Ductile iron pipe (DIP) is a cornerstone of modern water, wastewater, and industrial piping systems, prized for its durability, pressure resilience, and adaptability. The outside diameter (OD) of a 12-inch DIP is a critical dimension that ensures compatibility with fittings, valves, and trenchless installation methods. According to ANSI/AWWA C151, the standard OD for a 12-inch DIP is 13.20 inches (335.3 mm), while ISO 2531 specifies a slightly different OD of 335.5 mm for Class K9.
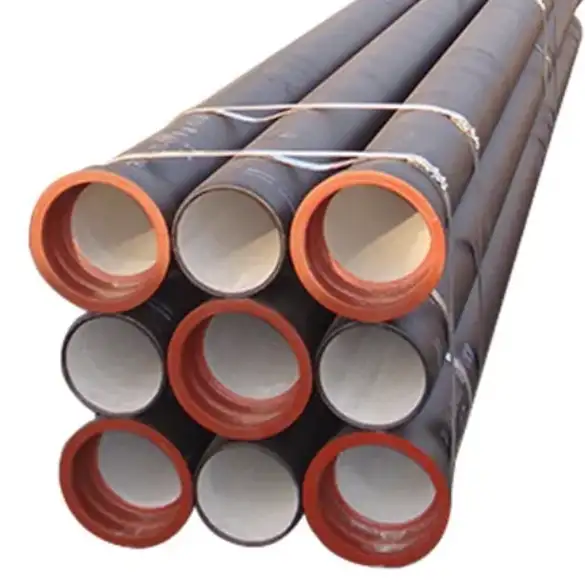
Global Standards for 12-Inch DIP OD
Standard | OD (inches/mm) | Pressure Class | Region |
---|---|---|---|
ANSI/AWWA C151 | 13.20″ / 335.3 mm | Class 50, 52, 56 | North America |
ISO 2531 | 335.5 mm | K9, K10, K12 | Europe, Asia |
GB/T 13295 | 335.0 mm | PN10, PN16 | China |
Key Takeaway: Minor OD variations exist between standards but are designed to maintain compatibility within regional systems.
Pressure Classes and OD Variations
The OD of a 12-inch DIP remains consistent across pressure classes, but wall thickness increases for higher-pressure ratings:
AWWA Class | Wall Thickness (mm) | OD Consistency | Max Pressure (psi) |
---|---|---|---|
50 | 7.6 | 13.20″ | 250 |
52 | 8.1 | 13.20″ | 300 |
56 | 9.0 | 13.20″ | 350 |
Applications:
-
Class 50: Low-pressure sewage systems.
-
Class 52: Municipal water distribution.
-
Class 56: High-pressure industrial pipelines.
Material Composition and Manufacturing
Ductile iron’s microstructure—nodular graphite in a ferrite-pearlite matrix—is achieved by adding magnesium during casting. This structure provides:
-
Tensile Strength: 60,000–90,000 psi (ASTM A536).
-
Elongation: 10–18%, ensuring flexibility under stress.
Manufacturing Process:
-
Melting: Iron scrap, steel, and carbon are melted at 2,300°F (1,260°C).
-
Nodularization: Magnesium treatment converts graphite flakes to spheroids.
-
Casting: Centrifugal casting ensures uniform OD and wall thickness.
Impact of OD on Jointing and Installation
A standardized OD simplifies compatibility with joint systems:
Joint Type | OD Tolerance | Installation Method |
---|---|---|
Push-On | ±1.5 mm | Rubber gasket compression |
Mechanical | ±1.0 mm | Bolted gland assembly |
Flanged | ±0.8 mm | Bolt torque alignment |
Installation Tip: Use laser-guided alignment tools to prevent joint stress due to OD mismatches.
OD vs. ID: Understanding Pipe Sizing
While OD is standardized, inner diameter (ID) decreases with higher pressure classes due to thicker walls:
Class | OD (mm) | ID (mm) | Lining Thickness (mm) |
---|---|---|---|
50 | 335.3 | 320.1 | 1.5 |
52 | 335.3 | 319.1 | 1.5 |
56 | 335.3 | 317.3 | 1.5 |
Design Consideration: ID impacts flow rates—engineers must account for lining thickness in hydraulic calculations.
