1018 steel (a low-carbon steel) and ductile iron (nodular cast iron) differ fundamentally in tensile strength (65,000 psi vs. 60,000-120,000 psi), corrosion resistance (poor vs. moderate with coatings), and cost (20-30% lower for 1018 steel). While 1018 steel excels in machinability and welding for automotive shafts, ductile iron outperforms in impact absorption and vibration damping for water pipes and gearboxes.
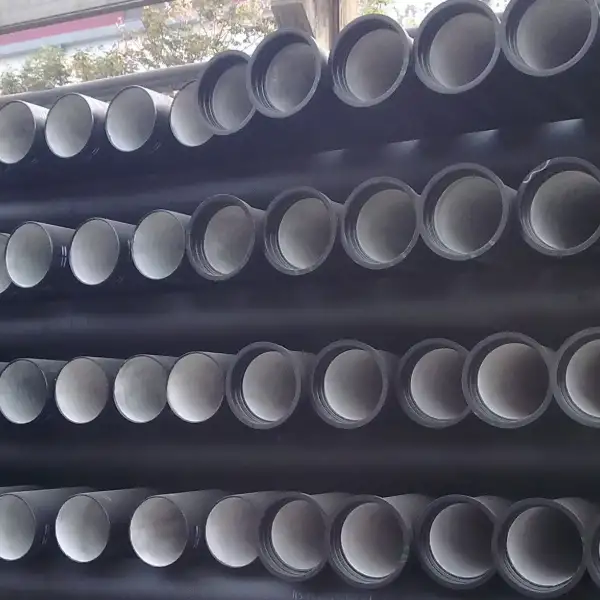
1. Composition and Microstructure
1018 Steel:
-
Chemical Composition: 1018 steel is a low-carbon steel with approximately 0.18% carbon content. It also contains small amounts of manganese, phosphorus, and sulfur.
-
Microstructure: The low carbon content results in a ferrite and pearlite microstructure, providing a balance between strength and ductility.
Ductile Iron:
-
Chemical Composition: Ductile iron, also known as nodular cast iron, typically contains 3.0–3.9% carbon and 1.8–2.8% silicon, along with trace amounts of manganese, phosphorus, sulfur, and magnesium.
-
Microstructure: The addition of magnesium transforms the graphite flakes found in gray iron into spherical nodules, enhancing ductility and toughness.
Comparison Table:
Property | 1018 Steel | Ductile Iron |
---|---|---|
Carbon Content | ~0.18% | 3.0–3.9% |
Silicon Content | ~0.2–0.4% | 1.8–2.8% |
Graphite Form | None | Spheroidal (nodular) |
Microstructure | Ferrite and pearlite | Ferrite matrix with graphite nodules |
2. Mechanical Properties
1018 Steel:
-
Tensile Strength: Approximately 440 MPa (63,800 psi).
-
Yield Strength: Approximately 370 MPa (53,700 psi).
-
Elongation at Break: Around 15%.
-
Hardness: Brinell hardness of about 126.
Ductile Iron (Grade 65-45-12):
-
Tensile Strength: Approximately 448 MPa (65,000 psi).
-
Yield Strength: Approximately 310 MPa (45,000 psi).
-
Elongation at Break: Around 12%.
-
Hardness: Brinell hardness ranging from 170 to 210.
Comparison Table:
Property | 1018 Steel | Ductile Iron (65-45-12) |
---|---|---|
Tensile Strength | ~440 MPa | ~448 MPa |
Yield Strength | ~370 MPa | ~310 MPa |
Elongation | ~15% | ~12% |
Hardness (Brinell) | ~126 | 170–210 |
3. Machinability and Weldability
Machinability:
-
1018 Steel: Known for excellent machinability due to its low carbon content and fine grain structure. It is often used in applications requiring extensive machining.
-
Ductile Iron: Offers good machinability, though not as high as 1018 steel. The presence of graphite nodules can lead to increased tool wear.
Weldability:
-
1018 Steel: Exhibits excellent weldability with all standard welding techniques. Preheating is generally not required.
-
Ductile Iron: Welding is more challenging due to the high carbon content and potential for graphite formation in the heat-affected zone, which can lead to brittleness. Specialized welding procedures and preheating are often necessary.
Comparison Table:
Property | 1018 Steel | Ductile Iron |
---|---|---|
Machinability | Excellent | Good |
Weldability | Excellent | Moderate to Poor |
Tool Wear | Low | Moderate to High |
Preheating Required | No | Often Yes |
4. Corrosion Resistance and Surface Finish
Corrosion Resistance:
-
1018 Steel: Susceptible to corrosion if not properly protected. Often requires coatings or painting for corrosion resistance.
-
Ductile Iron: Offers better inherent corrosion resistance due to the graphite content, which provides a degree of cathodic protection. However, it is still prone to corrosion in aggressive environments and may require protective coatings.
