The number of bolts required for a 10-inch ductile iron pipe flange depends on the flange class and applicable standards. According to the ANSI/AWWA C115/A21.15 standard for Class 125 flanges, a 10-inch ductile iron flange typically requires 12 bolts. These bolts are usually 7/8 inches in diameter and 3.5 inches in length, arranged evenly around a bolt circle diameter of 11.75 inches. The quantity of bolts used in ductile iron pipe installations is a critical factor in ensuring the integrity, safety, and durability of the pipeline system.However, the proper selection and number of bolts are essential for maintaining a tight, leak-free seal at joints. Factors such as pipe size, pressure requirements, and installation environment directly influence the number of bolts required. This article will explore the key factors that affect bolt quantity, provide comparisons between different pipe sizes and joint types, and address frequently asked questions about ductile iron pipe bolt quantity.
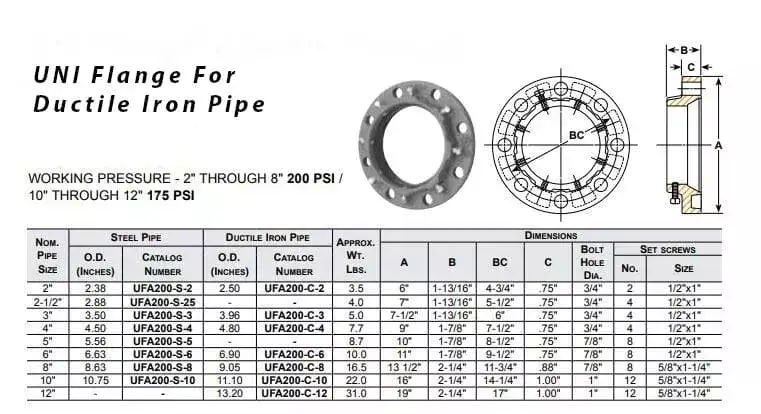
1. Factors Affecting Ductile Iron Pipe Bolt Quantity
The number of bolts required for ductile iron pipe connections depends on several critical factors. These include the pipe size, joint type, pressure rating, and environmental considerations. In general, larger pipes require more bolts to ensure a secure and stable connection, particularly when high pressure or external forces are involved.
-
Pipe Size: Larger diameter pipes require more bolts due to the increased surface area of the joint. Standard practice dictates that the number of bolts typically increases as the pipe diameter grows. For instance, a 6-inch pipe may require 4 bolts, while a 36-inch pipe may require up to 12 bolts or more, depending on the connection type.
-
Joint Type: The type of joint used also affects the bolt quantity. Ductile iron pipes often use flanged joints or push-on joints, with flanged joints typically requiring more bolts to secure the connection compared to push-on joints. This is because flanged joints involve bolted connections on both ends of the pipe, while push-on joints rely on rubber gaskets to create a seal.
-
Pressure Rating: The pressure rating of the pipeline plays a significant role in determining the number of bolts. Higher-pressure pipelines, such as those used in water transmission, require additional bolts to withstand the increased force. A standard pressure rating of 150 PSI might require fewer bolts, while a higher pressure rating, such as 350 PSI, will require more to prevent leaks and ensure the joint integrity.
-
Environmental Factors: External conditions, including soil type, moisture, and exposure to chemicals, also influence the number of bolts. In corrosive or chemically aggressive environments, additional bolts may be used to reinforce the pipe connections, particularly when extra sealing is necessary to prevent leakage.
Table 1: Bolt Quantity vs. Pipe Size and Pressure Rating
Pipe Size (Inches) | Pressure Rating (PSI) | Number of Bolts (Flanged Joints) | Number of Bolts (Push-On Joints) |
---|---|---|---|
6 | 150 | 4 | 2 |
12 | 150 | 6 | 4 |
24 | 250 | 8 | 6 |
36 | 350 | 12 | 8 |
48 | 350 | 14 | 10 |
2. Understanding Different Joint Types in Ductile Iron Pipes
Ductile iron pipes are available with a variety of joint types, each requiring different bolt quantities. Understanding the differences in joint designs is essential for determining the number of bolts needed for a secure and reliable connection.
