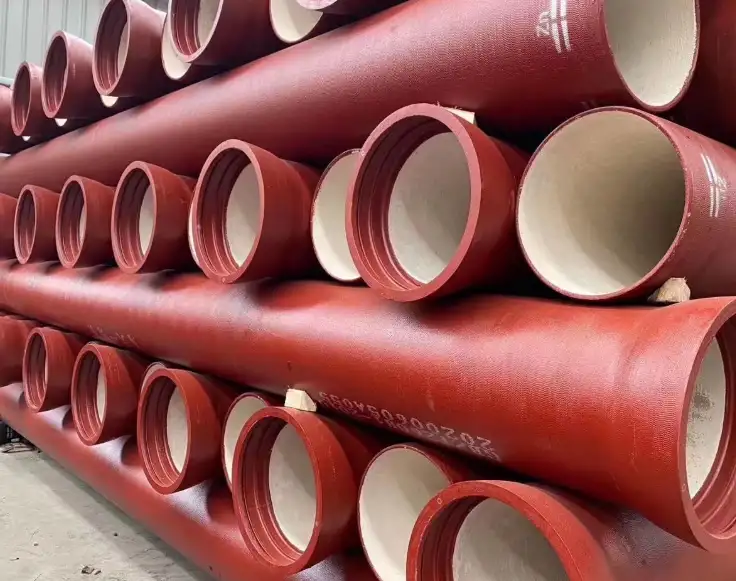
1. What is Ductile Iron?
Before answering whether ductile iron is an alloy, it’s important to understand what ductile iron actually is. Ductile iron, also known as ductile cast iron, is a type of cast iron that is characterized by its enhanced mechanical properties. This material is produced by adding small amounts of magnesium (and sometimes other alloying elements) to molten cast iron, which results in the formation of spheroidal (nodular) graphite within the iron. This transformation significantly improves the material’s strength and malleability.
Key Features of Ductile Iron:
-
High Strength: Ductile iron is much stronger than traditional cast iron due to the structure created by the spheroidal graphite.
-
Ductility: Unlike traditional cast iron, which is brittle and prone to cracking, ductile iron is much more flexible, allowing it to absorb stress and strain.
-
Good Shock Absorption: Its ability to handle impact and stress without fracturing makes ductile iron suitable for a wide range of applications.
-
Corrosion Resistance: Ductile iron is more resistant to corrosion than traditional cast iron, especially when coated or treated with specific protective layers.
The process of creating ductile iron by adding magnesium to molten iron is also called nodularization, and it results in an iron alloy with specific mechanical properties.
2. Is Ductile Iron an Alloy?
Now, to address the question directly: Is ductile iron an alloy?
The Composition of Ductile Iron:
Ductile iron is often referred to as an “alloyed” form of cast iron, but technically, it is not an alloy in the same sense as materials like steel or bronze. While ductile iron does contain alloying elements (such as magnesium, silicon, and manganese), its base metal is still iron. This is an important distinction that sets ductile iron apart from other true alloys.
An alloy is defined as a mixture of two or more elements, with at least one of them being a metal. In the case of ductile iron, the base metal is iron, and the alloying elements (magnesium and others) modify the properties of the iron but do not fundamentally change its nature as iron. Therefore, ductile iron can be considered an iron alloy, but it’s primarily categorized as a type of cast iron with improved properties due to alloying elements.
Key Differences Between Ductile Iron and True Alloys:
-
Base Metal: Ductile iron’s base metal is iron, while true alloys often use other metals as their base, such as steel (iron-carbon alloy), bronze (copper-tin alloy), or brass (copper-zinc alloy).
-
Role of Alloying Elements: In ductile iron, the alloying elements primarily serve to alter the graphite structure and improve mechanical properties, while in other alloys, the elements often combine to create a new material with different physical and chemical properties.
3. How Ductile Iron Differs from Other Cast Irons
To further understand whether ductile iron qualifies as an alloy, it’s useful to compare it to other forms of cast iron. Cast iron is a group of alloys that generally consist of iron and carbon, with varying levels of additional elements. Here are the main types of cast iron and how they compare to ductile iron:
Comparison of Ductile Iron with Other Cast Irons:
Type of Cast Iron | Composition | Properties | Applications |
---|---|---|---|
Ductile Iron | Iron, carbon, magnesium, and other elements | High strength, malleability, shock resistance | Automotive, infrastructure, machinery parts |
Gray Cast Iron | Iron, carbon, silicon, and other trace elements | Brittle, good machinability, excellent castability | Engine blocks, pipes, machine bases |
White Cast Iron | Iron, carbon, and low silicon | Hard, brittle, wear-resistant | Wear-resistant parts, castings |
Malleable Cast Iron | Iron, carbon, and small amounts of alloying elements | More malleable than gray cast iron | Pipe fittings, structural parts |
Steel | Iron and carbon with controlled levels of other elements | High tensile strength, toughness, ductility | Structural beams, automotive, manufacturing |
Distinct Features of Ductile Iron:
-
Unlike gray cast iron, which has flaky graphite that makes it brittle, ductile iron has nodular graphite, which provides enhanced strength and flexibility.
