Ductile iron pipe flanges feature 10 standardized widths ranging from 1/2″ to 24″ (DN15 to DN600), with typical dimensions including 3/4″, 1″, 2″, 4″, 6″, 8″, 10″, 12″, 16″, and 20″. These ANSI/AWWA C110/A21.10-compliant flanges maintain 125 psi to 250 psi pressure ratings, with widths precisely calibrated to bolt circle diameters and facing types (flat, raised, or ring joint). Proper flange width selection ensures leak-proof joints in water/wastewater systems while accommodating thermal expansion and seismic movements.
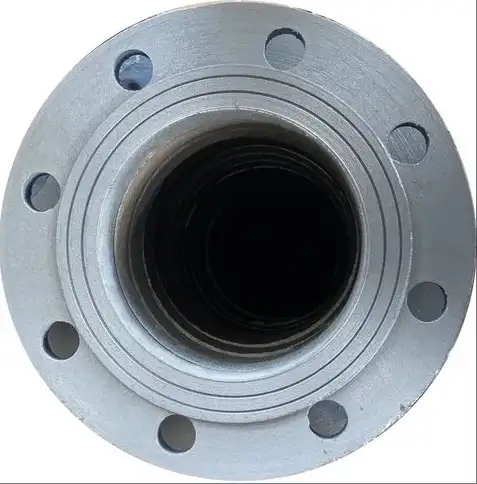
1. Standards and Specifications Governing Ductile Iron Pipe Flange Widths
Ductile iron pipe flanges are manufactured in accordance with several industry standards to ensure uniformity, safety, and compatibility. The primary standards include:
-
ANSI/AWWA C110/A21.10: Covers ductile iron and gray iron fittings with flanged ends, specifying dimensions and tolerances.
-
ANSI/AWWA C115/A21.15: Pertains to flanged ductile iron pipe with threaded flanges, detailing fabrication and dimensions.
-
ASME B16.1: Specifies dimensions for cast iron pipe flanges and flanged fittings, including Class 125 and Class 250.
-
ASME B16.42: Covers ductile iron fittings for pressure applications, including flange dimensions and tolerances.
These standards ensure that flanges meet specific requirements for pressure ratings, dimensions, and material properties, facilitating interoperability and safety in piping systems.
2. Dimensional Characteristics of Ductile Iron Pipe Flanges
The width of a ductile iron pipe flange is a critical dimension that affects the overall performance and compatibility of the piping system. Key dimensional characteristics include:
-
Flange Thickness: Varies based on pressure class and pipe size. For example, a 12-inch Class 150 flange typically has a thickness of 1.25 inches.
-
Bolt Circle Diameter (BCD): The diameter of the circle on which bolt holes are centered. This dimension ensures proper alignment and load distribution.
-
Number and Size of Bolt Holes: Determined by the flange size and pressure class, affecting the flange’s ability to withstand internal pressures.
Understanding these dimensions is essential for selecting the appropriate flange for a specific application, ensuring structural integrity and leak prevention.
3. Material Considerations and Coatings
Ductile iron flanges are chosen for their strength, durability, and resistance to corrosion. Material considerations include:
-
Ductile Iron Composition: Offers superior tensile strength and impact resistance compared to gray iron.
-
Coatings: Flanges are often coated with materials such as epoxy or bituminous coatings to enhance corrosion resistance.
-
Lining: Cement lining is commonly applied to the interior surfaces to prevent corrosion and improve flow characteristics.
Selecting the appropriate material and coating is vital for ensuring the longevity and performance of the flange in various environmental conditions.
4. Applications and Installation Practices
Ductile iron pipe flanges are utilized in a variety of applications, including:
-
Water Distribution Systems: Providing reliable connections in municipal water supply networks.
-
Wastewater Treatment Plants: Handling corrosive and abrasive fluids in treatment processes.
-
Industrial Piping Systems: Facilitating the transport of various industrial fluids under pressure.
Proper installation practices are crucial for ensuring the effectiveness of flanged connections. Key considerations include:
-
Alignment: Ensuring that flanges are properly aligned to prevent undue stress and potential leaks.
-
Bolt Torque: Applying the correct torque to bolts to achieve a uniform seal without damaging components.
-
Gasket Selection: Choosing appropriate gasket materials compatible with the conveyed fluid and operating conditions.
Adhering to best practices during installation helps maintain the integrity and performance of the piping system.
5. Comparative Analysis of Flange Widths Across Standards
Flange widths can vary based on the applicable standards and pressure classes. The following table provides a comparative analysis:
Nominal Pipe Size (inches) | Class 125 Flange Thickness (inches) | Class 250 Flange Thickness (inches) |
---|---|---|
4 | 0.94 | 1.38 |
6 | 1.00 | 1.50 |
8 | 1.12 | 1.62 |
10 | 1.19 | 1.75 |
12 | 1.25 | 2.00 |
This comparison highlights the increase in flange thickness with higher pressure classes, reflecting the need for greater strength to withstand elevated pressures.
6. Frequently Asked Questions (FAQs)
Q1: What factors determine the appropriate flange width for a ductile iron pipe?
A1: The appropriate flange width is determined by several factors, including the pipe’s nominal size, operating pressure, and the applicable industry standards. Larger pipe sizes and higher pressure ratings typically require thicker flanges to ensure structural integrity and prevent leaks. Standards such as ANSI/AWWA C110 and ASME B16.1 provide specific guidelines for flange dimensions based on these parameters.
Q2: How does flange width affect the performance of a piping system?
A2: Flange width directly impacts the strength and sealing capability of the connection. A flange that is too thin may not withstand the internal pressures, leading to deformation or failure. Conversely, an excessively thick flange may introduce unnecessary weight and cost. Proper flange width ensures a balance between structural integrity and economic efficiency, contributing to the overall performance and reliability of the piping system.
Q3: Can flanges of different standards be used interchangeably?
A3: While some flanges may have similar dimensions across different standards, interchangeability is not guaranteed. Variations in bolt hole patterns, flange thickness, and pressure ratings can lead to incompatibility. It is essential to verify that flanges conform to the same standard or are specifically designed to be compatible to ensure a proper fit and maintain system integrity.
Q4: What are the common materials used for ductile iron flange coatings?
A4: Common coatings for ductile iron flanges include epoxy, bituminous coatings, and fusion-bonded epoxy (FBE). These coatings provide corrosion resistance, enhancing the durability of the flanges in various environmental conditions. The choice of coating depends on factors such as the conveyed fluid, operating temperature, and exposure to corrosive elements.
Q5: How are flange widths maintained during manufacturing?
A5: Manufacturers adhere to strict quality control measures to ensure flange widths meet specified standards. This includes precise machining, regular inspections, and compliance with industry standards such as ANSI/AWWA and ASME. Advanced manufacturing techniques and equipment are employed to achieve the required tolerances and surface finishes, ensuring consistency and reliability in flange dimensions.
Q6: What maintenance practices are recommended for flanged connections?
A6: Regular inspection of flanged connections is essential to detect signs of wear, corrosion, or leakage. Maintenance practices include checking bolt tightness, replacing gaskets as needed, and applying protective coatings to prevent corrosion. Proper maintenance ensures the longevity and performance of the flanged connections, minimizing the risk of system failures and associated downtime.
References:
ANSI/AWWA C110/A21.10 – Ductile Iron and Gray Iron Fittings (American Water Works Association)
ASME B16.1 – Cast Iron Pipe Flanges and Flanged Fittings (American Society of Mechanical Engineers)