-
Flanged Joints: Flanged joints are the most common type used for ductile iron pipes, particularly in larger sizes. These joints consist of two flanges, one on each end of the pipe, that are bolted together. The number of bolts needed depends on the pipe diameter and pressure rating. Flanged joints provide a very strong and leak-resistant connection, especially when used with gaskets.
-
Push-On Joints: Push-on joints, also known as rubber gasket joints, are commonly used for smaller ductile iron pipes. These joints do not require bolts for assembly; instead, the pipe ends are fitted together with a rubber gasket that creates a seal. However, when additional sealing or reinforcement is needed in high-pressure or aggressive environments, bolts may be used as supplementary support.
-
Mechanical Joints: Mechanical joints are another common connection type for ductile iron pipes. These joints use a combination of bolts, glands, and rubber gaskets to achieve a leak-proof seal. The number of bolts used in mechanical joints is typically greater than in push-on joints but may be similar to flanged joints in smaller diameter pipes.
-
Restrained Joints: These joints are designed to prevent axial movement, which is critical in high-pressure pipelines. Restrained joints may involve additional bolts to prevent the pipe from dislodging under pressure or external forces. These joints are often used in regions with high seismic activity or areas prone to soil movement.
Table 2: Comparison of Joint Types
Joint Type | Required Bolts | Pipe Diameter Range | Pressure Rating Range | Advantages |
---|---|---|---|---|
Flanged Joint | 4-14 bolts | 6 inches – 48 inches | 150 PSI – 350 PSI | High strength, secure connection, easy maintenance |
Push-On Joint | 0-4 bolts | 6 inches – 24 inches | 150 PSI – 250 PSI | Cost-effective, simple installation |
Mechanical Joint | 4-10 bolts | 6 inches – 24 inches | 150 PSI – 300 PSI | Versatile, good for moderate pressures |
Restrained Joint | 6-12 bolts | 12 inches – 48 inches | 250 PSI – 350 PSI | Prevents movement, ideal for high-pressure applications |
3. Common Materials Used for Ductile Iron Pipe Bolts
Ductile iron pipe bolts are made from a variety of materials to provide the necessary strength and corrosion resistance. The most commonly used materials include:
-
Carbon Steel: Carbon steel bolts are often used in ductile iron pipe applications due to their strength and availability. However, they are susceptible to rust in harsh environments, and as a result, they may require coatings such as galvanization or epoxy to prevent corrosion.
-
Stainless Steel: Stainless steel bolts are highly resistant to corrosion and are used in applications where additional protection is necessary, such as in marine environments or areas with high humidity. Stainless steel bolts are more expensive than carbon steel but offer superior long-term durability.
-
Galvanized Steel: Galvanized steel bolts are carbon steel bolts that have been coated with zinc to prevent rusting. These bolts are commonly used in ductile iron pipe installations due to their good balance of cost and corrosion resistance. They are especially useful in environments where the bolts are exposed to moisture or chemicals.
-
Alloy Steel: Alloy steel bolts may be used in specialized applications requiring higher strength and resistance to wear and tear. These bolts are typically used in high-pressure systems where the risk of joint failure due to external forces is high.
Table 3: Comparison of Bolt Materials
Material | Corrosion Resistance | Strength | Cost | Common Applications |
---|---|---|---|---|
Carbon Steel | Moderate | High | Low | General use, non-corrosive environments |
Stainless Steel | Excellent | Very High | High | Marine environments, highly corrosive areas |
Galvanized Steel | Good | Moderate | Moderate | Water systems, general industrial use |
Alloy Steel | Excellent | Very High | High | High-pressure systems, heavy-duty applications |
4. Calculating the Correct Bolt Quantity for Your Ductile Iron Pipe Installation
To ensure a secure and leak-proof joint, it’s essential to calculate the correct number of bolts for ductile iron pipe installations. The calculation should account for several factors, including pipe size, joint type, pressure rating, and environmental conditions. The number of bolts can be determined by referencing standard guidelines provided by industry organizations such as the American Water Works Association (AWWA) or manufacturers’ recommendations.
-
Step 1: Identify the Pipe Size: Determine the pipe diameter to assess the basic number of bolts required. Larger pipes will naturally require more bolts due to the larger surface area of the joint.