Surface Finish:
-
1018 Steel: Can achieve a smooth surface finish, making it suitable for aesthetic applications.
-
Ductile Iron: Typically has a rougher surface finish due to the casting process. Additional machining may be required for applications demanding smooth surfaces.
Comparison Table:
Property | 1018 Steel | Ductile Iron |
---|---|---|
Corrosion Resistance | Moderate (with protection) | Better than 1018 (inherent) |
Surface Finish | Smooth | Rough (as-cast) |
Protective Coatings | Often Required | Sometimes Required |
5. Applications
1018 Steel:
-
Common Uses: Shafts, pins, rods, spindles, gears, and various machine parts.
-
Industries: Automotive, construction, machinery manufacturing, and general engineering.
Ductile Iron:
-
Common Uses: Pipes, fittings, automotive components, agricultural machinery, and heavy-duty gears.
-
Industries: Water and sewage, automotive, agriculture, and heavy machinery.
Comparison Table:
Application Area | 1018 Steel | Ductile Iron |
---|---|---|
Automotive Parts | Shafts, gears | Suspension components |
Machinery | Pins, rods | Housings, brackets |
Piping Systems | Not common | Widely used |
Structural Components | Yes | Yes |
6. Cost and Availability
Material Cost
1018 Steel: Generally, 1018 steel is more expensive than ductile iron. The higher cost is attributed to the additional processing steps involved in steel production, such as rolling and heat treatments, which enhance its mechanical properties and surface finish.
Ductile Iron: Ductile iron is typically less expensive, especially for large castings. Its lower production costs stem from the casting process, which requires less energy and fewer processing steps compared to steel manufacturing.
Production and Fabrication Costs
1018 Steel: The fabrication of 1018 steel components involves processes like machining, welding, and forming. While these processes are straightforward due to the material’s excellent machinability and weldability, they can add to the overall cost, especially for complex parts.
Ductile Iron: The casting process used for ductile iron allows for the production of complex shapes in a single operation, reducing the need for extensive machining. This capability can lead to significant cost savings in the production of intricate components.
Comparison Table:
Property | 1018 Steel | Ductile Iron |
---|---|---|
Material Cost | Higher | Lower |
Production Cost | Higher | Lower |
Availability | High (various forms) | High (cast forms) |
Frequently Asked Questions (FAQs)
Q1: Which material is better for welding applications, 1018 steel or ductile iron?
A1: 1018 steel is generally better suited for welding applications due to its low carbon content and excellent weldability. It can be welded using standard techniques without the need for preheating. Ductile iron, on the other hand, has a higher carbon content and requires specialized welding procedures, including preheating and controlled cooling, to prevent cracking and maintain mechanical properties.
Q2: Can 1018 steel and ductile iron be used interchangeably in structural applications?
A2: While both materials have comparable tensile strengths, their other properties differ significantly. 1018 steel offers better ductility and weldability, making it suitable for applications requiring forming and joining. Ductile iron provides better vibration damping and is more cost-effective for large castings. Therefore, interchangeability depends on the specific requirements of the application.
Q3: How do the corrosion resistance properties of 1018 steel and ductile iron compare?
A3: Ductile iron generally offers better inherent corrosion resistance due to the presence of graphite, which provides some cathodic protection. However, in aggressive environments, both materials may require protective coatings. 1018 steel is more prone to corrosion and typically needs additional protection, such as painting or galvanizing, to enhance its corrosion resistance.
Q4: Which material is more cost-effective for large-scale casting applications?
A4: Ductile iron is typically more cost-effective for large-scale casting applications. Its casting process allows for the production of complex shapes in a single operation, reducing the need for extensive machining and assembly. This capability, combined with lower material and production costs, makes ductile iron a preferred choice for large cast components.
Q5: What are the differences in machinability between 1018 steel and ductile iron?
A5: 1018 steel is known for its excellent machinability due to its low carbon content and fine grain structure. It is often used in applications requiring extensive machining. Ductile iron offers good machinability but not as high as 1018 steel. The presence of graphite nodules in ductile iron can lead to increased tool wear, making it less ideal for applications requiring high-precision machining.
Q6: Which material is more suitable for applications requiring high vibration damping?
A6: Ductile iron is more suitable for applications requiring high vibration damping. Its graphite-rich microstructure provides superior damping capacity compared to 1018 steel. This property makes ductile iron an excellent choice for components like engine blocks, pump housings, and machinery bases, where vibration damping is critical.
References:
1018 Steel Material Properties – MatWeb
ASTM Committee E28 on Metal Castings and Ductile Iron Standards
Ductile Iron – Wikipedia
Steel Alloys and Their Mechanical Properties – Engineering Toolbox