-
Ductile iron is more resistant to wear and tear compared to gray cast iron and is less prone to cracking under stress.
-
Ductile iron is often used in more demanding applications, including automotive and heavy machinery, because of its durability and impact resistance.
4. The Role of Alloying Elements in Ductile Iron
While ductile iron is not technically classified as a full alloy, the alloying elements it contains significantly enhance its properties. The primary alloying element in ductile iron is magnesium, which is added to the molten iron in precise amounts. The role of magnesium is to alter the graphite structure in the iron, transforming the graphite from flaky particles into spherical nodules.
Common Alloying Elements in Ductile Iron:
-
Magnesium (Mg): The key element that makes cast iron “ductile.” It promotes the formation of nodular graphite and increases tensile strength and ductility.
-
Silicon (Si): Silicon is often added to ductile iron to promote fluidity during casting and to improve the material’s resistance to oxidation.
-
Manganese (Mn): Manganese helps improve the strength of ductile iron by controlling the amount of sulfur and oxygen.
-
Phosphorus (P): Phosphorus is usually kept at low levels to avoid brittleness, but small amounts can enhance machinability and corrosion resistance.
-
Carbon (C): Ductile iron typically contains 3.0% to 4.0% carbon, which is crucial for its casting properties.
Impact of Alloying Elements on Properties:
-
The addition of magnesium and other elements alters the microstructure of the material, providing it with higher tensile strength, better wear resistance, and improved ductility.
-
The choice and amount of alloying elements can also affect the material’s corrosion resistance, fatigue strength, and machinability.
5. Applications of Ductile Iron
Ductile iron’s unique combination of strength, malleability, and corrosion resistance makes it suitable for a wide range of applications:
-
Automotive Industry: Components such as engine blocks, crankshafts, and suspension parts benefit from ductile iron’s strength and shock resistance.
-
Infrastructure: Ductile iron is commonly used in pipes and fittings for water, sewage, and gas systems due to its durability and resistance to corrosion.
-
Heavy Machinery: Parts such as gears, housings, and frames that need to absorb shocks and withstand high pressure often utilize ductile iron.
6. Commonly Asked Questions
1. Is ductile iron an alloy or just a type of cast iron?
Ductile iron is often categorized as a type of cast iron, but it is not a full alloy in the same sense as materials like steel or bronze. While it does contain alloying elements such as magnesium, these elements modify the properties of the base iron rather than creating a completely new alloy.
2. What makes ductile iron different from regular cast iron?
The primary difference between ductile iron and regular cast iron is the presence of spheroidal graphite. Ductile iron is created by adding magnesium to molten iron, which causes the graphite to form nodules instead of flakes. This gives ductile iron its higher strength, malleability, and improved shock resistance compared to regular cast iron, which is more brittle.
3. How does magnesium affect the properties of ductile iron?
Magnesium is the key element that transforms cast iron into ductile iron. It promotes the formation of nodular graphite, which prevents the material from cracking under stress and increases its tensile strength. The amount of magnesium added to the iron determines the final properties of the ductile iron, such as its malleability and corrosion resistance.
4. Can ductile iron be used for high-stress applications?
Yes, ductile iron is ideal for high-stress applications due to its high tensile strength and excellent shock absorption properties. It is commonly used in industries like automotive, construction, and manufacturing, where components are exposed to high levels of stress and need to resist impact without cracking or breaking.
5. Is ductile iron more expensive than gray cast iron?
Yes, ductile iron is typically more expensive than gray cast iron because of the additional alloying elements, such as magnesium, required to produce the material. The manufacturing process for ductile iron is also more complex and requires precise control of the alloying process. However, the increased durability and strength of ductile iron often justify the higher cost in applications where performance is critical.
6. What are the advantages of using ductile iron over steel?
While steel is stronger than ductile iron, ductile iron has advantages in certain applications. It is more castable and less expensive to produce in large quantities, making it ideal for mass production of parts. Additionally, ductile iron offers better wear resistance and corrosion resistance in some environments, making it preferable for components like pipes, automotive parts, and heavy machinery.
Conclusion
Ductile iron is a unique form of cast iron that is enhanced by the addition of alloying elements like magnesium, making it stronger, more flexible, and more durable than traditional cast iron. While it is not a full alloy in the strictest sense, it is an alloyed material with significant improvements in mechanical properties compared to standard cast iron. Understanding the composition, properties, and applications of ductile iron is essential for selecting the right material for a variety of industrial needs.