-
Step 2: Determine the Joint Type: The type of joint used (flanged, push-on, mechanical, or restrained) will affect the number of bolts needed. Flanged joints will typically require more bolts than push-on joints, which may not require bolts at all.
-
Step 3: Consider the Pressure Rating: Higher-pressure systems require more bolts to secure the joint, as higher forces are exerted on the pipe. Be sure to select the appropriate bolt quantity based on the pressure rating.
-
Step 4: Environmental Factors: Consider the environmental conditions, such as exposure to moisture or chemicals, to determine if additional bolts or protective coatings are necessary to prevent corrosion.
Example Calculation:
For a 24-inch ductile iron pipe with a pressure rating of 250 PSI and using a flanged joint, approximately 8 bolts are typically required. However, if the system is in a high-moisture area, an additional two bolts may be added to account for extra sealing requirements.
5. Maintenance and Inspection of Ductile Iron Pipe Bolts
Maintaining and inspecting the bolts in ductile iron pipe systems is crucial to prevent joint failure and ensure long-term performance.
Key procedures include:
- Visual Inspection – Check for corrosion, deformation, or thread damage
- Torque Verification – Ensure proper tightness using calibrated tools
- Lubrication – Apply anti-seize compounds to prevent galling
- Corrosion Protection – Monitor coating conditions and replace damaged protection
- Replacement Schedule – Follow manufacturer guidelines for bolt lifespan
For higher pressure applications, such as Class 250 flanges, the specifications may differ. It’s essential to consult the relevant standards or manufacturer guidelines to determine the exact bolt requirements for specific applications.
Table: Bolt Specifications for 10-Inch Ductile Iron Flanges
Flange Class | Number of Bolts | Bolt Diameter (inches) | Bolt Length (inches) | Bolt Circle Diameter (inches) |
---|---|---|---|---|
Class 125 | 12 | 7/8 | 3.5 | 11.75 |
Class 250 | Varies | Varies | Varies | Varies |
Note: “Varies” indicates that specifications depend on specific standards and should be verified accordingly.
Frequently Asked Questions (FAQs)
Q1: What is the standard number of bolts for a 10-inch ductile iron pipe flange?
A: For a 10-inch ductile iron pipe flange adhering to the ANSI/AWWA C115/A21.15 standard, the typical requirement is 12 bolts. These bolts are generally 7/8 inches in diameter and 3.5 inches in length, arranged on a bolt circle diameter of 11.75 inches.
Q2: Do bolt requirements change with different flange classes?
A: Yes, bolt requirements can vary depending on the flange class. Higher pressure classes, such as Class 250, may necessitate bolts of different sizes, lengths, or quantities to ensure a secure and leak-free connection. It’s crucial to consult the specific standards or manufacturer guidelines for accurate information.
Q3: Why is it important to adhere to standard bolt specifications?
A: Adhering to standard bolt specifications ensures the integrity and safety of the piping system. Using the correct number and size of bolts helps maintain proper sealing, prevents leaks, and ensures the system can handle the designated pressure loads. Deviating from standard specifications can compromise the system’s performance and safety.
Q4: Can I use bolts of different materials for ductile iron flanges?
A: While carbon steel bolts are commonly used, other materials like stainless steel or galvanized steel may be employed depending on the application’s environmental conditions and corrosion considerations. It’s essential to ensure that the chosen bolt material is compatible with the flange material and the operating environment.
Q5: How do I determine the correct torque for flange bolts?
A: The correct torque for flange bolts depends on factors such as bolt size, material, gasket type, and flange specifications. Manufacturers often provide torque guidelines, and standards like the AWWA C115/A21.15 offer recommendations. Proper torque ensures a secure seal without over-stressing the bolts or flanges.
Q6: Are there differences in bolt requirements between ductile iron and other pipe materials?
A: Yes, different pipe materials may have varying flange and bolt specifications due to differences in material strength, thermal expansion, and pressure ratings. Always refer to the relevant standards and manufacturer guidelines specific to the pipe material in use to determine accurate bolt requirements.
References:
ANSI/AWWA C115/A21.15 Standard – American Water Works Association (AWWA)
AWWA M41 Manual – Ductile-Iron Pipe and Fittings
EPA – Drinking Water Distribution Systems
Wikipedia – Flange (Plumbing)