Comparison with Alternative Materials
Material | OD (12″) | Max Pressure (psi) | Lifespan (Years) | Cost per Foot |
---|---|---|---|---|
DIP | 13.20″ | 350 | 100+ | 200–200–400 |
PVC | 13.50″ | 200 | 50–75 | 80–80–150 |
HDPE | 13.30″ | 160 | 50–100 | 100–100–200 |
Steel | 12.75″ | 500 | 30–50 | 250–250–600 |
Advantage: DIP balances pressure capacity, longevity, and corrosion resistance.
Corrosion Protection and OD Integrity
Coating Type | Application Method | OD Impact | Lifespan Extension |
---|---|---|---|
Cement Lining | Spin-coated | None | 50+ years |
Polyethylene | Encasement | +2–3 mm OD | 75+ years |
Zinc + Epoxy | Spray-applied | +0.5 mm OD | 30–50 years |
Best Practice: Conduct soil resistivity tests to select coatings for corrosive environments.
Material Composition and Manufacturing Process
Ductile iron is produced by adding small amounts of magnesium to molten iron, which causes the graphite to form as spherical nodules. This process enhances the material’s ductility and strength. The manufacturing process involves:
-
Melting: High-quality scrap iron is melted in an induction furnace.
-
Alloying: Magnesium is added to the molten iron to achieve the desired chemical composition.
-
Casting: The molten metal is poured into molds to form the pipe shape.
-
Heat Treatment: The castings are heat-treated to achieve the desired mechanical properties.
-
Machining: Final dimensions are achieved through machining processes.
Mechanical Properties and Performance
Ductile iron pipes exhibit superior mechanical properties compared to traditional cast iron pipes:
-
Tensile Strength: Approximately 60,000 psi (414 MPa)
-
Yield Strength: Approximately 42,000 psi (290 MPa)
-
Elongation: Approximately 10-15%
-
Impact Resistance: High, due to the material’s ductility
These properties make ductile iron pipes suitable for applications subjected to dynamic loads and environmental stresses.
Corrosion Resistance and Longevity
Ductile iron pipes offer excellent resistance to corrosion, especially when coated or lined with protective materials. The internal surfaces are often lined with cement mortar or epoxy coatings to prevent corrosion and extend the pipe’s lifespan. With proper maintenance, ductile iron pipes can last over 100 years.
Frequently Asked Questions (FAQs)
1. What is the outer diameter of a 12-inch ductile iron pipe?
An AWWA C151 standard 12-inch ductile iron pipe has an outside diameter of 13.20 inches (335.20 mm). This dimension ensures compatibility with various fittings and joints in piping systems.
2. How does the wall thickness of a 12-inch ductile iron pipe vary?
The wall thickness of a 12-inch ductile iron pipe varies depending on the pressure class. For example, a Class 350 pipe may have a wall thickness of 0.31 inches (7.87 mm), while a Class 250 pipe may have a wall thickness of 0.28 inches (7.11 mm).
3. What is the typical length of a 12-inch ductile iron pipe?
The typical length of a 12-inch ductile iron pipe is 20 feet (6.096 meters), although other lengths may be available depending on the manufacturer and project requirements.
4. What are the advantages of using ductile iron pipes over traditional cast iron pipes?
Ductile iron pipes offer superior strength, flexibility, and resistance to corrosion compared to traditional cast iron pipes. These properties result in longer service life and reduced maintenance costs.
5. Can ductile iron pipes be used for both water and wastewater systems?
Yes, ductile iron pipes are suitable for both water and wastewater systems. They are commonly used in municipal water distribution networks and sewage systems due to their durability and performance.
6. Are there any environmental benefits to using ductile iron pipes?
Ductile iron pipes are recyclable and have a longer lifespan, reducing the frequency of replacements and conserving resources. Additionally, their durability reduces the need for repairs and replacements, minimizing environmental impact.
Conclusion
12-inch ductile iron pipes are a reliable and durable choice for various infrastructure projects. Their standardized dimensions, superior mechanical properties, and resistance to corrosion make them suitable for applications in water distribution, sewage systems, and industrial operations. Understanding their specifications and benefits can aid in making informed decisions for infrastructure projects.